Korrosionsbeständige Legierungen in der Ölindustrie
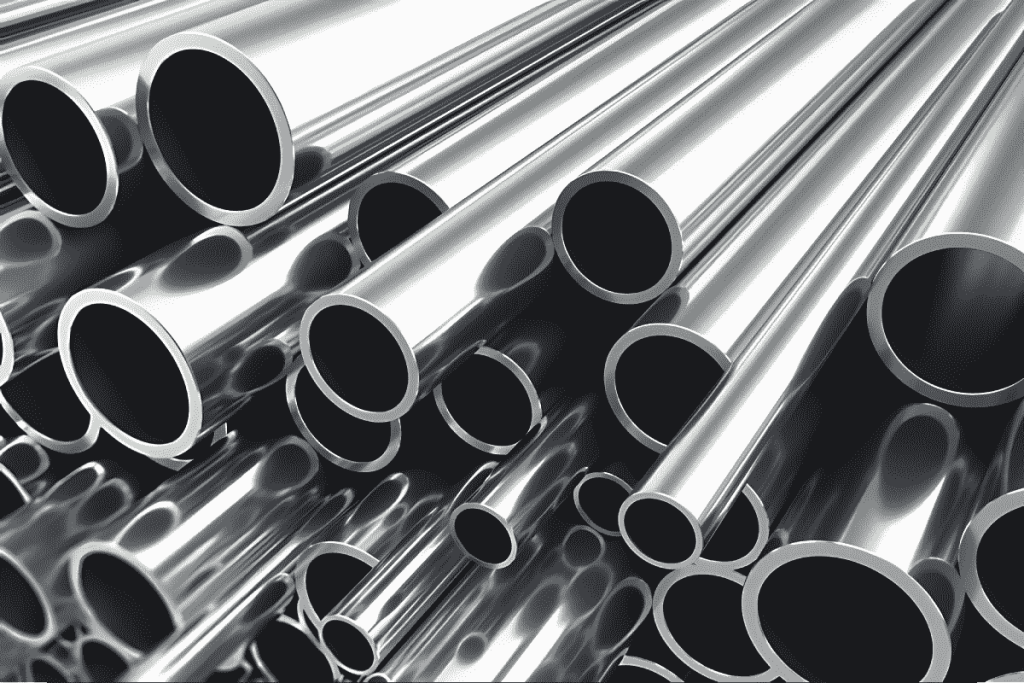
Inhaltsverzeichnis
Die Öl- und Gasindustrie benötigt Werkstoffe, die extremen Betriebsbedingungen wie hohem Druck, aggressiven chemischen Umgebungen und wechselnden Temperaturen standhalten können. Die Wahl der richtigen Werkstoffe für Pipelines, Tanks oder Offshore-Anlagen ist entscheidend für die Sicherheit, Haltbarkeit und Betriebskosten der Infrastruktur.
Kohlenstoffstahl und korrosionsbeständige Legierungen gehören zu den am häufigsten verwendeten Werkstoffen in diesem Sektor. Kohlenstoffstahl wird aufgrund seiner hohen mechanischen Festigkeit und relativ geringen Kosten häufig für den Bau von Rohrleitungen und Stützkonstruktionen verwendet. Seine Anfälligkeit für Korrosion in aggressiven Umgebungen macht es jedoch notwendig, korrosionsbeständige Legierungen wie Edelstahl, Nickel oder Titan in vielen Anwendungen zu verwenden.
In diesem Artikel werden die Eigenschaften von Kohlenstoffstahl und korrosionsbeständigen Legierungen, ihre Vorteile und Grenzen sowie ihre wichtigsten Unterschiede erörtert. Diese Analyse ermöglicht ein besseres Verständnis der Bedingungen, unter denen ein bestimmter Werkstoff am effektivsten ist, und der Trends bei der Entwicklung neuer Werkstofftechnologien.
