Aluminum and its alloys
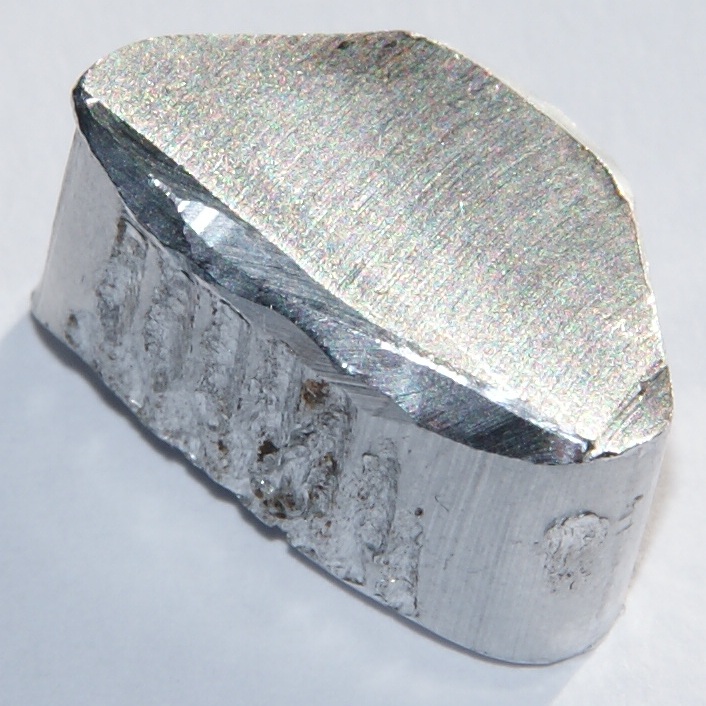
Table of contents
Characteristics of aluminum as a structural metal
Aluminum is one of the most widely used metals in industry, and its importance continues to grow, both in engineering applications and in everyday consumer products. As a chemical element, it is distinguished by its low density, good thermal and electrical conductivity, and high corrosion resistance, making it a beautiful material for modern construction.
One of its most characteristic features is its low specific weight of approximately 2.7 g/cm³, which makes it nearly three times lighter than steel. Combined with sufficient mechanical strength, this property allows for a significant reduction in the weight of a structure without compromising its functionality. In industries such as transportation, aviation, aerospace, and automotive, every kilogram saved matters—and that is where aluminum finds its natural application.
Pure aluminum does not have high mechanical strength. Still, its most significant potential is revealed in the form of alloys, which, thanks to the addition of elements such as copper, magnesium, silicon, manganese, and zinc, achieve significantly better strength, hardness, and technological parameters. It is aluminum alloys that form the basis of its industrial success, enabling the manufacturing of lightweight, durable, wear-resistant, and easy-to-machine components.
Additionally, aluminum is a highly recyclable material. Its reprocessing requires only a fraction of the energy consumed in its primary production, making it an environmentally friendly and economically viable raw material. This combination of physical, technological, and ecological properties means that aluminium remains not only a strategic raw material, but also a symbol of a modern approach to materials engineering.
Basic properties and types of technical aluminium
In industrial practice, pure aluminium in its chemically ideal form is rarely used. Instead, so-called technical aluminum is used, which, although still containing a predominant proportion of aluminum, also contains trace amounts of other elements such as iron, silicon, manganese, copper, and zinc. These additives are either by-products of the manufacturing process or deliberately added to influence the properties of the material.
One of the most recognizable advantages of technical aluminum is its ease of forming and machining, both in plastic and mechanical applications. This material can be rolled, stamped, drawn, and bent without incurring a significant risk of cracking or loss of structural integrity. This is why it is used in the manufacturing of thin-walled structural elements, profiles, pipes, and components with complex shapes.
Another important feature of technical aluminum is its relatively low melting point, ranging from approximately 650°C to 660°C. Compared to steel or other structural metals, this is a relatively low value, which facilitates heat treatment and casting, but at the same time imposes limitations when working in high-temperature conditions.
Aluminum also exhibits excellent thermal and electrical conductivity, which means that, in addition to its mechanical properties, it often serves as a conductive material, especially where weight and corrosion resistance are more important than extreme conductivity, as is the case in high-voltage lines or heat sinks.
Technical aluminum types can be categorized based on their degree of purity. Aluminum with a purity of over 99% retains most of the physical properties of primary aluminum, such as high plasticity, low strength, and excellent corrosion resistance. Lower purity grades – for example, containing approx. 98% aluminum has slightly lower corrosion resistance parameters, but may be more attractive from the point of view of manufacturing economy and availability of secondary raw materials.
It should be emphasized that technical aluminum is the basis for further alloying. Its purity, structure, and additives are the starting point for the development of specialized alloys, in which aluminum ceases to be merely a background for additives and becomes the foundation for a new class of construction materials with expanded applications.
