Methoden zur Prüfung der Materialstruktur
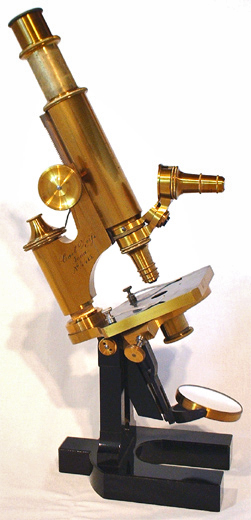
Inhaltsverzeichnis
Metalle und ihre Legierungen bilden die Grundlage der modernen Technologie. Ihre Eigenschaften resultieren jedoch nicht allein aus ihrer chemischen Zusammensetzung. Vielmehr spielen auch die innere Struktur des Materials eine Rolle. Das Verhalten von Metallen während der Bearbeitung, im Betrieb und sogar beim Versagen wird durch die Anordnung der Atome, die Bildung von Kristallkörnern, die Defekte in ihrem Netzwerk und die Organisation der gesamten Materialmasse auf Makroebene bestimmt. Aus diesem Grund ist die Untersuchung der Struktur metallischer Werkstoffe zu einem festen Bestandteil der Arbeit von Ingenieuren, Technologen und Qualitätsspezialisten geworden.
Die Strukturanalyse ermöglicht es uns zu verstehen, warum ein Metall hart und spröde ist, während ein anderes weich und extrem duktil ist. Durch Beobachtung und Messung ist es möglich, den Grad der Materialverfestigung zu beurteilen, die Richtigkeit der Wärmebehandlung zu überprüfen, Unregelmäßigkeiten und innere Fehler zu erkennen und das Verhalten eines Bauteils unter Betriebsbedingungen vorherzusagen. Darüber hinaus ermöglicht eine richtige Interpretation der Struktur die effektive Entwicklung neuer Legierungen, die Optimierung technologischer Prozesse und die Verlängerung der Lebensdauer von Strukturen.
Die Strukturforschung unterscheidet mehrere Beschreibungsebenen: die Kristallstruktur, d. h. die geordnete Anordnung der Atome im Kristallgitter, die Mikrostruktur, die unter dem Mikroskop sichtbare Körner und Phasen umfasst, und die Makrostruktur, die mit bloßem Auge oder unter leichter Vergrößerung sichtbar ist und in der die Ausrichtung