Methods of cathodic protection in oil pipelines
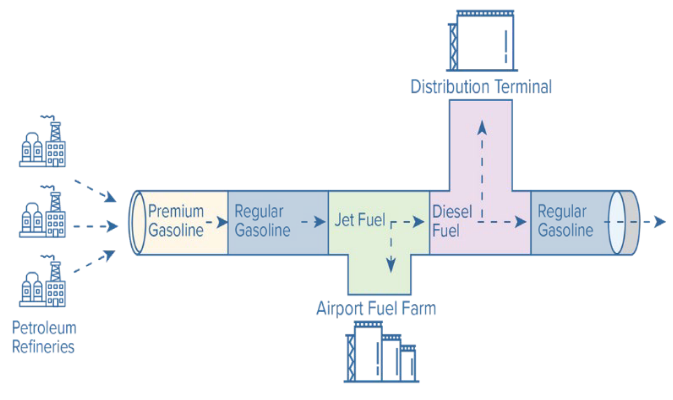
Table of contents
Corrosion is one of the most serious problems in the operation of oil pipelines. It leads to decreased structural strength, oil spills, and costly repairs and failures, which are both economic and environmental hazards. Proper protection of transmission infrastructure is key to ensuring pipelines’ long-term and safe operation.
One of the most effective methods for preventing corrosion in pipelines is cathodic protection. This electrochemical technology involves controlled delivery of electric current to the pipeline, which effectively reduces the metal’s oxidation process. This method is used in both underground and subsea pipelines, where corrosion is particularly intense.
This article will discuss the principles of cathodic protection, its types, system components and practical application in the oil industry. We will also analyze this technology’s benefits and its implementation challenges.
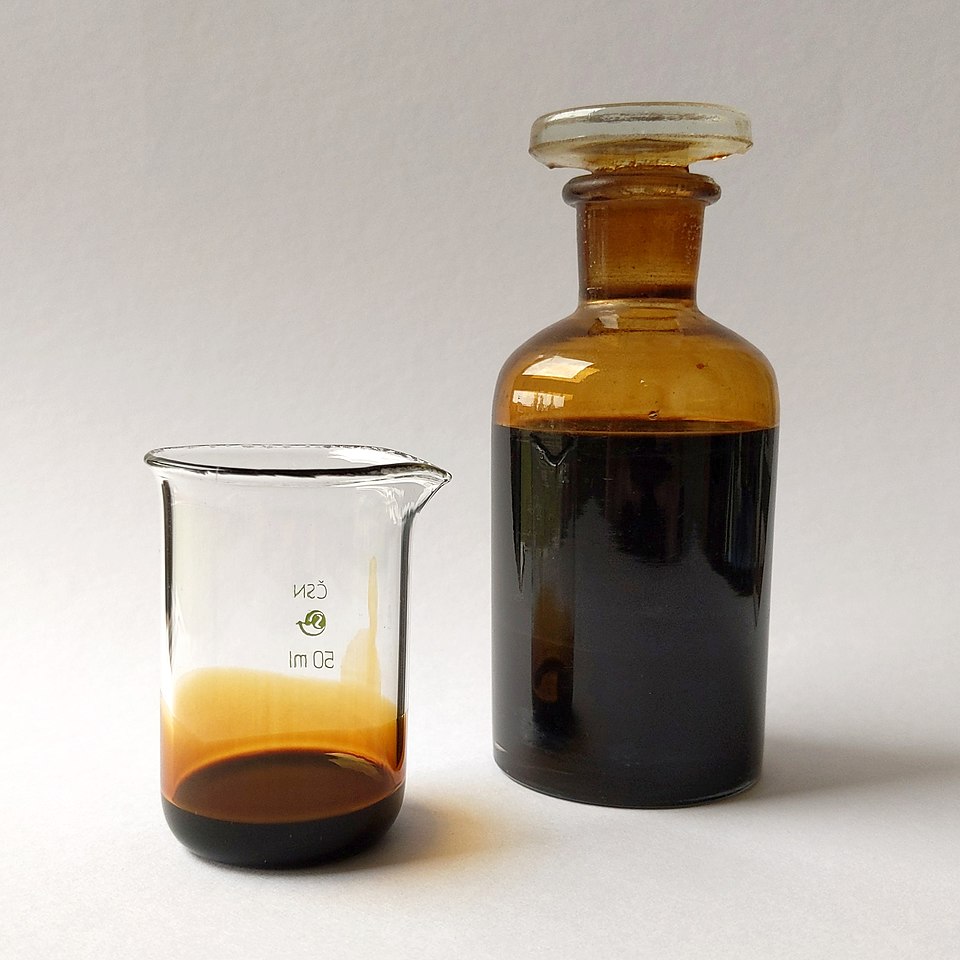
Principle of cathodic protection
Mechanism of electrochemical corrosion in pipelines
Electrochemical corrosion in metal pipelines results from the difference in electrical potentials between different parts of the structure. In the presence of moisture and electrolytes, (e.g., soil or seawater), the metal of the pipeline begins to act as a galvanic cell, where they occur:
- Anode – the area where metal oxidation and degradation occurs.
