Korrosionsbeständiga legeringar i oljeindustrin
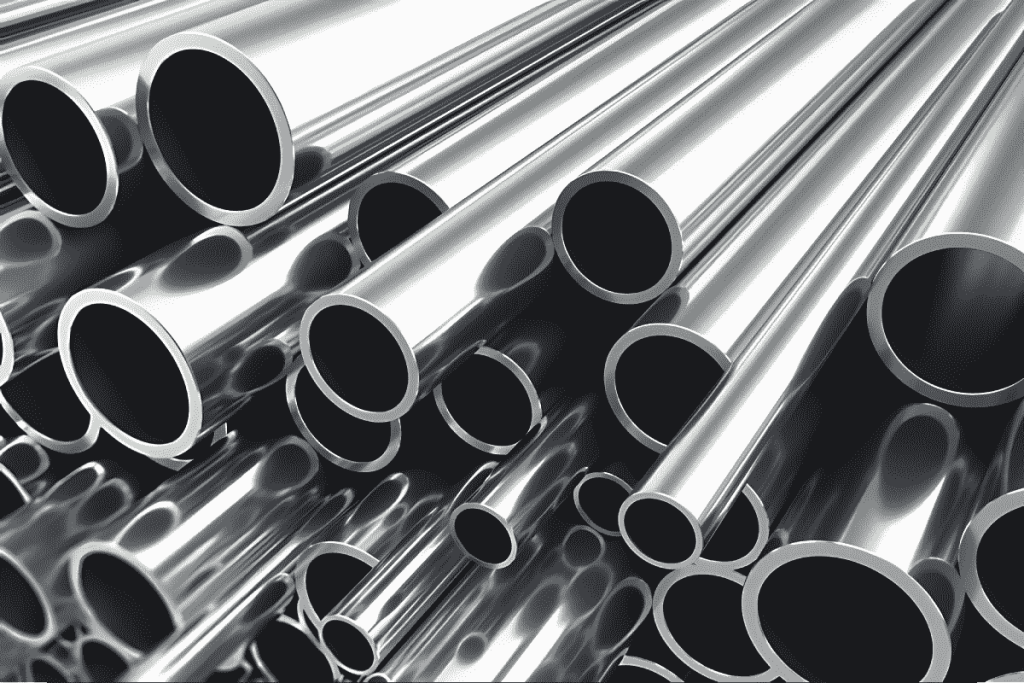
Innehållsförteckning
Olje- och gasindustrin kräver material som tål extrema driftsförhållanden som höga tryck, aggressiva kemiska miljöer och varierande temperaturer. Att välja rätt material för rörledningar, tankar eller offshore-installationer är avgörande för infrastrukturens säkerhet, hållbarhet och driftskostnader.
Kolstål och korrosionsbeständiga legeringar är bland de mest använda materialen inom denna sektor. Kolstål, på grund av dess höga mekaniska styrka och förhållandevis låga kostnad, används ofta vid konstruktion av rörledningar och stödstrukturer. Dess känslighet för korrosion i aggressiva miljöer gör det dock nödvändigt att använda korrosionsbeständiga legeringar som rostfritt stål, nickel eller titan i många applikationer.
I den här artikeln diskuteras egenskaperna hos kolstål och korrosionsbeständiga legeringar, deras fördelar och begränsningar samt deras viktigaste skillnader. Denna analys kommer att ge en bättre förståelse för de förhållanden under vilka ett visst material är mest effektivt och trenderna i utvecklingen av ny materialteknik.
