CNC turning centers – basic information

History of turning technology
Turning is one of the oldest manufacturing technologies on Earth. The earliest versions date back to the ancient Egyptians, who invented a two-person lathe operated by a bow around the 13th century BC. Fascinatingly, even though a great deal of time has passed since then, turning technology is still widely used for manufacturing various parts.
The strength of this method is its simplicity and efficiency. Of course, over the years, man has systematically developed and improved the process to the point that the machine tools in use today have little in common with what even our grandparents worked on. Modern CNC turning centers are very complex machines with powerful capabilities that have long since ceased to be reduced to turning only.
In the following article, we will introduce a little knowledge of modern machine tools used for turning.
CNC lathes and CNC turning centers: what is the difference?
You have probably encountered the terms “CNC lathe” and “CNC turning center” interchangeably.
Although there is no formal distinction between lathes and turning centers, the former term is commonly used to refer only to simpler machines – designed for CNC turning operations alone. By contrast, the term “turning center” usually refers to machines that integrate milling or drilling capabilities or those with counter spindles to perform operations on the other side of the part.
A CNC lathe is simply turning; it’s a 2-axis machine with X and Z axes with only one chuck. Opposite the chuck may be a tailstock to support the part, or in simpler designs, there is only the chuck itself.
A CNC turning center can incorporate milling capabilities, a secondary spindle, and a Y-axis to expand functionality. They are also called multi-tasking machines because they offer more than CNC turning. You can think of it as an evolution of the lathe. In the past, most people called such machines lathes. Still, as CNC machining became more complicated, they evolved into CNC turning centers after adding milling and counter spindles.
Construction of a CNC lathe
Whether you work on a lathe or a turning center, the basic parts are the same.
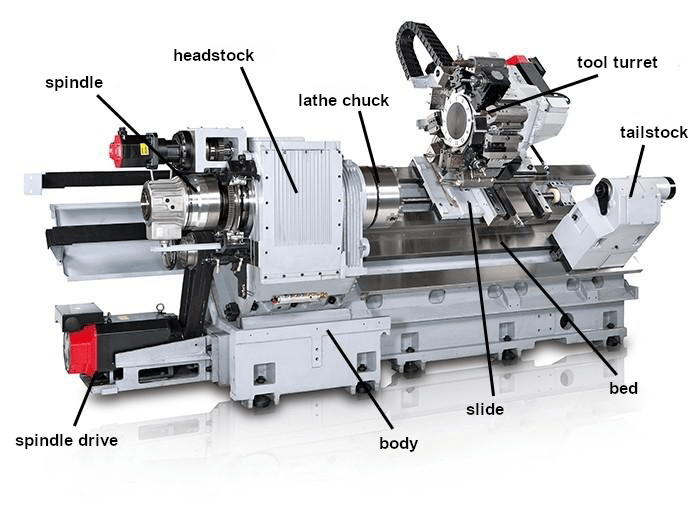
The headstock
The headstock houses the main spindle and the speed and gear change mechanisms. The main end of the spindle often contains a Morse taper. In early designs of industrial lathes, the spindle was driven directly by a flat pulley. Today, it is driven by an electric motor.
Bed
The bed of a lathe is a base connected to the headstock so that the slide and tailstock move in parallel with access to the spindle. This movement is facilitated by bed slides that hold the slide and tailstock on a fixed track.
Tool turret
The tool turret holds cutting tools and moves them longitudinally to the workpiece for CNC turning operations or perpendicularly for planning operations. The head consists of two castings: a top casting and a side casting.
Tailstock
The tailstock is mounted opposite the chuck of the machine tool’s main spindle. Unlike the spindle, the tailstock – which can be equipped with a taper for holding drills, reamers, or other tools – does not rotate. Alternatively, it travels longitudinally due to the influence of a lead screw.
CNC turning center configurations
There are two basic types of CNC turning centers: the traditional horizontal type, which has been around for a long time, and the vertical type, which differs in the alignment of the spindle rotation axis. In vertical CNC lathes, as the name suggests, the spindle rotates relative to a vertical axis.
Horizontal CNC lathes account for about 70 percent of the market because they have been around much longer. Every lathe maker took their first steps on a horizontal lathe.
Horizontal turning vs. vertical turning
Both horizontal lathes and vertical lathes have their characteristics. Inverted CNC vertical turning centers also exist, and they invert the placement of the spindle and lathe chuck. All three types of machines have the same basic components (headstock, slide, and more.), But they differ in orientation. Choosing a horizontal, vertical, or inverted lathe depends on several factors, but some practical principles can help you decide.
A vital benefit of a horizontal lathe is that gravity naturally directs the chips away from the workpiece. In other words, when turning, all the chips fall into the chip conveyor or basket.
