Metody badań struktury materiałów
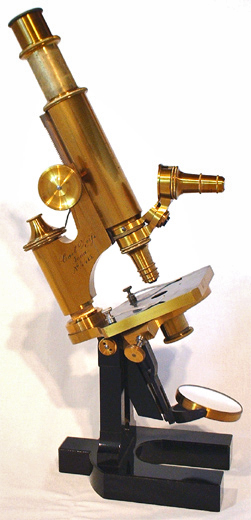
Spis treści
Choć metale i ich stopy są fundamentem współczesnej techniki, ich właściwości nie wynikają wyłącznie z chemicznego składu, lecz w równym stopniu – z wewnętrznej struktury materiału. To właśnie sposób, w jaki ułożone są atomy, jak kształtują się ziarna krystaliczne, jakie defekty występują w ich sieci i jak zorganizowana jest cała masa materiału w skali makro, decyduje o zachowaniu metalu podczas obróbki, eksploatacji, a nawet awarii. Z tego powodu badanie struktury materiałów metalowych stało się nieodłączną częścią pracy inżynierów, technologów i specjalistów ds. jakości.
Analiza struktury pozwala zrozumieć, dlaczego jeden metal jest twardy, ale kruchy, a inny – miękki, lecz wyjątkowo plastyczny. Dzięki obserwacjom i pomiarom możliwe jest ocenienie stopnia umocnienia materiału, kontrola poprawności obróbki cieplnej, wykrycie nieciągłości i wad wewnętrznych, a także przewidywanie zachowania elementu w warunkach eksploatacyjnych. Co więcej, właściwa interpretacja struktury umożliwia skuteczne projektowanie nowych stopów, optymalizację procesów technologicznych i przedłużanie trwałości konstrukcji.
W badaniach strukturalnych wyróżnia się kilka poziomów opisu: strukturę krystaliczną, czyli uporządkowany układ atomów w sieci krystalicznej; mikrostrukturę, obejmującą ziarna i fazy widoczne pod mikroskopem; oraz makrostrukturę, widoczną gołym okiem lub pod niewielkim powiększeniem, gdzie dostrzegalne są kierunki włóknistości, porowatość czy ślady odlewania. Uzupełnieniem są nowoczesne metody nieniszczące, które pozwalają ocenić stan wewnętrzny materiału bez jego zniszczenia, co ma kluczowe znaczenie w kontroli jakości gotowych elementów.