Properties and applications of aluminum alloys
It is in the form of alloys that aluminum reveals its full potential as a construction material – not only lightweight and corrosion resistant, but also durable, susceptible to heat treatment, and adaptable to a wide range of operating conditions. The addition of other elements to aluminum, such as copper, silicon, zinc, magnesium, or manganese, allows its properties to be radically changed, making aluminum alloys a group of materials with almost unlimited engineering possibilities.
The most important achievement in the field of aluminum alloys is the ability to control their structure through appropriate heat treatment processes. Through hardening, precipitation, aging, and annealing, their hardness, elasticity, creep resistance, and plasticity can be adjusted. An AA alloy, which in its raw state can be soft and easily deformable, becomes a material with properties similar to some carbon steels after aging.
Another unique feature of aluminum alloys is their natural resistance to atmospheric corrosion. A thin layer of aluminum oxide forms on the surface almost immediately after contact with oxygen, protecting the material from deeper oxidation. Combined with low density, this makes aluminum alloys widely used wherever durability, lightness, and longevity are essential—for example, in aviation, shipbuilding, bridge construction, and modern electric vehicles.
Another essential feature is the high plasticity of aluminum alloys. Regardless of whether the material is rolled, pressed, drawn, or shaped using volume methods, appropriately selected alloys retain the required ductility and crack resistance, enabling the manufacturing of thin-walled, complex components that would be more difficult or less economical to produce from other metals.
Key phase diagrams of aluminum alloys
Understanding the properties and behavior of aluminum alloys is impossible without reference to their phase diagrams, which describe the relationships between temperature, chemical composition, and internal structure of the material. It is these diagrams that determine which phases can form in the alloy, under what conditions phase transformations occur, and what final structure will be obtained upon completion of the technological process.
In the case of aluminum, two- and three-component phase diagrams are of key importance, in which aluminum is combined with elements such as copper, silicon, zinc, magnesium, or manganese. These combinations create characteristic phase transition zones, in which areas of solid solutions, two- or multi-phase mixtures, and eutectic or peritectic zones can be distinguished.
One of the most critical phase diagrams is the aluminum-copper phase diagram, which serves as the basis for many precipitation-hardening alloys. In this case, the most important secondary phase is Al₂Cu, which is formed as a result of controlled aging and is responsible for a significant increase in hardness and tensile strength. This phase diagram is used in duralumin alloys, which are commonly used in the aerospace industry.
Equally important is the aluminum-silicon phase diagram, which dominates in casting alloys. The presence of silicon improves castability and abrasion resistance, and with appropriate eutectic Al–Si refinement, it allows a very favorable compromise between strength and processability to be achieved. Such alloys are often used in engine castings, machine components, and mechanical housings.
Equally important is the aluminum-magnesium phase diagram, which is responsible for the formation of alloys with excellent corrosion resistance and a relatively low specific weight. Although less durable than copper or zinc phase diagrams, alloys of this type are ideal for marine applications and lightweight structures exposed to moisture and salt.
The aluminum-zinc phase diagram, on the other hand, offers exceptionally high mechanical strength, particularly after heat treatment. In combination with magnesium and copper, it forms the basis for the most technologically advanced alloys, which, despite their lower corrosion resistance, are used where maximum strength with minimum weight is crucial.
Each of these phase diagrams constitutes a scientific map of structural changes, knowledge of which is essential not only for metallurgists but also for every engineer working with construction materials. It is phase diagrams that allow us to predict, model, and design the behavior of alloys not only in the laboratory, but above all in real, industrial applications.
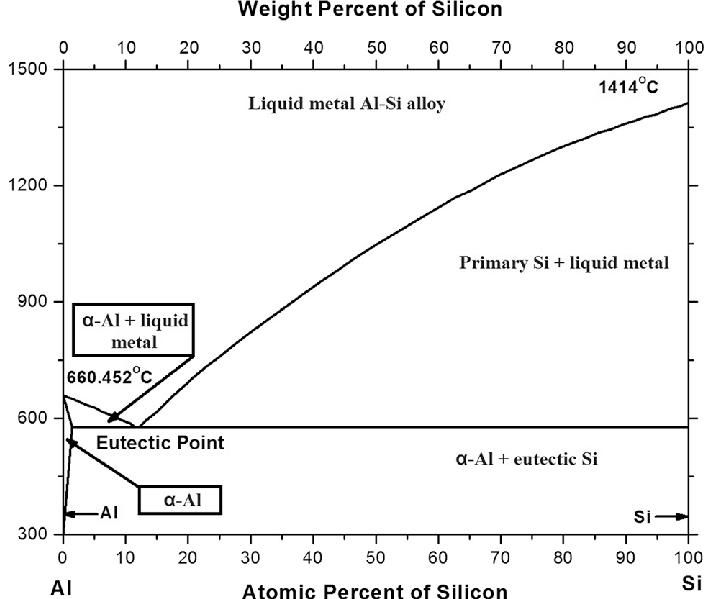
Aluminum casting alloys and their modification
Among the various types of aluminum alloys, casting alloys occupy a special place, as they are used where it is crucial to obtain complex shapes without the need for mechanical processing. Their popularity stems not only from the properties of aluminum itself, but also from the possibility of precise control of the structure during the solidification process.