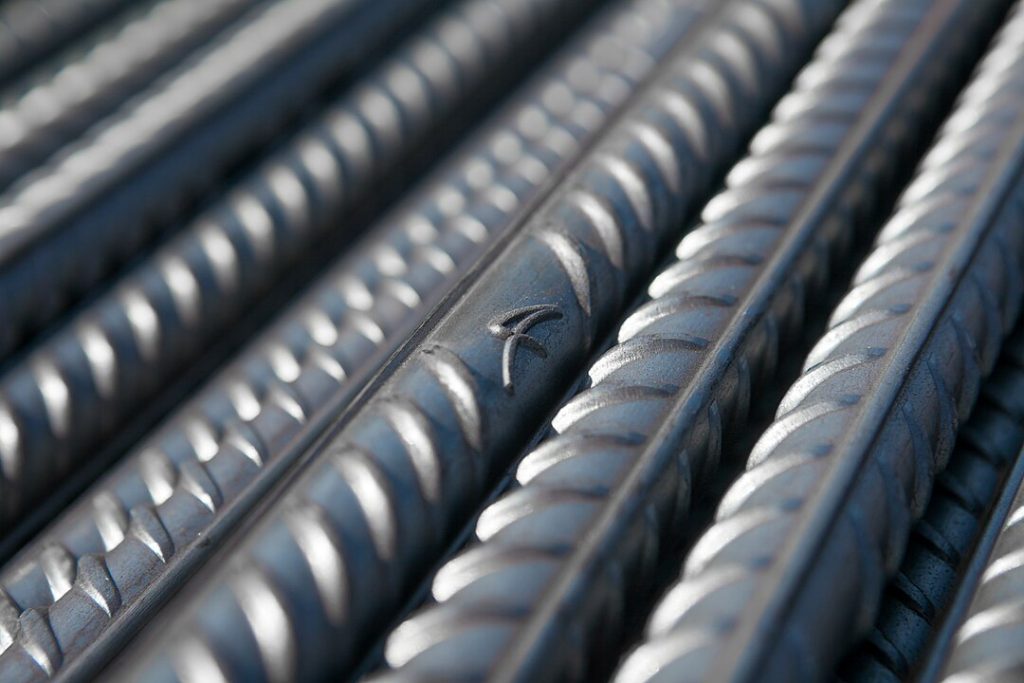
Kohlenstoffstahl – Eigenschaften und Anwendungen
Kohlenstoffstahl ist eine Legierung aus Eisen und Kohlenstoff, mit einem Kohlenstoffgehalt von in der Regel bis zu 2%. Je nach Kohlenstoffgehalt gibt es niedriggekohlte, mittelgekohlte und hochgekohlte Stähle. Die Ölindustrie verwendet hauptsächlich Stähle mit niedrigem Kohlenstoffgehalt, die eine gute Schweißbarkeit und Duktilität aufweisen, aber anfälliger für Korrosion sind als Legierungen mit einem höheren Gehalt an schützenden Legierungszusätzen.
Kohlenstoffstahl wird in der Ölindustrie vor allem wegen seines Preis-zu-Festigkeits-Verhältnisses verwendet. Seine Hauptvorteile sind: niedriger Preis – Kohlenstoffstahl ist viel billiger in der Herstellung als spezielle korrosionsbeständige Legierungen, gute mechanische Festigkeit – dadurch kann er in Strukturen verwendet werden, die schweren Belastungen ausgesetzt sind, und einfache Verfügbarkeit und Verarbeitung – die Möglichkeit der Massenproduktion und die einfache Schweiß- und Formgebung machen ihn weit verbreitet im Bau von Pipelines und Lagertanks.
Trotz dieser Vorteile hat Kohlenstoffstahl eine begrenzte Korrosionsbeständigkeit, insbesondere wenn er Meerwasser, Säuren und korrosiven Gasen ausgesetzt ist. In schwefelwasserstoffreichen Umgebungen können schwere Schäden durch Sulfidkorrosion auftreten, die zu Wasserstoffversprödung und Rissbildung im Material führen. Dieses Problem erzwingt den Einsatz zusätzlicher Schutzmethoden wie Korrosionsschutzbeschichtungen, Korrosionsinhibitoren und kathodischen Schutz, was wiederum die Betriebskosten erhöht.
