Heat treatment of metals
Table of contents
Controlled material transformation
In the world of materials engineering, it is not only the type of metal used to manufacture a given component that is crucial, but also how it has been transformed at the level of its internal structure. One of the most essential tools for this transformation is heat treatment, a set of technological processes that involve the controlled heating and cooling of metals or their alloys to alter their mechanical, physical, and sometimes chemical properties.
What makes heat treatment so unique is that it does not change the shape or chemical composition of the metal. Instead, it directly affects the internal structure of the material – the arrangement of atoms, the presence and nature of phases, and crystal defects. In practice, this means that it is possible to increase hardness, improve wear resistance, and enhance impact strength, thereby giving the material properties that cannot be achieved through chemical or mechanical processing.
However, heat treatment processes are not random. Their effectiveness depends on precise control of temperature, the time spent in a given temperature range, and the cooling rate. The changes that occur in the material during these stages are closely related to phase transformations and recrystallization, which determine the new, desired structure. Furthermore, heat treatment often prepares the material for subsequent processes, such as hardening, carburizing, sintering, or welding, and is crucial for the durability and reliability of the finished product.
Understanding the principles governing heat treatment allows materials to be designed not only in terms of their composition, but also their internal architecture. It is thanks to heat treatment that steel can be both flexible and rigid, resistant to abrasion, or capable of absorbing shocks, depending on how it has been treated with fire and time.
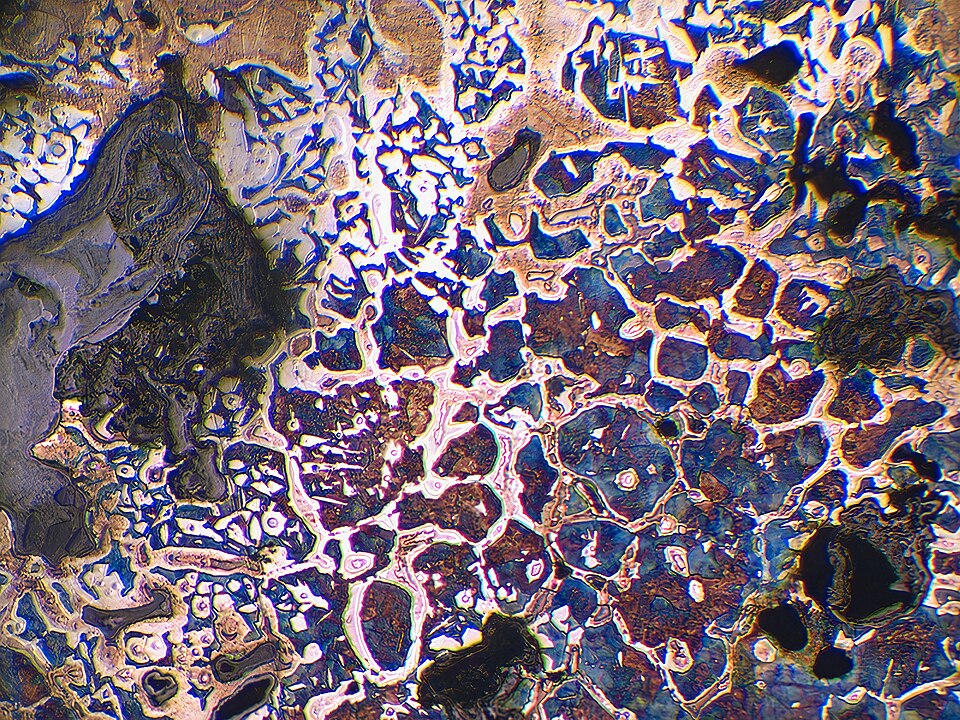
Stages of the heat treatment process
Heat treatment is a process that, although it may seem simple, is based on a precisely planned sequence of stages, each of which influences the final structural and functional properties of the material being treated. To achieve the desired technological goal, it is necessary to understand how and why each of these steps leads to a change in the metal’s properties.
The first and indispensable stage is heating the material to a strictly defined temperature. It is not just a matter of supplying heat energy – it is the temperature that determines whether and what phase changes will occur in the crystal structure. In the case of steel, this may mean a transition from ferrite to austenite, the start of the carbide dissolution process, or the activation of diffusion. It is not only crucial to reach the desired temperature, but also how we get there – heating too quickly can lead to thermal stresses, cracks, or structural inhomogeneities.
Once the correct temperature has been reached, annealing occurs, i.e., the material is maintained within a set temperature range for a specified period. This stage enables the achievement of a state of phase equilibrium and the completion of internal transformations. The tempering time must be adjusted according to the type of material, the thickness of the element, and the purpose of machining. Too short a time may result in incomplete transformations, while too long a time may lead to undesirable grain growth or structural degradation.
The last and one of the most crucial moments in the entire process is cooling. Its speed and course determine the structure that will form in the material after it leaves the high-temperature zone. Slow cooling can lead to the formation of pearlite or ferrite, whereas rapid cooling can result in the hardening of the metal and the formation of a martensitic structure. In this sense, cooling is not just the end of the process, but its culmination, which determines the final properties of the alloy.
