Corrosion-resistant alloys in the oil industry
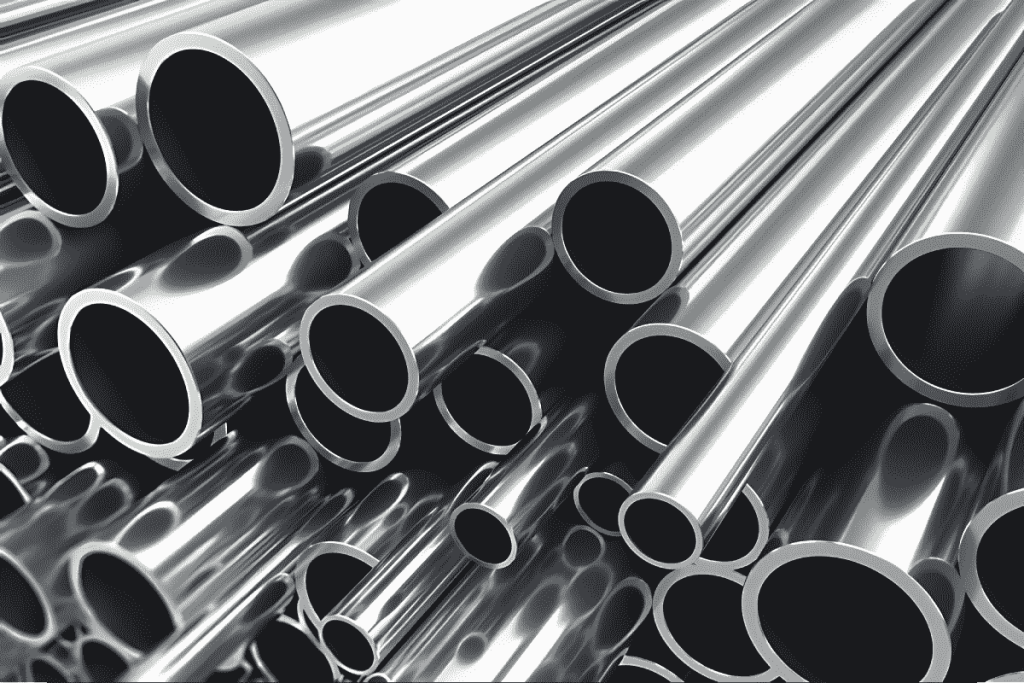
Table of contents
The oil and gas industry requires materials that can withstand extreme operating conditions such as high pressures, aggressive chemical environments and varying temperatures. Choosing the right materials for pipelines, tanks or offshore installations is critical to the safety, durability and operating costs of the infrastructure.
Carbon steel and corrosion-resistant alloys are among the most commonly used materials in this sector. Carbon steel, due to its high mechanical strength and relatively low cost, is widely used in the construction of pipelines and support structures. However, its susceptibility to corrosion in aggressive environments makes it necessary to use corrosion-resistant alloys such as stainless steel, nickel, or titanium in many applications.
This article will discuss the properties of carbon steel and corrosion-resistant alloys, their advantages and limitations, and their key differences. This analysis will provide a better understanding of the conditions under which a particular material is most effective and the trends in the development of new material technologies.
