Introduction to CAD Software
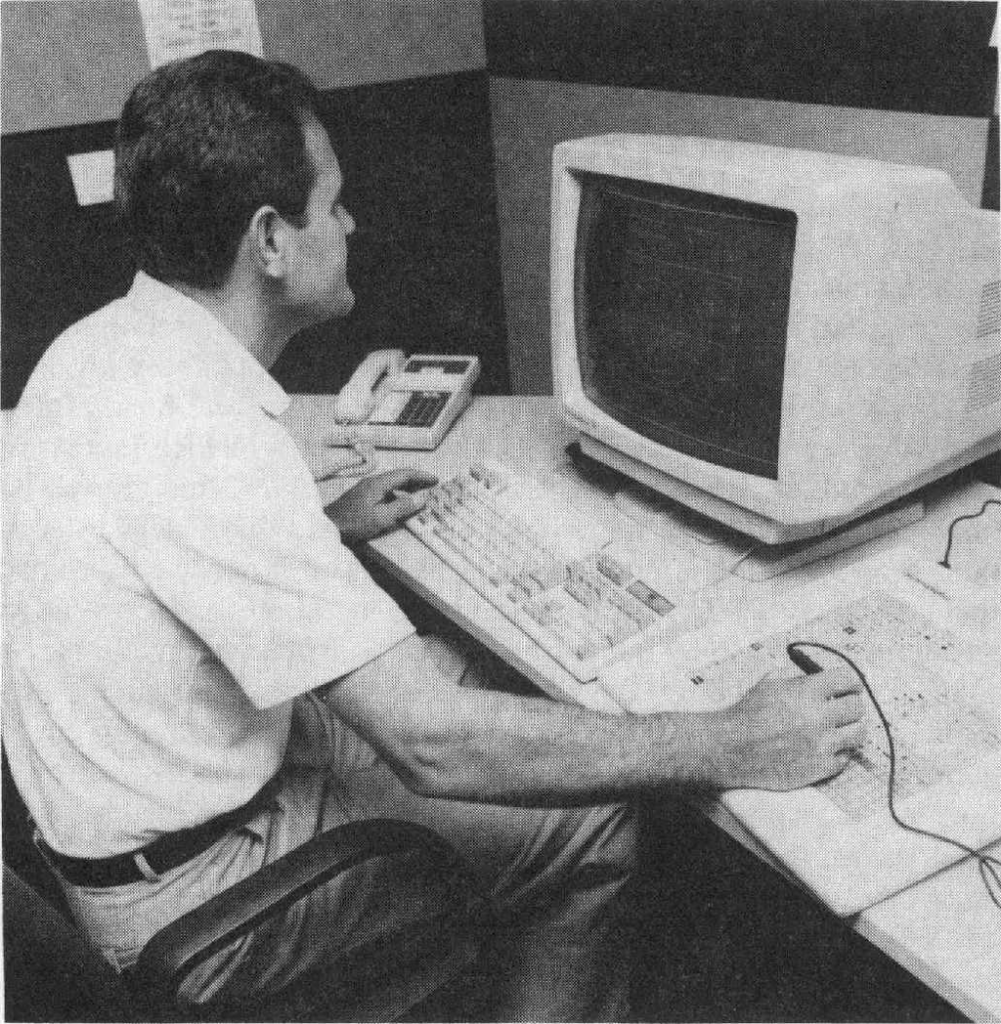
Table of contents
The development of information technology over the past decades has significantly affected how products are designed and manufactured. Digital transformation and automation of manufacturing processes have led to the development of tools to support these changes. One of the key solutions is CAD (Computer-Aided Design) software, which enables precise modeling and analysis of technical designs. This article outlines CAD software’s origins, functionality, and applications, focusing on its role in the engineering, architecture, and technology industries.
History and Definition of CAD
The origins of CAD software date back to the 1960s, when the first programs were developed to create technical drawings on computer screens. The first CAD systems were developed in response to the needs of the mechanical, architectural, and electronic design industries, which required more precise methods of developing technical documentation. The development of CAD was closely linked to advances in computer graphics, the increasing computing power of computers, and the automation of engineering processes.
As early as the 1950s, experiments with computer-aided design began. One of the pioneers was Patrick J. Hanratty, who, in 1957, created the PRONTO system, the first commercial CAD system to design numerical control of machines. It was the foundation for later-developed CAD programs.
A key moment was the appearance of the Sketchpad system by Ivan Sutherland in 1963. This system enabled the creation of drawings on a computer screen using a light stylus, a breakthrough in human-computer interaction. Sketchpad laid the foundation for future CAD programs and introduced concepts such as hierarchical object structures, geometric relationships, and editable nodes, which are the basis of today’s CAD tools.
The 1970s and 1980s saw the first commercial CAD programs, such as CATIA (1977) and AutoCAD (1982), which revolutionized design in many industries. CATIA gained popularity in the aerospace and automotive industries, while AutoCAD quickly became the standard in architecture and civil engineering due to its accessibility and ease of use.
