Swiss type lathe
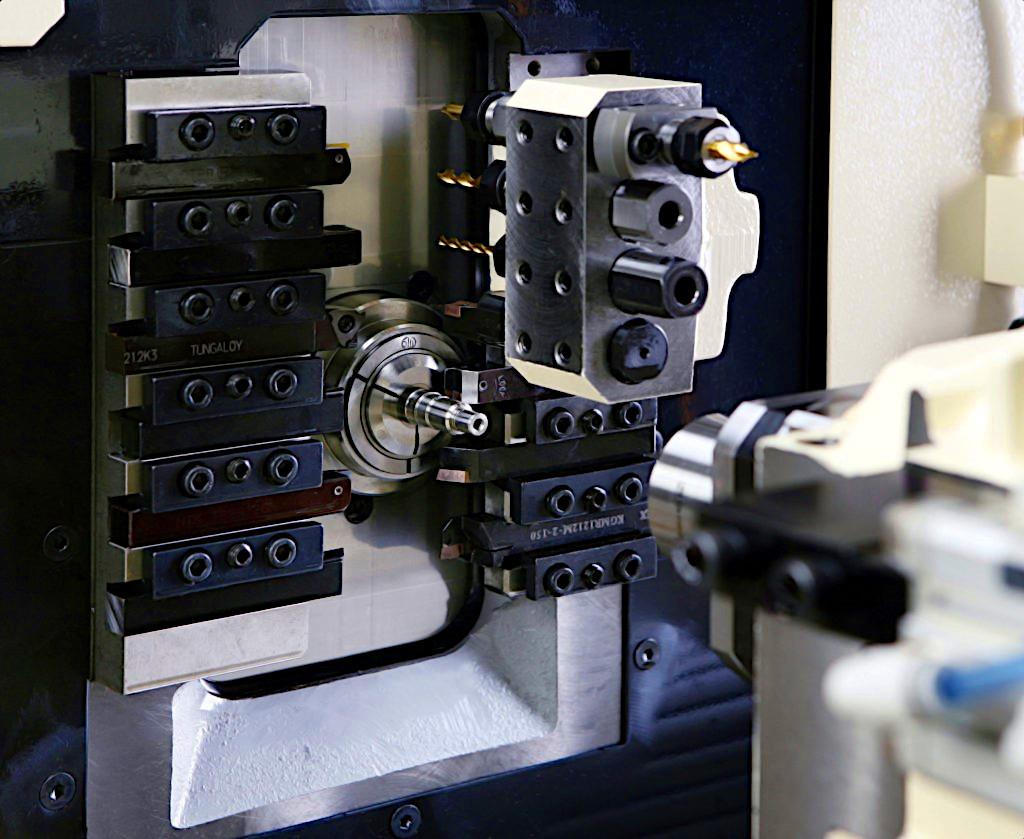
What is Swiss type lathe? What is it used for?
A Swiss type lathe is a specific type of lathe in which the material in the form of a bar, in addition to its rotary motion, simultaneously performs a longitudinal motion that allows cutting. This is possible due to the unique design of the machine using a guide bush. Such machines are also sometimes called Swiss automatic lathes or Swiss-type machines.
A bit of history
Swiss type lathes have their genesis in the watchmaking industry. An industry where the need to turn long, thin, complex parts with high accuracy was invaluable to the manufacturing process. At the height of the industrial revolution, an efficient watchmaker not only had to produce precision parts but also do so in a highly efficient manner to meet demand.
