Methods of testing material structure
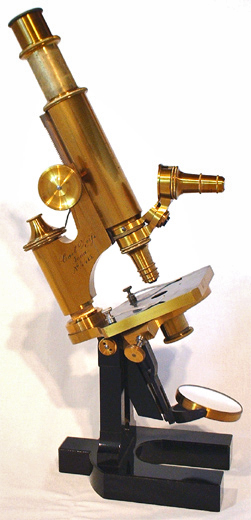
Table of contents
Although metals and their alloys are the foundation of modern technology, their properties do not result solely from their chemical composition, but equally from the internal structure of the material. It is how atoms are arranged, how crystal grains are formed, what defects occur in their network, and how the entire mass of material is organized on a macro scale that determines the behavior of metal during machining, operation, and even failure. For this reason, the study of the structure of metallic materials has become an integral part of the work of engineers, technologists, and quality specialists.
Structural analysis enables us to understand why one metal is hard yet brittle, while another is soft yet extremely ductile. Through observation and measurement, it is possible to assess the degree of material hardening, check the correctness of heat treatment, detect discontinuities and internal defects, and predict the behavior of a component under operating conditions. Furthermore, a proper interpretation of the structure enables the effective design of new alloys, the optimization of technological processes, and the extension of the service life of structures.
Structural research distinguishes several levels of description: crystal structure, i.e., the ordered arrangement of atoms in a crystal lattice; microstructure, comprising grains and phases visible under a microscope; and macrostructure, visible to the naked eye or under slight magnification, where the directions of fiber orientation, porosity, or casting marks are visible. These are complemented by modern non-destructive methods, which enable the internal condition of the material to be assessed without damaging it, a crucial aspect in the quality control of finished components.
In the following sections of the article, we will examine the most important research techniques used to analyze the structure of metal, both classic and modern, which enable a precise examination of the material and a deeper understanding of its properties.
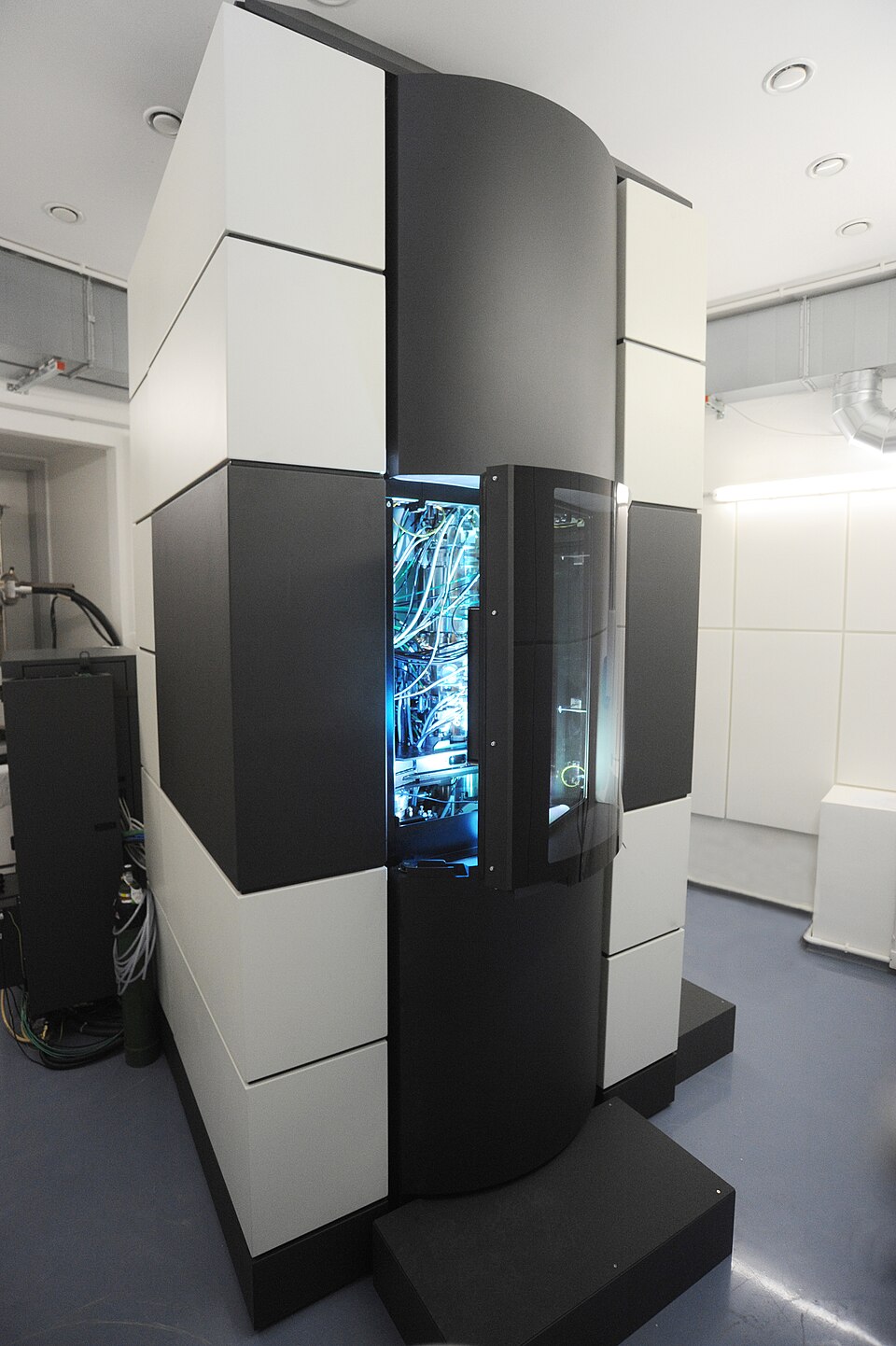
X-rays and electrons
The mechanical and technological properties of metals are based on their crystalline structure, i.e., the arrangement of atoms in space. Although invisible to the naked eye, it determines such fundamental properties as density, thermal conductivity, thermal expansion, and susceptibility to deformation. To investigate this atomic order, science and technology employ one of the most precise physical methods: X-ray diffraction, and to a lesser extent, electron diffraction.
