What is metal crystallization?
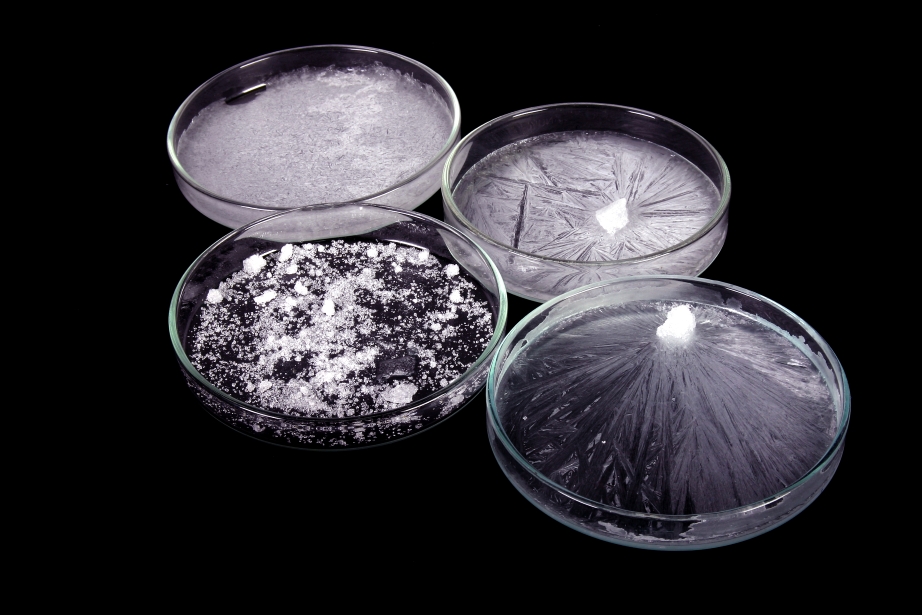
Table of contents
Crystallization is one of the fundamental physicochemical phenomena that occurs in metals, playing a crucial role in both their production and subsequent processing. This process, which involves the transition of metal from a liquid to a solid state through the arrangement of atoms into a regular crystal structure, determines the structure and properties of the resulting material. Depending on the solidification conditions, such as temperature, cooling rate, and the presence of impurities, metal can assume different crystalline forms, which in turn affect, among other things, its strength, susceptibility to further processing, and chemical properties.
Understanding the mechanisms of crystallization is particularly important in fields such as metallurgy, foundry, materials engineering, and joining technology. The practical applications of this knowledge range from the production of steel and special alloys to the controlled shaping of the microstructure of materials used in the aviation industry and nuclear energy. This article provides an overview of the physical and kinetic principles governing the crystallization process of metals, drawing on both theoretical knowledge and practical observations.
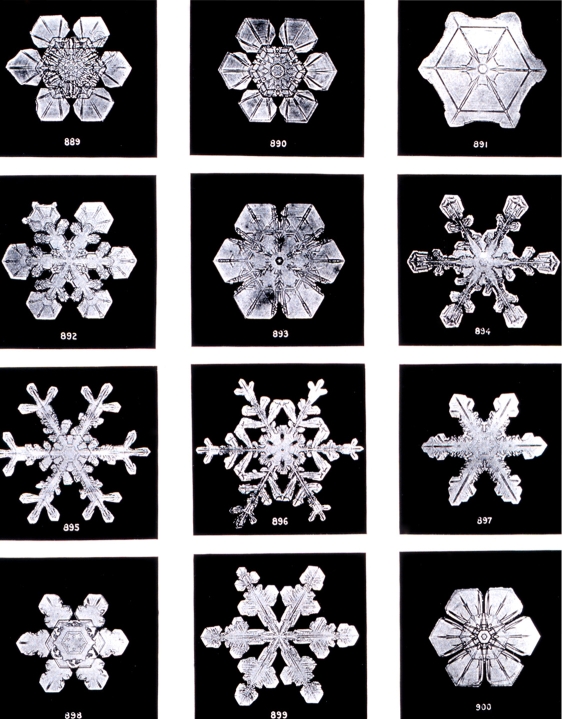
Energetic basis of phase transformations
Metals, like other substances, can exist in three states of matter: solid, liquid, and gas. The transition from one state to another occurs under strictly defined conditions of temperature and pressure, characteristic of each element. Under atmospheric pressure, the melting point and boiling point are particularly important, as they are fundamental physical properties of metals.