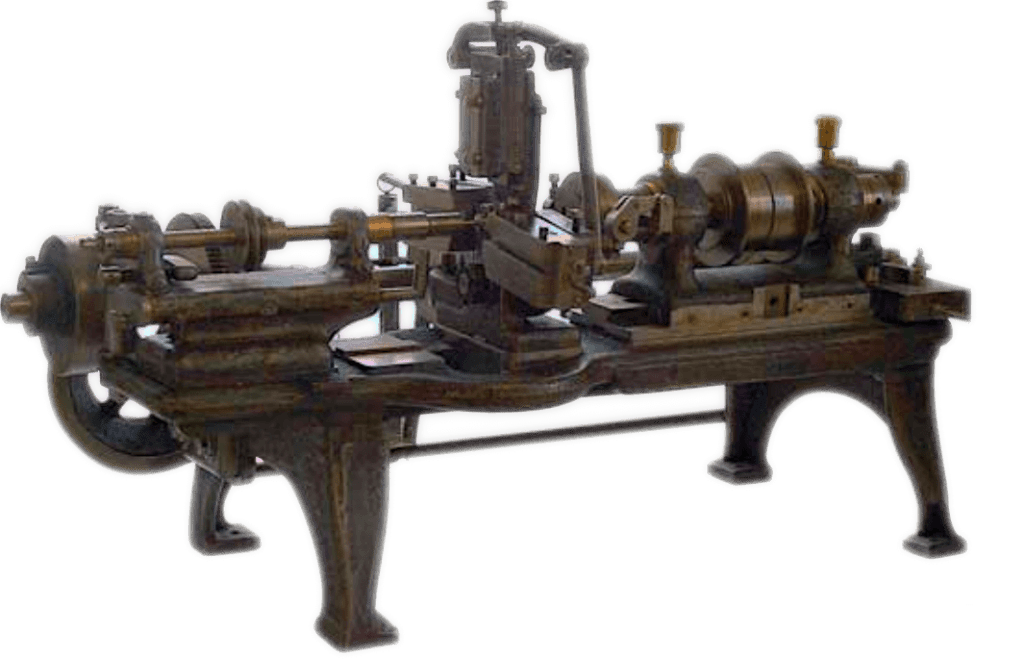
The invention of Swiss turning is credited to Jakob Schweizer, a watch manufacturer from Bienne, Switzerland, in the late 19th century. He developed the first lathe equipped with what later proved to be a timeless invention: a sliding headstock – allowing simultaneous rotation of the material and its longitudinal movement.
Turning on automatic lathes has now evolved much further than its creators could have imagined. While the automatic lathes of the 21st century are not necessarily made in Switzerland, they are all designed primarily for turning small, complex, precision metal parts, mainly for the automotive, medical, and electronics industries.
How lathe works?
Unlike conventional CNC lathes, in which the material is stationary and the tool moves, an automatic machine with a moving headstock allows the material to move along the Z-axis while the tool remains stationary. The bar is held in a spindle deep inside the machine housing and moved by a guide bush into the machining zone. Only the machined part is pulled out of the guide bushing, allowing the material to be supported securely, eliminating deflection for improved accuracy. For longer parts, the counter spindle grabs the finished front of the part to support it as it extends further through the bushing.
Guide bushing
The guide bushing is the most important component in any sliding head machine, and its precision and fit are critical to a proper CNC turning process. By its design, the guide bushing is similar to the classic clamping collets used in automatic lathe spindles. However, the main difference is the materials used in it – the inner surface is made of cemented carbide very precisely ground. This is due to the nature of the bushing work, which consists of a moving interaction with the bar of the workpiece material moving inside the bushing. The bushing allows you to adjust the clearance of the material clamping to adapt to a particular batch of raw material.
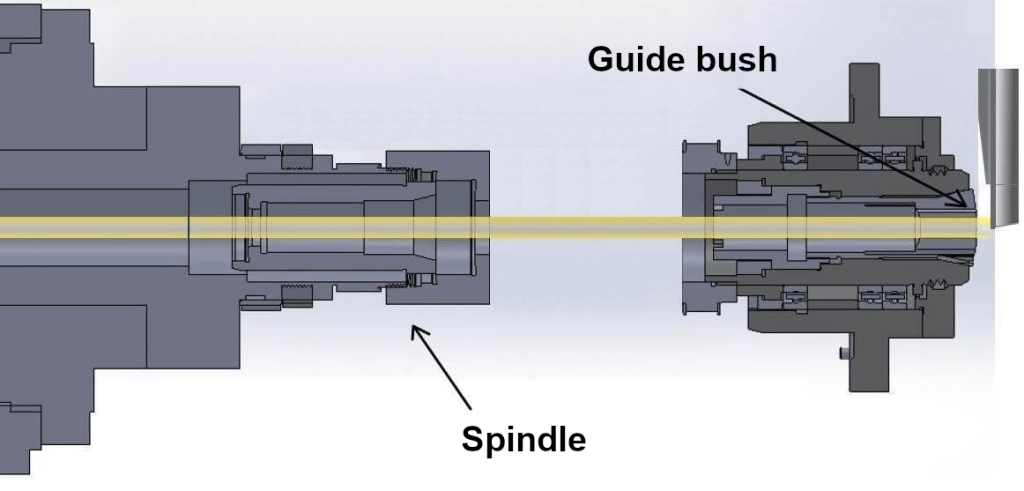
Deflection control
By supporting the workpiece bar with the guide bush, accuracy can be maintained throughout the precision turning process.
