Ursachen von Korrosion in der Öl- und Gasindustrie
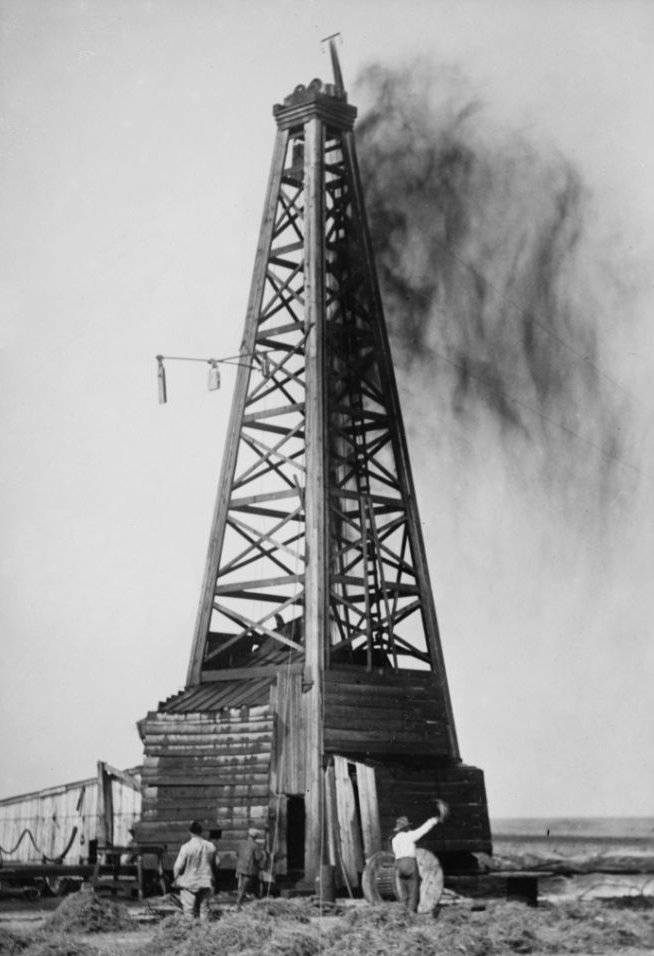
Inhaltsverzeichnis
Korrosion ist eines der größten Probleme in der Öl- und Gasindustrie und wirkt sich sowohl auf die Sicherheit als auch auf die Betriebskosten aus. Korrosion kommt in allen Bereichen der Öl- und Gasindustrie vor, von der Förderung über den Transport bis hin zur Lagerung von Rohöl und Gas. Die jährlichen Verluste durch Korrosion in der Industrie werden auf Milliarden von Dollar geschätzt. Unkontrollierte Korrosionsereignisse können zu katastrophalen Ausfällen der Infrastruktur führen.
Unzureichendes Korrosionsrisikomanagement kann Folgendes zur Folge haben:
- Beschädigung von Rohrleitungen und Lagertanks, wodurch sich das Risiko von Lecks und Explosionen erhöht.
- Produktionsunterbrechungen und hohe Reparaturkosten.
- Zersetzung von Metallteilen in Bohr- und Raffinerieanlagen verkürzt deren Lebensdauer.
- Umweltverschmutzung, insbesondere im Falle von Öl- oder Gasunfällen.
Der Schlüssel zur wirksamen Bekämpfung von Korrosion und zur Vermeidung unerwünschter Auswirkungen ist das Verständnis der Korrosionsursachen. Dieser Artikel befasst sich mit den wichtigsten Arten von Korrosion, die in der Öl- und Gasindustrie auftreten, sowie mit den Faktoren, die das Auftreten von Korrosion beschleunigen.
