Structure and properties of metal alloys
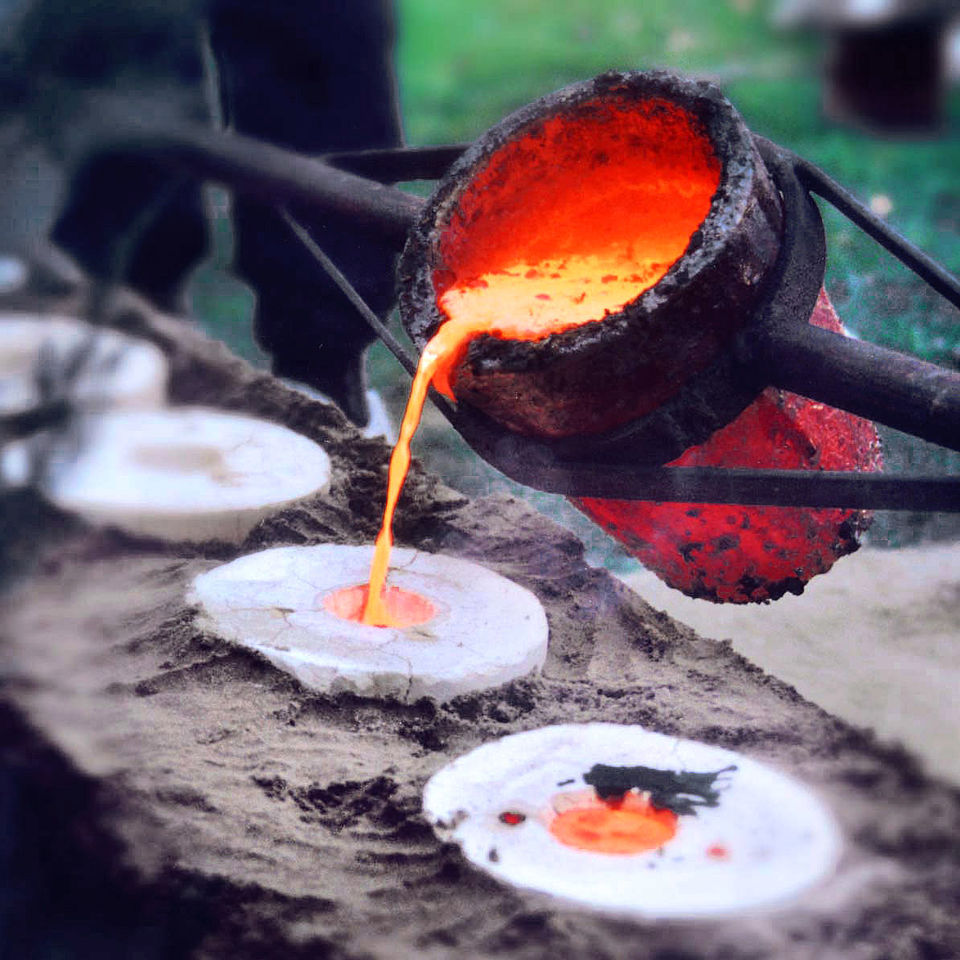
Table of contents
Why are pure metals not enough
Although pure metals have their unique properties, in technical practice, they are rarely sufficient. Aluminum, iron, and copper in their pure form are often too soft, not resistant to abrasion, corrosion, or high temperatures, to meet the requirements of modern construction materials. That is why, for centuries, people have been seeking ways to improve metals – and this has led to the creation of alloys, i.e., mixtures of two or more elements, at least one of which is a metal.
Melting different components and controlling their solidification enables the creation of entirely new materials, whose mechanical, physical, and chemical properties can be precisely tailored to specific applications. An example is steel, in which the mere addition of carbon to iron drastically changes its hardness and strength, making it one of the most common and versatile engineering materials.
The properties of alloys result not only from the presence of alloying elements, but also, and often primarily, from their internal structure. The arrangement of atoms in the crystal lattice, how individual elements are distributed throughout the material, the occurrence of different phases and transformations – all these factors are crucial for the behavior of an alloy under actual operating conditions. Understanding these relationships allows materials to be designed purposefully, not only by selecting their chemical composition, but also by controlling their internal structure.
In the following sections of this article, we will examine various types of alloy structures, ranging from solid solutions to intermetallic compounds and complex phases with unusual electronic structures. We will see that what happens at the atomic level determines how the entire material behaves.
