Obróbka cieplna metali
Spis treści
Kontrolowana transformacja materiału
W świecie inżynierii materiałowej kluczowe znaczenie ma nie tylko to, z jakiego metalu wykonany jest dany element, ale również to, w jaki sposób został on przekształcony na poziomie wewnętrznej struktury. Jednym z najważniejszych narzędzi tej transformacji jest obróbka cieplna, czyli zespół procesów technologicznych polegających na kontrolowanym nagrzewaniu i chłodzeniu metali lub ich stopów w celu zmiany ich właściwości użytkowych – mechanicznych, fizycznych, a niekiedy także chemicznych.
To, co czyni obróbkę cieplną tak wyjątkową, to fakt, że nie zmienia ona ani kształtu, ani składu chemicznego metalu. Zamiast tego wpływa bezpośrednio na strukturę wewnętrzną materiału – sposób rozmieszczenia atomów, obecność i charakter faz oraz defektów krystalicznych. W praktyce oznacza to możliwość zwiększenia twardości, odporności na zużycie, poprawy udarności, a także nadania materiałowi cech nieosiągalnych przy obróbce mechanicznej czy chemicznej.
Procesy cieplne nie są jednak działaniem przypadkowym. Ich skuteczność zależy od precyzyjnej kontroli temperatury, czasu utrzymywania w danym przedziale cieplnym oraz szybkości chłodzenia. Zmiany zachodzące w materiale podczas tych etapów są ściśle powiązane z przemianami fazowymi i rekrystalizacją, które warunkują nową, pożądaną strukturę. Co więcej, obróbka cieplna często stanowi przygotowanie materiału do dalszych procesów – takich jak hartowanie, nawęglanie, spiekanie czy spawanie – i ma kluczowe znaczenie dla trwałości i niezawodności gotowego wyrobu.
Zrozumienie zasad, jakimi rządzi się obróbka cieplna, pozwala projektować materiały nie tylko pod względem składu, ale także ich wewnętrznej architektury. To dzięki niej stal może być zarówno elastyczna, jak i twarda, odporna na ścieranie lub zdolna do amortyzowania uderzeń – w zależności od tego, jak została potraktowana ogniem i czasem.
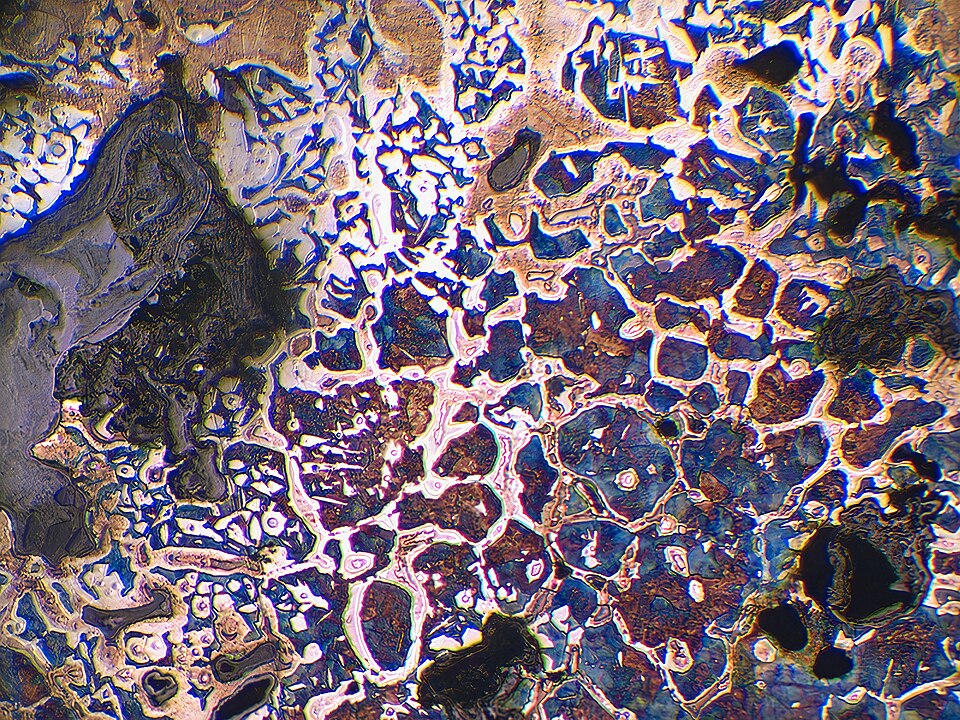
Etapy procesu obróbki cieplnej
Obróbka cieplna to proces, który – choć może wydawać się prosty w swojej istocie – w rzeczywistości opiera się na precyzyjnie zaplanowanej sekwencji etapów, z których każdy wpływa na ostateczny efekt strukturalny i użytkowy obrabianego materiału. Aby osiągnąć zamierzony cel technologiczny, konieczne jest zrozumienie, jak i dlaczego każdy z tych kroków prowadzi do przemiany właściwości metalu.