When a beam of X-rays hits a metal sample, its waves are scattered on regularly spaced atomic planes inside the crystal. This produces a characteristic diffraction pattern—a pattern of lines or spots—which can be recorded and analyzed. This phenomenon is described by the Bragg equation, which relates the angle of deflection of the rays to the distances between the planes of the crystal lattice. This enables the determination of the unit cell parameters, identification of the phases present in the material, and detection of internal stresses and the degree of deformation of the structure.
This technique, known as X-ray diffraction analysis (XRD), is used to study product corrosion in both scientific research and industrial control. For example, it is used in the identification of product corrosion, the evaluation of heat treatment effectiveness, and the examination of tool surface wear. A simplified, though less precise, version is the diffraction photograph taken in a photographic chamber using the Debye-Scherrer method.
Classical diffraction is complemented by electron analysis, which can be performed in specialized transmission microscopes. Thanks to their much shorter wavelength, electrons allow much smaller objects to be examined than X-rays. Electron diffraction observations enable the analysis of local crystal orientation on the scale of individual grains or layers, which is often crucial in thin-film and nanostructured materials.
Both X-rays and electrons are, therefore, a gateway to a world that cannot be seen directly. Their precise interaction with matter allows the study not only of crystal order, but also of defects, lattice dislocations, and the presence of stresses. In this way, diffraction techniques become the basis for materials engineering at the atomic level, where the real design of material properties begins.
Metallographic microscopy
Although the crystal structure determines the properties of metals at the atomic level, in engineering practice, it is equally important to analyze their microstructure – i.e., the mutual arrangement of grains, phases, boundaries, and possible discontinuities on a micrometer scale. To achieve this, metallographic microscopy is employed, which enables the observation of the surface of appropriately prepared samples in reflected light.
The basis of this test is the preparation of a so-called metallographic specimen – a smooth, polished surface of the sample, which is subjected to chemical etching. This process reveals grain boundaries and differences between phases due to varying degrees of reaction with the etching agent. The prepared surface is then observed under an optical microscope, which allows for magnifications of several hundred times, sufficient to assess grain size, the shape of non-metallic inclusions, and the nature of phase transformations.