All these stages – heating, soaking, and cooling – must be treated as a whole, precisely tailored to the material and functional requirements of the product. Their interrelationships make heat treatment not only an art, but above all a science of controlled internal transformation of metal.
The importance of heating and its parameters
Although the heat treatment process appears to begin when the material’s temperature is raised, heating itself is more important than just achieving the required temperature. This is the stage at which fundamental internal changes begin, influencing the further course of structural transformations. The method of heating determines not only the effectiveness of the entire process, but also the quality, uniformity, and safety of the workpiece.
The most critical parameter, of course, is temperature – it determines whether the material will enter the phase transformation range and how deeply these transformations will develop. In the case of steel, different temperature ranges determine whether ferrite transforms into austenite, whether cementite begins to dissolve, or whether recrystallization processes are activated. Each type of steel has a different critical temperature range, and exceeding this range, either upwards or downwards, can result in significant changes in mechanical properties.
Just as important as the temperature itself is the rate at which it is reached. Heating too quickly can lead to large temperature gradients between the surface and the core of the component, which promotes the formation of internal stresses, microcracks, and, in extreme cases, even deformation. On the other hand, raising the temperature too slowly can be uneconomical and unnecessarily prolong the production process. Therefore, engineers often choose compromise solutions – using controlled zone heating, stage heating, or protective atmospheres.
The uniformity of temperature throughout the component is also essential. In the case of large forgings, long shafts, or thin-walled profiles, temperature differences within different parts of the material can lead to heterogeneous phase transformations, resulting in a deterioration of mechanical properties or local stress concentrations. For this reason, furnaces used for heat treatment are equipped with precise measuring and control systems that maintain a stable heat distribution inside the heating chamber.
Heating is therefore not just the first step in the process – it is the moment when conscious interference with the structure of the material begins. Its proper execution requires not only knowledge of the technological parameters, but also an understanding of the physics of the phenomena involved – from atom diffusion to the initiation of crystalline transformations.
The role of annealing
If the heating temperature determines the conditions under which structural changes can occur, then the annealing time determines whether these changes will reach their full development. The annealing stage, although often underestimated, is one of the most crucial moments in heat treatment – it is what enables the material’s structure to stabilize in its new state and achieve the desired performance properties.
Annealing involves maintaining the metal at a constant temperature for a specified period, typically the temperature at which significant phase transformations occur. During this period, diffusion phenomena intensify: atoms of different elements move within the crystal lattice, equalizing the distribution of chemical components, dissolving previous precipitates, or forming new secondary phases. In the case of steel, this can be the dissolution of carbides in austenite, chemical homogenization, or stabilization of newly formed structures.
The length of the annealing must be selected individually for the type of material and the purpose of machining. For some processes, a few minutes are sufficient, while for others, especially with large cross-sections, the time can be up to several hours. A too short time may result in transformations not occurring throughout the entire volume of the material or being incomplete, leading to an uneven microstructure and heterogeneity of properties. On the other hand, excessively long annealing can lead to undesirable grain growth, reduced strength, and decreased resistance to fatigue cracking.
Annealing is also the moment when the internal structure “matures” – the crystal lattice is reconstructed, internal stresses are reduced, new phases are stabilized, and lattice defects are dispersed. This process, although invisible to the naked eye, determines whether hardening, annealing, or over-saturation will bring the expected results or end in failure.
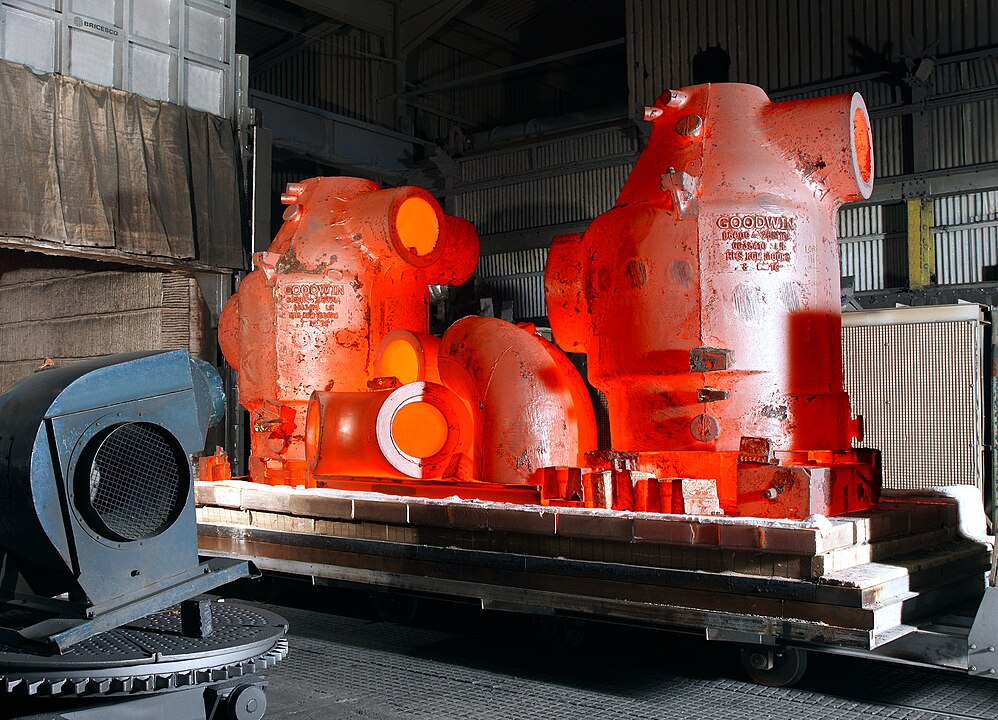
Cooling
Although the cooling stage occurs at the end of the heat treatment process, its importance cannot be underestimated. It is during cooling that the material’s final microstructure is established, which determines its ultimate mechanical properties. It can be said that all previous steps – heating and annealing – prepare the ground for what is decided in this one critical phase: how quickly and how the material releases heat.