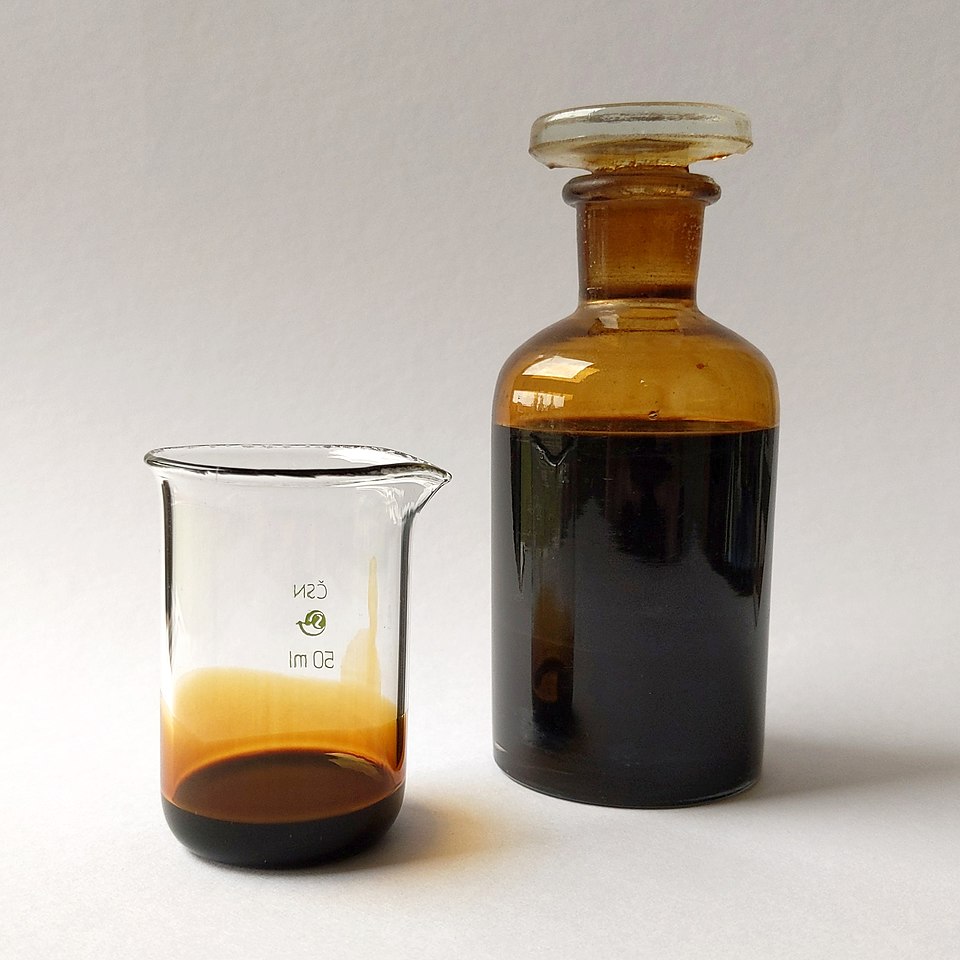
Arten von Korrosion in der Öl- und Gasindustrie
Abhängig von den Umgebungsbedingungen, der chemischen Zusammensetzung des Mediums und den Werkstoffeigenschaften kann Korrosion im Öl- und Gassektor verschiedene Formen annehmen. Die Unterscheidung zwischen den verschiedenen Korrosionsarten ist der Schlüssel zum wirksamen Schutz der Infrastruktur und zur Verlängerung ihrer Lebensdauer.
- Allgemeine Korrosion – ist die häufigste Art der Korrosion, bei der Metall auf der gesamten Oberfläche gleichmäßig oxidiert. Sie tritt in Gegenwart von Sauerstoff und Feuchtigkeit auf und führt zu einer allmählichen Zersetzung des Materials. Infolge dieses Prozesses nimmt die Dicke der Wände von Rohrleitungen und Tanks ab, was deren Festigkeit verringert. Diese Art der Korrosion ist relativ einfach zu überwachen. Sie erfordert jedoch systematische vorbeugende Maßnahmen wie Schutzbeschichtungen und Inhibitoren.
