Deformation and recrystallization of metals
Table of contents
Metals, as materials with a crystalline structure, can permanently change shape under the influence of external forces. This phenomenon, known as deformation, forms the basis of plastic working, a key technolóogical process in metallurgy and materials engineering.
In industrial practice, metals are subjected to various types of deformation, ranging from elastic deformation, which disappears when the load is removed, to plastic deformation, which results in a permanent change in the material’s dimensions and internal structure. It is this ability to undergo plastic deformation that allows metals to be rolled, drawn, bent, or forged without being destroyed.
The process of metal deformation is associated with significant changes in its internal structure, particularly at the level of the crystal lattice. This results in structural defects, such as dislocations, which, on the one hand, enable slippage and deformation, and on the other hand, lead to strengthening of the material. However, excessive crushing can result in a loss of plasticity and reduced resistance to further processing.
To restore the metal to its original properties, a recrystallization process is employed, which involves transforming the deformed structure into a new, ordered crystal structure, thereby regaining the plasticity and beneficial properties.
Understanding the mechanisms of deformation and recrystallization is crucial not only for designing technological processes but also for predicting the behavior of materials under operating conditions. This article explores both the theoretical foundations and practical applications of these phenomena, ranging from the atomic level to industrial settings.
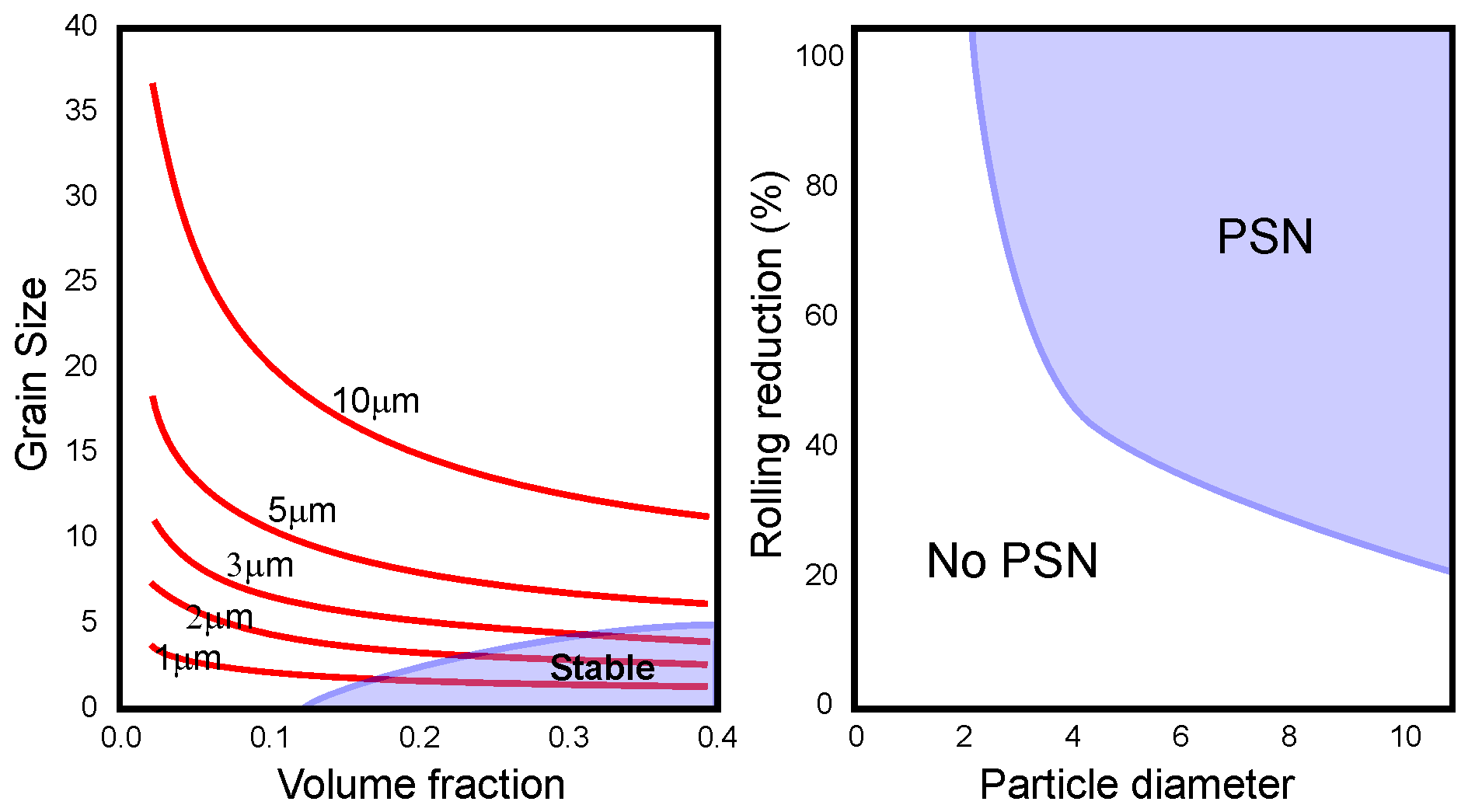
Elastic and plastic deformation
Under the influence of external forces, metal changes shape and dimensions. Depending on the magnitude and duration of these forces, we distinguish between two basic types of deformation: elastic and plastic.