W kolejnych częściach artykułu przyjrzymy się najważniejszym technikom badawczym stosowanym do analizy struktury metali – zarówno klasycznym, jak i nowoczesnym, które umożliwiają precyzyjne spojrzenie w głąb materiału i lepsze zrozumienie jego właściwości.
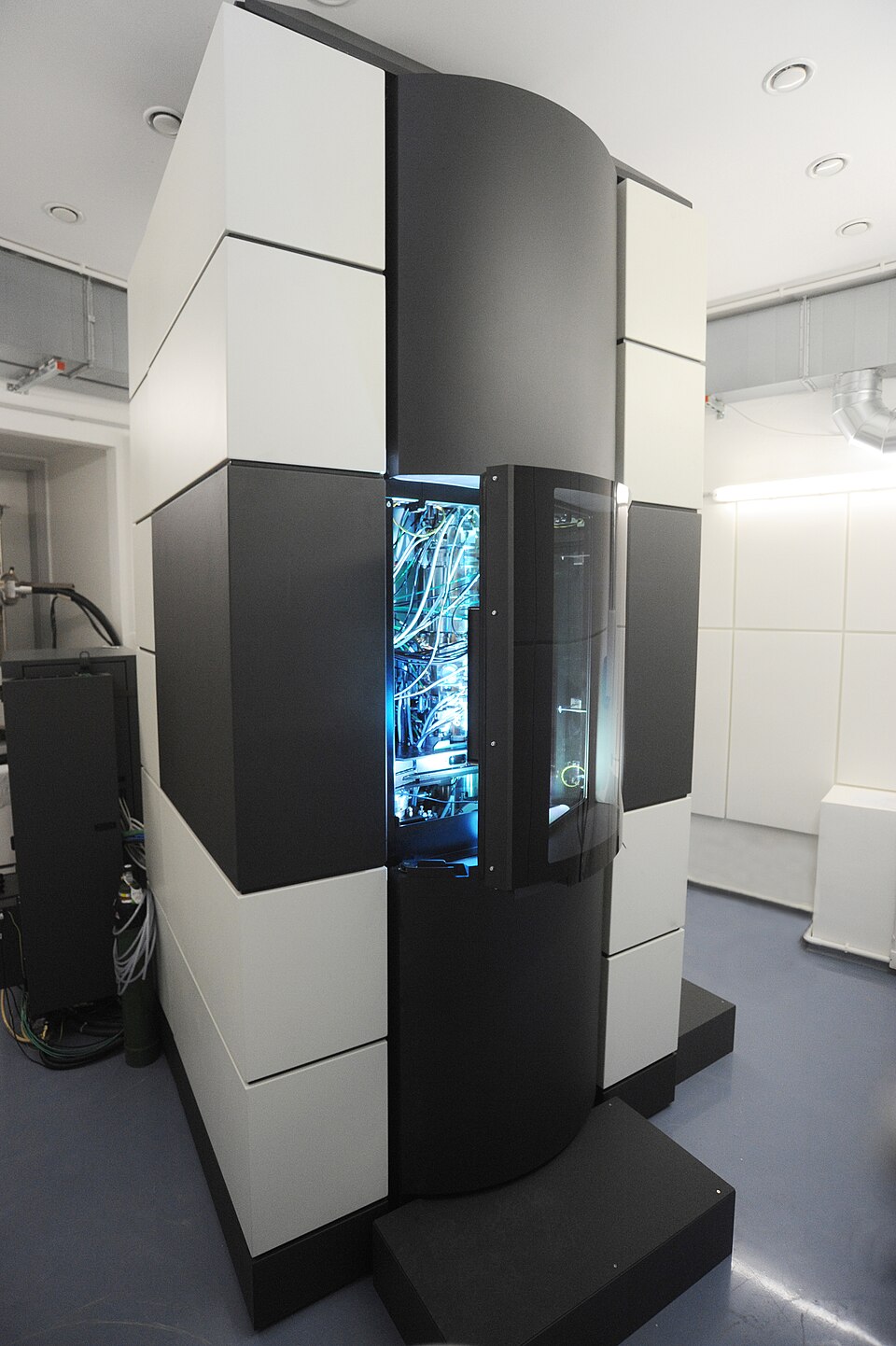
Promienie rentgenowskie i elektrony
Podstawą właściwości mechanicznych i technologicznych metali jest ich struktura krystaliczna, czyli sposób uporządkowania atomów w przestrzeni. Choć niewidoczna gołym okiem, decyduje ona o tak fundamentalnych cechach jak gęstość, przewodnictwo cieplne, rozszerzalność termiczna czy podatność na odkształcenie. Aby zajrzeć do tego atomowego porządku, nauka i technika wykorzystują jedną z najbardziej precyzyjnych metod fizycznych: dyfrakcję promieni rentgenowskich oraz, w mniejszym zakresie, dyfrakcję elektronów.
Gdy wiązka promieniowania rentgenowskiego pada na próbkę metalu, jej fale ulegają rozproszeniu na regularnie rozmieszczonych płaszczyznach atomowych wewnątrz kryształu. Powstaje wtedy charakterystyczny wzór dyfrakcyjny – układ linii lub plamek – który można zarejestrować i przeanalizować. Zjawisko to opisuje równanie Braggów, które pozwala powiązać kąt ugięcia promieni z odległościami między płaszczyznami sieci krystalicznej. Dzięki temu możliwe jest wyznaczenie parametrów komórki elementarnej, identyfikacja faz występujących w materiale, a także wykrycie naprężeń własnych i stopnia deformacji struktury.