Today, CAD software can be defined as a computer tool used to support the design, modeling, and documentation of products. Today’s CAD systems offer various capabilities, from creating simple 2D drawings to complex three-dimensional (3D) models. Thanks to built-in analysis and simulation functions, CAD also enables the testing of a design before its physical realization, significantly reducing production costs and shortening time to market.
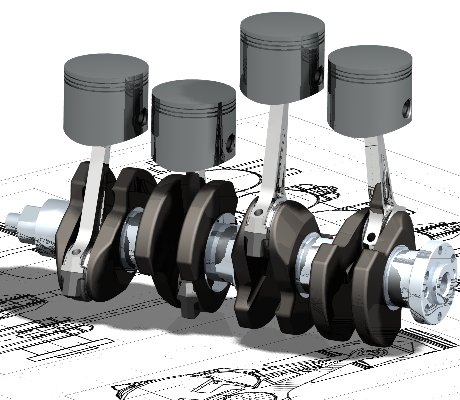
Basic Features of CAD Software
Geometric Modeling
CAD enables the creation of accurate 2D and 3D models that reflect the geometry of the designed object. Geometric modeling is the foundation of computer-aided design, allowing the creation of accurate representations of objects in space.
2D models are mainly used for technical drawings, schematics, and construction plans. They enable accurate representation of details, dimensions, and technical descriptions, which is crucial in architecture and mechanics.
3D models, on the other hand, allow for a realistic representation of objects in three dimensions. Such models can be rotated, scaled, and analyzed from different perspectives, making testing their functionality and compatibility easier. 3D modeling also supports visualization processes, enabling designers to present prototypes to clients and investors.
Advanced geometric modeling features include:
Analysis and Simulation
CAD programs offer tools for conducting strength, kinematic, and dynamic analysis. These functions allow detailed evaluation of the behavior of designed objects under realistic conditions.
Strength analyses include the evaluation of stresses, strains, and critical points in mechanical structures. They enable the optimization of materials and shapes, increasing the durability and safety of products. These tools are crucial in the design of components subjected to high loads, such as bridges, aircraft fuselages, and industrial machinery components.
Kinematic analyses allow the study of the motion of gears, levers, and hinge mechanisms. Kinematic simulations help engineers evaluate motion trajectories, rotation ranges, and collisions between components. This makes it possible to design systems with precisely controlled motion.
Dynamic analyses focus on studying the effects of time-varying forces, such as vibration and impact. They are used to test the resistance of designs to dynamic loads, which is particularly important in the automotive and aerospace industries. The analyses also support the design of vibration damping and increased structural stability.
CAD enables detailed numerical simulations through integration with FEA (Finite Element Method) modules. Thermal, flow, and electromagnetic analyses are other applications that help comprehensively examine designs before they are put into production.
Technical Documentation Automation
Creating technical drawings, bills of materials (BOMs), and manufacturing specifications is one of the key functions of CAD software, streamlining manufacturing processes and eliminating errors resulting from manual documentation.
Technical drawings generated in CAD are precise and comply with international standards (e.g., ISO, ANSI). They contain detailed information on dimensions, tolerances, and materials, allowing them to be used directly in production processes. CAD programs allow quick application of corrections and automatic updating of drawings based on changes in 3D models.
A bill of materials (BOM) lists all the components that make up a project, considering standard and non-standard components. The BOM facilitates supply chain management, production planning, and cost control. Through integration with Enterprise Resource Planning (ERP) systems, this data can be directly transferred to purchasing and logistics departments.
Manufacturing specifications include detailed instructions for assembly, machining, and inspection processes. They can include assembly diagrams, CNC tool parameters, and quality control information. Specification automation eliminates the risk of errors and reduces the time it takes to put a project into production.
With documentation automation features, CAD not only speeds up the work of designers but also supports communication between engineering, manufacturing, and inspection teams, ensuring that data is consistent and meets design intent.
Visualization
The ability to generate realistic renders and animations makes it easier to present a design. Visualization in CAD software plays a key role in the design process, enabling the creation of photorealistic images and dynamic animations of models.
Photorealistic rendering allows simulation of the appearance of materials, lighting, and shadows so designers can create presentations that accurately represent the final product. This feature is particularly useful in architecture, interior design, and consumer products, where the visual impact of the final product is a key aspect.
Animations make it possible to show the operation of mechanisms and assembly processes, making it easier to understand the function of a design. Animations are widely used to show dynamic mechanisms such as motors, hinges, and manufacturing processes.
Visual simulations support the analysis of ergonomics and user interaction with the design. Examples include simulations of vehicle interiors, machinery, or workspaces to assess the comfort and functionality of designs.
Interactive presentations and virtual reality (VR) are modern extensions of visualization functions, allowing designers and clients to explore models in real-time. With VR, it is possible to check the scale, proportions, and functionality of designs in virtual space before production begins.