- Galvanische Korrosion – tritt auf, wenn zwei verschiedene Metalle in einer leitenden Umgebung in elektrischem Kontakt sind. Das weniger edle Metall (Anode) wird beschleunigt oxidiert, während das edlere Metall (Kathode) geschützt bleibt. Dieses Phänomen ist besonders wichtig bei Rohrleitungssystemen und Offshore-Strukturen, wo verschiedene Materialien miteinander verbunden werden müssen. Durch die richtige Auswahl der Materialien und die elektrische Isolierung zwischen ihnen kann diese Art von Korrosion verringert werden.
- Lochfraßkorrosion – ist eine lokale Form der Korrosion, bei der sich das Metall an kleinen, aber tiefen Stellen zersetzt. Sie tritt meist in Gegenwart von Chloridionen auf, die zur Bildung von Grübchen beitragen und die Struktur des Materials schwächen. Im Gegensatz zur allgemeinen Korrosion, die sich gleichmäßig ausbreitet, kann die Lochfraßkorrosion schnell zur Perforation von Bauteilen führen. Die Verwendung von korrosionsbeständigen Werkstoffen und Inhibitoren ist entscheidend, um sie zu verringern.
- Stress Corrosion Cracking (SCC) – ist ein Prozess, bei dem ein Material unter der gleichzeitigen Einwirkung von mechanischer Spannung und einer aggressiven chemischen Umgebung Risse bekommt. Die Risse können sich allmählich entwickeln, die schwerwiegenden Folgen können jedoch zu einem plötzlichen Versagen der Ausrüstung führen. In Rohrleitungen und Behältern, die unter hohem Druck und in schwefelwasserstoffhaltigen Umgebungen betrieben werden, tritt SCC besonders häufig auf.
- Mikrobiell beeinflusste Korrosion (MIC – Microbially Influenced Corrosion) entsteht durch die Aktivität von Mikroorganismen, die den Metallabbau durch die Produktion aggressiver Chemikalien beschleunigen. Besonders problematisch ist die Aktivität von sulfatreduzierenden Bakterien (SRB), die zur Bildung von Schwefelwasserstoff führt, wodurch die Gefahr von Korrosion und Materialversprödung steigt. Die Bekämpfung dieser Art von Korrosion erfordert regelmäßige Desinfektion und den Einsatz von Bioziden.
- Erosionskorrosion – entsteht durch intensive Strömung von Flüssigkeiten oder Gasen, vor allem bei Vorhandensein von festen Partikeln wie Sand oder mineralischen Ablagerungen im Medium. Durch das Zusammenwirken von mechanischen und chemischen Faktoren kommt es zu einem allmählichen Abtrag der Schutzschicht des Metalls, was zu einem beschleunigten Verschleiß der Bauteile führt. Maßnahmen zur Verringerung dieser Art von Korrosion sind die Verwendung von Werkstoffen mit erhöhter Abriebfestigkeit und die Kontrolle der Strömungsparameter.
Wichtige Faktoren, die die Korrosion beschleunigen
Die Korrosion in der Öl- und Gasindustrie erfolgt unter dem Einfluss vieler Faktoren, die den Metallabbau erheblich beschleunigen können. Das chemische Umfeld, die physikalischen Bedingungen und die Strömungsdynamik haben einen entscheidenden Einfluss auf die Entwicklung von Korrosionsprozessen. Die Kenntnis dieser Faktoren ist für eine wirksame Korrosionsprävention und die optimale Auswahl von Schutzmethoden unerlässlich.
Die Anwesenheit von Sauerstoff (O₂)
Insbesondere in wässriger Umgebung ist Sauerstoff einer der wichtigsten Faktoren, der die Korrosion beschleunigt. Wenn Sauerstoff mit Metall in Kontakt kommt, oxidiert es. Dabei entstehen Korrosionsprodukte wie Oxide und Rost. Schon geringe Mengen Sauerstoff, insbesondere in wasser- oder feuchtigkeitshaltigen Rohrleitungen oder Behältern, können die Korrosionsgeschwindigkeit erheblich erhöhen. Den Zugang von Sauerstoff zur Metalloberfläche durch Dichtungen, Schutzbeschichtungen und den Einsatz von Inhibitoren einzuschränken, ist der Schlüssel zur Reduzierung dieser Art von Korrosion.