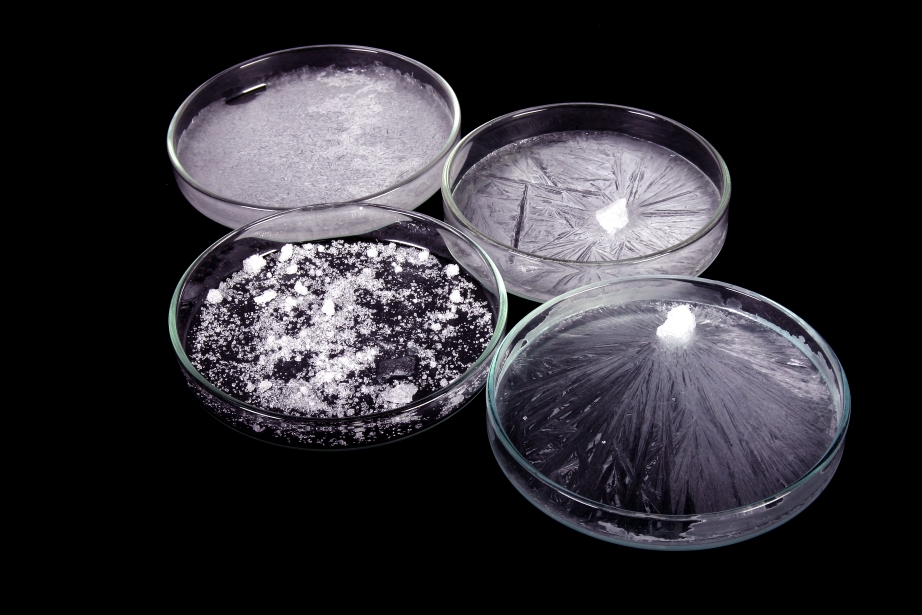
Metal alloys in the liquid and gaseous state
Although we most often analyze metal alloys in their solid state, their history begins much earlier, when the components are combined in liquid form. In this state, the atoms are arranged randomly, move freely relative to each other, and form a homogeneous mixture, provided that they are mutually soluble. Liquid alloys, such as molten iron, copper, or aluminum, exhibit properties typical of liquids, yet they also have the potential to form complex structures after solidification.
In the liquid state, very intense diffusion occurs, which promotes the even distribution of elements throughout the metal volume. Additionally, from a practical point of view, the ease of mixing of the components and their chemical homogeneity in the liquid facilitate control over the casting or solidification process. Nevertheless, it is at the moment of crystallization that the formation of the alloy structure begins, and the course of this process depends not only on the composition but also on the cooling rate and the presence of crystallization nuclei.
Under special conditions, gaseous alloy systems may also form, although these are of more laboratory than industrial significance. An example is metal mixtures in the vapor state, which form homogeneous systems in which the vapors of individual components can react with each other before condensation occurs. These phenomena are critical, among other things, in vacuum coating technology and physicochemical research, where phase equilibria are analyzed over a wide range of temperatures.
Both the liquid state and, to a limited extent, the gaseous state play a crucial role in materials engineering during the initial phases of alloy structure formation. It is often at the liquid solution stage that the chemical homogeneity, purity, and formability of a specific phase after solidification are determined. Therefore, understanding the phenomena occurring at high temperatures is a key stage in the design and quality control of modern metal alloys.
Solid solutions
As the liquid alloy crystallizes, the atoms of individual elements begin to occupy specific positions in the emerging crystal lattice. When the atoms of an impurity element penetrate the crystal structure of the base metal, forming a homogeneous phase with a constant distribution of components, we have a solid solution. This type of structure serves as the basis for most industrial metal alloys and represents the fundamental form of material reinforcement, eliminating the need to create separate chemical compounds.
Solid solutions can only form when the atoms of different elements are sufficiently compatible in terms of size, lattice structure, and electron structure. When these conditions are met, the impurity atoms can be incorporated into the crystal lattice of the parent metal without significantly distorting it. It is this arrangement that allows phase continuity to be maintained while introducing local disturbances that significantly affect the physical and mechanical properties of the material.
One of the key features of solid solutions is their single-phase nature. Regardless of the number of components, the entire material has a uniform crystal structure, which distinguishes it from multiphase systems in which several different types of crystallization coexist. Solid solutions therefore enable the material to remain cohesive while allowing its parameters to be controlled, for example by increasing its strength, hardness, or corrosion resistance.