From a thermodynamic point of view, only those processes that lead to a decrease in the free energy of the system occur spontaneously. Therefore, the phase formed in a given system has a lower free energy than the preceding phase. The lower the free energy, the greater the stability of a given phase under a given set of conditions.
For the crystallization process, it is crucial to compare the free energy of the liquid and solid phases. Below the crystallization temperature (i.e., the freezing point), the more stable phase is the solid because its free energy is lower. Above this temperature, the liquid phase is more stable. At the transition point, i.e., the theoretical crystallization temperature, both free energies are equal, which means that the liquid and solid coexist in a state of equilibrium.
However, for crystallization to begin, the liquid must be supercooled below its theoretical freezing point. The difference between the theoretical and actual temperatures at which solidification begins is referred to as the degree of supercooling. Similarly, during melting, overheating may occur, i.e., the transition temperature may shift upward relative to the theoretical equilibrium point.
Phase transitions are also accompanied by thermal effects – in the case of solidification, this is the release of latent heat, and in the case of melting, its absorption. Thanks to this phenomenon, characteristic horizontal sections appear on heating and cooling graphs, indicating the transformations taking place. Such graphs allow the crystallization process to be observed and analyzed over time.
In practice, thermal hysteresis is also observed – a phenomenon in which the transition temperature during heating differs from the transition temperature during cooling. This is a direct result of the liquid being supercooled or overheated. The slower the cooling, the lower the degree of supercooling, and the closer the process is to the theory.
Crystal nucleation and growth
The process of primary crystallization, i.e., the transition of liquid metal into a solid, takes place in two stages. It consists of the formation of stable crystal nuclei and the subsequent growth of crystals from these nuclei.
Nucleation only occurs when the total energy of the system decreases. On the one hand, the transition from the liquid to the solid phase causes a decrease in free energy, which promotes crystallization. On the other hand, however, the formation of a boundary surface between the liquid and the crystal generates additional surface energy, which has the opposite effect—it increases the energy of the system.
Crystallization occurs when the decrease in free energy associated with the ordering of atoms is greater than the increase in energy resulting from the formation of the embryo surface. The balance of these energies is described by the formula:
\[ \Delta F = -\Delta F_V \cdot V + \sigma \cdot A\]
- \(\Delta F_V\) – difference in free energy per unit volume,
- \(V\) – embryo volume,
- \(\sigma\) – surface tension,
- \(A\) – surface area of the nucleus.
Assuming that the nucleus has a spherical shape, it is possible to calculate the critical radius of the nucleus (rk), which determines the boundary between stable and unstable nuclei:
\[r_k = \frac{2\sigma}{\Delta F_V}\]
Only nuclei with a radius equal to or greater than rk will be stable and able to grow into full-fledged crystals. Nuclei smaller than rk dissolve back into the liquid because their existence would be associated with an increase in the energy of the system.
The degree of supercooling of the liquid has a key influence on the size of rk. The greater the supercooling, the greater the difference in free energy between the liquid and the crystals, and the smaller the critical radius. As a result, more stable nuclei are formed, leading to faster crystallization and a finer metal structure.
The presence of foreign solid inclusions in the liquid can also induce nucleation. Such particles (e.g., oxides, nitrides, cracks in the mold) can reduce the local surface tension and facilitate heterogeneous nucleation, even with less supercooling.
Simultaneously with nucleation, crystal growth occurs. This process involves the attachment of successive layers of atoms to the surface of the nucleus. Screw dislocations are of particular importance here, as their presence facilitates the growth process. In such places, a spiral fault forms, which attracts additional atoms, resulting in continuous and effective crystal growth. This phenomenon was described by F.C. Frank and is known as the growth spiral.