- Cathode – the area where ions from the environment are reduced and the metal does not corrode.
This process leads to gradual decomposition of the pipeline, especially in areas exposed to aggressive agents such as sulfur compounds, oxygen or chlorides.
How does cathodic protection work?
Cathodic protection involves directing the corrosion reaction so that the pipeline acts as a cathode, which eliminates metal degradation. To do this, an external electron source neutralizes the pipeline’s electrochemical potential and prevents its oxidation. In practice, cathodic protection works by:
- Lowering the electrochemical potential of the metal below the level at which corrosion occurs.
- Providing external electrons to the pipeline structure, which prevents the metal from oxidizing.
- The use of sacrificial anodes or direct current (ICCP) systems to control the flow of protective current.
Through the use of cathodic protection, corrosion processes are significantly slowed or completely inhibited, allowing for long-term protection of transmission infrastructure.
Main components of the cathodic protection system
The cathodic protection system consists of several key components:
- Anodes – responsible for providing protective current and gradual wear instead of the pipeline.
- DC sources – used in ICCP protection for controlled delivery of electrons to the pipeline.
- Sensors and reference probes – to monitor the protection level and electrochemical potential of the installation.
- Cables and connection systems – to ensure effective transmission of protective current.
These systems must be regularly monitored and maintained to ensure their effectiveness and adaptation to operating conditions.
Types of cathodic protection
Cathodic protection of oil pipelines can be implemented in two ways: by using galvanic (sacrificial) anodes or by supplying direct current from an external source (ICCP – Impressed Current Cathodic Protection). The choice of the appropriate method depends on environmental conditions, the pipeline’s length and the surrounding medium’s electrical conductivity.
Galvanic cathodic protection
Galvanic protection involves the use of sacrificial anodes, which are made of metals with a lower electrochemical potential than the pipeline material. As a result, the anode undergoes controlled corrosion, protecting the pipeline metal from degradation.
In galvanic protection systems, anodes are usually made of zinc, magnesium or aluminum. These materials have a higher electrochemical potential than pipeline steel, so that they donate electrons to the protected structure and gradually wear themselves out.
Advantages of this method include no need for an external power source, which simplifies installation, good performance in low-resistivity environments such as seawater, andminimal maintenance requirements because the system operates passively.
Unfortunately, like any method, it has its limitations: shorter life of anodes which gradually wear out and need to be replaced, and less effectiveness in high resistivity environments (e.g., dry soils), where the protective current spreads weaker.
Cathodic protection with external current (ICCP)
ICCP (Impressed Current Cathodic Protection) uses an external DC source to deliver electrons to a pipeline, eliminating the risk of corrosion. It is a more advanced method mainly used in long pipelines and high-resistivity environments.
The ICCP system uses insoluble anodes made of degradation-resistant materials such as titanium coated with mixed metal oxides (MMO), graphite, or metallurgical silicon. A rectifier that supplies voltage to the anodes generates a protective current, forcing electrons to flow into the pipeline and protecting it from oxidation.
Advantages of this method include: long-term protection because ICCP anodes do not wear out as quickly as galvanic anodes, adjustable intensity of protection allowing the level of protection to be adjusted to changing operating conditions, and the ability to protect large pipelines and offshore installations where galvanic anodes would be insufficient.
Limitations of ICCP protection: It requires electrical power, which means additional operating costs, protection against power failures, and more complicated installation requiring monitoring and periodic adjustment of the system.
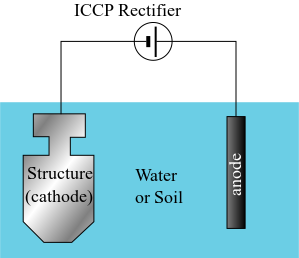
Key components of a cathodic protection system
A cathodic protection system consists of several key components that together effectively protect pipelines against corrosion. Proper selection and regular maintenance are critical to the longevity of the transmission infrastructure.