One of the breakthroughs in this field was the construction of a metallographic microscope by Le Chatelier, which enabled the observation of reflected light on opaque surfaces, such as metals. To this day, these types of microscopes are a basic tool in quality control laboratories, research and development departments, and technical universities. They enable the examination of whether a material has a uniform structure, whether thermal and mechanical processes have been carried out correctly, and whether any hazardous defects are present.
Despite its limited resolution compared to electron microscopy, light microscopy has a significant practical advantage – it is relatively fast, inexpensive, and allows for the evaluation of a large sample area. This makes it indispensable for analyzing high-volume manufacturing, where the speed of diagnosis and repeatability of results are crucial.
Microstructural observations enable the classification of metals based on their thermal and technological history, the evaluation of the effectiveness of heat treatment, and the analysis of the state of deformation or the degree of material disintegration. Metallographic microscopy, therefore, opens the way to understanding what lies beneath the surface of metal – and often determines its success or failure under operating conditions.
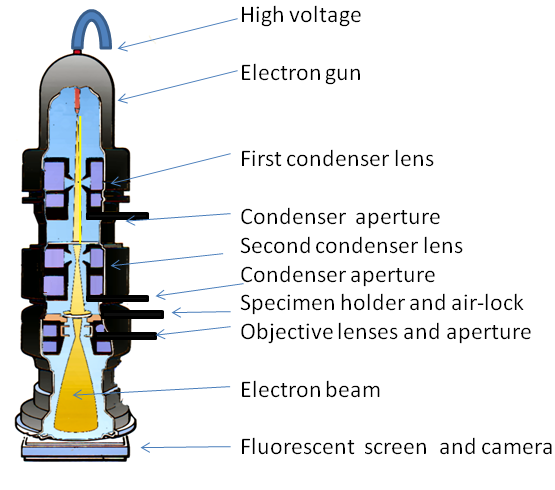
Electron microscopy
When detail beyond the capabilities of light microscopy is required, electron microscopy is used – a technique that allows the structure of a material to be analyzed with nanometer accuracy, or even down to individual atoms. Unlike visible light, whose wavelength limits the resolution of conventional microscopes, an electron beam, thanks to its much shorter wavelength, provides insight into the finest details of metal structure, including grain boundaries, phase dispersions, network defects, and fracture patterns.
The principle of operation of an electron microscope is based on the emission and focusing of electrons onto the surface of a sample under high-vacuum conditions. Depending on the device’s design, there are two main types: scanning electron microscope (SEM) and transmission electron microscope (TEM). The former allows for imaging of the topography and chemical composition of surfaces. At the same time, the latter enables the X-ray imaging of thin metal foils, yielding a detailed image of the internal structure.
In SEM, the electron beam moves linearly across the sample surface, and detectors register the reflected or secondary electrons. The resulting image is characterized by high depth of field and high resolution, which allows the study of fracture morphology, sintered structures, wear surfaces, and micro-teeth formed as a result of machining. In addition, integrated microanalysis systems, such as EDS (Energy-Dispersive Spectroscopy), enable the determination of the chemical composition of the examined sample fragments, making this technique extremely versatile.
TEM, in turn, offers even higher resolution, allowing imaging of the crystal lattice, atomic misalignments, and the presence of point defects. Since the sample must be very thin, its preparation is more complex, but the results are incomparably more precise. This allows for the study of phenomena occurring at phase boundaries, in reinforced areas, or after diffusion processes.
Electron microscopy has opened up a whole new dimension in materials diagnostics, allowing not only the quality of products to be assessed, but also the mechanisms of their degradation and failure to be understood. Modern devices of this class are capable of performing microstructural, spectroscopic, and phase analysis simultaneously, which makes them a key tool in modern materials engineering, especially in the fields of special alloys, nanomaterials, and thin-film functional systems.
Macroscopy
Although advanced research techniques enable us to examine the material with remarkable accuracy, the importance of macroscopy, i.e., observing metal on a scale visible to the naked eye or at low magnifications, cannot be overstated. This is often where material diagnosis begins, as much of the key information about the quality, origin, and technological history of a metal is contained in its macrostructure.
