Industry 4.0 – what is it, and what does it mean for the CNC industry?
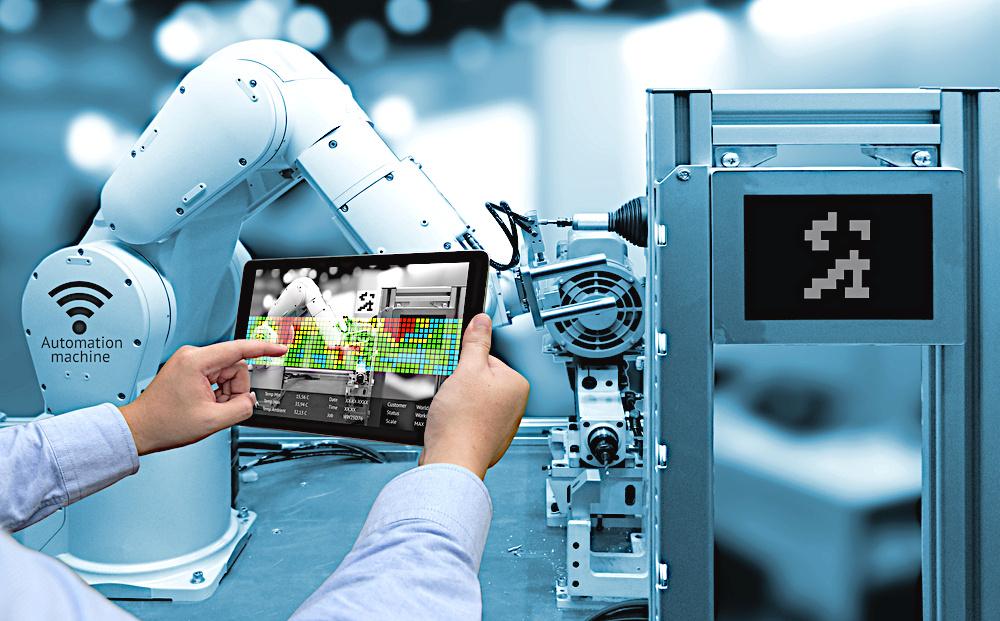
What is Industry 4.0?
Industry 4.0, or Smart Industry, as it is also called, is a hot topic in the manufacturing industry. What will it mean for the CNC machining market? Why does it matter for the future of the metal machining industry?
Industry 4.0, or Smart Industry, is an industry focused on automation. The defining feature is the attempt to replace human thought processes with automated systems. People call it the digital revolution for a reason. Information and communication technologies are being rapidly integrated into the production process – from design to distribution – as new product technologies appear on the market.
Organizations, machinery, and other production resources are progressively undergoing digitization. This is leading to so-called intelligent factories. Processes, people, and machines are constantly connected, doing work faster and smarter. It is affecting the entire manufacturing industry. This, of course, applies to CNC machining workplaces. The metal machining sector on CNC machines is particularly susceptible to implementing Industry 4.0 tools because of the large amounts of digital data available to today’s numerically controlled machine tools.
Industry 4.0: The Fourth Industrial Revolution
At the end of the 19th century, the world was confronted with the first industrial revolution. The invention of the steam engine is emblematic of the far-reaching industrial changes that affected Europe at the time. For the first time, continuous mechanical power was possible. Hydropower and mechanics made manual and labor-intensive manufacturing processes faster and more efficient. In about 150 years, the second and third industrial revolutions made this possible. These were heralded by mass production and the introduction of robots, respectively.
In the 21st century, we are facing the fourth industrial revolution: Industry 4.0. Thanks to the rise of the Internet and the radical development of the so-called Internet of Things, people and technology are increasingly connected. At the core of this process is the wireless sharing and collection of data. This is not only true for the refrigerator and the TV; it is especially true for industrial equipment, business operations, and precision parts manufacturing processes.
We are collecting more and more data, and software is getting smarter. The result is intelligent cooperation between automation, information systems, and production systems. In short, everything is connected. We can rightly refer to the network society, a term coined by Dutch professor Jan van Dijk. it is more than just a clever marketing term: the fourth industrial revolution has begun.
Autonomous robots: an essential part of Industry 4.0
For some time, manufacturers in various sectors have been using robots to perform complex tasks. The current revolutionary changes in robotics are emblematic of the changes in the CNC machining industry, which reflect Industry 4.0. Robots are becoming more autonomous, more flexible, and more willing to cooperate. What’s more, they are increasingly connected to each other and to other machines.
These connections are becoming more reliable and secure. This also means that robots are increasingly interesting to the precision machining industry. For example, robots loading CNC machine tools offer a wide range of functions not so long ago out of reach. The use of collaborative robots in CNC milling and CNC turning operations is becoming more common, both for loading and unloading machine tools but also for performing additional operations. Additional operations in CNC machining processes include measuring workpieces, cleaning, sorting, packing, and many others.
How will Industry 4.0 change production in CNC machining plants?
It is bringing about new production methods, business models, and sectors. What was a year ago can now be considered obsolete. All of these innovations characterize intelligent manufacturing processes. For example, machines are capable of working autonomously. This allows continuous optimization of production processes.
Flexibility is another critical concept characterizing these changes in the precision manufacturing industry. Products with different specifications are being produced in different quantities and with varying lead times in a fully automated process. Apart from accommodating a broader range of products, this system also performs tasks such as cleaning, deburring, turning over, or clamping within the same setup.
In the era of Industry 4.0, your machines will have the capacity to establish seamless communication with automation solutions, delivering ongoing status updates. This applies to both immediate concerns like current production tasks and longer-term issues such as identifying components with signs of wear. This leads to a highly efficient, predictable, and consequently more profitable production process.