Technika ta, zwana rentgenowską analizą dyfrakcyjną (XRD), jest stosowana zarówno w badaniach naukowych, jak i w kontroli przemysłowej – na przykład przy identyfikacji produktów korozji, ocenie skuteczności obróbki cieplnej czy badaniu zużycia powierzchni narzędzi. Wersją uproszczoną, choć mniej precyzyjną, są zdjęcia dyfrakcyjne wykonywane w komorach fotograficznych metodą Debye’a-Scherrera.
Uzupełnieniem klasycznej dyfrakcji jest analiza elektronowa, możliwa do przeprowadzenia w specjalistycznych mikroskopach transmisyjnych. Dzięki znacznie krótszej długości fali, elektrony pozwalają badać znacznie mniejsze obiekty niż promienie X. Obserwacje dyfrakcji elektronowej umożliwiają analizę lokalnej orientacji krystalicznej w skali pojedynczych ziaren lub warstw, co bywa kluczowe w materiałach cienkowarstwowych i nanostrukturalnych.
Zarówno promienie X, jak i elektrony są zatem bramą do świata, którego nie da się zobaczyć bezpośrednio. Ich precyzyjne oddziaływanie z materią umożliwia badanie nie tylko porządku krystalicznego, ale też defektów, przemieszczeń sieciowych czy obecności naprężeń. W ten sposób techniki dyfrakcyjne stają się podstawą dla inżynierii materiałowej na poziomie atomowym – tam, gdzie rozpoczyna się prawdziwe projektowanie właściwości materiału.
Mikroskopia metalograficzna
Choć struktura krystaliczna decyduje o właściwościach metali na poziomie atomowym, to w praktyce inżynierskiej równie ważna jest analiza ich mikrostruktury – czyli wzajemnego układu ziaren, faz, granic i ewentualnych nieciągłości w skali mikrometrów. Aby to osiągnąć, stosuje się mikroskopię metalograficzną, która pozwala obserwować powierzchnię odpowiednio przygotowanych próbek w świetle odbitym.
Podstawą tego badania jest przygotowanie tzw. zgładu metalograficznego – gładkiej, wypolerowanej powierzchni próbki, która zostaje poddana trawieniu chemicznemu. Proces ten uwidacznia granice ziaren oraz różnice między fazami dzięki różnemu stopniowi reakcji z odczynnikiem trawiącym. Następnie tak spreparowana powierzchnia jest obserwowana pod mikroskopem optycznym, który pozwala uzyskać powiększenia rzędu kilkuset razy, wystarczające do oceny wielkości ziaren, kształtu wtrąceń niemetalicznych czy charakteru przemian fazowych.
Jednym z przełomowych osiągnięć w tej dziedzinie było skonstruowanie mikroskopu metalograficznego przez Le Chateliera, który umożliwił obserwację odbitego światła na powierzchniach nieprzezroczystych – takich jak metale. Do dziś tego typu mikroskopy są podstawowym narzędziem pracy w laboratoriach kontroli jakości, działach badawczo-rozwojowych oraz uczelniach technicznych. Dzięki nim możliwe jest zbadanie, czy materiał ma jednolitą strukturę, czy procesy cieplne i mechaniczne zostały przeprowadzone prawidłowo oraz czy nie występują w nim groźne defekty.
Mikroskopia świetlna, mimo ograniczonej rozdzielczości w porównaniu do mikroskopii elektronowej, ma istotną przewagę praktyczną – jest stosunkowo szybka, niedroga i pozwala na ocenę znacznej powierzchni próbki. Dlatego jest niezastąpiona przy analizie seryjnej produkcji, gdzie liczy się szybkość diagnozy i powtarzalność wyników.