Macroscopy enables the assessment of visible features without the need for microscopic analysis, including porosity distribution, fiber orientation in forged materials, the course of casting zone boundaries, the presence of cracks, delamination, or so-called primary defects that arise during the manufacturing stage. With proper preparation of the sample surface – by grinding, etching, or breaking – it is possible to reveal large structures, such as dendrites, phase transition zones, or scale distribution.
Particularly valuable information is provided by the observation of fractures – surfaces formed as a result of a crack in the element. Depending on the nature of the material and the mechanism of damage, the fracture may have different characteristics: it may be shiny and grainy in the case of a brittle fracture, or dull and fibrous in the case of a ductile fracture. This analysis, often performed as part of fractographic testing, enables the identification of the type of damage, its origin, and the possible presence of material inhomogeneities that may have contributed to the failure.
In industrial practice, macroscopy plays an important role in the quality control of castings, forgings, sheet metal, and welds. It is also indispensable in the analysis of damage to components operating under variable loads, where it is crucial to identify the source of crack initiation. In combination with photographic documentation, macroscopic observations become not only a diagnostic tool, but also evidence in the analysis of failure causes.
Although it may seem to be the simplest of research techniques, macroscopy often provides the first and most direct clues that guide further, more detailed micro- and submicroscopic investigations. Macroscopy allows us to quickly determine whether the material under investigation requires further analysis or whether its structure is satisfactory.
Non-destructive methods
In situations where maintaining the integrity of the material is an absolute requirement and removing or damaging the sample is unacceptable, non-destructive methods, also known as NDT (Non-Destructive Testing), are used. These techniques enable the assessment of material quality, the detection of internal and surface defects, as well as the verification of the structure’s compliance with design requirements, without the need to damage the tested element.
One of the most commonly used non-destructive methods is radiographic testing, which uses X-rays or gamma rays. These rays penetrate the material, and their attenuation depends on the density and thickness of the internal structures. These differences are recorded on special inserts or digital sensors, which allow an image of the material cross-section to be obtained. This method can detect air bubbles, shrinkage cavities, discontinuities, and non-metallic inclusions that could weaken the structural strength of the component.
Another commonly used technique is ultrasonic testing, in which high-frequency sound waves are passed through the material. Any discontinuities, such as cracks, delamination, or voids, cause the wave to reflect or refract, which can be easily recorded on the measuring device’s screen. Ultrasonic testing is highly accurate, fast, and safe, making it suitable for inspecting thick and complex components.
Magnetic particle testing is very useful for ferromagnetic materials. It involves creating a magnetic field in the tested element and applying fine ferromagnetic particles to its surface. In the presence of defects, such as scratches or surface cracks, the magnetic field lines are disrupted, causing a local accumulation of particles that allows the defect to be easily identified visually.
All these methods share a common advantage: they enable complete diagnostics of a material or product without destroying it, which is crucial not only in the quality control phase but also during periodic maintenance inspections. They are successfully used in the aerospace, energy, petrochemical, and automotive industries, as well as wherever structural safety and operational reliability are a priority.
Non-destructive methods are now an indispensable part of quality management systems, allowing potential hazards to be detected promptly before costly failures occur. They are a testament to technological progress, which allows the interior of a material to be assessed with the same effectiveness as if it were transparent, without the need to interfere with its structure.
Methods of testing material structure – summary
Understanding and controlling the internal structure of metals is one of the most important tools available to materials engineers today. It is crystal, microstructural, macroscopic, and non-destructive analysis that allows us to fully understand how a material will behave in real conditions – under load, in contact with chemical agents, during intense friction, or at varying temperatures.
This knowledge is crucial not only in the design of new materials, but also in their verification, evaluation of the manufacturing process, and even in the investigation of damage causes. Thanks to the use of a variety of testing methods – from X-rays to electron microscopes and ultrasound – it is possible to obtain a comprehensive picture of the material, ranging from the atomic level to macroscopic features visible to the naked eye.
Each of the techniques discussed plays a specific role, and their complementarity allows not only to locate defects, but also to predict their effects and avoid them in the future. As a result, modern materials research is becoming the basis for responsible engineering, one that relies not only on intuition or experience, but on verifiable data and precise diagnosis.
In a world where the safety, durability, and quality of structures have a direct impact on human life and the environment, understanding the interior of metal is not a luxury,but a necessity.