Pierwszym i nieodzownym etapem jest nagrzewanie materiału do ściśle określonej temperatury. Nie chodzi tu wyłącznie o dostarczenie energii cieplnej – to właśnie temperatura determinuje, czy i jakie przemiany fazowe zajdą w strukturze krystalicznej. W przypadku stali może to oznaczać przejście z ferrytu w austenit, rozpoczęcie procesu rozpuszczania węglików czy aktywację dyfuzji. Kluczowe jest nie tylko osiągnięcie żądanej temperatury, ale także sposób, w jaki do niej dochodzimy – zbyt szybkie nagrzewanie może prowadzić do naprężeń cieplnych, pęknięć lub niejednorodności strukturalnych.
Po osiągnięciu właściwej temperatury następuje wygrzewanie, czyli utrzymanie materiału w ustalonym przedziale cieplnym przez określony czas. Ten etap pozwala na osiągnięcie stanu równowagi fazowej oraz na pełne zakończenie przemian wewnętrznych. Czas wygrzewania musi być dostosowany do rodzaju materiału, grubości elementu oraz celu obróbki – zbyt krótki może skutkować niepełnymi przemianami, zbyt długi zaś może prowadzić do niepożądanego wzrostu ziarna czy degradacji struktury.
Ostatnim, a zarazem jednym z najbardziej decydujących momentów w całym procesie jest chłodzenie. Od jego szybkości i przebiegu zależy, jaka struktura ustali się w materiale po opuszczeniu obszaru wysokich temperatur. Powolne chłodzenie może prowadzić do powstania perlitu lub ferrytu, natomiast gwałtowne – do zahartowania metalu i uzyskania struktury martenzytycznej. W tym sensie chłodzenie nie jest jedynie końcem procesu, lecz jego kulminacyjnym punktem, który przesądza o właściwościach końcowych stopu.
Wszystkie te etapy – nagrzewanie, wygrzewanie i chłodzenie – muszą być traktowane jako całość, precyzyjnie dostosowana do wymagań materiałowych i funkcjonalnych danego wyrobu. Ich wzajemne relacje tworzą z obróbki cieplnej nie tylko sztukę, ale przede wszystkim naukę o kontrolowanej przemianie wewnętrznej metalu.
Znaczenie nagrzewania i jego parametrów
Choć proces obróbki cieplnej wydaje się zaczynać od momentu podniesienia temperatury materiału, to samo nagrzewanie ma znacznie większe znaczenie, niż tylko osiągnięcie wymaganej wartości cieplnej. Jest to etap, w którym rozpoczynają się fundamentalne zmiany wewnętrzne, mające wpływ na dalszy przebieg przemian strukturalnych. Od sposobu nagrzewania zależy nie tylko skuteczność całego procesu, ale także jakość, jednorodność i bezpieczeństwo obrabianego detalu.
Najważniejszym parametrem jest oczywiście temperatura – to ona warunkuje, czy materiał wejdzie w zakres przemian fazowych, i jak głęboko się one rozwiną. W przypadku stali różne przedziały temperatury decydują o tym, czy mamy do czynienia z przemianą ferrytu w austenit, rozpoczęciem rozpuszczania cementytu czy aktywacją procesów rekrystalizacji. Każdy typ stali ma inne zakresy temperatury krytycznej, a ich przekroczenie – zarówno w dół, jak i w górę – może skutkować poważnymi zmianami właściwości mechanicznych.