Elastic deformation
Elastic deformation is a temporary deformation that disappears after the load is removed, meaning that the material returns to its original shape and dimensions. At the atomic level, there is a change in the distance between atoms in the crystal lattice, without its permanent transformation. Under tensile forces, the lattice cells elongate, while under compressive forces, they shorten.
In the range of elastic deformation, there is a linear relationship between stress and relative deformation, described by the formula:
\[ \sigma = E \,\cdot\,\epsilon\]
- \(\sigma\) – stress,
- \(\epsilon\) – relative deformation,
- \(E\) – longitudinal elastic modulus (Young’s modulus).
Young’s modulus is a measure of a material’s stiffness – the higher its value, the faster the stress increases with increasing deformation. It depends on the type of metal, the type of crystal lattice, and the direction of the load (especially in single crystals).
In addition to axial stresses, materials may also experience tangential (shear) stresses, which cause the layers of atoms to move relative to each other. Such deformation can also be elastic and is measured by the transverse elastic modulus.
Plastic deformation
When the force exceeds the so-called elastic limit, the material begins to deform permanently – this is plastic deformation. After the load is removed, the sample does not return to its original shape, and the changes in the crystal structure are irreversible.
Plastic deformation occurs mainly in two ways: by slipping – the displacement of parts of the crystal relative to each other along the so-called easy slip planes, where the metal offers the least resistance, and by twinning – the transformation of part of the crystal into a mirror image of the other part, particularly common in metals with a hexagonal or FCC lattice.
The plasticity of a metal is closely related to its crystal structure – the more planes and directions of easy slip there are, the greater the plastic deformation capacity. For example, in an FCC structure (e.g., aluminum), slip occurs more easily than in a hexagonal structure (e.g., zinc, magnesium).
The ability to undergo plastic deformation determines the technological shaping possibilities of a metal, but also influences the distribution of internal stresses, the formation of crystallographic texture, and further strength properties of the material.
Microscopic mechanisms of deformation
The process of plastic deformation of metal does not involve the uniform displacement of entire fragments of the material. This phenomenon occurs at the microscopic level through the local displacement of atoms along specific planes and directions, with its main mechanisms being slip and twinning.
Crystal slip
Slip involves the displacement of parts of a crystal relative to each other along so-called easy slip planes, i.e., those with the highest atom density and the lowest resistance to dislocation movement. This phenomenon occurs when the shear stresses in these planes exceed the critical shear stress.
The slip planes and the directions in which the material moves depend on the crystal lattice structure. The more such structures there are, the greater the metal’s plasticity. This is why aluminum is very ductile and magnesium, for example, is relatively brittle.
Shear does not affect the entire crystal at once – it starts locally and then spreads along the lattice. In places where shear has occurred, characteristic shear lines or bands form, which are visible under a microscope.
Twinning
The second possible mechanism is twinning, which involves part of the crystal being oriented as a mirror image of the other part relative to a specific plane, known as the twin plane.
This process occurs particularly easily in metals with a hexagonal structure and some FCC metals (e.g., copper, silver) at low temperatures or during rapid deformation. Twin formation allows deformation where slip is limited, which is why it plays a special role in metals with a small number of easy slip systems.
Dislocations and the theory of actual slip
Although it was believed for many years that slip requires the displacement of entire planes of atoms at once, research has shown that the actual stresses required for such a displacement would be thousands of times greater than those observed in practice.
The solution to this contradiction was found in dislocation theory. According to this theory, slip occurs through the movement of dislocations – linear defects in the crystal structure. Instead of the simultaneous movement of the entire plane of atoms, the deformation proceeds in stages, as if a “wave of deformation” were moving through the crystal.
Dislocations can move relatively easily, but their movement is hindered by obstacles such as other dislocations, grain boundaries, impurities, or secondary phase particles. As their number increases, a strengthening effect occurs, resulting in increased resistance to further slip.