der Fasern, die Porosität oder Gussmarken erkennbar sind. Ergänzt werden diese durch moderne zerstörungsfreie Verfahren, mit denen der innere Zustand des Materials ohne Beschädigung beurteilt werden kann, was für die Qualitätskontrolle von Fertigbauteilen von entscheidender Bedeutung ist.
In den nächsten Teilen dieses Textes werden die wichtigsten Methoden vorgestellt, mit denen man die Struktur von Metallen untersuchen kann. So kann man das Material genau untersuchen und besser verstehen, wie es sich verhält.
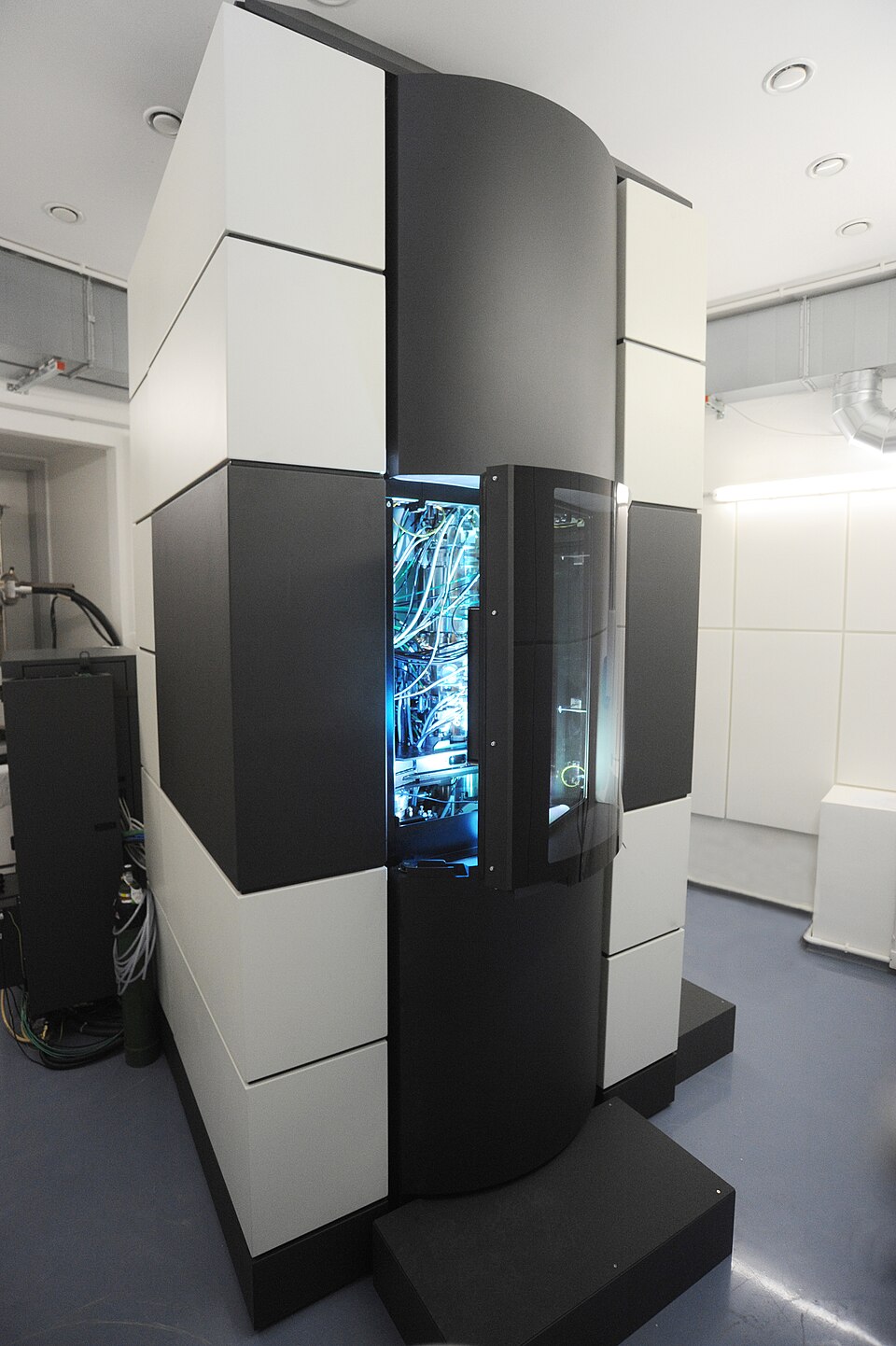
Röntgenstrahlen und Elektronen
Die mechanischen und technologischen Eigenschaften von Metallen beruhen auf ihrer kristallinen Struktur, d. h. der Anordnung der Atome im Raum. Sie ist zwar für das bloße Auge unsichtbar, bestimmt aber grundlegende Eigenschaften wie Dichte, Wärmeleitfähigkeit, Wärmeausdehnung und Verformbarkeit. Um diese atomare Ordnung zu untersuchen, bedienen sich Wissenschaft und Technik einer der präzisesten physikalischen Methoden: der Röntgenbeugung und in geringerem Maße der Elektronenbeugung.
Wenn ein Röntgenstrahl auf eine Metallprobe trifft, werden seine Wellen an regelmäßig angeordneten Atomebenen im Kristall gestreut. Dabei entsteht ein charakteristisches Beugungsmuster – ein Muster aus Linien oder Punkten –, das aufgezeichnet und analysiert werden kann. Dieses Phänomen wird durch die Bragg-Gleichung beschrieben, die den Ablenkungswinkel der Strahlen mit den Abständen zwischen den Ebenen des Kristallgitters in Beziehung setzt. Dies ermöglicht die Bestimmung der Parameter der Elementarzelle, die Identifizierung der im Material vorhandenen Phasen und die Erkennung innerer Spannungen und des Verformungsgrades der Struktur.