Almost every technical alloy – from bronzes and brasses, through alloy steels, to nickel superalloys – contains solid solutions as a fundamental structural component. Their presence determines how the material behaves during plastic machining, how it reacts to temperature changes, and how it ages or undergoes phase transformations during use.
Intergranular and intragranular solid solutions
Although the term “solid solution” refers to a homogeneous phase, its actual nature can take various forms, depending on where and how the impurity atoms are distributed in the crystal lattice of the base metal. There are two basic types of solutions: interstitial and intrastipital, each of which involves a different mechanism for incorporating foreign atoms and has a distinct effect on the material’s properties.
In interstitial solutions, the atoms of the impurity component replace some of the atoms of the base metal in the regular lattice sites of the crystal lattice. This means that, while maintaining the type and symmetry of the lattice, impurities enter directly into its structure, modifying the local distances between atoms and the internal stresses. Such solutions can form when the atomic radius of the impurity element is close to that of the parent atom, while maintaining structural and electronic compatibility. An example of such a system is a copper-nickel alloy, where both lattices have similar crystallographic parameters, allowing nickel impurities to easily replace copper atoms.
In interstitial solutions, on the other hand, the atoms of the impurity element do not occupy lattice sites, but penetrate the free spaces—the so-called interstitial cavities—between the atoms of the base metal. This type of solution is characteristic of situations where the impurity atoms are much smaller than the solvent atoms. In the case of metals, this most often applies to non-metallic elements such as carbon, nitrogen, or hydrogen, which can penetrate the metal structure, forming so-called interstitial solutions. A classic example of this is steel, which is a solution of iron and carbon in which small carbon atoms are embedded in the spaces between the iron atoms.
Both types of solid solutions significantly affect the mechanical properties of metals. The introduction of impurities – both into the lattice nodes and into the interstitial spaces – causes local disturbances in the structure, which hinder the movement of dislocations and thus increase the hardness and strength of the alloy. At the same time, they can affect thermal and electrical conductivity, chemical resistance, and the material’s behavior during plastic working.
How the crystal lattice affects the properties of metal alloys
In an ideal solid solution, the distribution of impurity atoms in the crystal lattice of the parent metal can be random, leading to a statistical scattering of foreign atoms among the solvent atoms. However, in many cases, especially at appropriate concentration ratios and under specific temperature conditions, atoms begin to show a tendency to orderly arrangement in the lattice space. Instead of a random arrangement, they form repetitive configurations that lead to the formation of ordered structures with their distinct physical properties.
This type of order consists of atoms of different elements occupying strictly defined positions in the lattice, forming a superstructure in which it is possible to predict which type of atom will be found at a given node. Such structures usually arise when there are strong chemical interactions or differences in binding energy between the elements in the alloy, which favor specific spatial configurations. The ordering process can occur spontaneously during slow cooling of the alloy or be induced deliberately by appropriate heat treatment.
The ordering of atoms not only changes the local geometry of the crystal lattice but also affects the mechanical, electrical, and magnetic properties of the material. Compared to disordered solutions, ordered structures often exhibit greater hardness and thermodynamic stability, but may also be characterized by reduced plasticity, which is essential in structural and technological applications.
An example of an ordered structure is the Cu₃Au system, in which copper and gold atoms occupy specific positions in a space-centered cubic lattice. In this configuration, a phase with a regular atomic distribution is formed, which confers material properties not present in a standard, random solution of the same elements. Ordered solid solutions can also exhibit characteristic diffraction effects, allowing their presence to be detected and analyzed using X-rays.
The introduction of structural order is one of the more subtle ways of engineering material properties. It not only improves performance but also allows precise control of the structure at the atomic level, which is becoming an increasingly desirable and widely used tool in today’s materials industry.
Intermetallic phases and chemical compounds
In specific alloy systems, instead of simple solid solutions – even ordered ones – completely new crystal structures form, distinct from both the base metal and the alloying element. These new, independent structural forms, known as intermetallic phases, are one of the most complex phenomena in alloy engineering. Although they appear to be mixtures of two or more elements, their nature is more similar to chemical compounds than to typical solutions.
Intermetallic phases are characterized by a strictly defined ratio of the atoms of the elements that make them up, which means that their chemical composition is not fluid but limited to a narrow stoichiometric range. Their crystal structure features a regular, orderly arrangement of atoms in specific, often complex configurations, sometimes completely different from those found in the fundamental structures of metals. These can be cubic, rhombic, tetragonal, or even hexagonal systems with a vast number of atoms in the unit cell.