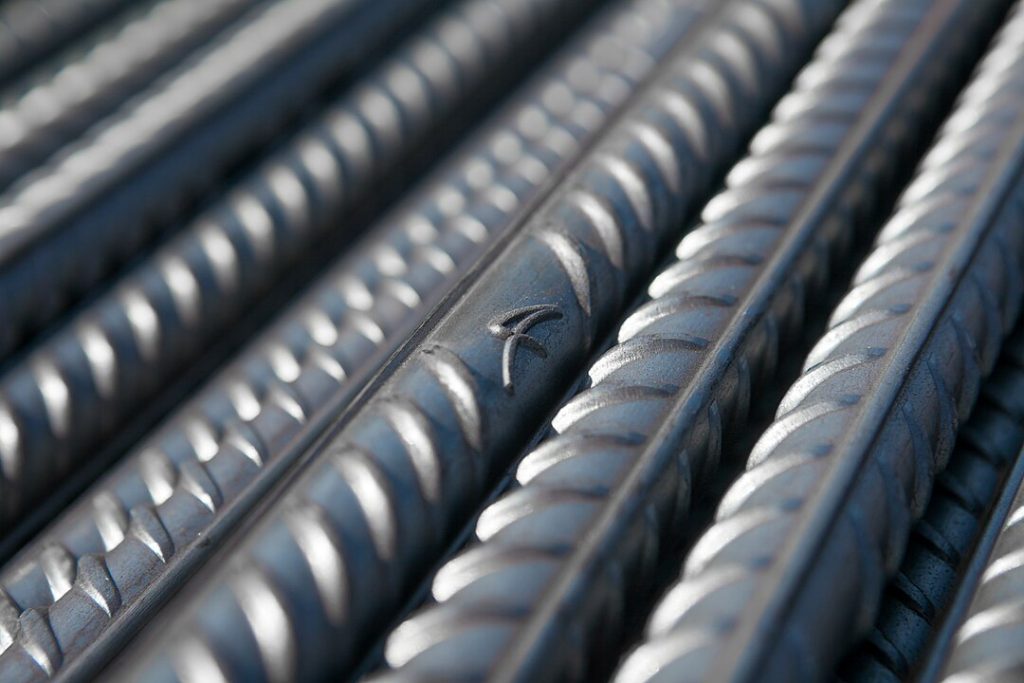
Kolstål – egenskaper och användningsområden
Kolstål är en legering av järn och kol, med en kolhalt på vanligtvis upp till 2 %. Beroende på mängden kol finns det stål med låg kolhalt, medelhög kolhalt och hög kolhalt. Oljeindustrin använder huvudsakligen stål med låg kolhalt, som har god svetsbarhet och duktilitet men är mer känsliga för korrosion än legeringar med ett högre innehåll av skyddande legeringstillsatser.
Kolstål används i stor utsträckning inom oljeindustrin främst på grund av dess förhållande mellan pris och hållfasthet. Dess viktigaste fördelar är: lågt pris – kolstål är mycket billigare att producera än specialiserade korrosionsbeständiga legeringar; god mekanisk hållfasthet – vilket gör att det kan användas i strukturer som utsätts för tunga belastningar samt lätt tillgänglighet och bearbetning – möjligheten till massproduktion och enkel svetsning och formning gör att det används i stor utsträckning vid konstruktion av rörledningar och lagringstankar.
Trots dessa fördelar har kolstål begränsat korrosionsmotstånd, särskilt när det utsätts för havsvatten, syror och frätande gaser. I vätesulfidrika miljöer kan allvarliga skador uppstå på grund av sulfidkorrosion, vilket leder till väteförsprödning och sprickbildning i materialet. Detta problem tvingar fram användning av ytterligare skyddsmetoder, till exempel korrosionsskyddande beläggningar, korrosionsinhibitorer och katodiskt skydd, vilket i sin tur ökar driftskostnaderna.
Korrosionsbeständiga legeringar – typer och egenskaper
Rostfria stål
Rostfria stål är legeringar av järn, krom och ofta nickel och molybden, som uppvisar hög korrosionsbeständighet på grund av bildandet av ett skyddande skikt av kromoxider på metallytan. Detta skikt förhindrar ytterligare nedbrytning av materialet, vilket gör rostfria stål lämpliga för användning i aggressiva kemiska miljöer, höga temperaturer och förhållanden som utsätts för havsvatten. Rostfritt stål används inom:
- Transmissionssystem i marina miljöer där vattnet innehåller klorider som påskyndar korrosion.
- Industriella högtemperatursystem där traditionellt kolstål kan brytas ned.
- Raffinaderitankar och -system som utsätts för aggressiva kemikalier.
Den breda användningen av rostfritt stål inom petroleumindustrin beror främst på deras mångsidighet och gynnsamma mekaniska egenskaper. De används i transmissionsrörledningar, lagringstankar och apparater som används i raffinaderiprocesser där kontakt med frätande ämnen är oundviklig.