Physical workpieces subjected to any force will naturally deflect. As for conventional CNC lathes, when the cutting forces cause too much deflection, the dimensional accuracy of the cutting process will mostly deteriorate. For conventional lathes, the rule of thumb is that when turning parts with a length-to-diameter ratio greater than 3 to 1, tailstock support is required to prevent excessive deflection.
As for sliding head machines, the guide bushing supports the workpiece bar so close to the cutting tools that the deflection caused by cutting forces is effectively zero. The user can cut excess material in a single pass while maintaining high dimensional precision.
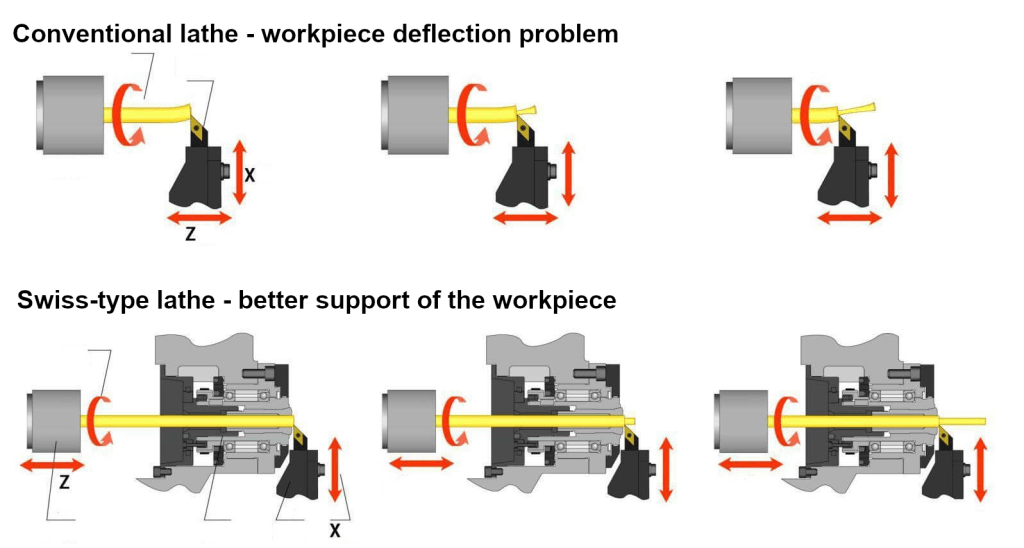
Negative becomes positive
In automatic lathes with a movable headstock, Z-axis movements are derived from material movement instead of turning tool movement. This particular difference is reflected in the programming of the machine. On conventional lathes, the material protrudes from the chuck a certain distance. In such a situation, Z zero is assumed on the face of the material, and anything in the direction of the material has negative values.
In Swiss-type automatic lathes, on the other hand, the turning tools remain stationary as the material extends. The surface of the material face is also zero in the Z-axis as on conventional lathes. Still, everything beyond that surface will be positive. This difference is very important to keep in mind in connection with Z-axis offsets. This means that deeper drilling or longer turning requires a “minus” offset on conventional lathes but will require a “plus” offset on sliding head machines.
Machining in stages
By default, in classic CNC turning, cutting operations are divided into roughing and finishing. First, we remove excess material from the entire profile with a roughing tool. We machine the same profile with a finishing tool using a smaller allowance to achieve the desired dimension.
In Swiss-type automatic lathes, the division of the process into stages looks completely different. This is because the length of the guide bush requires the machined parts to be divided into sections. Otherwise, a section of the bar already machined could fall out of the guide bushing during the return movement. To avoid this phenomenon, the part is machined by dividing it into sections with a length shorter than the length of the guide bushing’s working part. This allows full use of the support provided by the bushing.
Oil instead of coolant
Most Swiss machining machines use oil as a machining aid instead of water-based coolant. This means that lubricity will be greater. Advantages of oil include the absence of odor-causing bacteria and the elimination of the orange peel effect on hands after prolonged contact with coolant. Increasing tool life with oil cooling is also of great importance.
The main disadvantage of water-based coolants is that oil is not as effective at dissipating heat, so the sliding head machine can quickly heat up in the work zone area. Equipping these machines with fire protection systems is necessary for manufacturing without employee supervision.