Diese als Röntgenbeugungsanalyse (XRD) bezeichnete Technik wird sowohl in der wissenschaftlichen Forschung als auch in der industriellen Kontrolle zur Untersuchung von Produktkorrosion eingesetzt. Sie wird beispielsweise zur Identifizierung von Produkt korrosion, zur Bewertung der Wirksamkeit von Wärmebehandlungen und zur Untersuchung des Verschleißes von Werkzeugoberflächen eingesetzt. Eine vereinfachte, wenn auch weniger genaue Version ist die Beugungsfotografie, die in einer Fotokammer nach der Debye-Scherrer-Methode aufgenommen wird.
Die klassische Beugung wird durch die Elektronenanalyse ergänzt, die in speziellen Transmissionsmikroskopen durchgeführt werden kann. Elektronen ermöglichen dank ihrer viel kürzeren Wellenlänge die Untersuchung viel kleinerer Objekte als Röntgenstrahlen. Mithilfe von Elektronenbeugungsbeobachtungen kann die lokale Kristallorientierung im Maßstab einzelner Körner oder Schichten analysiert werden. Dies ist insbesondere bei dünnen Schichten und nanostrukturierten Materialien von entscheidender Bedeutung.
Sowohl Röntgenstrahlen als auch Elektronen sind daher ein Tor zu einer Welt, die mit bloßem Auge nicht sichtbar ist. Die präzise Wechselwirkung mit Materie ermöglicht die Untersuchung nicht nur der Kristallordnung, sondern auch von Defekten, Gitterversetzungen und Spannungen. Die Beugungstechniken sind die Grundlage für die Materialtechnik auf atomarer Ebene. Dort beginnt die eigentliche Gestaltung der Materialeigenschaften.
Metallographische Mikroskopie
Obwohl die Kristallstruktur die Eigenschaften von Metallen auf atomarer Ebene bestimmt, ist es in der technischen Praxis ebenso wichtig, ihre Mikrostruktur zu analysieren – also die gegenseitige Anordnung von Körnern, Phasen, Grenzen und möglichen Unstetigkeiten im Mikrometerbereich. Dazu wird die metallographische Mikroskopie eingesetzt, die die Beobachtung der Oberfläche entsprechend präparierter Proben im reflektierten Licht ermöglicht.
Grundlage dieser Untersuchung ist die Präparation einer sogenannten metallographischen Probe – einer glatten, polierten Oberfläche der Probe, die einer chemischen Ätzung unterzogen wird. Durch diesen Vorgang werden Korngrenzen und Unterschiede zwischen den Phasen sichtbar. Der Grund dafür ist, dass die Reaktionsgrade mit dem Ätzmittel unterschiedlich sind. Anschließend wird die präparierte Oberfläche unter einem optischen Mikroskop betrachtet, das eine mehrere hundertfache Vergrößerung ermöglicht. Diese reicht aus, um die Korngröße, die Form nichtmetallischer Einschlüsse und die Art der Phasenumwandlungen zu beurteilen.
Einer der Durchbrüche auf diesem Gebiet war die Konstruktion eines metallographischen Mikroskops durch Le Chatelier, das die Beobachtung von reflektiertem Licht auf undurchsichtigen Oberflächen wie Metallen ermöglichte. Bis heute sind diese Mikroskope ein grundlegendes Werkzeug in Qualitätskontrolllabors, Forschungs- und Entwicklungsabteilungen sowie technischen Hochschulen. Sie ermöglichen die Untersuchung, ob ein Werkstoff eine gleichmäßige Struktur aufweist, ob thermische und mechanische Prozesse korrekt durchgeführt wurden und ob gefährliche Fehler vorhanden sind.
Trotz ihrer im Vergleich zur Elektronenmikroskopie begrenzten Auflösung hat die Lichtmikroskopie einen wesentlichen praktischen Vorteil: Sie ist relativ schnell, kostengünstig und ermöglicht die Untersuchung großer Probenflächen. Dies macht sie unverzichtbar für die Analyse großvolumiger Fertigungsprozesse, bei denen die Schnelligkeit der Diagnose und die Wiederholbarkeit der Ergebnisse entscheidend sind.
Mithilfe mikrostruktureller Beobachtungen können Metalle anhand ihrer thermischen und technologischen Vorgeschichte klassifiziert, die Wirksamkeit von Wärmebehandlungen bewertet und der Verformungszustand oder der Grad des Materialzerfalls analysiert werden. Die metallografische Mikroskopie ist somit ein entscheidender Faktor, um das Verhalten von Metallen unter Betriebsbedingungen zu verstehen und ihren Erfolg oder Misserfolg zu beeinflussen.