Korrosionsbeständige Legierungen – Arten und Eigenschaften
Nichtrostende Stähle
Nichtrostende Stähle sind Legierungen aus Eisen, Chrom und oft auch Nickel und Molybdän, die durch die Bildung einer Schutzschicht aus Chromoxiden auf der Metalloberfläche eine hohe Korrosionsbeständigkeit aufweisen. Diese Schicht verhindert eine weitere Zersetzung des Materials, so dass sich nichtrostende Stähle für den Einsatz in aggressiven chemischen Umgebungen, hohen Temperaturen und unter Meerwassereinfluss eignen. Rostfreier Stahl wird verwendet in:
- Übertragungssysteme in Meeresumgebungen, wo das Wasser Chloride enthält, die die Korrosion beschleunigen.
- Industrielle Hochtemperatursysteme, in denen herkömmlicher Kohlenstoffstahl beschädigt werden könnte.
- Raffinerietanks und Systeme, die aggressiven Chemikalien ausgesetzt sind.
Die breite Anwendung von nichtrostenden Stählen in der Erdölindustrie ist hauptsächlich auf ihre Vielseitigkeit und günstigen mechanischen Eigenschaften zurückzuführen. Sie werden in Transportleitungen, Lagertanks und Apparaten für Raffinerieprozesse verwendet, wo der Kontakt mit korrosiven Substanzen unvermeidlich ist.
In der Schifffahrt sind nichtrostende Stähle oft das Baumaterial der Wahl, weil sie gegen Chloride resistent sind, die die Lochkorrosion beschleunigen. In Hochtemperatursystemen wie Wärmetauschern und Raffinerieöfen behalten nichtrostende Stähle ihre Stabilität und Festigkeit bei, so dass sie über lange Zeiträume hinweg eingesetzt werden können, ohne dass die Gefahr einer Schwächung der Metallstruktur besteht.
Trotz ihrer vielen Vorteile können nichtrostende Stähle anfällig für Spannungsrisskorrosion und Lochkorrosion sein, insbesondere in Gegenwart von aggressiven Chloridionen. Daher werden unter extremen industriellen Bedingungen oft zusätzliche Schutzmaßnahmen wie Korrosionsinhibitoren oder Schutzbeschichtungen eingesetzt, um die Lebensdauer des Materials weiter zu verlängern.
Nickel- und Titan-Legierungen
Nickel- und Titanlegierungen gehören zu den fortschrittlichsten korrosionsbeständigen Werkstoffen für den Einsatz unter anspruchsvollsten Betriebsbedingungen. Aufgrund ihrer einzigartigen chemischen und mechanischen Eigenschaften werden sie in Anlagen eingesetzt, die unter extremen Temperaturen, sauren Umgebungen und Hochdruckbedingungen arbeiten.
Nickellegierungen wie Inconel weisen eine außergewöhnliche Beständigkeit gegen Schwefelwasserstoff (H₂S), Säuren und hohe Temperaturen auf, was sie ideal für Tiefbohrungen und Raffinerieanlagen macht. Dank ihrer metallurgischen Struktur sind sie auch resistent gegen Spannungskorrosion, was Risse und Ausfälle in Tiefseesystemen verhindert.
Titan und seine Legierungen zeichnen sich durch ihre extrem hohe Korrosionsbeständigkeit im Meerwasser aus, was sie für den Einsatz in Offshore-Strukturen, Ölplattformen und Unterwasser-Pipelines geeignet macht. Ihre im Vergleich zu anderen Metallen geringe Dichte ermöglicht den Bau von leichten und dennoch stabilen Strukturen, die unter extremen Bedingungen viele Jahre lang ohne Wartung betrieben werden können.
Eine der Hauptbeschränkungen bei der Verwendung von Nickel- und Titanlegierungen sind ihre hohen Kosten, die ihre Verwendung oft auf die anspruchsvollsten Anwendungen beschränken. Aus diesem Grund werden häufig Hybridlösungen verwendet, bei denen Bauteile aus korrosionsbeständigen Legierungen mit preiswerteren Werkstoffen wie Kohlenstoffstahl kombiniert werden, die zusätzlich gegen Degradation geschützt sind.
Trotz des hohen Preises von Nickel- und Titanlegierungen sind sie aufgrund ihrer Zuverlässigkeit und ihres geringen Wartungsbedarfs in Bereichen, in denen ein Versagen zu katastrophalen ökologischen und wirtschaftlichen Folgen führen könnte, nicht zu ersetzen.