Vorhandensein von Schwefelwasserstoff (H₂S) und Kohlendioxid (CO₂)
Die beiden häufigsten korrosiven Gase in der Erdölindustrie sind Schwefelwasserstoff (H₂S) und Kohlendioxid (CO₂). CO₂ („süße Korrosion“) – bildet bei Kontakt mit Wasser Kohlensäure (H₂CO₃). Diese senkt den pH-Wert und beschleunigt die Auflösung von Metallen, was zu Hohlräumen in Rohrleitungen und Tanks führt. H₂S („saure Korrosion“) – führt zur Bildung von Eisensulfiden (FeS). Diese können eine schützende Wirkung haben, erhöhen aber auch die Gefahr von lebhafter Korrosion und Wasserstoffversprödung. Die Korrosionswirkung dieser Gase hängt von ihrer Konzentration, der Temperatur und dem Druck ab. In aggressiven Umgebungen müssen daher Werkstoffe verwendet werden, die gegen CO und H₂S beständig sind.

Feuchtigkeit und das Vorhandensein von Wasser
Wasser spielt bei den meisten Korrosionsprozessen eine wichtige Rolle, da es als Elektrolyt wirkt und den Stromfluss zwischen Anode und Kathode auf der Metalloberfläche ermöglicht. Je nach seiner chemischen Zusammensetzung kann es die Korrosion in unterschiedlichem Maße beschleunigen.
- Süßwasser – enthält Sauerstoff, der die Metalloxidation fördert.
- Meerwasser – reich an Chlorid-Ionen (Cl-), die die Lochfraßkorrosion verstärken.
- Lagerstättenwasser – kann Sulfate, Karbonate und sulfatreduzierende Bakterien enthalten, die zu mikrobieller Korrosion führen.
Das Management des Wassergehalts in Ölsystemen umfasst seine Abtrennung, die Entfernung von korrosiven Verbindungen und die Verwendung von Inhibitoren.
Temperatur und Druck
Hohe Temperatur und hoher Druck sind einige der Schlüsselfaktoren, die die Geschwindigkeit und die Art der Korrosionsprozesse in der Öl- und Gasindustrie beeinflussen. Ihr Einfluss ist besonders wichtig in extremen Umgebungen wie Tiefbohrungen, Hochdruck-Pipelines und Offshore-Anlagen.
Die Temperatur wirkt sich direkt auf die Geschwindigkeit der chemischen und elektrochemischen Reaktionen aus, die zu Korrosion führen. Ein Temperaturanstieg beschleunigt die Oxidation von Metallen und die Reaktionen mit korrosiven Gasen und erhöht deren Aggressivität. Gleichzeitig können Schutzschichten, wie die passive Oxidschicht auf nichtrostenden Stählen, destabilisiert werden, wodurch das Metall anfälliger für Korrosion wird. Erhöhte Temperaturen wirken sich auch auf die Löslichkeit von Gasen in Wasser aus – CO₂ und H₂S können intensiver mit Wasser reagieren und aggressive Säuren bilden, die Metalloberflächen angreifen.
Hohe Temperaturen können auch zum Abbau von Korrosionsinhibitoren führen, d. h. von Stoffen, die die Zersetzung von Metall verlangsamen. Einige Inhibitoren verlieren unter extremen thermischen Bedingungen ihre schützenden Eigenschaften, so dass der Einsatz von resistenteren Chemikalien erforderlich wird. Spezifische Korrosionsarten wie Hochtemperaturkorrosion, d.h. Metalloxidation ohne flüssiges Wasser, die z.B. in Kesseln und Wärmetauschern auftritt, können unter bestimmten Bedingungen auftreten. Die Sulfidkorrosion, die in schwefelhaltiger Umgebung auftritt und vor allem in der Erdölraffination von Bedeutung ist, ist eine weitere Korrosionsart.