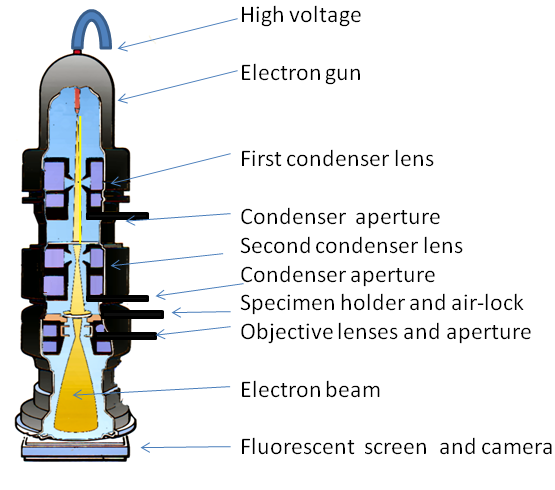
Elektronenmikroskopie
Wenn Details erforderlich sind, die über die Möglichkeiten der Lichtmikroskopie hinausgehen, kommt die Elektronenmikroskopie zum Einsatz – eine Technik, mit der die Struktur eines Materials mit Nanometergenauigkeit oder sogar bis hinunter zu einzelnen Atomen analysiert werden kann. Im Gegensatz zu sichtbarem Licht, dessen Wellenlänge die Auflösung herkömmlicher Mikroskope begrenzt, ermöglicht ein Elektronenstrahl dank seiner viel kürzeren Wellenlänge Einblicke in feinste Details der Metallstruktur, einschließlich Korngrenzen, Phasendispersionen, Netzwerkdefekten und Bruchmustern.
Das Funktionsprinzip eines Elektronenmikroskops basiert auf der Emission und Fokussierung von Elektronen auf die Oberfläche einer Probe unter Hochvakuumbedingungen. Je nach Bauart des Geräts gibt es zwei Haupttypen: das Rasterelektronenmikroskop (REM) und das Transmissionselektronenmikroskop (TEM). Ersteres ermöglicht die Abbildung der Topografie und der chemischen Zusammensetzung von Oberflächen. Letzteres ermöglicht gleichzeitig die Röntgenbildgebung dünner Metallfolien und liefert ein detailliertes Bild der inneren Struktur.
Im SEM bewegt sich der Elektronenstrahl linear über die Probenoberfläche, und Detektoren registrieren die reflektierten oder sekundären Elektronen. Das resultierende Bild zeichnet sich durch eine hohe Tiefenschärfe und Auflösung aus. Dadurch ist die Untersuchung verschiedener Strukturen möglich, wie beispielsweise Bruchmorphologien, Sinterstrukturen, Verschleißflächen und Mikroverzahnungen, die durch die Bearbeitung entstanden sind. Darüber hinaus ermöglichen integrierte Mikroanalysesysteme wie EDS (Energiedispersive Spektroskopie) die Bestimmung der chemischen Zusammensetzung der untersuchten Probenfragmente, was diese Technik äußerst vielseitig macht.
Die TEM bietet wiederum eine noch höhere Auflösung und ermöglicht die Abbildung des Kristallgitters, atomarer Fehlausrichtungen und das Vorhandensein von Punktdefekten. Da die Probe sehr dünn sein muss, ist ihre Vorbereitung komplexer, aber die Ergebnisse sind unvergleichlich präziser. Dies ermöglicht die Untersuchung von Phänomenen, die an Phasengrenzen, in verstärkten Bereichen oder nach Diffusionsprozessen auftreten.
Die Elektronenmikroskopie hat der Materialdiagnostik eine völlig neue Dimension eröffnet. Denn damit lässt sich nicht nur die Qualität von Produkten beurteilen, sondern auch das Verständnis für die Mechanismen ihrer Alterung und ihres Versagens erweitern. Moderne Geräte dieser Klasse sind in der Lage, mikrostrukturelle, spektroskopische und Phasenanalysen gleichzeitig durchzuführen, was sie zu einem wichtigen Werkzeug in der modernen Werkstofftechnik macht, insbesondere in den Bereichen Sonderlegierungen, Nanomaterialien und dünnschichtige Funktionssysteme.