With advanced visualization tools, CAD enables the creation of impactful marketing materials, digital prototypes, and demonstrations that improve communication and design decisions.
Integration with CAM
Combining CAD with CAM (Computer-Aided Manufacturing) software enables automation of manufacturing processes. CAM systems allow CAD designs to be converted into CNC (Computer Numerical Control) machine control instructions, eliminating the need for manual programming. This makes the manufacturing process more precise, repeatable, and efficient.
CAD/CAM integration allows direct collaboration between design and manufacturing, reducing time spent on marketing. Designers can test and optimize models in the CAD environment and then transfer them directly to CAM systems, where they are converted into machine code.
In addition, CAM software supports operations such as milling, turning, laser cutting, waterjet cutting, and 3D printing. This makes it possible to produce both simple components and complex structures with high precision.
Modern CAD/CAM systems also support integration with Industry 4.0 technologies, enabling real-time monitoring of manufacturing processes and automatic adjustment of machine parameters in response to design changes or quality requirements.
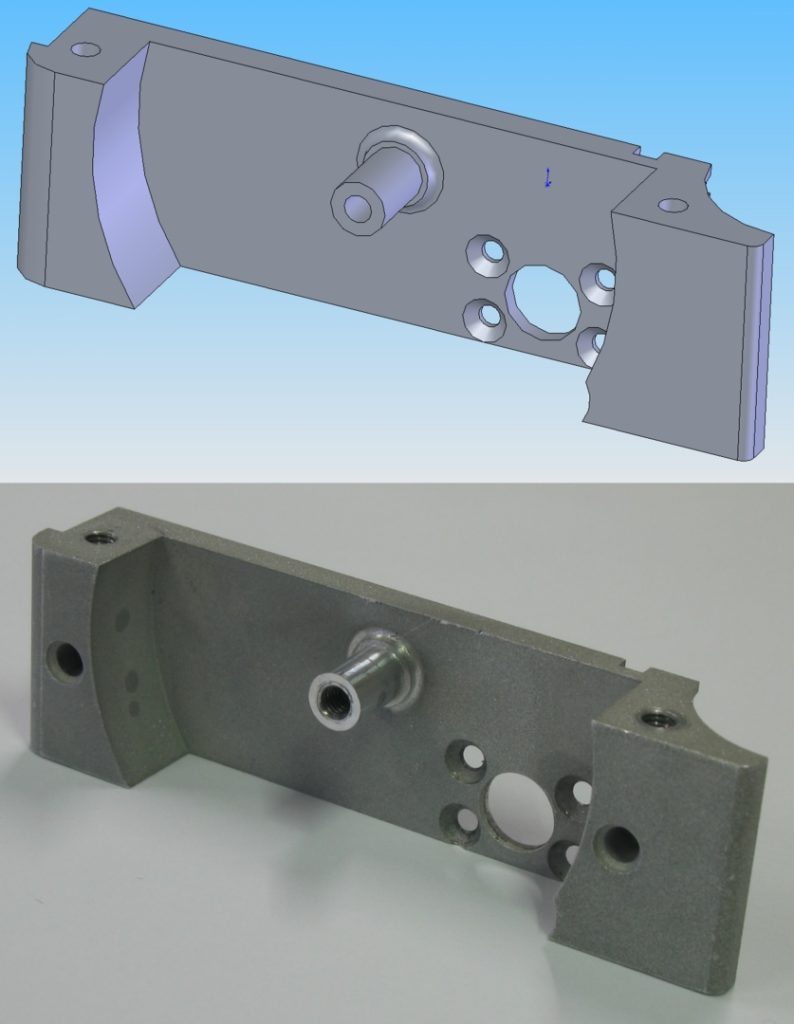
CAD applications
CAD software is used in many industries:
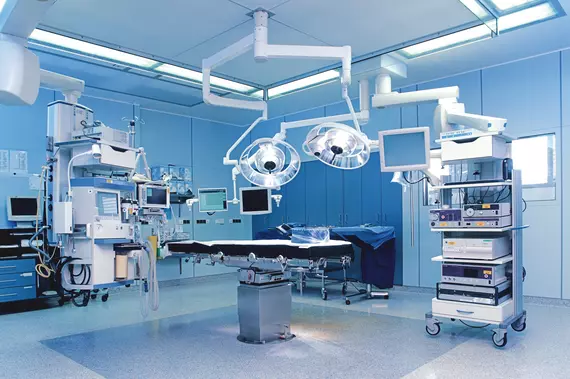
Future Trends in CAD
The future of CAD software is focused on integration with modern technologies:
Introduction to CAD Software – Summary
CAD software has become an indispensable tool in modern design and manufacturing. Its versatility, precision, and integration with modern technologies make it applicable to many industries. The future of CAD is further developed towards automation, intelligent analysis, and integration with virtual and augmented reality systems. This will ensure that CAD remains a key element in supporting innovation and industrial development.