Erhöhte Temperaturen können auch zu Spannungsrisskorrosion führen. Dabei handelt es sich um die Bildung von Rissen im Gefüge eines Werkstoffs, die durch eine Kombination aus mechanischer Beanspruchung und aggressiver chemischer Umgebung verursacht wird. Da sich diese Schäden unbemerkt entwickeln und zu einem plötzlichen Versagen führen können, sind sie besonders gefährlich.
Druck wirkt sich auf die Intensität der Korrosion aus, indem er die physikalisch-chemischen Eigenschaften der im System vorhandenen Gase und Flüssigkeiten verändert. Hoher Druck erhöht die Löslichkeit von CO₂ und H₂S in Wasser, wodurch das Medium aggressiver gegenüber Strukturmaterialien wird. Wenn diese Gase mit Feuchtigkeit kombiniert werden, bilden sie Säuren, die die Metallzersetzung beschleunigen, was in Systemen, die unter hohem Druck betrieben werden, besonders problematisch erscheint.
Als weiterer wichtiger Faktor ist zu berücksichtigen, dass hoher Druck die Materialbeständigkeit beeinträchtigt. Extremer Druck führt zu verstärkten chemischen und mechanischen Einflüssen auf Metalloberflächen in tiefen Bohrlöchern und Pipelines. Dies kann zu einer Schwächung der Materialstruktur und zu einer erhöhten Anfälligkeit für Kavitation führen – die Bildung und das Kollabieren von Dampfblasen, die zu einer Beschädigung der Metalloberfläche durch heftige Stöße und zu einer Beschleunigung des Abbaus führen können.
Beispiele für typische korrosionsgefährdete Stellen
Korrosion tritt in der Öl- und Gasindustrie bei vielen Infrastrukturkomponenten auf, vor allem dort, wo Metalle aggressiven chemischen Umgebungen, hohem Druck und hohen Temperaturen ausgesetzt sind. Ihre Auswirkungen können Pipelines, Tanks und Prozessanlagen beschädigen, was zu kostspieligen Ausfallzeiten und Sicherheitsrisiken führt.
Pipelines, Tanks und Übertragungssysteme
Rohrleitungen und Lagertanks gehören zu den am häufigsten korrodierenden Infrastrukturkomponenten, da ihre Wände in ständigem Kontakt mit einem Medium stehen, das Wasser, CO₂, H₂S und mechanische Verunreinigungen enthält. Innenkorrosion kann zu Lochfraß und Perforation führen, während Außenkorrosion, verursacht durch Feuchtigkeit, Sauerstoff und Streuströme, die Struktur des Materials schwächt. Besonders gefährdet sind unterirdische Rohrleitungen und Tanks, die Temperaturschwankungen ausgesetzt sind, die Kondensation und die Entwicklung von atmosphärischer Korrosion verursachen. Korrosionsschutz basiert auf kathodischem Schutz, dem Einsatz von Inhibitoren und Schutzbeschichtungen.
Offshore-Infrastruktur und Bohrausrüstung
Offshore-Bohrplattformen und Pipelines arbeiten in einer äußerst aggressiven Umgebung, in der Salzwasser, starke Strömungen und hohe Luftfeuchtigkeit die Korrosion beschleunigen. Galvanische Korrosion tritt an den Grenzflächen verschiedener Metalle auf, was besonders gefährlich ist, und Erosionskorrosion, die unter dem Einfluss von starkem Wasserstrom und Schwebeteilchen zu Oberflächenschäden führt. Insbesondere in Gegenwart von H₂S sind Bohrlochausrüstungen, einschließlich Rohre und Ventile, zusätzlich der Spannungsrisskorrosion und Wasserstoffversprödung ausgesetzt. Hochdruckbeständige Werkstoffe, kathodischer Korrosionsschutz und spezielle Korrosionsschutzbeschichtungen werden eingesetzt, um die Schädigung zu verringern.
