Causes of corrosion in the oil and gas industry
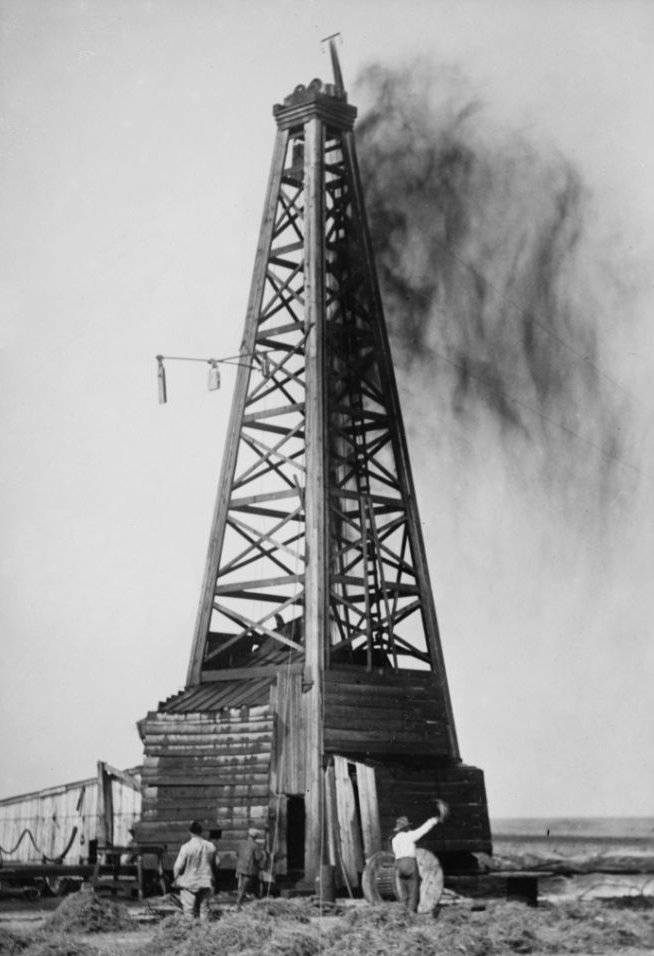
Table of contents
Corrosion is one of the most serious problems in the oil and gas industry, affecting safety and operating costs. It occurs in all stages of operation – from extraction to transportation to storage of raw materials. Annual corrosion-related losses in the industry are estimated to be billions of dollars, and uncontrolled corrosion events can lead to catastrophic infrastructure failures.
Inadequate corrosion risk management can result in the following:
- Damage to pipelines and storage tanks, increasing the risk of leaks and explosions.
- Production interruptions and high repair costs.
- Degradation of metal parts in drilling and refining equipment shortens its life.
- Environmental pollution, especially in the case of oil or gas spills.
Understanding the causes of corrosion is key to effectively controlling it and preventing unwanted effects. This article will discuss the main types of corrosion occurring in the oil and gas industry and the factors that accelerate it.