The cooling rate determines which phases will have a chance to form and which will be “frozen” in a transitional state. Rapid cooling, typical of the hardening process, stops diffusion transformations and leads to the formation of metastable structures, such as martensite – a harsh but brittle atomic structure. This approach significantly increases the material’s hardness, but requires subsequent tempering to restore its minimum plasticity and resistance to cracking.
Slow cooling, used for example during annealing, allows phase transformations to proceed smoothly, leading to the formation of structures such as pearlite, ferrite, or sorbite. These systems, although less complicated, are characterized by greater homogeneity and resistance to variable loads, which makes them more suitable for components operating under long-term stress.
The method of cooling is also essential – whether it occurs in air, water, oil, or a controlled gas atmosphere. Each of these environments offers a different intensity of heat transfer and thus influences the kinetics of phase transformations. Furthermore, the choice of cooling medium also affects the risk of deformation, cracking, or oxidation of the workpiece’s surface.
In this sense, cooling is not just a mechanical process of heat removal – it is an active stage in the formation of the metal structure, which requires the same precision and planning as the other phases of heat treatment. Its course determines whether we obtain a hard, resilient material that is suitable for further machining or one that is too brittle and prone to failure.
Types of atmospheres used in heat treatment
Many heat treatment processes occur at elevated temperatures, where the metal surface becomes particularly sensitive to its surrounding environment. Under such conditions, even brief contact with air can lead to oxidation, decarburization, carburization, or absorption of harmful gases, which adversely affect the quality, appearance, and properties of the product. Therefore, the selection of the appropriate furnace atmosphere in which the heat treatment process occurs plays a crucial role.
One of the most commonly used solutions is the use of protective atmospheres, designed to limit chemical reactions between the metal and its environment. These can be inert gases, such as argon or nitrogen, which do not react with the material being processed, or mixtures of reducing gases, such as hydrogen and nitrogen, which additionally counteract oxidation. Such atmospheres are used wherever it is crucial to maintain a clean metal surface, for example, in the machining of tool steels, stainless steels, or special alloys.
In processes aimed at altering the chemical composition of a material’s surface layer, active atmospheres saturated with the appropriate elements are used. In the case of carburizing, these are mixtures rich in hydrocarbons, such as methane or propane, which supply carbon atoms to the steel surface, enabling the formation of diffusion-hardened layers. Similarly, atmospheres containing ammonia are used for nitriding processes, and gases containing boron hydrides are used for boriding. These types of treatments, which combine heat treatment with chemical treatment, enable a significant improvement in abrasion and corrosion resistance without requiring a change to the entire volume of the material.
Some modern technologies also use a technological vacuum as a heat treatment environment. Thanks to the complete removal of air and active gases, it is possible to carry out processes in completely neutral conditions, which is particularly important in the manufacturing of precision aerospace machined parts, surgical tools, or electronic components. Vacuum furnaces also enable precise temperature control and eliminate gas impurities that could affect the material’s microstructure.
Heat treatment of metals – summary
Although heat treatment has been used in the metallurgical industry for centuries, it remains a modern and dynamic field. Modern technologies no longer treat it as a simple way to harden or stress-relieve metal – today, it is a precise engineering tool that allows the microstructure of materials to be consciously shaped in a predictable, repeatable, and application-specific manner.
Understanding how temperature, time, and the thermal environment affect phase transformations and the distribution of atoms in the crystal structure allows us to design not only the mechanical properties, but also the chemical resistance, thermal conductivity, dimensional stability, and fatigue life of a material. It is thanks to heat treatment that steel can become both complex and resilient, and that an element made of a seemingly simple metal can acquire properties similar to those of composite materials.
In the age of advanced technologies – from the aviation industry to energy and medicine – the control of thermal processes with accuracy down to single degrees, minutes, and even atoms is also becoming increasingly important. High-temperature simulations, protective atmospheres, heat gradient control, and the use of technological vacuum allow us to achieve a level of quality that was unattainable just a few decades ago. Heat treatment is no longer a secondary stage – it has become a central element of material design.
That is why knowledge of thermal processes, their course, and their impact on the properties of metals is one of the pillars of modern materials engineering today. It is not enough to know the chemical composition of an alloy – you need to understand how to “burn” the best out of it.