Kühlsysteme und Wärmetauscher
Kühlsysteme und Wärmetauscher sind anfällig für Korrosion, die durch hohe Temperaturen, wechselnde Betriebsbedingungen und aggressive Chemikalien in technologischen Prozessen entsteht. Zu den häufigsten Problemen gehören Erosionskorrosion, die durch eine schnelle Flüssigkeitsströmung verursacht wird, mikrobielle Korrosion, die mit Bakterienwachstum zusammenhängt, und Vibrationskorrosion, die Metallkomponenten unter mechanischen und umweltbedingten Belastungen schwächt. Die richtige Auswahl der Werkstoffe, die regelmäßige Kontrolle der Wasserzusammensetzung und die zyklische Reinigung der Systeme sind wichtige Vorbeugungsmaßnahmen.
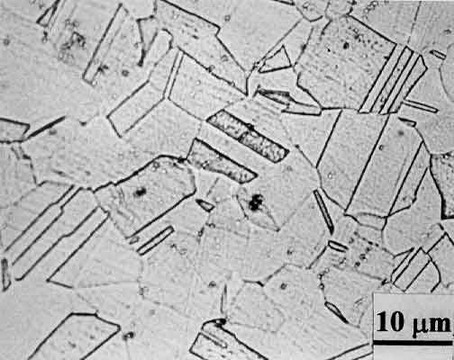
Auswirkungen von Korrosion in der Öl- und Gasindustrie
Korrosion im Öl- und Gassektor hat schwerwiegende wirtschaftliche, ökologische und betriebliche Folgen. Die Verschlechterung der Infrastruktur führt zu ungeplanten Ausfallzeiten, erhöhten Wartungskosten und Risiken für die Sicherheit von Mensch und Umwelt.
Erhöhte Betriebs- und Wartungskosten
In der Öl- und Gasindustrie ist Korrosion einer der Hauptfaktoren, die die Betriebskosten beeinflussen. Beschädigte Pipelines zu reparieren, korrodierte Komponenten auszutauschen und Korrosionsschutzsysteme zu implementieren, verursacht enorme Kosten. Erhebliche finanzielle Aufwendungen sind auch für häufige Inspektionen und die Überwachung des Zustands der Infrastruktur erforderlich. Weltweit belaufen sich die jährlichen korrosionsbedingten Kosten in diesem Bereich auf Milliarden von Dollar.
Fortschreitende Korrosion kann die Ursache für Anlagenausfälle, Leckagen und Schäden an Rohrleitungen und Behältern sein, mit der Folge von Produktionsunterbrechungen. Diese Unterbrechungen führen nicht nur zu einer Verringerung der betrieblichen Effizienz, sondern auch zu zusätzlichen finanziellen Verlusten im Zusammenhang mit Reparaturen und Verzögerungen bei der Auslieferung. Im Extremfall kann Korrosion zum vollständigen Ausfall der Infrastruktur führen, was besonders bei Offshore-Anlagen und Tiefseebohrungen problematisch ist.
Die Korrosion von Öl- und Gasinfrastrukturen kann zu katastrophalen Ausfällen führen, wie z. B. Pipelinebrüchen, entzündlichen Leckagen und Explosionen, die das Leben und die Gesundheit der Arbeiter und der umliegenden Gemeinden direkt bedrohen. Gas- oder Ölaustritte können Brände und in extremen Fällen Explosionen auf Bohrinseln oder in Raffinerien verursachen. Die richtige Vorbeugung und Kontrolle von Korrosion ist der Schlüssel zur Minimierung des Unfallrisikos.
Auswirkungen auf die Umwelt
Katastrophale Auswirkungen auf aquatische und terrestrische Ökosysteme hat Korrosion, die zum Austritt von Öl, Gas oder Chemikalien führt. Das Eindringen dieser Stoffe in den Boden und das Grundwasser führt zu Kontaminationen, die Jahrzehnte andauern können. Ölverschmutzungen in den Meeren führen zu großen Verlusten an Meerestieren und zur Zerstörung von Küstenlebensräumen. Umweltkatastrophen infolge von Ölverschmutzungen verursachen oft Schäden in Millionenhöhe und führen zu Sanktionen gegen die Unternehmen, die für die Ölverschmutzung verantwortlich sind.