Die Wahl zwischen nichtrostenden Stählen und Nickel- und Titanlegierungen hängt in erster Linie von den Umweltbedingungen und den Besonderheiten der Anwendung ab. Nichtrostende Stähle bieten ein günstiges Verhältnis zwischen Preis und Korrosionsbeständigkeit, während Nickel- und Titanlegierungen selbst in den extremsten Umgebungen maximalen Schutz bieten, allerdings zu wesentlich höheren Betriebskosten. Die Erdölindustrie ist bestrebt, den Einsatz dieser Werkstoffe zu optimieren und ihre Vorteile zu kombinieren, um die Haltbarkeit und Effizienz der Infrastrukturen zu maximieren.
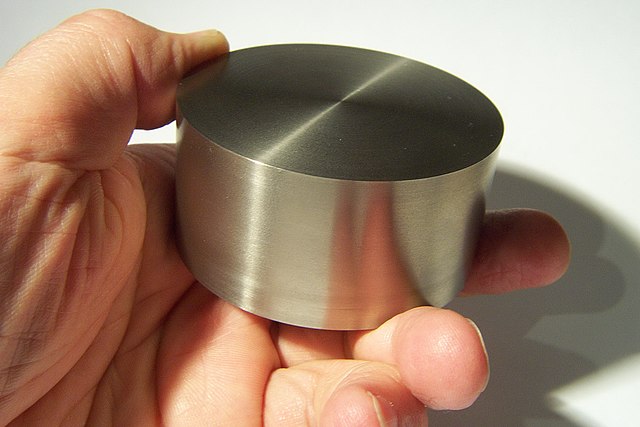
Vergleich von Kohlenstoffstahl und korrosionsbeständigen Legierungen
Die Wahl des richtigen Werkstoffs in der Öl- und Gasindustrie hängt von vielen Faktoren ab, z. B. Korrosionsbeständigkeit, mechanische Festigkeit, Produktions- und Wartungskosten und Betriebsbedingungen. Trotz seiner Beliebtheit ist Kohlenstoffstahl nicht immer die beste Wahl, insbesondere in chemisch aggressiven Umgebungen, in denen zersetzungsbeständigere Werkstoffe erforderlich sind.
Der Hauptunterschied zwischen Kohlenstoffstahl und korrosionsbeständigen Legierungen ist ihre Fähigkeit, rauen Betriebsbedingungen standzuhalten. Kohlenstoffstahl ist zwar billig und weit verbreitet, erfordert aber einen zusätzlichen Schutz, um eine schnelle Zersetzung zu vermeiden. Im Gegensatz dazu bieten korrosionsbeständige Legierungen wie Edelstahl und Nickellegierungen einen natürlichen Schutz gegen korrosive Stoffe, was ihre Lebensdauer erheblich verlängert und den Wartungsaufwand verringert.
Korrosionsbeständigkeit in verschiedenen Umgebungen
Einer der wichtigsten Faktoren bei der Auswahl eines Werkstoffs ist seine Korrosionsbeständigkeit in einer bestimmten Betriebsumgebung. Kohlenstoffstahl zeigt eine hohe Korrosionsanfälligkeit in Gegenwart von Feuchtigkeit, Sauerstoff, Schwefelwasserstoff (H₂S) und Kohlendioxid (CO₂). Besonders bei unterirdischen Rohrleitungen und Offshore-Anlagen, wo der Kontakt mit Meerwasser und Mineralsalzen unvermeidlich ist, sind zusätzliche Schutzmethoden wie Schutzbeschichtungen, Korrosionsinhibitoren oder kathodischer Schutz notwendig.
Nichtrostende Stähle, Nickel- und Titanlegierungen weisen eine wesentlich höhere Korrosionsbeständigkeit auf, weil sie natürliche Schutzschichten bilden, die eine weitere Beschädigung der Metalloberfläche verhindern. Nickellegierungen sind besonders wirksam in sauren Umgebungen, während Titan sich gut in maritimen Anlagen bewährt, in denen intensives Seewasser Kohlenstoffstahl schnell zersetzen kann.