Factors influencing crystallization
Although the metal crystallization process is based on the principles of thermodynamics and kinetics, in real industrial conditions, it is influenced by many external variables. These factors influence both the number of crystal nuclei formed and the rate of crystal growth, which directly translates into the final structure of the solidified metal. The most important factors include:
- The temperature of the metal before casting and the time it is kept at this temperature – the higher the temperature and the longer the time, the greater the possibility of removing impurities and the more homogeneous the solidification conditions.
- The casting temperature affects the degree of supercooling, which in turn influences the number of nuclei and grain structure.
- Casting method – techniques such as gravity casting, siphon casting, or directional casting affect the temperature distribution in the mold, which regulates the crystallization process.
- Cooling rate – one of the most important parameters; rapid cooling promotes a fine-grained structure, while slow cooling leads to a coarse-grained structure.
- Type and temperature of the casting mold – a mold made of materials that conduct heat well (e.g., metal) and a cool mold accelerate heat transfer, increasing the supercooling of the liquid.
- Quality of liquid metal – the presence of non-metallic inclusions (e.g., oxides, sulfides) can significantly affect heterogeneous nucleation, which in turn changes the nature of the grains formed.
- Surface tension of metal at solidification temperature – determines the ease of formation of an interphase surface between the liquid and the nucleus.
- Mechanical shocks, vibrations, and ultrasonic waves can increase the number of nuclei and accelerate crystallization, thereby affecting the structure and homogeneity of the material.
Although the relationships between these factors and the course of crystallization are theoretically known, in practice, their interactions are complex and difficult to predict with certainty. There is no single universal theory that takes all variables into account simultaneously.
To simplify the description of the crystallization process, G. Tammann proposed two parameters:
- The number of crystal nuclei forming spontaneously in a unit volume within one minute.
- Linear crystallization rate, i.e., the growth rate of crystals measured in millimeters per minute.
Both quantities depend strictly on the degree of supercooling of the liquid. With increasing supercooling, both the number of nuclei and the crystallization rate initially increase, reach a maximum, and then decrease. In extreme cases, with very high supercooling, the liquid may solidify as an amorphous body.
The cooling rate is often treated as an approximate equivalent of the degree of supercooling, allowing it to be used in practice as a tool for controlling the material’s structure.
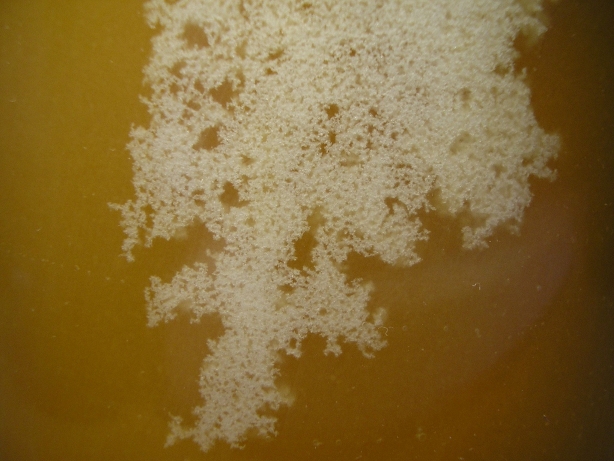
Crystal shape and structure of castings
During crystallization, crystals of various shapes form from the liquid, depending on the thermal and spatial conditions under which solidification occurs. The most common crystalline form in metals is dendrites – branched structures resembling trees, whose name originates from the Greek word “dendron” (meaning tree).
Dendritic crystals form because crystal growth occurs faster in the direction of heat dissipation, most often perpendicular to the walls of the mold. Initially, the main axis of the dendrite (primary) is formed, from which secondary branches develop at an angle, followed by tertiary branches, creating a characteristic structure. As crystallization progresses, the dendrites elongate and thicken until they begin to touch each other, which stops their further growth.
Once the dendrites have finished growing, the inter-dendritic spaces are filled with the remaining liquid metal, which fills the empty areas and also solidifies. As a result, the dendrites transform into crystalline grains, and the final structure of the metal consists of closely packed grains.