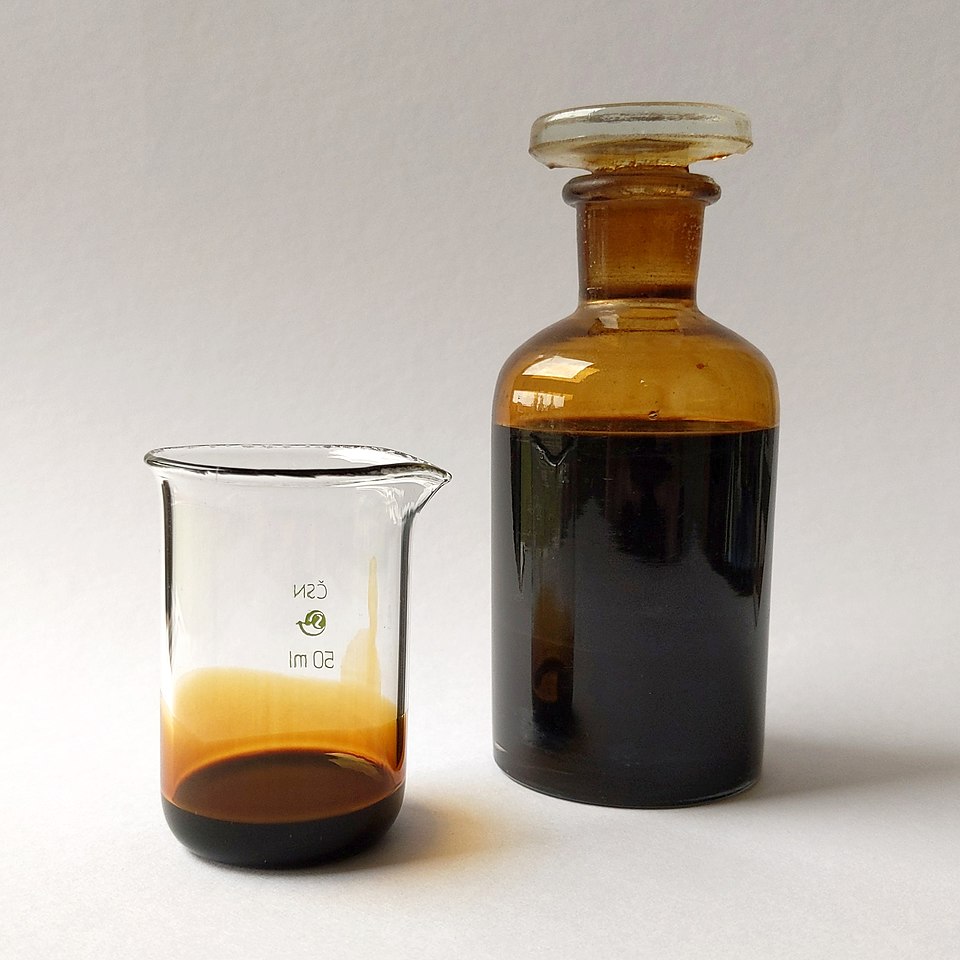
Types of corrosion in the oil and gas industry
Corrosion in the oil and gas sector can take different forms depending on environmental conditions, the medium’s chemical composition and the materials’ properties. Distinguishing between different types of corrosion is key to effectively protecting infrastructure and extending its life.
- General corrosion – is the most common type of corrosion, in which metal undergoes uniform oxidation over the entire surface. It occurs in the presence of oxygen and moisture, leading to gradual degradation of the material. As a result of this process, the thickness of the walls of pipelines and tanks decreases, reducing their strength. Although this type of corrosion is relatively easy to monitor, it requires systematic preventive measures such as protective coatings and inhibitors.
- Galvanic corrosion – occurs when two different metals are in electrical contact in a conductive environment. The less noble metal (anode) undergoes accelerated oxidation, while the more noble metal (cathode) remains protected. This phenomenon is particularly important in pipeline systems and offshore structures, where joining different materials is necessary. Proper selection of materials and electrical insulation between them is used to reduce this type of corrosion.
- Pitting corrosion – is a local form of corrosion in which the metal degrades at small but deep points. It most often occurs in the presence of chloride ions, which contribute to the formation of pits, weakening the material’s structure. Unlike general corrosion, which distributes uniformly, pitting corrosion can quickly lead to the perforation of structural components. The use of corrosion-resistant materials and inhibitors is crucial in reducing it.
- Stress Corrosion Cracking (SCC) – is a process in which a material cracks under the simultaneous action of mechanical stress and an aggressive chemical environment. Cracks can develop gradually, but severe consequences lead to sudden equipment failure. SCC occurs especially in pipelines and tanks operating at high pressure and in environments containing hydrogen sulfide.
- Microbially Influenced Corrosion (MIC) occurs due to the activity of microorganisms that accelerate metal degradation by producing aggressive chemicals. Particularly problematic is the activity of sulfate-reducing bacteria (SRB), which leads to the formation of hydrogen sulfide, increasing the risk of corrosion and material embrittlement. Combating this type of corrosion requires regular disinfection and the use of biocides.