Mechanische Festigkeit und Haltbarkeit unter Betriebsbedingungen
Die in der Erdölindustrie verwendeten Materialien müssen neben der Korrosionsbeständigkeit auch eine ausreichende mechanische Festigkeit aufweisen. Kohlenstoffstahl bietet eine hohe Widerstandsfähigkeit gegenüber statischen und dynamischen Belastungen, deshalb wird er häufig für Pipelines und Stützkonstruktionen verwendet. In extremen Umgebungen wie Tiefseebohrungen oder Anlagen, die hohen Temperaturen und Drücken ausgesetzt sind, kann er jedoch anfällig für Spannungskorrosion und Korrosionsrisse sein, was seine Haltbarkeit einschränkt.
Korrosionsbeständige Legierungen, insbesondere Nickel- und Titanlegierungen, behalten ihre Eigenschaften auch unter extrem rauen Bedingungen bei. Sie sind resistent gegen hohe Temperaturen, Schwefelwasserstoff und aggressive Chemikalien und halten daher viel länger als herkömmlicher Kohlenstoffstahl. Auch ihre mechanische Festigkeit ist höher, so dass dünnere Rohrleitungswände und Strukturkomponenten verwendet werden können, ohne dass die Gefahr einer Schwächung der Struktur besteht.
Produktions- und Wartungskosten
Die Materialkosten spielen bei der Planung von Erdöl-Infrastrukturen eine wichtige Rolle. Kohlenstoffstahl ist relativ billig in der Herstellung, weshalb er häufig für Rohrleitungen und Lagertanks verwendet wird. Seine Korrosionsanfälligkeit erfordert jedoch einen zusätzlichen Schutz, der Kosten für Wartung, Reparatur und Inspektion verursacht.
Obwohl korrosionsbeständige Legierungen in der Herstellung viel teurer sind, bieten sie geringere Betriebskosten, weil sie keine häufigen Inspektionen und kostspieligen Präventivmaßnahmen erfordern. Ihr Einsatz kann langfristig Geld sparen, vor allem in Anlagen, die unter extremen Bedingungen mit hohem Ausfallrisiko und Materialverschleiß arbeiten.
Beispiele für Anwendungen in der Ölindustrie
In der Praxis hängt die Wahl des Werkstoffs von den Besonderheiten der jeweiligen Anwendung ab. CKohlenstoffstahl mit zusätzlichen Schutzmaßnahmen wird am häufigsten in Onshore- und unterirdischen Rohrleitungen verwendet, da unter diesen Bedingungen die Korrosionsgefahr durch Schutzbeschichtungen und kathodischen Schutz wirksam kontrolliert werden kann.
In Offshore-Anlagen, wo die Bedingungen viel aggressiver sind, werden Edelstähle sowie Nickel- und Titanlegierungen häufiger verwendet. Diese Materialien können jahrzehntelang ohne kostspielige Reparaturen eingesetzt werden. Besonders bei Tiefbohrungen und Pipelines, die aggressive Chemikalien transportieren, sind Materialien mit höherer Beständigkeit für die Zuverlässigkeit der Infrastruktur notwendig.
Praktische Anwendung der beiden Werkstoffgruppen
Die Wahl zwischen Kohlenstoffstahl und korrosionsbeständigen Legierungen hängt von den Betriebsbedingungen und den Anforderungen an die Haltbarkeit und Zuverlässigkeit der Infrastruktur ab. Beide Arten von Werkstoffen sind in der Erdölindustrie weit verbreitet, aber ihre Wirksamkeit hängt von der spezifischen Umgebung ab, in der sie eingesetzt werden.
Verwendung von Kohlenstoffstahl in Pipelines und Tanks
Kohlenstoffstahl ist das in der Erdölindustrie am häufigsten verwendete Baumaterial, vor allem wegen seiner mechanischen Festigkeit und seines niedrigen Preises. Er wird vor allem für den Bau von Rohrleitungen zum Transport von Erdöl und Erdgas sowie für Lagertanks und Stützkonstruktionen verwendet.
Kohlenstoffstahl eignet sich gut für Onshore-Rohrleitungen, da seine Korrosionsanfälligkeit mit kathodischem Schutz, Korrosionsschutzbeschichtungen und Korrosionsinhibitoren kontrolliert werden kann. Bei unterirdischen Installationen werden isolierende Polyethylen- oder Epoxidbeschichtungen verwendet, um den Kontakt des Metalls mit Feuchtigkeit und Erde zu verringern.