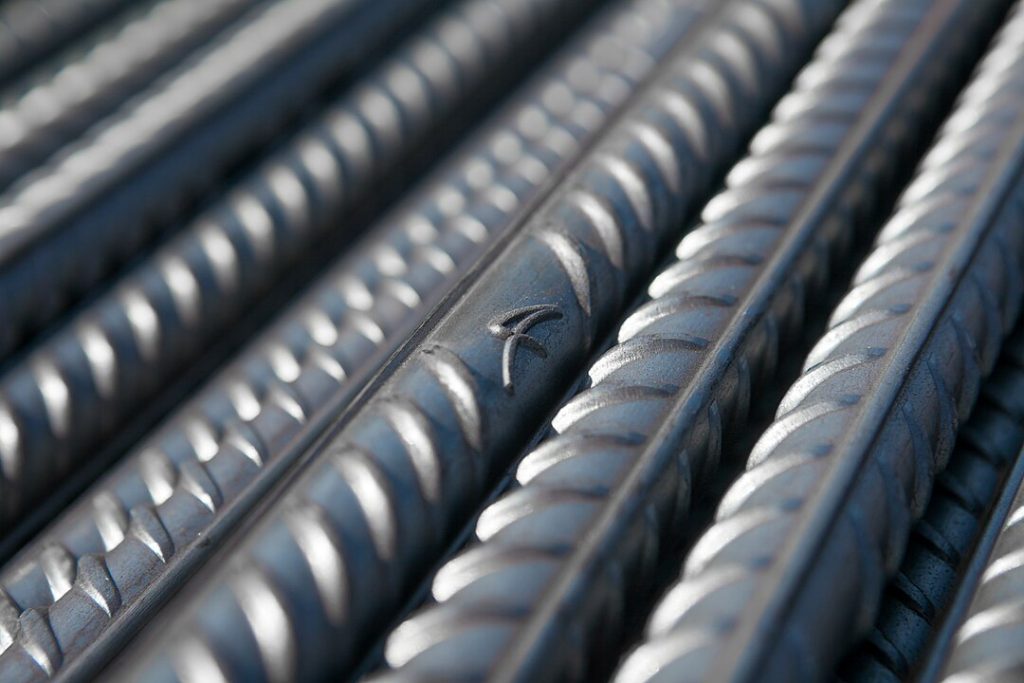
Carbon steel – properties and applications
Carbon steel is an alloy of iron and carbon, with a carbon content usually up to 2%. Depending on the amount of carbon, there are low-carbon, medium-carbon, and high-carbon steels. The oil industry mainly uses low-carbon steels, which have good weldability and ductility but are more susceptible to corrosion than alloys with a higher content of protective alloying additives.
Carbon steel is widely used in the oil industry mainly because of its price-to-strength ratio. Its key advantages are: low price – carbon steel is much cheaper to produce than specialized corrosion-resistant alloys, good mechanical strength – enabling it to be used in structures subjected to heavy loads, and easy availability and processing – the possibility of mass production and ease of welding and forming make it widely used in the construction of pipelines and storage tanks.
Despite these advantages, carbon steel has limited corrosion resistance, especially when exposed to seawater, acids and corrosive gases. In hydrogen sulfide-rich environments, severe damage can occur from sulfide corrosion, leading to hydrogen embrittlement and cracking of the material. This problem forces the use of additional methods of protection, such as anti-corrosion coatings, corrosion inhibitors and cathodic protection, which in turn increases operating costs.
Corrosion-resistant alloys – types and characteristics
Stainless steels
Stainless steels are alloys of iron, chromium and often nickel and molybdenum, which exhibit high corrosion resistance due to the formation of a protective layer of chromium oxides on the metal surface. This layer prevents further degradation of the material, which makes stainless steels suitable for use in aggressive chemical environments, high temperatures and conditions exposed to seawater. Stainless steel is used in:
- Transmission systems in marine environments where water contains chlorides that accelerate corrosion.
- Industrial high-temperature systems where traditional carbon steel could degrade.
- Refinery tanks and systems that are exposed to aggressive chemicals.
The wide application of stainless steels in the petroleum industry mainly due to their versatility and favorable mechanical properties. They are used in transmission pipelines, storage tanks, and apparatus used in refinery processes where contact with corrosive substances is inevitable.
In the marine environment, stainless steels are often the construction material of choice because they resist chlorides, which accelerate pitting corrosion. In high-temperature systems such as heat exchangers and refinery furnaces, stainless steels maintain stability and strength, allowing them to be used for long periods of time without the risk of weakening the metal structure.
Despite their many advantages, stainless steels can be susceptible to stress corrosion cracking and pitting corrosion, especially in the presence of aggressive chloride ions. Therefore, under extreme industrial conditions, additional protection, such as corrosion inhibitors or protective coatings, is often used to extend the life of the material further.
Nickel and titanium alloys
Nickel and titanium alloys are among the most advanced corrosion-resistant materials for use in the most demanding operating conditions. Their unique chemical and mechanical properties make them used in installations operating in extreme temperatures, acidic environments and high-pressure conditions.
Nickel alloys, such as Inconel, show exceptional resistance to hydrogen sulfide (H₂S), acids, and high temperatures, making them ideal for deep well applications and refinery systems. Thanks to their metallurgical structure, they also resist stress corrosion, preventing cracks and failures in deepwater systems.