- Erosion corrosion – occurs due to intensive flow of liquid or gas, mainly when the medium contains solid particles such as sand or mineral deposits. The combination of mechanical and chemical factors causes gradual abrasion of the metal’s protective layer, leading to accelerated wear of components. Materials with increased abrasion resistance are used and flow parameters are controlled to reduce this type of corrosion.
Key factors accelerating corrosion
Corrosion in the oil and gas industry occurs under the influence of many factors that can significantly accelerate metal degradation. The chemical environment, physical conditions, and fluid flow dynamics have a key influence on the development of corrosion processes. Knowledge of these factors is essential for effective corrosion prevention and optimal selection of protection methods.
The presence of oxygen (O₂)
Oxygen is one of the main factors accelerating corrosion, especially in aqueous environments. When it comes into contact with a metal, it causes it to oxidize, leading to the formation of corrosion products such as oxides and rust. Even small amounts of oxygen can significantly increase the rate of corrosion, especially when present in pipelines or tanks containing water or moisture. Restricting oxygen access to the metal surface through seals, protective coatings and the use of inhibitors is key to reducing this type of corrosion.
Presence of hydrogen sulfide (H₂S) and carbon dioxide (CO₂)
Hydrogen sulfide (H₂S) and carbon dioxide (CO₂) are the two most common corrosive gases in the petroleum industry. CO₂ (“sweet corrosion”) – when in contact with water, forms carbonic acid (H₂CO₃), which lowers the pH and accelerates metal dissolution, leading to cavities in pipelines and tanks. H₂S (“acid corrosion”) – causes the formation of iron sulfides (FeS), which can have a protective effect, but also increases the risk of live corrosion and hydrogen embrittlement. The effect of these gases on corrosion depends on their concentration, temperature and pressure, making it necessary to use CO₂ and H₂S-resistant materials in aggressive environments.

Moisture and the presence of water
Water is key in most corrosion processes because it acts as an electrolyte, allowing current to flow between the anode and cathode on the metal surface. Depending on its chemical composition, it can accelerate corrosion to varying degrees.
- Fresh water – contains oxygen, which promotes metal oxidation.
- Seawater – rich in chloride ions (Cl⁻), which intensify pitting corrosion.
- Reservoir water – can contain sulfates, carbonates, and sulfate-reducing bacteria, leading to microbial corrosion.
Management of water content in oil systems includes its separation, removal of corrosive compounds and use of inhibitors.
Temperature and pressure
High temperature and pressure are some of the key factors influencing the rate and nature of corrosion processes in the oil and gas industry. Their impact is particularly significant in extreme environments such as deep wells, high-pressure pipelines and offshore installations.
Temperature directly affects the rate of chemical and electrochemical reactions leading to corrosion. An increase in temperature accelerates metal oxidation and reactions with corrosive gases, increasing their aggressiveness. At the same time, it can destabilize protective layers, such as the passive oxide layer on stainless steels, making the metal more susceptible to corrosion. Elevated temperature also affects the solubility of gases in water – CO₂ and H₂S can react more intensively with water, forming aggressive acids that attack metal surfaces.
High temperatures can also lead to the breakdown of corrosion inhibitors, which are substances used to slow the degradation of metal. Some inhibitors lose their protective properties under extreme thermal conditions, requiring the use of more resistant chemicals. Specific types of corrosion can also occur under certain conditions, such as high-temperature corrosion, which is metal oxidation without liquid water, occurring in boilers and heat exchangers, for example. Another type is sulfide corrosion, occurring in sulfur-rich environments, which is particularly important in oil refining processes.
Elevated temperatures can also promote stress corrosion cracking (SCC), which is the formation of cracks in a material’s structure caused by a combination of mechanical stress and an aggressive chemical environment. This type of damage is particularly dangerous because it can develop imperceptibly, leading to sudden failure.
Pressure affects the intensity of corrosion by changing the physicochemical properties of the gases and liquids present in the system. High pressure increases the solubility of CO₂ and H₂S in water, making the medium more aggressive toward structural materials. These gases, combined with moisture, form acids that accelerate metal degradation, which is particularly problematic in systems operated at high pressure.
