Thermal and chemical treatment of metals
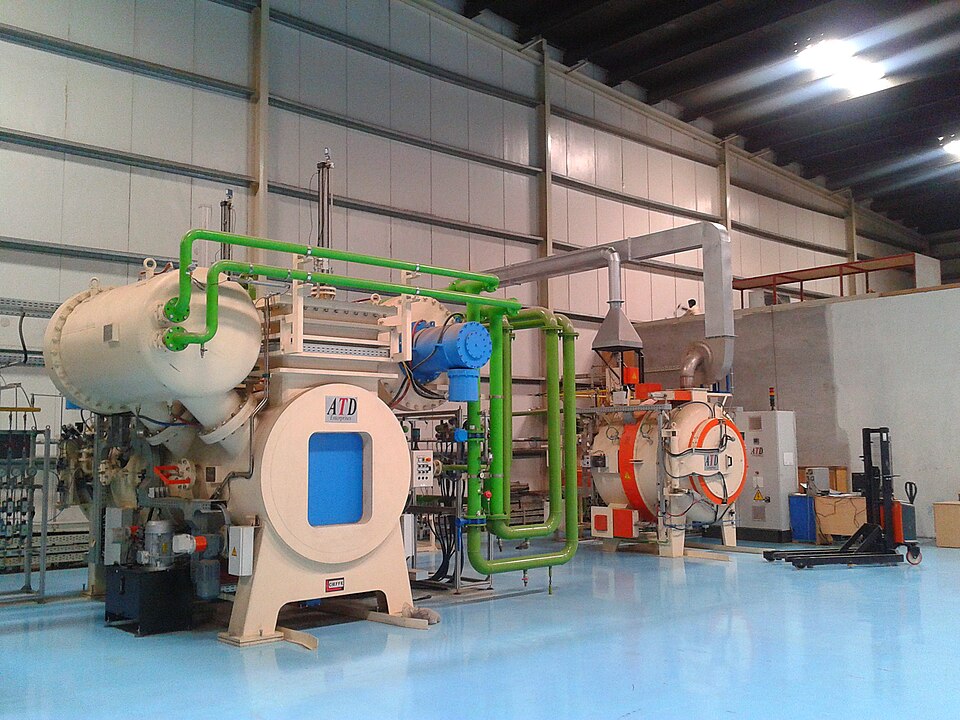
Table of contents
Modern engineering structures require materials with high surface strength, high resistance to abrasion, fatigue, and chemical agents, while maintaining ductility and toughness of the core. This desirable combination of properties can be achieved through heat and chemical treatment.
Heat and chemical treatment is a set of technological processes involving the saturation of the surface layer of metal elements with active chemical elements (such as carbon, nitrogen, boron, chromium) while simultaneously applying heat. As a result of these treatments, structural and chemical changes occur in the surface layer of the metal, which radically alter its properties.
The result of well-performed heat and chemical treatment is a hard, wear-resistant surface layer while maintaining a ductile and malleable core, which significantly increases the durability of machine parts and tools.
Depending on the element used and the process, there are different types of thermochemical treatment, the most common of which are carburizing, nitriding, and carbonitriding (also known as cyaniding), as well as more specialized methods such as chromium plating, aluminum plating, and boron plating.
In the following sections of this article, we will examine the mechanisms of these processes in greater detail, their practical applications, and their influence on the microstructure and properties of the surface layer of metals.
Mechanism of action – diffusion of elements
The basis of all heat and chemical treatment processes is the phenomenon of diffusion, i.e,. The spontaneous movement of atoms from an area of higher concentration to an area of lower concentration. In this case, we are dealing with the diffusion of an active chemical element (e.g., carbon, nitrogen) into the metal, most often iron. The process of metal surface saturation consists of three stages:
- Adsorption of active atoms – atoms of the saturating element settle on the metal surface, forming a so-called transition layer.
- Surface diffusion – atoms move across the surface, looking for suitable places to “enter” the crystal structure.
- Internal (volumetric) diffusion – at a sufficiently high temperature, the atoms diffuse into the metal, settling in the free spaces of the crystal lattice (most often between the nodes, in the so-called lattice gaps).