Kohlenstoffstahl in Tanks für Erdölprodukte wird mit Schutzbeschichtungen geschützt und regelmäßig auf Materialverluste überwacht. In Umgebungen, in denen aggressive Chemikalien vorhanden sind, müssen in kritischen Bereichen der Struktur ein zusätzlicher Schutz oder korrosionsbeständigere Legierungen verwendet werden.
Korrosionsbeständige Legierungen in Offshore-Anlagen und säurehaltigen Umgebungen
In Umgebungen, in denen sich Kohlenstoffstahl schnell zersetzt, werden Edelstähle sowie Nickel- und Titanlegierungen verwendet. Diese Materialien sind hochgradig korrosionsbeständig und widerstehen extremen Temperaturen und Drücken. Beispiele für solche Umgebungen sind Bohrplattformen, Unterwasser-Rohrleitungen und Anlagen, die aggressive Chemikalien transportieren.
Auf Offshore-Plattformen werden nichtrostende Stähle in Rohrleitungssystemen und Stützkonstruktionen verwendet, die Meerwasser und unterschiedlichen Temperaturen ausgesetzt sind. Nichtrostende Stähle, die Molybdän und Nickel enthalten, die das Material vor Lochfraß und Spannungsrisskorrosion schützen, eignen sich besonders gut für diese Bedingungen.
Für Offshore-Pipelines werden häufig Titanlegierungen verwendet, die sich durch ihre Beständigkeit gegen Seewasser und ihr geringes Eigengewicht auszeichnen, wodurch sie leichter zu installieren und zu transportieren sind. Aufgrund ihrer Langlebigkeit können Pipelines aus Titan jahrzehntelang ohne umfangreiche Wartung betrieben werden.
Herkömmlicher Kohlenstoffstahl zersetzt sich in sauren Umgebungen, in denen H₂S und CO₂ vorhanden sind, schnell durch Sulfid- und Dioxidkorrosion. In solchen Fällen werden Nickellegierungen wie Inconel verwendet, um vor aggressiven Chemikalien zu schützen und Spannungsrisskorrosion zu verhindern.
Verwendung von Hybridwerkstoffen
Aufgrund von Unterschieden bei Kosten und Eigenschaften werden in der technischen Praxis häufig Hybridlösungen verwendet. Dabei wird Kohlenstoffstahl mit korrosionsbeständigen Materialien in den Bereichen kombiniert, die am anfälligsten für eine Beschädigung sind.
Bei Ölpipelines gibt es Systeme, bei denen das Innere der Rohre mit einer Schicht aus einer korrosionsbeständigen Legierung beschichtet ist, während die äußere Struktur aus Kohlenstoffstahl besteht. Dieser Ansatz ermöglicht eine Kostensenkung und gewährleistet gleichzeitig eine hohe Haltbarkeit der Komponenten, die aggressiven Substanzen ausgesetzt sind.
In ähnlicher Weise werden bei Lagertanks Beschichtungen aus Nickel und Titan Legierungen an den Stellen verwendet, die mit Chemikalien in Berührung kommen, während andere Bauteile aus Kohlenstoffstahl gefertigt sind. Dies sorgt für eine langlebige und dennoch wirtschaftlich tragfähige Konstruktion.
Korrosionsbeständige Legierungen in der Ölindustrie – Zusammenfassung
Die Wahl der Werkstoffe in der Erdölindustrie wirkt sich auf die Haltbarkeit der Infrastruktur, die Sicherheit und die Betriebskosten aus. Kohlenstoffstahl ist zwar billig und weit verbreitet, erfordert aber einen zusätzlichen Korrosionsschutz. Korrosionsbeständige Legierungen, wie rostfreie Stähle, Nickel und Titan, bieten eine längere Haltbarkeit, sind aber teurer.
Die Ölindustrie entwickelt moderne Beschichtungen, Überwachungssysteme und neue Metalllegierungen, um die Korrosionsbeständigkeit zu verbessern und die Kosten zu optimieren. Zunehmend werden Hybridlösungen eingesetzt, die die wirtschaftlichen Vorteile von Kohlenstoffstahl mit der Langlebigkeit von korrosionsbeständigen Legierungen kombinieren.
Dieser Artikel basiert auf dem Buch „Metallurgy and Corrosion Control in Oil and Gas Production“ von Robert Heidersbach.