Another important factor is the effect of high pressure on the durability of materials. In deep wells and transmission pipelines, extreme pressure causes more intense chemical and mechanical impacts on metal surfaces. This can weaken the material’s structure and increase susceptibility to cavitation – the formation and collapse of vapor bubbles, which can damage the metal surface through violent impacts, accelerating its degradation.
Examples of typical sites exposed to corrosion
Corrosion in the oil and gas industry occurs in many infrastructure components, especially where metals are exposed to aggressive chemical environments, high pressure, and temperature. Its effects can damage pipelines, tanks, and process equipment, causing costly downtime and safety risks.
Pipelines, tanks and transmission systems
Pipelines and storage tanks are among the most frequently corroding infrastructure components, as their walls are in constant contact with a medium containing water, CO₂, H₂S and mechanical impurities. Internal corrosion can lead to pitting and perforation, while external corrosion, caused by moisture, oxygen and stray currents, weakens the structure of the material. Underground pipelines and tanks exposed to temperature changes, which cause condensation and the development of atmospheric corrosion, are particularly at risk. Corrosion prevention is based on cathodic protection, the use of inhibitors and protective coatings.
Offshore infrastructure and drilling equipment
Offshore drilling platforms and pipelines operate in an extremely aggressive environment, where salt water, strong currents and high humidity accelerate corrosion. Galvanic corrosion occurs at the interface of various metals, which is particularly dangerous, and erosion corrosion, which leads to surface damage under the influence of strong water flow and suspended particles. Drilling equipment, including pipes and valves, is additionally subject to stress corrosion and hydrogen embrittlement, especially in the presence of H₂S. To reduce degradation, high-pressure resistant materials, anodic cathodic protection and specialized anti-corrosion coatings are used.
Cooling systems and heat exchangers
Cooling systems and heat exchangers are susceptible to corrosion resulting from high temperatures, varying operating conditions and aggressive chemicals used in technological processes. Among the most common problems are erosion corrosion, caused by rapid fluid flow, microbial corrosion, associated with bacterial growth, and vibration corrosion, which weakens metal components under mechanical and environmental stresses. Proper selection of materials, regular control of water composition and cyclic cleaning of systems are key preventive measures.
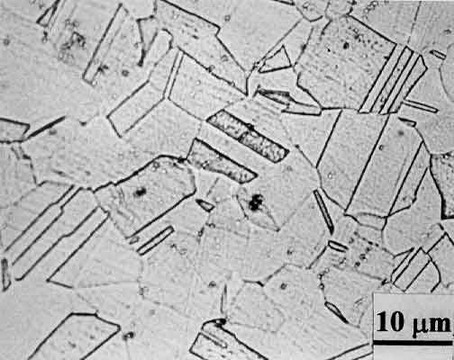
Effects of corrosion in the oil and gas industry
Corrosion in the oil and gas sector has serious economic, environmental, and operational consequences. Degradation of infrastructure leads to unplanned downtime, increased maintenance costs, and risks to human and environmental safety.
Increased operating and maintenance costs
Corrosion is one of the main factors affecting operating costs in the oil and gas industry. Repairing damaged pipelines, replacing corroded components and implementing corrosion protection systems generate huge expenses. In addition, frequent inspections and monitoring of the condition of the infrastructure require significant financial outlays. Globally, annual corrosion-related costs in this industry reach billions of dollars.
Progressive corrosion can lead to equipment failures, leaks and damage to pipelines and tanks, resulting in the need to stop production. Interruptions not only reduce operational efficiency, but also generate additional financial losses related to repairs and delivery delays. In extreme cases, corrosion can cause a complete shutdown of infrastructure, which is particularly problematic for offshore installations and deepwater wells.
Corrosion of oil and gas infrastructure can lead to catastrophic failures, such as pipeline ruptures, flammable spills and explosions, which directly threaten the life and health of workers and surrounding communities. Gas or oil leaks can cause fires and, in extreme cases, explosions on oil rigs or in refining plants. Proper prevention and control of corrosion is key to minimizing the risk of accidents.