Meanwhile, Titanium and its alloys are distinguished by their extremely high resistance to corrosion in seawater, making them suitable for use in offshore structures, oil rigs, and subsea pipelines. Their low density compared to other metals allows the construction of lightweight yet strong structures that can operate in extreme conditions for many years without maintenance.
One of the main limitations of using nickel and titanium alloys is their high cost, which often limits their use to only the most demanding applications. For this reason, hybrid solutions are often used, combining components made of corrosion-resistant alloys with cheaper materials, such as carbon steel, which are additionally protected against degradation.
Despite the high price of nickel and titanium alloys, their reliability and minimal maintenance needs make them replaceable in areas where failure could lead to catastrophic environmental and economic consequences.
The choice between stainless steels and nickel and titanium alloys depends primarily on environmental conditions and the specifics of the application. Stainless steels offer a favorable balance between price and corrosion resistance, while nickel and titanium alloys provide maximum protection even in the most extreme environments, but at a much higher operating cost. The oil industry is seeking to optimize the use of these materials, combining their advantages to maximize infrastructure durability and efficiency.
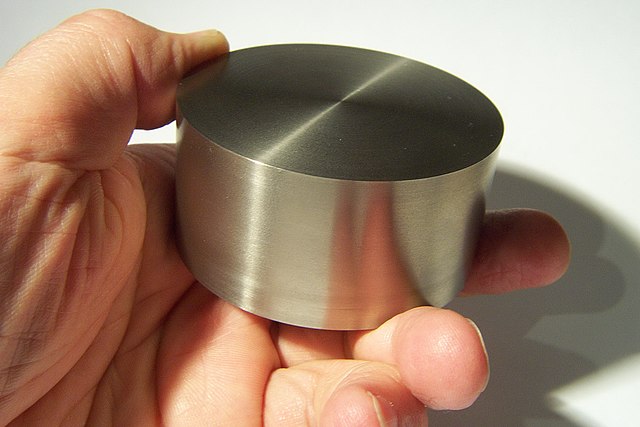
Comparison of carbon steel and corrosion-resistant alloys
Choosing the right material in the oil and gas industry depends on many factors, such as corrosion resistance, mechanical strength, production and maintenance costs, and operating conditions. Despite its popularity, carbon steel is not always the best option, especially in chemically aggressive environments where more degradation-resistant materials are needed.
The main difference between carbon steel and corrosion-resistant alloys is their ability to withstand harsh operating conditions. Carbon steel, while cheap and widely available, requires additional protection to avoid rapid degradation. In contrast, corrosion-resistant alloys, such as stainless steel and nickel alloys, feature natural protection against corrosive agents, significantly extending their life and reducing maintenance.
Resistance to corrosion in different environments
One of the key factors in selecting a material is its resistance to corrosion in a particular operating environment. Carbon steel shows high susceptibility to corrosion in the presence of moisture, oxygen, hydrogen sulfide (H₂S) and carbon dioxide (CO₂). Particularly in underground pipelines and offshore installations, where contact with seawater and mineral salts is unavoidable, additional protection methods such as protective coatings, corrosion inhibitors or cathodic protection are necessary.
Stainless steels, nickel, and titanium alloys show much higher corrosion resistance because they form natural protective layers that prevent further damage to the metal surface. Nickel alloys are particularly effective in acidic environments, while titanium performs well in marine installations where intense seawater exposure could quickly degrade carbon steel.
Mechanical strength and durability under operating conditions
Materials used in the oil industry must have adequate mechanical strength in addition to corrosion resistance. Carbon steel offers high resistance to static and dynamic loads, which makes it often used in transmission pipelines and support structures. However, in extreme environments, such as deepwater wells or installations subjected to high temperatures and pressures, it can be susceptible to stress corrosion and corrosion cracking, limiting its durability.
Corrosion-resistant alloys, particularly nickel and titanium alloys, retain their properties even under extremely harsh conditions. They are resistant to high temperatures, hydrogen sulfide and aggressive chemicals, making them last much longer than traditional carbon steel. Their mechanical strength is also higher, allowing thinner pipeline walls and structural components to be used without the risk of weakening the structure.