Temperature plays a crucial role here – the higher it is, the faster the diffusion, the greater the depth of saturation of the layer, but also the greater the risk of grain growth and changes in the material’s core.
Depending on the type of element, the diffusing atoms interact with iron atoms to form various solid solutions or chemical compounds (e.g., nitrides, carbides, borides). It is their presence that is responsible for the increased hardness of the surface layer, increased resistance to abrasion and fatigue, and improved corrosion and heat resistance.
The diffusion process occurs according to the concentration gradient, meaning that the concentration of the saturating element decreases with increasing depth. This results in a characteristic layered structure: a saturated zone (surface) – very hard, a transition zone – with gradually changing properties, and a core – retaining the original properties of the metal.
It is precisely this gradual structural and chemical change that gives heat treatment an advantage over other surface technologies, such as coating or spraying.
Carburizing
Carburizing is a heat treatment process in which the surface of a steel component is saturated with carbon to increase its hardness, wear resistance, and fatigue resistance. It is particularly used for low-carbon steels, which are not suitable for hardening on their own. Still, after carburizing, they gain a hard surface while retaining the ductility of the core.
Principle of operation
The carburizing process involves heating steel to the austenitizing temperature (approx. 880–950°C) and maintaining it in an atmosphere containing active carbon for a specified time (from several to several dozen hours), depending on the required layer depth.
During this time, carbon atoms adsorb on the surface and then diffuse into the steel, occupying the interstitial spaces of the austenite crystal lattice. After saturation, the components are hardened and tempered, allowing for high layer hardness (often greater than 60 HRC) while maintaining a ductile core.
Types of carburizing
Powder carburizing
- Traditionally used in a bed of charcoal and activators (e.g., BaCO₃),
- Not very precise, difficult to control,
- Currently, it is less commonly used, mainly in small-batch production of tools and antique parts.
Gas carburizing
- Most commonly used in industry,
- Carried out in an atmosphere of carburizing gases (e.g., CO, CH₄) in gas-tight furnaces,
- Enables precise control of temperature, time, and atmosphere composition,
- Allows for the achievement of a uniform carburized layer with a depth of up to several mm.
Vacuum (low-pressure) carburizing
- A modern method using cyclical feeding of carbonizing gas under vacuum conditions,
- Allows for high purity of the layer, without oxidation and deformation,
- Especially recommended for precise mechanical parts (e.g., gears, bearings).
Structure and properties of the carburized layer
After hardening, a structure of carbon-saturated martensite is formed in the surface layer, transitioning into bainite, ferrite, or pearlite as the material is penetrated deeper. The carburized layer achieves a hardness of over 62 HRC, is characterized by high abrasion and contact fatigue resistance, but has low resistance to high temperatures and corrosion (which limits its applications).