Environmental impact
Corrosion leading to oil, gas or chemical spills has catastrophic effects on aquatic and terrestrial ecosystems. The leakage of these substances into soil and groundwater causes contamination that can persist for decades. Oil spills into the oceans cause huge losses in marine populations and destruction of coastal habitats. Environmental incidents resulting from corrosion accidents often lead to multi-million dollar damages and sanctions for the companies responsible for the spills.
One of the most notable cases of corrosion leading to an environmental disaster was the Prudhoe Bay oil spill in Alaska in 2006. The oil transport pipeline perforated as a result of internal corrosion caused by sediment accumulation and insufficient corrosion inhibitor control. Through the damage to the infrastructure, over 200,000 gallons of oil leaked into the Arctic tundra, contaminating an area of several hectares. The spill had a catastrophic impact on the local ecosystem, destroying animal habitat and leading to long-term ecological consequences. A costly decontamination operation was required, and the company managing the infrastructure was hit with financial penalties and forced to make infrastructure upgrades.
Strategies to minimize and prevent corrosion
Corrosion in the oil and gas industry is inevitable, but can be effectively controlled and mitigated through appropriate protection strategies. Effective corrosion risk management not only extends the life of infrastructure, but also reduces operating costs and the risk of failure.
Cathodic protection
One of the most effective methods of protecting metals against corrosion is cathodic protection, which is mainly used in pipelines, tanks and underground and offshore structures. It involves the application of electric current or active anodes to reduce the electrochemical potential of the protected metal, so that the corrosion process is inhibited.
There are two main types of cathodic protection:
- Galvanic protection (using sacrificial anodes) – uses metals with a lower electrochemical potential, such as zinc, magnesium or aluminum, which undergo controlled wear, thus protecting the actual structural material.
- Impressed Current Cathodic Protection (ICCP) – involves connecting a direct current source to the structure to be protected, which prevents corrosion through the controlled delivery of electrons.
Cathodic protection systems are essential in transmission pipelines, offshore structures and storage tanks where corrosion is particularly intense.
Application of corrosion inhibitors
Corrosion inhibitors are special chemicals added to the working medium to slow down or completely inhibit corrosion reactions. They act by forming a protective layer on the metal surface or modifying the corrosive properties of the environment.
The division of corrosion inhibitors includes:
- Anodic inhibitors – reduce the rate of metal oxidation reaction.
- Cathodic inhibitors – reduce the rate of oxygen or hydrogen reduction reaction.
- Mixed inhibitors – act simultaneously on the anode and cathode, slowing down the entire electrochemical process.
Corrosion inhibitors are widely used in the oil and gas industry, especially in pipelines, water transmission systems and drilling equipment, where mechanical or cathodic protection is difficult to implement.
Selection of resistant materials and protective coatings
Proper selection of materials is key to reducing the risk of corrosion. Environments with high chemical aggressiveness use stainless steels, nickel alloys, high-strength alloy steels and titanium which exhibit enhanced corrosion resistance.
Additional protection is provided by anti-corrosion coatings, which act as a barrier between the metal and the aggressive environment. Among the most commonly used solutions are:
- Epoxy and polyurethane coatings – used in pipelines and tanks.
- Metal protective coatings (e.g., zinc, aluminum) – provide cathodic protection for long periods of time.
- Ceramic and composite protective barriers – used in extreme environments, such as oil rigs and refinery installations.
Causes of corrosion in the oil and gas industry – summary
Corrosion in the oil and gas industry leads to high costs, safety risks and environmental damage. Effective infrastructure protection requires understanding corrosion mechanisms and implementing appropriate prevention strategies, such as cathodic protection, corrosion inhibitors, protective coatings and regular monitoring.
Corrosion prevention is critical to increasing infrastructure longevity and minimizing the risk of failure. Modern technologies allow increasingly effective control of this process, which is important given increasing operational and environmental requirements.
This article is based on the book “Metallurgy and Corrosion Control in Oil and Gas Production”, Robert Heidersbach.