Crushing and strengthening
During plastic deformation, especially under cold working conditions, the metal’s structure undergoes significant changes. This process, known as crushing, involves permanent deformation of the metal, accompanied by an increase in the density of dislocations and other network defects. These changes have a significant impact on the material’s properties, both mechanical and physicochemical.
Crushing
As crushing increases:
- The number of dislocations begins to increase, forming complex, irregular meshes,
- At higher deformations (10–25%), continuous walls form, surrounding areas with fewer defects – so-called cells,
- Further deformation leads to a concentration of dislocations in the walls and changes in the shape of the cells.
As a result, the metal’s structure becomes severely distorted, and its ability to undergo further deformation is reduced. Other properties of the metal also change: electrical conductivity decreases, coercivity and residual magnetism increase, solubility in acids increases, and density decreases while specific volume increases.
Crushing not only changes the shape of grains but also changes their spatial orientation, leading to the formation of a so-called deformation texture – a structural arrangement characteristic of a specific direction of deformation (e.g., rolling, drawing).
Hardening of metal
An increase in dislocation density leads to a phenomenon known as hardening. This consists of the fact that the movement of subsequent dislocations is increasingly impeded by existing obstacles (other dislocations, grain boundaries, inclusions), so that increasingly greater forces are required to continue the deformation.
The effects of strengthening are visible in the properties of the metal: the yield strength increases, while the tensile strength and hardness also increase; conversely, plastic properties such as elongation, necking, and impact strength decrease.
These phenomena have been illustrated, for example, in studies of pure iron, where a significant increase in strength was observed, along with a decrease in ductility, with increasing degree of crushing.
Recrystallization
After intense plastic deformation, the metal structure is characterized by a high density of defects, primarily dislocations and crystal lattice distortions. Such material is in an energetically unstable state, with a much higher internal energy than cast or annealed metal. To restore its original properties, a recrystallization process is carried out, which involves heating the metal to restore its correct crystal structure.
Stages of the recrystallization process
- Healing occurs at relatively low temperatures (e.g., for iron, approx. 300–400°C), point defects diffuse, opposite dislocations are annihilated, and dislocations are rearranged; the structure does not change visibly under a microscope, but the physical (e.g., conductivity) and mechanical properties improve slightly.
- Polygonization – dislocations are rearranged, forming so-called subgrain boundaries. Areas with slightly different crystal orientations are formed, which reduce the internal energy of the material. This is a form of internal rearrangement leading to structural stabilization, but without complete grain reconstruction.
- Primary recrystallization begins above the so-called recrystallization temperature, in areas with high dislocation density. New grain nuclei, free of defects, are formed; these nuclei grow at the expense of the deformed structure until it is completely replaced. The metal regains its plasticity and homogeneity.
- Grain growth – after recrystallization, the grains can continue to grow, and spontaneous enlargement of large grains at the expense of small ones occurs, which reduces the total grain boundary area and thus the energy of the system. Under uncontrolled annealing conditions, abnormal grain growth may occur, resulting in the formation of single, very large grains, which are undesirable in structures requiring high strength.
Recrystallization increases the plasticity of the metal, restores its mechanical and technological properties, makes the material more homogeneous and predictable, and reduces internal stress and brittleness. This process is used in practice as so-called recrystallization annealing, which is necessary, for example, in drawing, rolling, bending, and other plastic operations, both between operations and at the end of the processing.
Temperature and factors influencing recrystallization
The recrystallization temperature is the lowest temperature at which, within one hour, complete restoration of the structure deformed by crushing occurs. This value is not constant – it depends on several factors, including the material, the size of the crushing, the purity of the metal, and the cooling method. For most pure metals, the recrystallization temperature ranges from 0.3 to 0.5 times the melting point (expressed in Kelvin).
Controlling the recrystallization conditions enables the microstructure to be tailored to meet technological requirements, enhances the ductility of the material before further processing, and achieves the desired grain size, which in turn affects properties such as hardness, fatigue resistance, and electrical conductivity.
However, excessively high temperatures or prolonged annealing times can lead to excessive grain growth, which weakens the metal and impairs its properties; therefore, the recrystallization process requires precise selection of parameters.
Factors affecting the recrystallization temperature
- Degree of deformation – the greater the deformation, the greater the dislocation density, the more sites for new grain nucleation, and thus the lower the temperature required for recrystallization. With very low deformation (below 5-10%), the recrystallization process may not occur at all.
- Chemical purity of the metal – pure metals recrystallize more easily and at lower temperatures; the presence of impurities (e.g., carbon, sulfur, phosphorus) hinders grain boundary movement, thereby increasing the recrystallization temperature.