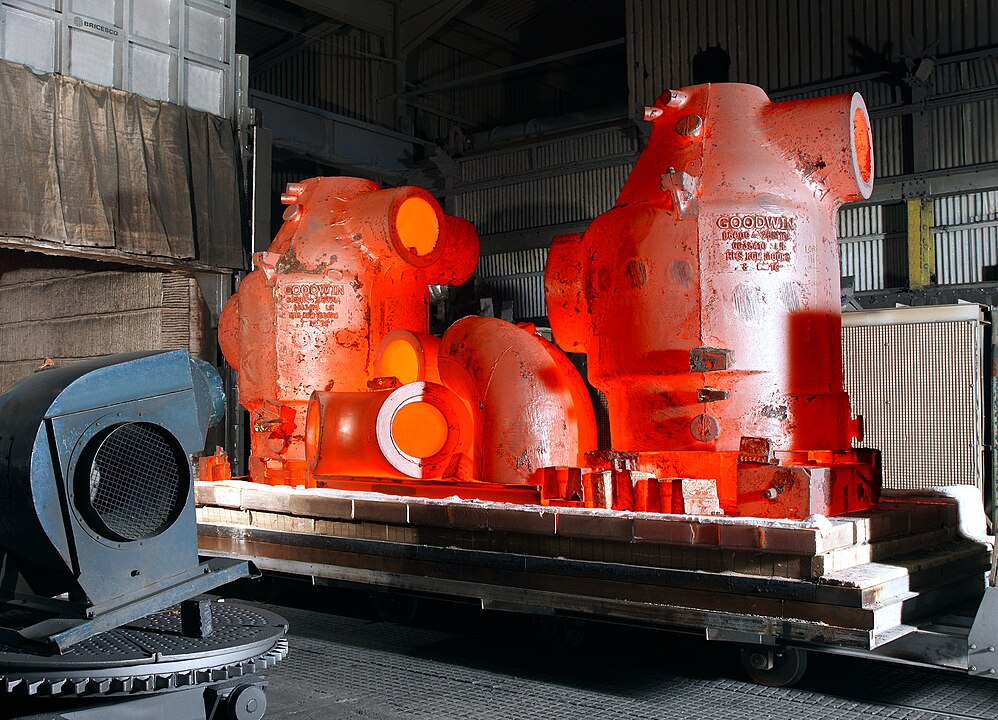
Nitriding
Nitriding is a process that saturates a metal surface with nitrogen, increasing hardness, wear resistance, corrosion resistance, and fatigue resistance without the need for hardening. Unlike carburizing, nitriding is typically carried out at lower temperatures (usually 500–580°C), which minimizes the risk of deformation, maintains the dimensional accuracy of the workpiece, and preserves the core structure.
During nitriding, nitrogen atoms adsorb on the surface of the steel, diffuse into the crystal structure, and form bonds with alloy metal atoms (such as Al, Cr, Mo, V), leading to the formation of intermetallic nitrides (e.g., AlN, CrN, VN). It is these compounds that are responsible for the high hardness and surface resistance.
Types of nitriding
Gas nitriding
- Carried out in an ammonia (NH₃) atmosphere, which decomposes into active nitrogen and hydrogen.
- Popular, inexpensive, and well-recognized.
- Process time: 10 to 100 hours.
- Layer thickness up to 0.5 mm, hardness up to 1100 HV.
Ion nitriding (plasma)
- Carried out under low-pressure conditions using an electric field,
- The metal surface acts as a cathode, and nitrogen molecules are attracted and “driven” into the material,
- Enables precise control of the depth and profile of the layer,
- The process is clean, fast, energy-efficient, and ideal for precision parts.
Salt bath nitriding
- Less commonly used, involves immersing parts in a solution of cyanides and nitrates.
- Conditions are more difficult to control, but the layer can be more resistant to corrosion.
The effectiveness of nitriding depends on the content of nitrogen-forming elements (e.g., Al, Cr, Mo, V), as well as on the microstructure and previous heat treatment. The steel should be heat-treated beforehand and the surface thoroughly cleaned (free of scale, grease, and rust).
A typical layer consists of two zones: a bonded layer, which is very hard, thin (10–20 μm), and composed mainly of nitrides, and a diffusion support layer, which is thicker (up to 0.5 mm) and responsible for load transfer.
Its characteristic features include a hardness of 900–1200 HV, excellent resistance to abrasion and fatigue, high corrosion resistance, especially when using stainless steels, and no need for hardening after the process, which reduces deformation and costs.
Carbonitriding (cyaniding)
Carbonitriding, also known as cyaniding, is a thermochemical treatment process in which the metal surface is simultaneously saturated with carbon and nitrogen. The treatment aims to achieve a hard, thin surface layer that offers high resistance to wear, abrasion, and fatigue, with a shorter treatment time compared to classic carburizing.
Compared to carburizing, the process temperature is lower, usually in the range of 700–900°C, the saturation time is shorter, and the resulting layer is thinner but harder due to the presence of nitrides.
Carbonitriding involves heating steel to the appropriate temperature and maintaining it in an environment containing both carbon and nitrogen, such as in the form of gases (CH₄ + NH₃) or salt baths (cyanates, cyanides).
During this process, carbon and nitrogen atoms adsorb onto the surface and then diffuse into the material, forming a mixed diffusion layer that contains carbides and nitrides of iron and alloying elements.