Równie istotne, co sama wartość temperatury, jest tempo jej osiągania. Zbyt szybkie nagrzewanie może prowadzić do wystąpienia dużych gradientów cieplnych pomiędzy powierzchnią a rdzeniem elementu, co sprzyja tworzeniu się naprężeń wewnętrznych, mikropęknięć, a w skrajnych przypadkach nawet deformacji. Z drugiej strony, zbyt wolne podnoszenie temperatury bywa nieekonomiczne i niepotrzebnie wydłuża proces produkcyjny. Dlatego inżynierowie często wybierają kompromisowe rozwiązania – korzystając z kontrolowanego nagrzewania strefowego, etapowego lub z wykorzystaniem atmosfer ochronnych.
Nie bez znaczenia jest również równomierność temperatury w całym elemencie. W przypadku dużych odkuwek, długich wałów czy cienkościennych profili, różnice temperatury w różnych partiach materiału mogą prowadzić do niejednorodnych przemian fazowych, a w efekcie – do pogorszenia właściwości mechanicznych lub lokalnych koncentracji naprężeń. Dlatego też piece stosowane do obróbki cieplnej są wyposażone w precyzyjne systemy pomiarowe i sterujące, pozwalające utrzymać stabilny rozkład cieplny wewnątrz komory grzewczej.
Nagrzewanie to zatem nie tylko pierwszy krok procesu – to moment, w którym rozpoczyna się świadoma ingerencja w strukturę materiału. Jego właściwe przeprowadzenie wymaga nie tylko znajomości parametrów technologicznych, ale także zrozumienia fizyki zachodzących zjawisk – od dyfuzji atomów po inicjację przemian krystalicznych.
Rola wygrzewania
Jeśli temperatura nagrzewania wyznacza warunki, w jakich mogą zachodzić przemiany strukturalne, to czas wygrzewania decyduje o tym, czy te przemiany dojdą do pełni swojego rozwoju. Etap wygrzewania, choć często niedoceniany, jest jednym z najistotniejszych momentów obróbki cieplnej – to właśnie on pozwala strukturze materiału ustabilizować się w nowym stanie i osiągnąć pożądane właściwości użytkowe.
Wygrzewanie polega na utrzymaniu metalu przez określony czas w stałej temperaturze – najczęściej tej, w której rozpoczynają się istotne przemiany fazowe. W tym okresie dochodzi do intensyfikacji zjawisk dyfuzyjnych: atomy różnych pierwiastków przemieszczają się w sieci krystalicznej, wyrównując rozkład składników chemicznych, rozpuszczając wcześniejsze wydzielenia, bądź tworząc nowe fazy wtórne. W przypadku stali może to być rozpuszczanie węglików w austenicie, homogenizacja chemiczna lub stabilizacja nowo powstałych struktur.
Długość wygrzewania musi być dobrana indywidualnie do rodzaju materiału i celu obróbki. Dla niektórych procesów wystarczy kilka minut, w innych – szczególnie przy dużych przekrojach elementów – czas ten sięga nawet kilku godzin. Zbyt krótki czas może sprawić, że przemiany nie zajdą w całej objętości materiału lub będą niepełne, co skutkuje nierównomierną mikrostrukturą i niejednorodnością właściwości. Z kolei zbyt długie wygrzewanie może prowadzić do niepożądanego wzrostu ziarna, obniżenia wytrzymałości oraz zmniejszenia odporności na pękanie zmęczeniowe.
Wygrzewanie to również moment, w którym struktura wewnętrzna „dojrzewa” – dochodzi do rekonstrukcji sieci krystalicznej, redukcji naprężeń wewnętrznych, stabilizacji nowych faz i rozproszenia defektów sieciowych. Jest to proces, który – choć niewidoczny gołym okiem – decyduje o tym, czy hartowanie, wyżarzanie czy przesycanie przyniesie oczekiwany efekt, czy też zakończy się niepowodzeniem.