Production and maintenance costs
Material cost plays a key role in petroleum infrastructure engineering decisions. Carbon steel is relatively cheap to produce, making it widely used in pipelines and storage tanks. However, its susceptibility to corrosion requires additional protection, which generates costs associated with maintenance, repair and inspection.
Although corrosion-resistant alloys are much more expensive to produce, they offer lower operating costs because they do not require frequent inspections and costly preventive measures. Their use can save money in the long run, especially in installations operating in extreme conditions with high risk of failure and material degradation.
Examples of applications in the oil industry
In practice, the choice of material depends on the specifics of the application. Carbon steel with additional protections is most often used in onshore and underground pipelines because, under these conditions, the risk of corrosion can be effectively controlled with protective coatings and cathodic protection.
In offshore installations, where conditions are much more aggressive, stainless steels and nickel and titanium alloys are more commonly used. These materials can operate for decades without costly repairs. Particularly in deep wells and pipelines transporting aggressive chemicals, materials with higher resistance are necessary for infrastructure reliability.
Practical application of both groups of materials
The choice between carbon steel and corrosion-resistant alloys depends on operating conditions and infrastructure durability and reliability requirements. Both types of materials are widely used in the oil industry, but their effectiveness depends on the specific environment in which they are used.
Use of carbon steel in pipelines and tanks
Carbon steel is the oil industry’s most widely used construction material, mainly because of its mechanical strength and low price. It is primarily used in the construction of pipelines transporting crude oil and natural gas, as well as in storage tanks and support structures.
Carbon steel performs well in onshore pipelines because its susceptibility to corrosion can be controlled with cathodic protection, anti-corrosion coatings, and corrosion inhibitors. Underground installations use insulating polyethylene or epoxy coatings to reduce the metal’s contact with moisture and soil.
Carbon steel in petroleum product tanks is protected with protective coatings and regularly monitored for material loss. In environments where aggressive chemicals are present, additional protection or more corrosion-resistant alloys must be applied in critical areas of the structure.
Corrosion-resistant alloys in offshore installations and acidic environments
In environments where carbon steel degrades rapidly, stainless steels and nickel and titanium alloys are used. These materials are highly resistant to corrosion and extreme temperatures and pressures. Examples of such environments include drilling platforms, subsea pipelines, and installations transporting aggressive chemicals.
On offshore platforms, stainless steels are used in piping systems and support structures that are exposed to seawater and varying temperatures. Stainless steels containing molybdenum and nickel, which protect the material from pitting and stress corrosion cracking, perform particularly well in these conditions.
Offshore pipelines often use titanium alloys, which are characterized by resistance to seawater and low dead weight, making them easier to install and transport. Due to their durability, pipelines made of titanium can be operated for decades without extensive maintenance.
Traditional carbon steel degrades quickly through sulfide and dioxide corrosion in acidic environments, where H₂S and CO₂ are present. In such cases, nickel alloys such as Inconel are used to protect against aggressive chemicals and resist stress corrosion cracking.
Use of hybrid materials
Due to differences in cost and properties, hybrid solutions are often used in engineering practice. These involve combining carbon steel with corrosion-resistant materials in the areas most vulnerable to degradation.
In oil pipelines, one can encounter systems in which the interior of the pipes is coated with a layer of corrosion-resistant alloy, while the outer structure remains made of carbon steel. This approach allows for cost reduction while ensuring high durability of components exposed to aggressive substances.
Similarly, storage tanks use nickel and titanium alloy coatings at the points of contact with chemicals, while other structural components are made of carbon steel. This makes for a durable yet economically viable design.
Corrosion-resistant alloys in the oil industry – summary
The choice of materials in the oil industry affects infrastructure durability, safety and operating costs. Carbon steel, while cheap and widely used, requires additional corrosion protection. Corrosion-resistant alloys, such as stainless, nickel and titanium steels, offer greater durability, but come at a higher cost.
The oil industry is developing modern coatings, monitoring systems and new metal alloys to improve corrosion resistance and optimize costs. Increasingly, hybrid solutions are being used, combining the economic advantages of carbon steel with the durability of corrosion-resistant alloys.
This article is based on the book “Metallurgy and Corrosion Control in Oil and Gas Production”, Robert Heidersbach.