Makroskopie
Obwohl wir dank fortschrittlicher Forschungstechniken das Material mit bemerkenswerter Genauigkeit untersuchen können, ist die Bedeutung der Makroskopie, d. h. der Beobachtung von Metall im für das bloße Auge sichtbaren Maßstab oder bei geringer Vergrößerung, nicht zu unterschätzen. Hier beginnt oft die Materialdiagnose, da viele wichtige Informationen über die Qualität, Herkunft und technologische Geschichte eines Metalls in seiner Makrostruktur enthalten sind.
Die Makroskopie ermöglicht die Beurteilung sichtbarer Merkmale. Dafür ist keine mikroskopische Analyse nötig. Zu den sichtbaren Merkmalen zählen die Porenverteilung, die Faserorientierung in geschmiedeten Werkstoffen, der Verlauf von Gusszonengrenzen, das Vorhandensein von Rissen, Delamination oder sogenannte Primärfehler. Diese entstehen während der Fertigung. Die Probenoberfläche muss vorbereitet werden. Dafür gibt es verschiedene Methoden. Man kann sie schleifen, ätzen oder brechen. So lassen sich große Strukturen sichtbar machen. Dazu zählen Dendriten, Phasenübergangszonen oder Zunderverteilungen.
Besonders wertvolle Informationen liefert die Untersuchung von Bruchstellen – Oberflächen, die durch einen Riss im Element entstanden sind. Je nach Materialart und Beschädigungsmechanismus kann die Bruchstelle unterschiedliche Eigenschaften aufweisen. Die Beschaffenheit des Bruchmaterials kann bei einem spröden Bruch glänzend und körnig sein, während sie bei einem duktilen Bruch matt und faserig ist. Diese Analyse, die häufig im Rahmen von fraktografischen Untersuchungen durchgeführt wird, ermöglicht die Identifizierung der Art der Beschädigung, ihrer Ursache und des möglichen Vorhandenseins von Materialinhomogenitäten, die zum Versagen beigetragen haben könnten.
Die Qualitätskontrolle von Gussteilen, Schmiedeteilen, Blechen und Schweißnähten erfolgt in der industriellen Praxis häufig mithilfe der Makroskopie. Sie ist auch unverzichtbar bei der Analyse von Schäden an Bauteilen, die unter wechselnden Belastungen betrieben werden. In solchen Fällen ist es entscheidend, die Quelle der Rissbildung zu identifizieren. In Verbindung mit einer fotografischen Dokumentation werden makroskopische Beobachtungen nicht nur zu einem Instrument zur Diagnose, sondern auch zu einem Mittel zur Beweisführung bei der Fehlersuche.
Obwohl sie als einfachste Forschungstechnik erscheint, liefert die Makroskopie oft die ersten und direktesten Hinweise, die zu weiteren, detaillierteren mikro- und submikroskopischen Untersuchungen führen. Mit Hilfe der Makroskopie lässt sich schnell feststellen, ob das untersuchte Material einer weiteren Analyse bedarf oder ob seine Struktur zufriedenstellend ist.
Zerstörungsfreie Methoden
In Situationen, in denen die Unversehrtheit des Materials eine absolute Voraussetzung ist und eine Entnahme oder Beschädigung der Probe nicht akzeptabel ist, kommen zerstörungsfreie Methoden, auch bekannt als ZfP (zerstörungsfreie Prüfung), zum Einsatz. Diese Techniken ermöglichen die Beurteilung der Materialqualität, die Erkennung von inneren und äußeren Fehlern sowie die Überprüfung der Übereinstimmung der Struktur mit den Konstruktionsanforderungen, ohne das geprüfte Element zu beschädigen.
Eine der am häufigsten verwendeten zerstörungsfreien Methoden ist die Röntgenprüfung, bei der Röntgen- oder Gammastrahlen zum Einsatz kommen. Diese Strahlen durchdringen das Material und werden je nachdem, wie dicht und dick die inneren Strukturen sind, schwächer. Die dabei entstehenden Unterschiede werden auf speziellen Einsätzen oder digitalen Sensoren aufgezeichnet, wodurch ein Bild des Materialquerschnitts erstellt werden kann. Mithilfe dieses Verfahrens lassen sich Luftblasen, Schrumpfhohlräume, Unregelmäßigkeiten und nichtmetallische Einschlüsse erkennen, die die strukturelle Festigkeit des Bauteils beeinträchtigen könnten.