I marin miljö är rostfritt stål ofta det konstruktionsmaterial som väljs eftersom de motstår klorider, som påskyndar gropfrätning. I högtemperatursystem som värmeväxlare och raffinaderiugnar bibehåller rostfria stål stabilitet och styrka, vilket gör att de kan användas under långa tidsperioder utan risk för att metallstrukturen försvagas.
Trots sina många fördelar kan rostfria stål vara mottagliga för spänningskorrosionssprickor och gropfrätning, särskilt i närvaro av aggressiva kloridjoner. Under extrema industriella förhållanden används därför ofta ytterligare skydd, såsom korrosionsinhibitorer eller skyddsbeläggningar, för att förlänga materialets livslängd ytterligare.
Nickel- och titanlegeringar
Nickel- och titanlegeringar är bland de mest avancerade korrosionsbeständiga materialen för användning i de mest krävande driftsförhållanden. Deras unika kemiska och mekaniska egenskaper gör att de används i installationer som arbetar i extrema temperaturer, sura miljöer och högtrycksförhållanden.
Nickellegeringar, såsom Inconel, uppvisar exceptionell resistens mot vätesulfid (H₂S), syror och höga temperaturer, vilket innebär att de är utmärkta för applikationer i djupa brunnar och raffinaderisystem. Tack vare sin metallurgiska struktur motstår de också stresskorrosion, vilket förhindrar sprickor och fel i djupvattensystem.
Samtidigt kännetecknas titan och dess legeringar av sin extrema motståndskraft mot korrosion i havsvatten, vilket gör dem lämpliga för användning i offshore-strukturer, oljeriggar och undervattensrörledningar. Deras låga densitet jämfört med andra metaller gör det möjligt att bygga lätta men ändå starka strukturer som kan fungera under extrema förhållanden i många år utan underhåll.
En av de största begränsningarna med att använda nickel- och titanlegeringar är deras höga kostnad, vilket ofta begränsar deras användbarhet till endast de mest krävande applikationerna. Därför används ofta hybridlösningar, där komponenter av korrosionsbeständiga legeringar kombineras med billigare material, till exempel kolstål, som dessutom är skyddade mot nedbrytning.
Trots det höga priset på nickel- och titanlegeringar gör deras tillförlitlighet och minimala underhållsbehov dem ersättliga i områden där haverier kan leda till katastrofala miljömässiga och ekonomiska konsekvenser.
Valet mellan rostfritt stål och nickel- och titanlegeringar beror främst på miljöförhållandena och applikationens specifika egenskaper. Rostfria stål erbjuder en gynnsam balans mellan pris och korrosionsbeständighet, medan nickel- och titanlegeringar ger maximalt skydd även i de mest extrema miljöerna, men till en mycket högre driftskostnad. Oljeindustrin strävar efter att optimera användningen av dessa material och kombinera deras fördelar för att maximera infrastrukturens hållbarhet och effektivitet.
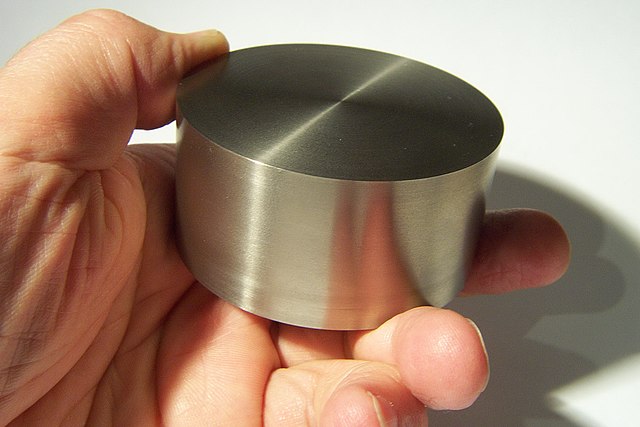
Jämförelse mellan kolstål och korrosionsbeständiga legeringar
Att välja rätt material inom olje- och gasindustrin påverkas av många faktorer, till exempel korrosionsbeständighet, mekanisk styrka, produktions- och underhållskostnader samt driftsförhållanden. Trots sin popularitet är kolstål inte alltid det bästa alternativet, särskilt inte i kemiskt aggressiva miljöer där det krävs mer nedbrytningsbeständiga material.