- Grain size before deformation – metals with a fine-grained structure before deformation have more boundaries, which facilitates nucleation, while coarse-grained structures require greater overheating.
- Cooling rate after deformation – slow cooling promotes healing and polygonization, followed by recrystallization, while rapid cooling (quenching) can stop the transformation process, leaving a crushed structure.
- Deformation texture and internal stresses – areas with intense crushing or unfavorable crystallographic orientations recrystallize faster. Some grain orientations may cause preferential growth, leading to the formation of a recrystallization texture.
Material destruction
Metal destruction is the final stage of its mechanical work – the moment when the material loses its continuity and ceases to fulfill its structural function. Depending on the load conditions, temperature, internal structure, and type of material, destruction can occur in two basic ways: as brittle scrap or ductile scrap.
Brittle scrap
Brittle scrap occurs when the material breaks suddenly without prior plastic deformation. It is characterized by: no elongation or narrowing of the sample, a flat fracture surface, often with characteristic shell-like patterns, a loud, “glass-like” fracture, and a high fracture propagation speed.
This mechanism dominates in metals with low plasticity (e.g., cast iron, some hardened steels), particularly at low temperatures, under dynamic or impact loads, and in the presence of defects, notches, and pre-existing cracks, which act as stress concentrators. Brittle scrap is transcrystalline (through the grains) or intercrystalline (along the grain boundaries) in nature, depending on the microstructure and impurities present.
Shear (ductile) scrap
Shear scrap occurs in materials that undergo significant plastic deformation before breaking. Its characteristics include significant elongation of the sample, narrowing at the point of breakage (known as the neck), a fracture surface with a rough, fibrous structure, and destruction resulting from dislocation creep and the growth of microcracks.
This type of failure is characteristic of soft and easily deformable metals (e.g., copper, aluminum) that work at room or elevated temperatures, and under static or slowly increasing loads. Shear failure can be considered “safer” because it gives a warning signal – deformation – before the material breaks completely.
The type of failure depends on many factors, including temperature – lower temperatures promote brittleness, load rate – the faster, the greater the risk of brittle fracture, structure and chemical composition – impurities can cause intergranular brittleness, presence of surface defects – promote failure without deformation, and duration of stress – prolonged loading can lead to creep and failure at low stress levels.
Mechanical property testing of metals
To assess how a metal will behave under mechanical loads, it is necessary to conduct appropriate laboratory tests to determine its strength, ductility, hardness, and resistance to fracture and creep. The results of these tests are the basis for selecting a material for a specific technical application.
Tensile test
One of the basic tests is the tensile test, which allows for the determination of the modulus of elasticity (E), yield strength, tensile strength, as well as relative elongation and reduction in area.
Based on the tensile test, a stress-strain diagram is prepared, which illustrates the deformation of the metal from the elastic phase through the plastic phase to fracture. This test provides key information about the material’s behavior under static working conditions.
Hardness tests
Hardness is the resistance of a material to permanent deformation under the influence of a harder body. The most commonly used methods are Brinell (HB) – a steel ball, Vickers (HV) – a diamond pyramid, and Rockwell (HR) – a steel cone or ball. Hardness correlates with other mechanical properties – the harder the metal, the greater its strength, but often the lower its ductility.
Impact tests
These are used to assess the resistance of metal to rapid dynamic loads. They are performed using the Charpy pendulum (notched test) and the Izod pendulum. The result is given as the amount of energy required to break the sample, which illustrates the behavior of the material under impact load, crucial, for example, in the automotive, railway, and aviation industries.
Creep testing
Creep is the slow, progressive deformation of metal under the action of a constant load and temperature. The test involves applying a long-term load to the sample and measuring the deformation over time. It is of great importance in the selection of materials for components operating at elevated temperatures, such as turbines, boilers, and reactors.
Modern assessment methods
In addition to classic tests, non-destructive methods and advanced microscopic techniques are increasingly being used, such as EBSD analysis (electron backscatter diffraction), SEM/TEM microscopy, ultrasonic and X-ray testing, and nanometric hardness testing (nanoindentation). These methods enable the examination of structure, defects, and mechanical properties with extreme precision, without destroying the sample.
Deformation and recrystallization of metals – summary
Understanding the mechanisms of deformation and recrystallization in metals is crucial from both scientific and engineering perspectives. The way a metal reacts to stress determines not only its durability and reliability, but also its formability and processability.
Conscious control of the internal structure of a material, through the appropriate selection of deformation and heat treatment conditions, allows for the optimization of mechanical properties, which is used in almost every field of industry: from machine construction, through aviation, to nuclear energy.
Knowledge of these processes is not just theory – it is a tool for conscious material design, tailored to the real conditions of its operation.