Obserwacje mikrostrukturalne umożliwiają klasyfikację metali według ich historii cieplnej i technologicznej, ocenę skuteczności obróbki cieplnej, analizę stanu zgniotu czy stopnia dezintegracji materiału. Mikroskopia metalograficzna otwiera zatem drogę do zrozumienia tego, co kryje się pod powierzchnią metalu – a często decyduje o jego sukcesie lub awarii w warunkach eksploatacyjnych.
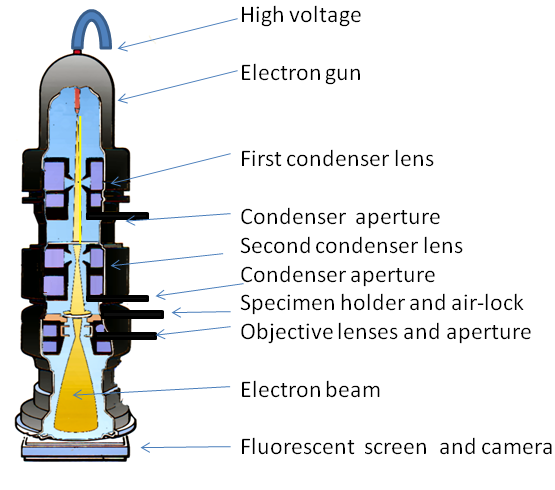
Mikroskopia elektronowa
Gdy wymagana jest szczegółowość wykraczająca poza możliwości mikroskopii świetlnej, sięga się po mikroskopię elektronową – technikę, która pozwala analizować strukturę materiału z dokładnością rzędu nanometrów, a nawet pojedynczych atomów. W przeciwieństwie do światła widzialnego, którego długość fali ogranicza rozdzielczość konwencjonalnych mikroskopów, wiązka elektronów – dzięki znacznie krótszej fali – umożliwia wgląd w najdrobniejsze szczegóły budowy metalu, w tym granice podziarn, dyspersje faz, defekty sieciowe czy przebiegi pęknięć.
Podstawą działania mikroskopu elektronowego jest emisja i skupienie elektronów na powierzchni próbki w warunkach wysokiej próżni. W zależności od konstrukcji urządzenia rozróżnia się dwie główne odmiany: skaningowy mikroskop elektronowy (SEM) i transmisyjny mikroskop elektronowy (TEM). Pierwszy pozwala na obrazowanie topografii i składu chemicznego powierzchni, drugi – na prześwietlenie cienkich foli metalicznych i uzyskanie szczegółowego obrazu struktury wewnętrznej.
W SEM wiązka elektronów przesuwa się liniowo po powierzchni próbki, a detektory rejestrują elektrony odbite lub wtórne. Powstały obraz charakteryzuje się dużą głębią ostrości i wysoką rozdzielczością, co umożliwia badanie morfologii przełomów, struktur spieków, powierzchni zużycia czy mikroząbków powstałych w wyniku obróbki. Dodatkowo, zintegrowane systemy mikroanalizy – takie jak EDS (Energy Dispersive Spectroscopy) – pozwalają określić skład chemiczny badanych fragmentów próbki, co czyni tę technikę niezwykle wszechstronną.
TEM z kolei oferuje jeszcze większą rozdzielczość, pozwalającą na obrazowanie układu sieci krystalicznej, błędów ułożenia atomów i obecności defektów punktowych. Ponieważ próbka musi być bardzo cienka, przygotowanie jej jest bardziej złożone, ale wyniki – nieporównywalnie bardziej precyzyjne. Umożliwia to badanie zjawisk zachodzących na granicach faz, w obszarach umocnionych czy po procesach dyfuzji.