Anodes
Anodes in cathodic protection systems act as a source of electrons that counteract the corrosion process. Depending on the type of cathodic protection, different types of anodes are used:
- Galvanic (sacrificial) anodes – are made of more electrochemically active metals than pipeline steel. The most common anodes are made of zinc, magnesium and aluminum, which gradually dissolve, giving up electrons to the protected installation. They are mainly used in underground pipelines and marine installations.
- Insoluble anodes (ICCP) – used in cathodic protection systems with external current. They are made of corrosion-resistant materials such as titanium and coated with mixed metal oxides (MMO), graphite, and metallurgical silicon. Their task is to conduct protective current without wearing out, providing long-term protection for large installations.
Proper anode selection is crucial to the effectiveness of cathodic protection. Factors such as the operating environment, pipeline length, and the medium’s electrical conductivity determine the selection of a particular type of anode.
Power sources
In ICCP cathodic protection systems, a DC power source is an indispensable component that allows controlled delivery of electrons to the pipeline. There are two basic types of power sources:
- DC rectifiers – devices that convert alternating current to direct current of a certain voltage and amperage. They make it possible to precisely adjust the level of cathodic protection to the operating conditions.
- Power supply from renewable energy sources – at locations far from the power grid, power systems based on solar panels and wind turbines are used, allowing energy independence and lower operating costs.
Proper operation of an ICCP cathodic protection system requires continuous monitoring of voltage and current to ensure optimal levels of corrosion protection.
Monitoring and control of the system
To ensure the effectiveness of cathodic protection, it is necessary to continuously control the electrochemical potential of the pipeline. For this purpose, various monitoring technologies are used:
- Reference probes (measuring electrodes) – placed near the protected installation, allow measuring the potential of the pipeline relative to the environment. The most commonly used electrodes are Cu/CuSO₄ (copper/copper sulfate) for underground pipelines and Ag/AgCl (silver/silver chloride) for marine installations.
- Corrosion current sensors – detect anomalies in protective current flow, allowing rapid response in case of system failure.
- Remote monitoring systems – using IoT and telemetry technologies to keep track of cathodic protection parameters in real time and respond to potential threats.
Regular inspection and monitoring allow quick detection of potential faults and adjusting system parameters, increasing protection efficiency and reducing maintenance costs.
Cables and connection systems
In cathodic protection systems, it is extremely important to have appropriate cables and electrical connections to effectively flow protective current. Key components of the system include: cables that are resistant to corrosion and mechanical damage and covered with an insulating layer to protect against moisture and chemicals, anodic and cathodic connectors which must be adequately insulated to minimize current loss, andtest boxes and test pointsthat allow the effectiveness of the system to be checked at various locations along the pipeline.
Improperly made connections can lead to loss of protective current and ineffective corrosion protection, so the selection and quality of the electrical installation are crucial to the effectiveness of the entire system. A cathodic protection system consists of many cooperating components whose proper functioning ensures effective corrosion protection. Anodes, power sources, monitoring systems, and cables and connections must be properly sized and regularly inspected to ensure the long-term protection of oil pipelines.
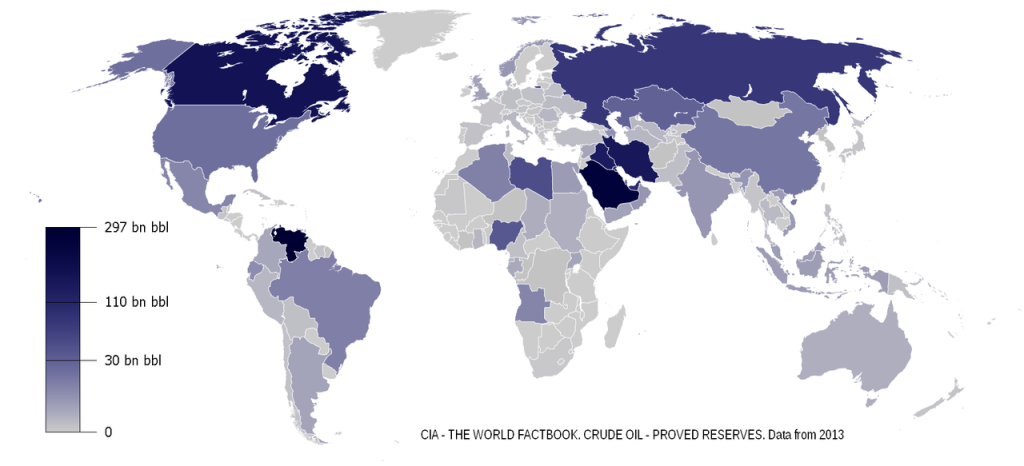
Practical application of cathodic protection in oil pipelines
Cathodic protection is one of the most widely used methods of corrosion protection in oil pipelines. It’s effectiveness has been proven in many projects around the world, in both underground and subsea installations. In this section, we will discuss real-world use cases of cathodic protection, challenges to its implementation and key industry regulations.