In exceptional cases, when there is not enough liquid metal (e.g., as a result of shrinkage during solidification or in the presence of porosity), the dendrites may not be filled. They then remain visible and can be observed, for example, in shrinkage cavities. There are known cases of giant dendrites being found, for example, the so-called Chernov crystal, which is 39 cm long, discovered in the shrinkage cavity of a 100-ton ingot.
Based on observations of steel solidification in a mold, three main crystallization zones can be distinguished in the cross-section of the ingot:
- Frozen crystal zone – a thin layer of metal at the mold walls, which solidifies immediately due to severe supercooling. It consists of very fine, chaotically arranged crystals.
- Columnar crystal zone – formed as a result of directional growth of crystals from the mold walls into the metal. These crystals are elongated and perpendicular to the walls, by the direction of heat transfer.
- Free crystal zone – located in the central part of the ingot, where there is no directional heat flow. Few, larger, and chaotically arranged crystals form there, which sometimes sink to the bottom of the liquid.
As crystallization progresses, the chemical composition of the residual liquid also changes. The first crystals to crystallize are relatively pure, while impurities (e.g., sulfur, phosphorus, carbon) concentrate in the solidifying liquid last, usually in the upper part of the ingot, near the shrinkage cavity. This phenomenon is known as macroscopic segregation, as opposed to microscopic segregation that occurs within individual grains.
Depending on the degree of deoxidation and degassing of the steel, different types of solidification are distinguished:
- Killed steels – well degassed, solidify calmly, with few gas bubbles. They exhibit better properties and lower impurity content.
- Non-killed steels – intensely “boiling” during solidification, with a large number of bubbles, whose structure resembles Swiss cheese. Their yield is higher, but their properties are poorer.
- Semi-killed steels – intermediate between the above, obtained by partial deoxidation, e.g., with manganese and aluminum.
Transformations in the solid state
Some metals can adopt different crystal structures depending on temperature and pressure, resulting in a phenomenon known as polymorphism or allotropy. This means that the same element can crystallize in several different structural forms, which differ in the type of spatial network.
The individual allotropic varieties are designated by Greek letters: α, β, γ, etc., which are added as indices to the chemical symbol. The α variety is typically stable at the lowest temperatures, while the other forms emerge as the temperature increases.
Each variety has its own characteristic physical, chemical, and mechanical properties. The transition from one structure to another – e.g., from hexagonal to regular – is a process comparable to crystallization from a liquid and is called secondary crystallization. During this process, the following occurs:
- nucleation (formation of a new phase),
- growth of new crystals in an already solid structure.
Since allotropic transformations occur in a solid environment, they can retain some of the crystallographic orientation of the previous phase, which is important, for example, in the heat treatment of metals. These transformations are often accompanied by thermal effects: heat release during cooling and heat absorption during heating.
On temperature graphs, this manifests as “temperature stops,” similar to those observed during melting or solidification.
Allotrope phenomena are technologically important because they change the properties of a material, such as strength, hardness, or thermal expansion. For this reason, many thermal processes (e.g., hardening or annealing) utilize the controlled transition between allotropic forms.
Allotrope transformations also tend to overheat or overcool, which in practice means that they may not occur exactly at the equilibrium temperature, but slightly above it.
What is metal crystallization – summary
The process of metal crystallization is a complex physicochemical phenomenon that depends on many factors, both thermodynamic and kinetic. Free energy, the degree of supercooling, cooling conditions, and the presence of crystal nuclei and their ability to grow are of key importance here.
Understanding the principles of crystallization enables the control of a metal’s microstructure, which in turn influences its mechanical, technological, and functional properties. This knowledge is applied, among other areas, in casting, metallurgy, alloy technology, welding, and heat treatment.
The example of iron clearly illustrates how different structural and magnetic varieties influence the behavior of a material, depending on the temperature. Therefore, knowledge of the crystallization process and phase transformations is fundamental to materials engineering and essential in industrial practice.