Precision machining
Precision metal machining on CNC machines is our core competency.
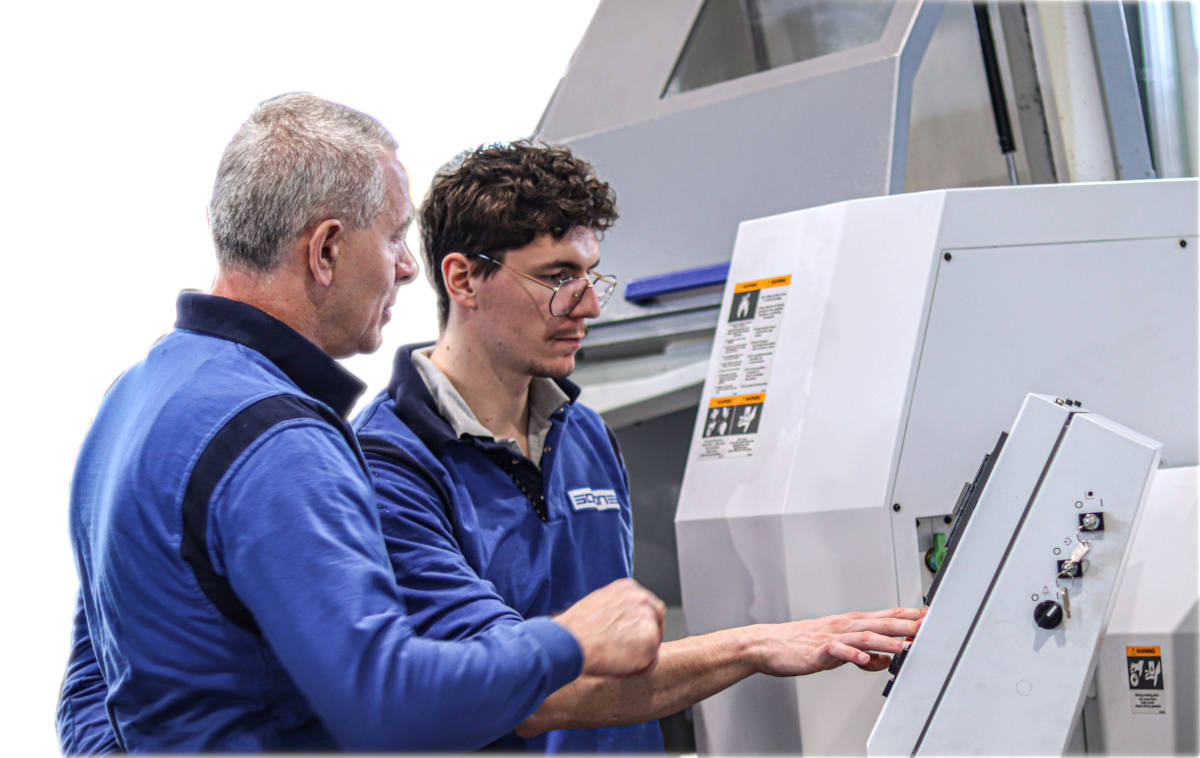
What is precision machining?
Precision machining is the process of precision parts manufacturing using machine tools and cutting tools. The manufacturing process itself involves shaping the geometry of the part by cutting material from a block of raw material. The distinctive feature of this manufacturing method is that it maintains the high precision of the manufactured components.
Parts manufacturing by this method is based on the fundamentals of CNC machining technology, except that much more focus is placed on the quality of execution of each operation within the process. As part of the precision machining process, almost all machining operations, such as CNC turning, CNC milling, drilling, and others, are used. Turning is a very efficient process in the production of parts.
To achieve the expected tight dimensional tolerances of the precision parts produced, operations such as grinding, polishing, honing, and other such operations are particularly important in this manufacturing process. These are methods of material machining designed to finish parts with a focus on the highest dimensional precision.
The process flow of precision machining
Precision machining is a complex, multi-step process that aims to achieve uncompromising quality in manufactured parts ultimately. The individual steps may vary depending on the category of machined parts. Still, a few basic process steps can be distinguished:
1. Design: the first step is to create a detailed design of the part to be machined. This design will include specifications for the size, shape, and tolerances of the part.
2. Programming: The next step is to create a program for the machine tool that will be used to create the part. This program will contain instructions for the machine on moving and machining the material to create the desired part.
3. Setup and Inspection: Before machining can begin, the machine must be equipped with the proper tools, and the material to be machined must be checked to ensure it meets specifications.
4 Machining: The machining process involves the machine following a programmed set of instructions to achieve the desired shape and dimensions of the part by cutting and shaping the material.
5 Inspection and quality control: Once the machining process is complete, the part is inspected to ensure it meets specifications and tolerances. Adjustments, if required, are implemented, and the part undergoes testing to verify that it aligns with the desired quality standards.
6. Packaging and shipping: the final step is to pack and ship the finished parts to the customer.
What materials can be used in precision CNC machining?
Due to the high flexibility of the process, the versatility of the machine tools used, and the ever-expanding capabilities of cutting tools, there is a wide range of materials for precision machining. Among the most popular are:
Advantages of precision machining
Precision machining is becoming increasingly important in parts manufacturing for industry. This is due to a number of undeniable advantages of this manufacturing method.
Applications
This technology finds applications across a broad spectrum of industries and uses, including:

Sabner – expert in precision machining
Our company has been engaged in metal machining since its foundation. Over the years of activity in the industry, we have developed our competence in this field to an expert level. This now allows us to focus mainly on precision machining as the most demanding form of metal machining.
The process uses advanced technology and machinery to manufacture metal parts for a wide range of industries, including aerospace, medical, and automotive. Using computer-aided design (CAD) software and computer numerical control (CNC) software, we can produce highly complex and intricate precision parts that meet or exceed industry standards.
Our experienced engineers collaborate closely with our clients to understand their distinct needs and specifications, guaranteeing that the end product attains the utmost quality.