Application of cathodic protection in various conditions
In pipelines transporting crude oil and its products, cathodic protection is used to prevent corrosion caused by metal contact with moist soil and groundwater. In environments with low soil resistivity (e.g., wet, swampy areas), galvanic anodes are used, while in areas with high resistivity (e.g., desert areas, dry soils), ICCP protection must be used because the natural flow of protective current is limited.
Offshore transmission pipelines are exposed to strong seawater, which is a strong electrolyte that accelerates corrosion processes. In this type of environment, galvanic cathodic protection with aluminum or zinc anodes is the standard solution, as it provides long-term protection without the need for an external power supply. For large offshore structures, such as oil rigs and marine terminals, it is more common to use ICCP systems, which allow precise control of the level of protection.
Challenges in implementing cathodic protection
Despite the effectiveness of cathodic protection, its implementation is associated with various technical and operational challenges. Among the most common problems are:
- Inadequate system design – improper placement of anodes or misspecification of protection current parameters, can lead to ineffective pipeline protection or even accelerate local damage.
- Variability in environmental conditions – differences in soil composition, water salinity or temperature may require continuous adjustment of the ICCP protection system to match the level of protection to operating conditions.
- Interference with other installations – in areas with a large number of pipelines, cables or power infrastructure, there may be interference with the protective current flow, requiring detailed study and optimization of the system.
- Maintenance and monitoring – cathodic protection systems require regular inspections and measurements to ensure long-term effectiveness. Lack of proper monitoring can lead to unnoticed failures and faster pipeline degradation.
Standards and regulations for cathodic protection
Cathodic protection in the oil industry is strictly regulated by international norms and standards which specify requirements for the design, installation and monitoring of protection systems. Among the most important standards are the following:
- NACE SP0169 – an international standard developed by the National Association of Corrosion Engineers (NACE) that specifies rules for designing and maintaining cathodic protection systems for underground pipelines.
- ISO 15589-1 – an international standard governing cathodic protection of steel pipelines, considering both ICCP systems and galvanic anodes.
- DNV-RP-F103 – Guidelines for cathodic protection of pipelines and subsea structures applicable to the offshore industry.
- EN 12954 – a European standard specifying requirements for cathodic protection of pipelines transporting hydrocarbons and water.
Compliance with these regulations is key to ensuring operational safety and effective corrosion protection.
Benefits of cathodic protection
Cathodic protection plays a key role in protecting oil pipelines from corrosion, ensuring their long-term durability and reliability. It can effectively reduce the risk of failure, reduce maintenance costs and meet regulatory requirements, making it one of the most cost-effective methods of protecting transmission infrastructure.
Pipelines prone to corrosion require frequent inspections and repairs, which generate significant operating costs and the risk of downtime in the transmission of raw materials. With cathodic protection, corrosion processes are significantly slowed down or completely inhibited, allowing the installation’s life to be extended by up to several decades. This means less need to replace pipeline sections, reduced breakdowns and lower maintenance expenses.
Inadequate corrosion protection can lead to oil and gas leaks, which pose a serious environmental threat and can result in severe financial penalties for pipeline operators. Cathodic protection systems minimize the risk of pipeline perforations and uncontrolled leaks, preventing environmental disasters and increasing the safety of crude transportation.
In addition to the technical aspects, cathodic protection is also necessary to meet international safety standards, such as NACE SP0169 and ISO 15589-1, which regulate the use of corrosion prevention measures. Implementing this technology avoids problems of non-compliance and reduces the financial risks of possible sanctions and damages.
Methods of cathodic protection in oil pipelines – summary
Cathodic protection is an indispensable method of protecting oil pipelines from corrosion, ensuring their longevity and reliability. It effectively reduces metal degradation, reduces the risk of failure and lowers maintenance costs.
Today’s cathodic protection systems, supported by modern monitoring and regulation technologies, make it possible to effectively adjust the level of protection to changing conditions. Their use is not only recommended, but also required by international norms and safety standards, making them an indispensable part of oil infrastructure management.
This article is based on the book “Metallurgy and Corrosion Control in Oil and Gas Production”, Robert Heidersbach.