After carbonitriding, the hardness is as high as 850–1000 HV, the layer has high abrasion resistance and good resistance to oxidation and corrosion (better than after carburizing alone). The layer is typically 0.2–0.5 mm thick,, and there is very little deformation; often, no further heat treatment is required. Thanks to these properties, carbonitriding is used, among other things, for gears, shafts, bushings, screws, and components that require high surface resistance and dimensional accuracy.
Types of carbonitriding
Gas carbonitriding
- Carried out in an atmosphere of a mixture of saturating gases (e.g., ammonia and hydrocarbon gases),
- Most commonly used in industry,
- Allows control of process parameters and obtains a hard layer with a thickness of 0.1–0.5 mm.
Bath carbonitriding (cyaniding)
- Performed in cyanide salt solutions (NaCN, KCN),
- A very fast process, but harmful to the environment (cyanide toxicity),
- Currently, it is less and less used and is often replaced by non-toxic cyaniding (e.g., using cyanates).
Ion carbonitriding
- A modern method is performed under vacuum conditions.
- Enables precise shaping of the diffusion layer.
- Used in the production of parts with complex geometries and precision requirements.
Other types of diffusion impregnation
In addition to carburizing, nitriding, and carbonitriding, several other thermochemical treatment processes involve impregnating the metal surface with various elements to achieve specialized properties, such as resistance to high temperatures, corrosion, erosion, or oxidation.
Each of these processes allows the surface layer to be adapted to very specific operating conditions where standard methods (such as hardening) prove insufficient. Their use often increases the service life and reliability of key components in equipment operating in extreme environments. The most important of these are presented below:
Diffusion chromium plating
This involves saturating the metal surface with chromium at a high temperature (900–1100°C). It is carried out in a gas atmosphere (e.g., chromium chlorides) or powder baths.
Diffusion chromium plating creates a layer of iron chromide, which is characterized by:
- very good corrosion and oxidation resistance,
- hardness and abrasion resistance,
- resistance to gases and aggressive chemicals.
Used in the chemical, petrochemical, and energy industries (e.g., boiler tubes, valves, reactor components).
Aluminizing (alumination)
A process of saturating a surface with aluminum, usually at a temperature of 800–1050°C. It leads to the formation of FeAl or Fe₃Al intermetallic compounds. Its main advantages include:
- high resistance to oxidation at high temperatures,
- protection against gas erosion and metallurgical slags,
- Improved resistance to corrosion under the influence of sulfur and chlorides.
Used in turbines, heat exchangers, boilers, and jet engines.
Boronizing (boriding)
Boronizing is a surface treatment that involves the diffusion of boron into the metal’s structure. Boronizing results in the formation of hard borides, such as FeB, Fe₂B, with a layer hardness of up to 1800–2000 HV. Boronizing is characterized by:
- excellent abrasion resistance,
- resistance to acids, alkalis, and brines,
- brittleness, which limits its use in dynamic components.
Used for: cutting tools, molds, dies, and friction elements.
Siliconizing
Siliconizing involves saturating the surface with silicon at a temperature of approximately. 1000°C. This results in the formation of iron silicides, which provide resistance to oxidation and high-temperature corrosion as well as increased hardness and fatigue strength. Used in metallurgy, in components exposed to high temperatures and contact with slag.
Thermal and chemical treatment of metals – summary
Thermal and chemical treatment are among the most important tools in materials engineering, enabling the targeted modification of metal surface properties without affecting their internal structure. Thanks to processes such as carburizing, nitriding, carbonitriding, and chromium plating, it is possible to achieve a combination of high surface hardness, ductility, and core strength.
These treatments increase resistance to wear, corrosion, fatigue, and high temperatures, which directly translates into a longer service life for machine and equipment components. The skilful selection of the process type, thermal parameters, and starting material enables engineers to optimize designs for their actual operating conditions.
Modern industry cannot function without precise surface modification methods – that is why thermochemical treatment remains not only an important scientific issue, but above all a practical tool for building the durability, reliability, and safety of technical structures.