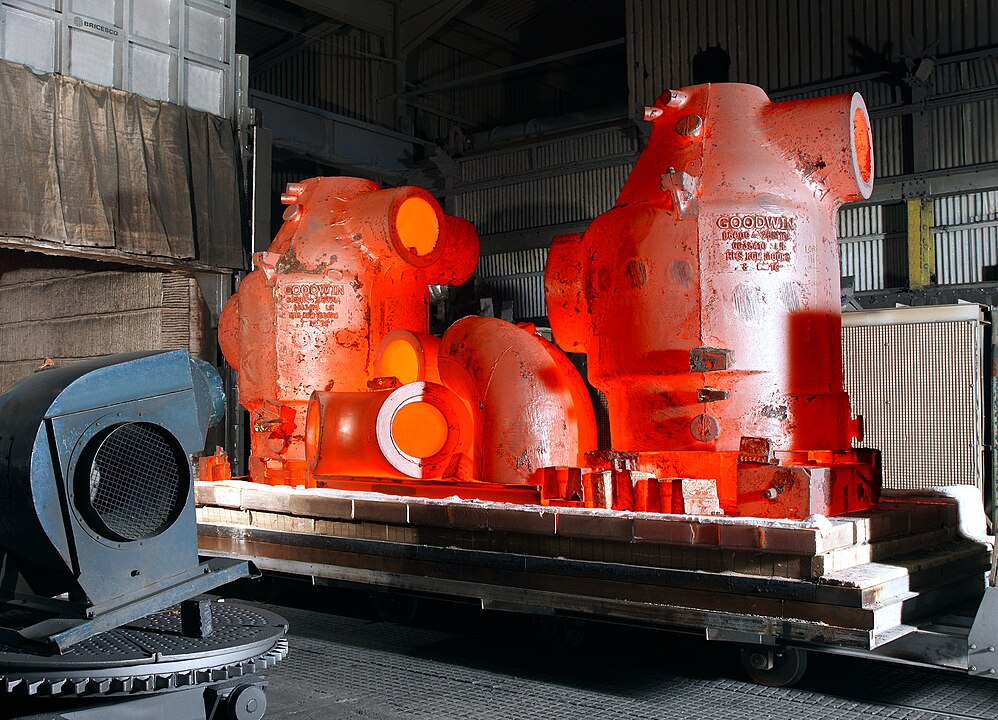
Chłodzenie
Choć etap chłodzenia następuje na końcu procesu obróbki cieplnej, jego znaczenia nie można traktować marginalnie. To właśnie podczas chłodzenia następuje ostateczne ustalenie mikrostruktury materiału, która przesądza o jego końcowych właściwościach mechanicznych. Można powiedzieć, że wszystkie wcześniejsze działania – nagrzewanie i wygrzewanie – przygotowują grunt pod to, co rozstrzyga się w tej jednej, krytycznej fazie: jak szybko i w jaki sposób materiał oddaje ciepło.
Szybkość chłodzenia decyduje o tym, które fazy będą miały szansę się ukształtować, a które zostaną „zamrożone” w stanie przejściowym. Gwałtowne chłodzenie, typowe dla procesu hartowania, powoduje zatrzymanie przemian dyfuzyjnych i prowadzi do powstania struktur metastabilnych, takich jak martenzyt – wyjątkowo twardy, ale i kruchy układ atomowy. Takie podejście pozwala znacząco podnieść twardość materiału, ale wymaga późniejszego odpuszczania, by przywrócić mu minimalną plastyczność i odporność na pękanie.
Z kolei powolne chłodzenie, stosowane na przykład podczas wyżarzania, umożliwia spokojny przebieg przemian fazowych, prowadząc do powstania struktur takich jak perlit, ferryt czy sorbit. Te układy, choć mniej twarde, charakteryzują się większą jednorodnością i odpornością na obciążenia zmienne, co czyni je bardziej odpowiednimi do elementów pracujących pod długotrwałym naprężeniem.
Nie bez znaczenia pozostaje też sposób chłodzenia – czy odbywa się ono w powietrzu, wodzie, oleju, czy może w kontrolowanej atmosferze gazowej. Każde z tych środowisk oferuje inną intensywność odbierania ciepła, a tym samym wpływa na kinetykę przemian fazowych. Co więcej, wybór medium chłodzącego wpływa również na ryzyko powstania odkształceń, pęknięć lub utlenienia powierzchni obrabianego elementu.
W tym sensie chłodzenie nie jest jedynie mechanicznym procesem odbierania ciepła – to aktywny etap kształtowania struktury metalu, który wymaga takiej samej precyzji i planowania, jak pozostałe fazy obróbki cieplnej. Od jego przebiegu zależy, czy uzyskamy materiał twardy, sprężysty, podatny na dalszą obróbkę, czy też zbyt kruchy i narażony na awarie.