The primary component of most aluminum casting alloys is silicon, which serves several crucial functions. Firstly, it significantly lowers the melting point of the alloy, which improves its castability, allowing even complex casting molds to be filled. At the same time, silicon has a positive effect on the wear resistance and dimensional stability of castings. However, the coarse structure of the aluminum-silicon eutectic, formed as a result of free solidification, does not always guarantee optimal mechanical properties.
That is why the casting industry widely uses modification of these alloys, i.e., the controlled introduction of additives that affect the shape and size of phase precipitates. The primary objective of modification is to transform the needle-like, sharp silicon structure into a more spherical and fine form, thereby enhancing the ductility, impact strength, and overall strength of the material. The most commonly used modifiers include elements such as sodium, strontium, and titanium – each acts at a different stage of the solidification process. Still, they all share one common goal: to make the casting structure more homogeneous and mechanical.
It is worth noting that aluminum casting alloys are a material that is highly dependent on processing technology. Even the best-designed chemical composition will not produce the expected results without proper melting, liquid metal purification, mold filling, and cooling. Each of these stages can affect phase distribution, grain size, and porosity, which in turn affect the performance of the finished product.
When appropriately modified and processed, casting alloys become not only functional but also economically efficient materials, allowing for the rapid mass production of components with complex geometries and high-performance requirements. Their role in the automotive, electrical engineering, and construction industries cannot be overestimated today, and further development of modification and machining technologies only strengthens their position among modern construction materials.
Hydronalium and duralumin
Alongside casting alloys, alloys intended for plastic working constitute an equally important group of aluminum materials. Their chemical composition and structure are optimized for rolling, stamping, forging, and drawing, allowing the material to be formed into the desired shape without remelting. Among them, hydronalium and duralumin play a special role – two types of alloys that have set the standards for modern materials engineering for decades.
Hydronalium is a trade name for aluminum alloys with added magnesium and small amounts of manganese. The main advantage of this material is its exceptional corrosion resistance, even in chemical and marine environments. It is this feature, combined with good ductility and weldability, that has made hydronalium one of the favorite materials in the shipbuilding industry, tank construction, and components exposed to moisture and salt. Although its mechanical strength is moderate, it is sufficient for applications where chemical resistance is more critical than structural rigidity.
Duralumin, on the other hand, is an alloy with entirely different properties. The primary alloying elements are copper, with additional contributions from magnesium, manganese, and silicon. Thanks to appropriate hardening and aging, duralumin achieves very high mechanical strength—comparable to some structural steels—while maintaining a significantly lower density. This makes these alloys widely used in the aerospace industry, where every gram of weight matters and the material must be able to withstand high loads.
However, it is essential to note that duralumin has limited corrosion resistance, particularly in the presence of moisture and certain chemicals. For this reason, additional surface protection is often used, such as anodizing, varnishing, or coating with other aluminum alloys, which improves its durability in aggressive environments. This combination of strength and appropriately selected surface protection allows duralumin to be used in aircraft load-bearing structures, composite bridges, and frame elements of special vehicles.
Both types of alloys – hydronalium and duralumin – demonstrate the versatility of aluminum applications when the chemical composition and processing technology are appropriately selected. It is not aluminum itself that determines the properties of a material, but how science and technology exploit its potential.
Aluminum and its alloys – summary
Although aluminum has long been overshadowed by iron and its alloys, it is now the focus of attention for engineers, designers, and technologists worldwide. Its unique combination of low weight, corrosion resistance, thermal conductivity, and the possibility of shaping its structure through alloying additives makes it not only a versatile material but also indispensable in many industries.
Modern materials engineering is no longer limited to using aluminum as a lightweight metal—it treats it as a platform for creating functional materials tailored to extremely diverse requirements. Thanks to their heat treatment and surface machining capabilities, aluminum alloys can be optimized for specific parameters, including strength, plasticity, chemical resistance, conductivity, and fatigue life.
Moreover, aluminum recycling serves as a model for sustainable development in the materials industry. The reuse of this metal involves minimal energy consumption. It does not cause any significant loss of its properties, making it a material that is fully compatible with the concept of a circular economy.
The role of aluminum and its alloys is not limited to the aerospace, automotive, and construction industries. It is also used in electronics, energy, medicine, public transport, and even in the architecture of modern cities. Regardless of the industry, aluminum offers a combination of lightness and strength, as well as durability and ease of processing. It is this flexibility that makes it the material of the future.
Understanding the properties, processing technologies, and the impact of alloying additives enables engineers to consciously design components that not only meet technical requirements but also respond to growing expectations for energy efficiency, durability, and a greener manufacturing footprint. Aluminum is no longer an alternative—it is the standard for modern design.