In general, horizontal CNC lathes are more flexible because they can have longer beds relative to the spindle size. They can also use bar feeders and usually have tailstocks, which is rare in vertical versions. On the other hand, for machining short parts with large diameters, especially if they are heavy parts, a vertical CNC machining lathe will work very well.
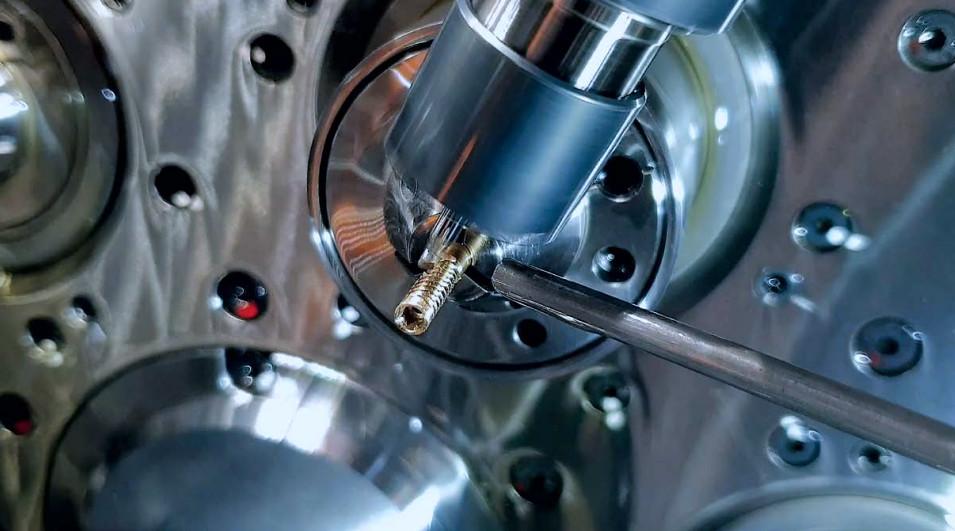
One of the advantages of a vertical lathe is that gravity aids in securely holding your part in the chuck. Chips, however, can be a problem, especially if the part is concave, as it can trap the chips inside. So, there is a risk of re-cutting the chips created by improper evacuation from the machining zone. Another issue with a vertical lathe is that the chips fall into the spindle, so its protection must be highly effective.
It is primarily the size of turned parts that is usually the deciding factor in choosing a lathe version. When we look at larger parts, many automotive applications (transmission blanks, brake discs, and more) are made vertically and usually with a double spindle. One of the benefits is that gravity helps clamp the part; once the part is inserted into the chuck, it seats itself, and its weight presses it against the chuck jaws.
There are parts as large as 500 mm in diameter machined on a horizontal machine, but loading them is always difficult because you have to push the part into the chuck and then hold it while clamping.
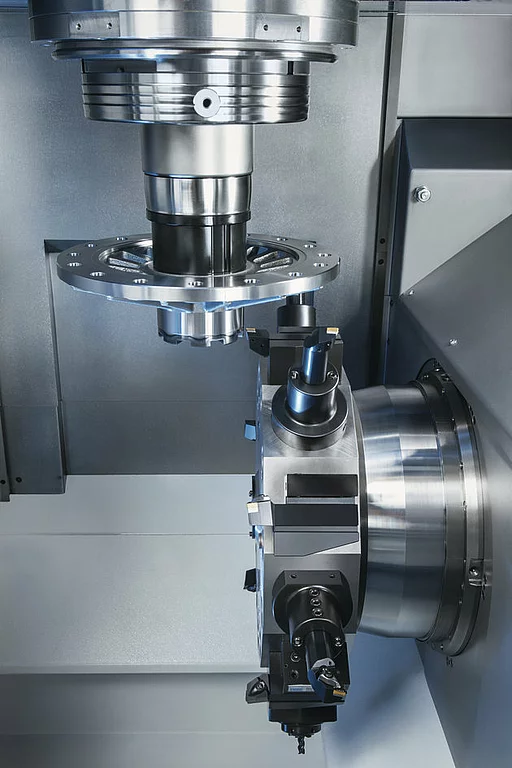
Another factor to consider when choosing between horizontal and vertical configurations is the degree to which the CNC turning center will be automated. Horizontal lathes are considered easier to automate due to the availability and popularity of bar feeders, which are responsible for supplying material to manufacturing.
On the other hand, however, when manufacturing from blank pieces – castings or forgings in these cases, automatic loading will be easier to implement on a vertical center. First, gravity assists in depositing the part in the chuck, and a robot is not needed to push it into position.
Secondly, these machines, especially vertical CNC lathes with an inverted spindle, have a moving spindle that works as a blank loader.
The potential of CNC turning technology
As you can see, today’s CNC machine tool market offers various technical solutions that can be used when producing parts. Whether the right technology and machine is selected for a particular task will often determine the success of the entire project. It is worth trusting the specialists at Sabner in this area, who have many years of experience in CNC turning for the most demanding customers.