The formation of intermetallic phases is most often the result of strong chemical interactions between the components, such as differences in electronegativity, ionic radius, or electronic structures. They are often the result of a local energy balance in which the arrangement of atoms in a regular, compact compound proves more advantageous than the random arrangement characteristic of solid solutions. Examples of such phases are Fe₃C (cementite), Mg₂Pb, and CuZn, as well as more exotic arrangements used in titanium, nickel, and aluminum alloys.
Intermetallic phases have a significant impact on the properties of a material. On the one hand, they can significantly increase hardness and abrasion resistance, as they are often very brittle and difficult to deform. On the other hand, their presence can reduce plasticity and machinability, which requires careful balancing of their quantity and distribution. In engineering materials, particularly in steels and superalloys, these phases are often intentionally controlled components of the microstructure, achieved through appropriate heat treatments such as annealing or aging.
Managing the presence of intermetallic phases is a significant challenge in modern metallurgy. Their proper formation can lead to the creation of materials with unique properties – from super-hard tools to creep-resistant alloys and modern functional coatings used in aerospace technologies.
Electron and interstitial phases
In addition to classic solid solutions and intermetallic phases, some metal alloys exhibit even more complex systems known as electron phases and interstitial phases. Their formation is no longer determined solely by crystal lattice geometry and simple stoichiometric relationships, but by more complex electronic interactions that influence their stability and properties.
Electron phases arise in alloys in which the decisive factor for the stability of the structure is not a specific ratio of atoms, but the ratio of valence electrons to the number of atoms in the crystal lattice. In simpler terms, a particular number of electrons per unit of structure determines whether a given configuration is energetically favorable.
This phenomenon has been described in detail within the Hume-Rothery concept, which shows that in certain alloys, particularly those containing transition metals, the formation of ordered structures depends on threshold values of the number of electrons per atom. This enables the prediction of which phases will form in a given alloy system, even when the differences in atomic radii and electronegativity are not immediately apparent.
Interstitial phases, on the other hand, are characteristic of systems in which small atoms, such as carbon, boron, or hydrogen, occupy the empty spaces within the crystal lattice of a larger metal, forming stable systems with well-defined stoichiometric proportions. Unlike simple interstitial solutions, the arrangement of small atoms here is not random. Still, it follows specific rules, resulting in the formation of a highly ordered structure with a distinct unit cell. An example of such a phase is cementite (Fe₃C), where carbon atoms penetrate the iron structure, forming a compound that is very hard but brittle.
Both electron and interstitial phases are critical from the perspective of materials engineering. Their presence in an alloy can significantly alter the material’s mechanical, thermal, and electrical properties. Thanks to their controlled precipitation, it is possible to create materials with increased creep resistance, increased hardness, and resistance to high temperatures and aggressive chemical environments. Such properties are particularly valued in the aerospace, nuclear power, and tooling industries, where there is no room for compromise between durability and safety.
Although their structures are complex and their formation mechanisms difficult to grasp without advanced research methods, these phases are becoming an increasingly desirable tool for the deliberate modeling of the microstructure and properties of modern materials.
Structure and properties of metal alloys – summary
Modern materials engineering is not only about selecting the correct elements, but above all about consciously shaping the internal structure of materials, from the atomic level to the micro- and macrostructure. Metal alloys are not just a mechanical mixture of components – they are complex systems in which the arrangement of atoms, their interactions, and their organization in space determine their final physical, chemical, and technological properties.
Understanding the mechanisms of solid solution formation, intermetallic phases, and electron phases, as well as their influence on crystal structure, enables us not only to better interpret the behavior of known materials but also to design new ones with precisely defined properties. It is thanks to this knowledge that alloys are now being developed that can withstand the extreme temperatures of jet engines. These shape memory alloys respond to thermal stimuli, and steels that are resistant to wear in the most demanding industrial environments.
The structure of alloys is therefore not just a subject of theoretical analysis – it is the foundation for all technological, design, and operational activities. The ability to predict how a given additive will affect the structure and what phases may form in a given system is one of the most essential tools available to a materials engineer. Therefore, deepening our knowledge of the internal structure of metals and their alloys remains a key element in the development of modern technologies and innovation-based industry.