Den största skillnaden mellan kolstål och korrosionsbeständiga legeringar är deras förmåga att motstå tuffa driftsförhållanden. Kolstål, som är billigt och allmänt tillgängligt, kräver ytterligare skydd för att undvika snabb nedbrytning. Korrosionsbeständiga legeringar, som rostfritt stål och nickellegeringar, har däremot ett naturligt skydd mot korrosiva ämnen, vilket avsevärt förlänger deras livslängd och minskar underhållet.
Motståndskraft mot korrosion i olika miljöer
En av de viktigaste faktorerna vid val av material är dess motståndskraft mot korrosion i en viss driftsmiljö. Kolstål uppvisar hög känslighet för korrosion i närvaro av fukt, syre, vätesulfid (H₂S) och koldioxid (CO₂). Särskilt i underjordiska rörledningar och offshoreinstallationer, där kontakt med havsvatten och mineralsalter är oundviklig, är ytterligare skyddsmetoder som skyddsbeläggningar, korrosionsinhibitorer eller katodiskt skydd nödvändiga.
Rostfria stål, nickel- och titanlegeringar uppvisar mycket högre korrosionsbeständighet eftersom de bildar naturliga skyddsskikt som förhindrar ytterligare skador på metallytan. Nickellegeringar är särskilt effektiva i sura miljöer, medan titan fungerar bra i marina installationer där intensiv exponering för havsvatten snabbt kan bryta ned kolstål.
Mekanisk hållfasthet och hållbarhet under driftförhållanden
Material som används inom oljeindustrin måste ha tillräcklig mekanisk hållfasthet utöver korrosionsbeständighet. Kolstål erbjuder högt motstånd mot statiska och dynamiska belastningar, vilket gör att det ofta används i transmissionsrörledningar och stödstrukturer. I extrema miljöer, till exempel djupvattenbrunnar eller installationer som utsätts för höga temperaturer och tryck, kan det dock vara mottagligt för spänningskorrosion och korrosionssprickor, vilket begränsar dess hållbarhet.
Korrosionsbeständiga legeringar, särskilt nickel- och titanlegeringar, behåller sina egenskaper även under extremt tuffa förhållanden. De är resistenta mot höga temperaturer, vätesulfid och aggressiva kemikalier, vilket gör att de håller mycket längre än traditionellt kolstål. Den mekaniska hållfastheten är också högre, vilket gör det möjligt att använda tunnare rörledningsväggar och strukturella komponenter utan att riskera att försvaga strukturen.
Produktions- och underhållskostnader
Materialkostnaden spelar en viktig roll i beslut om teknik för oljeinfrastruktur. Kolstål är relativt billigt att producera, vilket gör att det används i stor utsträckning i rörledningar och lagringstankar. Dess korrosionsbenägenhet kräver dock ytterligare skydd, vilket genererar kostnader för underhåll, reparation och inspektion.
Även om korrosionsbeständiga legeringar är mycket dyrare att producera, medför de lägre driftskostnader eftersom de inte kräver frekventa inspektioner och kostsamma förebyggande åtgärder. Användningen av dem kan spara pengar på lång sikt, särskilt i installationer som är i drift under extrema förhållanden med hög risk för haverier och materialnedbrytning.
Exempel på tillämpningar inom oljeindustrin
I praktiken beror valet av material på de specifika egenskaperna hos tillämpningen. Kolstål med extra skydd används oftast i rörledningar på land och under jord eftersom korrosionsrisken under dessa förhållanden kan kontrolleras effektivt med skyddsbeläggningar och katodiskt skydd.
I offshoreinstallationer, där förhållandena är mycket mer aggressiva, är rostfria stål och nickel- och titanlegeringar vanligare. Dessa material kan användas i årtionden utan kostsamma reparationer. Särskilt i djupa brunnar och rörledningar som transporterar aggressiva kemikalier är material med högre motståndskraft nödvändiga för infrastrukturens tillförlitlighet.