Eine weitere häufig verwendete Technik ist die Ultraschallprüfung, bei der hochfrequente Schallwellen durch das Material geleitet werden. Unregelmäßigkeiten wie Risse, Delaminationen oder Hohlräume bewirken eine Reflexion oder Brechung der Wellen, die auf dem Bildschirm des Messgeräts leicht erfasst werden können. Die Ultraschallprüfung ist äußerst genau, schnell und sicher und eignet sich daher für die Prüfung dicker und komplexer Bauteile.
Die Magnetpulverprüfung ist eine nützliche Methode zur Prüfung ferromagnetischer Werkstoffe. Dabei wird ein Magnetfeld im zu prüfenden Element erzeugt und feine Teilchen, die sich von Magneten angezogen lassen, auf dessen Oberfläche aufgebracht. Sind Fehler wie Kratzer oder Oberflächenrisse vorhanden, werden die Magnetfeldlinien unterbrochen. Dadurch sammeln sich die Partikel lokal an und der Fehler kann leicht visuell erkannt werden.
All diese Methoden haben einen gemeinsamen Vorteil: Sie ermöglichen eine vollständige Diagnose eines Materials oder Produkts, ohne es zu zerstören, was nicht nur in der Qualitätskontrolle, sondern auch bei regelmäßigen Wartungsinspektionen von entscheidender Bedeutung ist. Ihre Einsatzgebiete sind die Luft- und Raumfahrt, die Energie-, Petrochemie- und Automobilindustrie sowie alle Branchen, in denen strukturelle und betriebliche Sicherheit an erster Stelle stehen.
Zerstörungsfreie Methoden sind heute ein unverzichtbarer Bestandteil von Qualitätsmanagementsystemen, da sie es ermöglichen, potenzielle Gefahren rechtzeitig zu erkennen, bevor kostspielige Ausfälle auftreten. Sie sind ein Beweis für den technologischen Fortschritt, der eine Beurteilung des Inneren eines Materials so effektiv wie bei Transparenz ermöglicht, ohne in dessen Struktur eingreifen zu müssen.
Methoden zur Prüfung der Materialstruktur – Zusammenfassung
Das Verständnis und die Kontrolle der inneren Struktur von Metallen ist eines der wichtigsten Werkzeuge, über die Materialingenieure heute verfügen. Erst durch kristallographische, mikrostrukturelle, makroskopische und zerstörungsfreie Analysen können wir vollständig verstehen, wie sich ein Werkstoff unter realen Bedingungen verhält, wobei wir dabei von der Belastung über den Kontakt mit chemischen Stoffen, die starke Reibung bis hin zu unterschiedlichen Temperaturen alles berücksichtigen.
Dieses Wissen ist nicht nur für die Entwicklung neuer Werkstoffe von entscheidender Bedeutung, sondern auch für deren Überprüfung, die Bewertung des Herstellungsprozesses und sogar für die Untersuchung von Schadensursachen. Durch den Einsatz unterschiedlicher Testmethoden – von Röntgenstrahlung über Elektronenmikroskope bis hin zu Ultraschall – ist es möglich, ein vollständiges Bild des Materials zu erhalten, das von der atomaren Ebene bis zu makroskopischen Charakteristika reicht, die mit dem bloßen Auge erkennbar sind.
Jede der vorgestellten Techniken spielt eine spezifische Rolle, und ihre Komplementarität ermöglicht es nicht nur, Defekte zu lokalisieren, sondern auch ihre Auswirkungen vorherzusagen und in Zukunft zu vermeiden. Die moderne Materialforschung bildet somit die Grundlage für ein verantwortungsbewusstes Ingenieurwesen, das nicht mehr allein auf Intuition oder Erfahrung, sondern auf überprüfbare Daten und präzise Diagnosen setzt.
In einer Welt, in der die Sicherheit, Langlebigkeit und Qualität von Bauwerken direkten Einfluss auf das Leben der Menschen und die Umwelt haben, ist das Verständnis des Inneren von Metallen kein Luxus, sondern eine Notwendigkeit.