Mikroskopia elektronowa otworzyła zupełnie nowy wymiar w diagnostyce materiałowej, pozwalając nie tylko oceniać jakość wyrobów, ale też zrozumieć mechanizmy ich degradacji i awarii. Współczesne urządzenia tej klasy są w stanie przeprowadzić analizę mikrostrukturalną, spektroskopową i fazową jednocześnie, co czyni je kluczowym narzędziem nowoczesnej inżynierii materiałowej – szczególnie w obszarze badań stopów specjalnych, nanomateriałów i cienkowarstwowych układów funkcjonalnych.
Makroskopia
Choć zaawansowane techniki badawcze pozwalają zaglądać w głąb materiału z niezwykłą dokładnością, nie można przecenić znaczenia makroskopii, czyli obserwacji metalu w skali dostępnej dla oka lub przy niewielkich powiększeniach. To właśnie od niej często rozpoczyna się diagnoza materiałowa, ponieważ wiele kluczowych informacji na temat jakości, pochodzenia i historii technologicznej metalu zawartych jest w jego makrostrukturze.
Makroskopia umożliwia ocenę cech widocznych bez konieczności mikroskopowej analizy: rozkładu porowatości, kierunku włókien w materiale kutym, przebiegu granic stref odlewniczych, obecności pęknięć, rozwarstwień czy tzw. wad pierwotnych, powstałych na etapie wytwarzania. Dzięki odpowiedniemu przygotowaniu powierzchni próbki – przez szlifowanie, trawienie lub przełamanie – możliwe staje się uwidocznienie dużych struktur, takich jak dendryty, strefy przemian fazowych czy rozkład zgorzelin.
Szczególnie cenne informacje dostarcza obserwacja przełomów – powierzchni powstałych na skutek pęknięcia elementu. W zależności od charakteru materiału i mechanizmu uszkodzenia przełom może mieć różne cechy: być błyszczący i ziarnisty w przypadku pęknięcia kruchego, lub matowy i włóknisty przy pęknięciu plastycznym. Analiza ta, często wykonywana w ramach badań fractograficznych, pozwala na rozpoznanie typu zniszczenia, jego genezy oraz ewentualnej obecności niejednorodności materiałowych, które mogły przyczynić się do awarii.
W praktyce przemysłowej makroskopia pełni ważną rolę w kontroli jakości odlewów, odkuwek, blach i spoin. Jest też niezastąpiona w analizie uszkodzeń elementów pracujących w warunkach zmiennych obciążeń, gdzie kluczowe jest rozpoznanie źródła inicjacji pęknięcia. W połączeniu z dokumentacją fotograficzną, makroskopowe obserwacje stają się nie tylko narzędziem diagnostycznym, ale też dowodowym w przypadku analizy przyczyn awarii.
Choć może wydawać się najprostszą z technik badawczych, makroskopia często dostarcza pierwszych i najbardziej bezpośrednich wskazówek, które ukierunkowują dalsze, bardziej szczegółowe badania mikro- i submikroskopowe. To właśnie ona pozwala szybko rozpoznać, czy badany materiał wymaga dalszej analizy, czy też jego struktura nie budzi zastrzeżeń.
Metody nieniszczące
W sytuacjach, gdy zachowanie integralności materiału jest absolutnym warunkiem, a usunięcie próbki lub jej uszkodzenie są niedopuszczalne, sięga się po metody nieniszczące, znane też jako NDT (Non-Destructive Testing). Te techniki umożliwiają ocenę jakości materiału, wykrywanie wad wewnętrznych i powierzchniowych, a także weryfikację zgodności struktury z wymaganiami projektowymi – bez konieczności naruszania badanego elementu.
Jedną z najczęściej stosowanych metod nieniszczących jest badanie radiograficzne, wykorzystujące promieniowanie rentgenowskie lub gamma. Promienie te przenikają przez materiał, a ich osłabienie zależy od gęstości i grubości wewnętrznych struktur. Różnice te rejestrowane są na specjalnych płytkach lub czujnikach cyfrowych, co pozwala uzyskać obraz przekroju materiału. Dzięki tej metodzie można wykryć pęcherze powietrzne, jamy skurczowe, nieciągłości, a także wtrącenia niemetaliczne, które mogłyby osłabić wytrzymałość konstrukcyjną elementu.