Praktisk tillämpning av båda materialgrupperna
Valet mellan kolstål och korrosionsbeständiga legeringar beror på driftsförhållanden och infrastrukturens krav på hållbarhet och tillförlitlighet. Båda typerna av material används i stor utsträckning inom oljeindustrin, men deras effektivitet beror på den specifika miljö där de används.
Användning av kolstål i pipelines och tankar
Kolstål är oljeindustrins mest använda konstruktionsmaterial, främst på grund av dess mekaniska styrka och låga pris. Det används främst i konstruktionen av rörledningar som transporterar råolja och naturgas, samt i lagringstankar och stödstrukturer.
Kolstål fungerar bra i rörledningar på land eftersom dess känslighet för korrosion kan kontrolleras med katodiskt skydd, korrosionsskyddande beläggningar och korrosionsinhibitorer. Vid underjordiska installationer används isolerande polyeten- eller epoxibeläggningar för att minska metallens kontakt med fukt och jord.
Kolstål i tankar för petroleumprodukter skyddas med skyddsbeläggningar och övervakas regelbundet med avseende på materialförlust. I miljöer där aggressiva kemikalier förekommer måste ytterligare skydd eller mer korrosionsbeständiga legeringar användas i kritiska delar av konstruktionen.
Korrosionsbeständiga legeringar i offshore-installationer och sura miljöer
I miljöer där kolstål bryts ned snabbt används rostfria stål samt nickel- och titanlegeringar. Dessa material är mycket motståndskraftiga mot korrosion och extrema temperaturer och tryck. Exempel på sådana miljöer är borrplattformar, undervattensrörledningar och installationer som transporterar aggressiva kemikalier.
På offshoreplattformar används rostfria stål i rörsystem och stödstrukturer som utsätts för havsvatten och varierande temperaturer. Rostfria stål som innehåller molybden och nickel, som skyddar materialet mot gropfrätning och spänningskorrosion, fungerar särskilt bra under dessa förhållanden.
Offshore-rörledningar använder ofta titanlegeringar, som kännetecknas av motståndskraft mot havsvatten och låg dödvikt, vilket gör dem enklare att installera och transportera. Tack vare sin hållbarhet kan rörledningar tillverkade av titan användas i årtionden utan omfattande underhåll.
Traditionellt kolstål bryts snabbt ned genom sulfid- och dioxidkorrosion i sura miljöer, där H₂S och CO₂ förekommer. I sådana fall används nickellegeringar som Inconel för att skydda mot aggressiva kemikalier och motstå spänningskorrosionssprickor.
Användning av hybridmaterial
På grund av skillnader i kostnad och egenskaper används ofta hybridlösningar i ingenjörspraxis. Dessa innebär att man kombinerar kolstål med korrosionsbeständiga material i de områden som är mest utsatta för nedbrytning.
I oljeledningar kan man stöta på system där rörens insida är belagd med ett lager av korrosionsbeständig legering, medan den yttre strukturen förblir tillverkad av kolstål. Detta tillvägagångssätt möjliggör kostnadsreduktion samtidigt som det säkerställer hög hållbarhet hos komponenter som utsätts för aggressiva ämnen.
På samma sätt använder lagringstankar beläggningar av nickel- och titanlegeringar vid kontaktpunkterna med kemikalier, medan andra strukturella komponenter är tillverkade av kolstål. Detta ger en hållbar men ändå ekonomiskt genomförbar design.
Korrosionsbeständiga legeringar i oljeindustrin – sammanfattning
Valet av material inom oljeindustrin påverkar infrastrukturens hållbarhet, säkerhet och driftskostnader. Kolstål, som är billigt och används i stor utsträckning, kräver ytterligare korrosionsskydd. Korrosionsbeständiga legeringar, som rostfritt stål, nickelstål och titanstål, ger större hållbarhet, men har en högre kostnad.
Oljeindustrin utvecklar moderna ytbeläggningar, övervakningssystem och nya metallegeringar för att förbättra korrosionsbeständigheten och optimera kostnaderna. I allt större utsträckning används hybridlösningar som kombinerar de ekonomiska fördelarna med kolstål med hållbarheten hos korrosionsbeständiga legeringar.
Denna artikel är baserad på boken ”Metallurgy and Corrosion Control in Oil and Gas Production” av Robert Heidersbach.