More scrap
Scrap can become a problem, especially with expensive materials. Due to the geometry of Swiss-type automatic lathes, a scrap of 150 to 300 mm must remain from each machined bar. This is because the end of the bar is held by the spindle, which is located inside the machine housing and never reaches the machining zone. The presence of a guide bushing does not allow this. For this reason, on Swiss-type lathes, the number of parts that can be made from a single bar is always slightly lower than on classic machines.
Multitasking
Unlike a traditional CNC machine with 3 or 4 axes, sliding-head automatic lathes can be equipped with up to 13 axes. This adds significant value, reducing work time and labor intensity because operators do not have to transfer work in progress to another machine for completion.
The availability of driven tools gives Swiss-type lathes the ability to mill. At the same time, the material slides out of the guide bush. The Y axis provides full milling capabilities unavailable on most conventional CNC lathes. In addition to driven tools for basic machining, many sliding head machines have a station with a toolset for counter spindle operations. This allows the other side of the workpiece to be finished after it has been cut off and caught in the counter spindle.
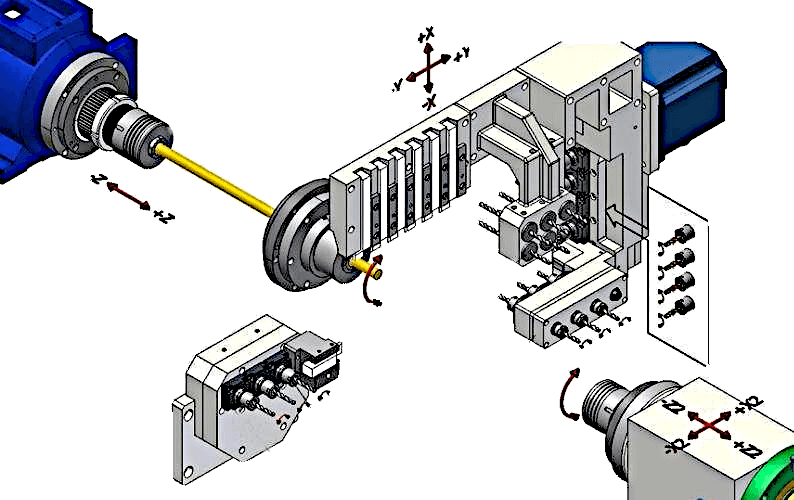
Advantages of Swiss type automatic lathes
The benefits of sliding head machines stem from the guide bush, as well as the geometry and mechanics within the tool zone.
Application of Swiss type automatic lathes
Although watchmakers have already taken over Swiss-type lathes for many years for other applications, they remain widely used in this industry. The medical industry is also enthusiastic about adopting this technology, particularly for producing surgical screws and tools that must adhere to exceptionally stringent quality standards. But the popular applications for these machines continue. Below is a short list of the other most important applications.
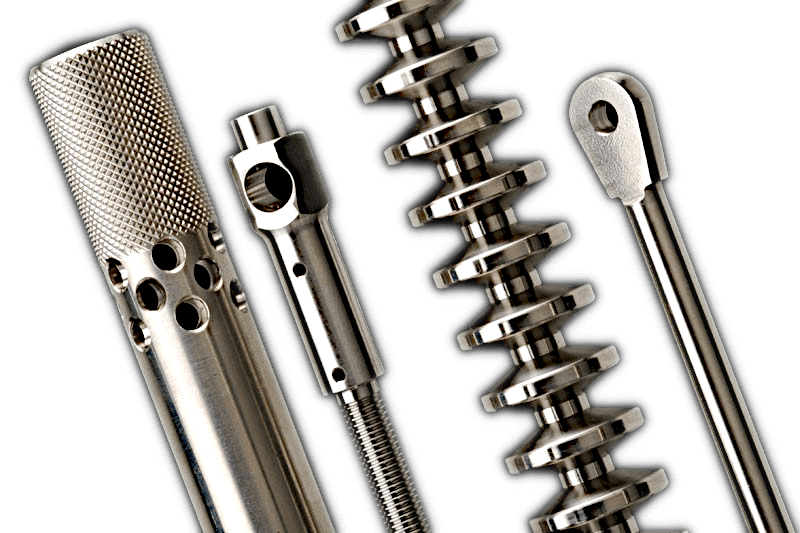