Inną powszechnie stosowaną techniką są badania ultradźwiękowe, w których przez materiał przepuszcza się fale dźwiękowe o wysokiej częstotliwości. Wszelkie nieciągłości – takie jak pęknięcia, rozwarstwienia czy pustki – powodują odbicie lub załamanie fali, co można łatwo zarejestrować na ekranie urządzenia pomiarowego. Badania ultradźwiękowe cechują się dużą precyzją, są szybkie, bezpieczne i nadają się do kontroli grubych i złożonych elementów.
W przypadku materiałów ferromagnetycznych bardzo przydatne okazują się badania magnetyczno-proszkowe. Polegają one na wytworzeniu pola magnetycznego w badanym elemencie i naniesieniu na jego powierzchnię drobnych cząstek ferromagnetycznych. W obecności wad – takich jak rysy lub pęknięcia powierzchniowe – linie pola magnetycznego ulegają zakłóceniu, powodując lokalne zgromadzenie cząstek, co pozwala łatwo zidentyfikować defekt wizualnie.
Wszystkie te metody mają wspólną zaletę: pozwalają wykonać pełną diagnostykę materiału lub wyrobu bez jego zniszczenia, co jest kluczowe nie tylko w fazie kontroli jakości, ale także podczas okresowych przeglądów eksploatacyjnych. Stosowane są z powodzeniem w przemyśle lotniczym, energetycznym, petrochemicznym, motoryzacyjnym i wszędzie tam, gdzie bezpieczeństwo konstrukcji i niezawodność działania są priorytetem.
Metody nieniszczące stanowią dziś nieodzowną część systemów zarządzania jakością i pozwalają w porę wykrywać potencjalne zagrożenia, zanim dojdzie do kosztownych awarii. Są świadectwem postępu technicznego, który umożliwia ocenę wnętrza materiału z taką samą skutecznością, jakby był on przezroczysty – bez potrzeby ingerencji w jego strukturę.
Metody badań struktury materiałów – podsumowanie
Zrozumienie i kontrola struktury wewnętrznej metali stanowią dziś jedno z najważniejszych narzędzi w rękach inżyniera materiałowego. To właśnie analiza krystaliczna, mikrostrukturalna, makroskopowa i nieniszcząca pozwala w pełni zrozumieć, jak materiał będzie się zachowywał w realnych warunkach – pod obciążeniem, w kontakcie z czynnikami chemicznymi, podczas intensywnego tarcia czy zmiennych temperatur.
Wiedza ta jest kluczowa nie tylko przy projektowaniu nowych materiałów, ale również przy ich weryfikacji, ocenie poprawności procesu produkcji, a nawet przy badaniu przyczyn uszkodzeń. Dzięki zastosowaniu różnorodnych metod badawczych – od promieni rentgenowskich po mikroskopy elektronowe i ultradźwięki – możliwe jest uzyskanie pełnego obrazu materiału: od poziomu atomowego aż po cechy makroskopowe widoczne gołym okiem.
Każda z omówionych technik pełni określoną rolę, a ich komplementarność pozwala nie tylko lokalizować wady, ale też przewidywać ich skutki i unikać ich w przyszłości. W efekcie nowoczesne badania struktury materiałów stają się podstawą odpowiedzialnej inżynierii – takiej, która nie opiera się wyłącznie na intuicji czy doświadczeniu, lecz na sprawdzalnych danych i precyzyjnej diagnozie.
W świecie, w którym bezpieczeństwo, trwałość i jakość konstrukcji mają bezpośrednie przełożenie na ludzkie życie i środowisko, poznanie wnętrza metalu staje się nie luksusem, lecz koniecznością.