Rodzaje atmosfer stosowanych w obróbce cieplnej
Wiele procesów obróbki cieplnej odbywa się w podwyższonych temperaturach, gdzie powierzchnia metalu staje się szczególnie wrażliwa na oddziaływanie otaczającego środowiska. W takich warunkach nawet krótki kontakt z powietrzem może prowadzić do utleniania, odwęglenia, nawęglenia lub absorpcji szkodliwych gazów, co wpływa niekorzystnie na jakość, wygląd i właściwości wyrobu. Dlatego tak istotną rolę odgrywa dobór odpowiedniej atmosfery pieca, w której przebiega proces cieplny.
Jednym z najczęściej stosowanych rozwiązań są atmosfery ochronne, mające na celu ograniczenie reakcji chemicznych między metalem a otoczeniem. Mogą to być gazy obojętne, takie jak argon czy azot, które nie wchodzą w reakcję z obrabianym materiałem, lub mieszaniny gazów redukujących, np. wodoru z azotem, które dodatkowo przeciwdziałają utlenianiu. Tego rodzaju atmosfery są wykorzystywane wszędzie tam, gdzie kluczowe jest zachowanie czystej powierzchni metalu – na przykład w obróbce stali narzędziowych, stali nierdzewnych czy stopów specjalnych.
W procesach, których celem jest zmiana składu chemicznego warstwy wierzchniej materiału, stosuje się atmosfery aktywne – nasycone odpowiednimi pierwiastkami. W przypadku nawęglania są to mieszaniny bogate w węglowodory, jak metan lub propan, które dostarczają atomów węgla do powierzchni stali, umożliwiając tworzenie warstw utwardzonych dyfuzyjnie. Analogicznie, do procesów azotowania używa się atmosfer zawierających amoniak, a do borowania – gazów zawierających borowodory. Tego typu zabiegi, łączące obróbkę cieplną z chemiczną, pozwalają znacząco poprawić odporność na ścieranie i korozję bez konieczności zmiany całej objętości materiału.
Niektóre nowoczesne technologie wykorzystują również próżnię technologiczną jako środowisko obróbki cieplnej. Dzięki całkowitemu usunięciu powietrza i gazów aktywnych możliwe jest przeprowadzenie procesów w warunkach całkowicie neutralnych, co ma szczególne znaczenie w produkcji precyzyjnych części lotniczych, narzędzi chirurgicznych czy komponentów elektronicznych. Próżniowe piece umożliwiają również bardzo dokładne sterowanie temperaturą oraz eliminację wszelkich zanieczyszczeń gazowych, które mogłyby wpływać na mikrostrukturę materiału.
Obróbka cieplna metali – podsumowanie
Obróbka cieplna, choć od wieków wykorzystywana w przemyśle metalurgicznym, nie przestaje być dziedziną nowoczesną i dynamiczną. Współczesne technologie nie traktują jej już jako prostego sposobu na utwardzanie czy odprężanie metalu – to dziś precyzyjne narzędzie inżynierskie, pozwalające świadomie kształtować mikrostrukturę materiałów w sposób przewidywalny, powtarzalny i dostosowany do konkretnych zastosowań.
Zrozumienie, jak temperatura, czas i środowisko cieplne wpływają na przemiany fazowe i rozkład atomów w strukturze krystalicznej, pozwala projektować nie tylko właściwości mechaniczne, ale też odporność chemiczną, przewodność cieplną, stabilność wymiarową czy trwałość zmęczeniową materiału. To właśnie dzięki obróbce cieplnej stal może stać się jednocześnie twarda i sprężysta, a element wykonany z pozornie prostego metalu zyskuje właściwości zbliżone do materiałów kompozytowych.
W dobie zaawansowanych technologii – od przemysłu lotniczego, przez energetykę, po medycynę – coraz większego znaczenia nabiera również kontrola procesów cieplnych z dokładnością do pojedynczych stopni, minut, a nawet atomów. Wysokotemperaturowe symulacje, atmosfery ochronne, kontrola gradientów cieplnych i wykorzystanie próżni technologicznej pozwalają osiągnąć jakość, która jeszcze kilkadziesiąt lat temu była poza zasięgiem. Obróbka cieplna przestaje być etapem wtórnym – staje się centralnym elementem projektowania materiałów.
Właśnie dlatego znajomość procesów cieplnych, ich przebiegu i wpływu na właściwości metali, jest dziś jednym z filarów nowoczesnej inżynierii materiałowej. Nie wystarczy bowiem znać skład chemiczny stopu – trzeba rozumieć, jak „wypalić” z niego to, co najlepsze.