Einer der bemerkenswertesten Fälle, in denen Korrosion zu einer Umweltkatastrophe geführt hat, war die Ölpest in der Prudhoe Bay in Alaska im Jahr 2006, bei der die Öltransportpipeline durch innere Korrosion infolge von Sedimentablagerungen und unzureichendem Korrosionsschutz perforiert wurde. Die Beschädigung der Infrastruktur hatte das Auslaufen von mehr als 200.000 Gallonen Öl in die arktische Tundra und die Verschmutzung einer Fläche von mehreren Hektar zur Folge. Der Ölteppich hatte katastrophale Auswirkungen auf das lokale Ökosystem, die Zerstörung von Lebensräumen für Tiere und Pflanzen und langfristige ökologische Folgen. Eine kostspielige Dekontaminierung war erforderlich, und das Unternehmen, das für die Verwaltung der Infrastruktur zuständig war, wurde mit finanziellen Sanktionen und der Verpflichtung zur Modernisierung der Infrastruktur belegt.
Strategien zur Minimierung und Vermeidung von Korrosion
Korrosion in der Öl- und Gasindustrie ist unvermeidlich, kann aber durch geeignete Schutzstrategien wirksam kontrolliert und gemildert werden . Ein wirksames Korrosionsrisikomanagement verlängert nicht nur die Lebensdauer der Infrastruktur, sondern senkt auch die Betriebskosten und das Ausfallrisiko.
Kathodischer Schutz
Eine der wirksamsten Methoden zum Schutz von Metallen vor Korrosion ist der kathodische Schutz, der vor allem bei Rohrleitungen, Tanks sowie unterirdischen und Offshore-Strukturen eingesetzt wird. Dabei werden elektrischer Strom oder aktive Anoden eingesetzt, um das elektrochemische Potenzial des zu schützenden Metalls zu verringern, so dass der Korrosionsprozess gehemmt wird.
Es gibt zwei Hauptarten des kathodischen Schutzes:
- Galvanischer Schutz (unter Verwendung von Opferanoden) – werden Metalle mit geringerem elektrochemischen Potenzial wie Zink, Magnesium oder Aluminium verwendet, die einem kontrollierten Verschleiß unterliegen und so den eigentlichen Baustoff schützen.
- Kathodischer Korrosionsschutz mit eingeprägtem Strom (ICCP) – beinhaltet den Anschluss einer Gleichstromquelle an die zu schützende Struktur, die durch die kontrollierte Abgabe von Elektronen Korrosion verhindert.
Kathodische Schutzsysteme sind bei Übertragungsleitungen, Offshore-Strukturen und Lagertanks, wo die Korrosion besonders stark ist, unerlässlich.
Anwendung von Korrosionsinhibitoren
Korrosionsinhibitoren sind spezielle Chemikalien, die dem Arbeitsmedium zugesetzt werden, um Korrosionsreaktionen zu verlangsamen oder vollständig zu verhindern. Sie wirken, indem sie eine Schutzschicht auf der Metalloberfläche bilden oder die korrosiven Eigenschaften der Umgebung verändern.
Die Einteilung der Korrosionsinhibitoren umfasst:
- Anodische Inhibitoren – reduzieren die Geschwindigkeit der Metalloxidationsreaktion.
- Kathodische Inhibitoren – reduzieren die Geschwindigkeit der Sauerstoff- oder Wasserstoffreduktionsreaktion.
- Gemischte Inhibitoren – wirken gleichzeitig an der Anode und der Kathode und verlangsamen den gesamten elektrochemischen Prozess.
Korrosionsinhibitoren sind in der Öl- und Gasindustrie weit verbreitet, vor allem in Pipelines, Wassertransportsystemen und Bohrausrüstungen, wo mechanischer oder kathodischer Schutz schwierig zu realisieren ist.
Auswahl widerstandsfähiger Werkstoffe und Schutzschichten
Die richtige Auswahl der Werkstoffe ist der Schlüssel zur Verringerung des Korrosionsrisikos. In Umgebungen mit hoher chemischer Aggressivität werden Edelstähle, Nickellegierungen, hochfeste legierte Stähle und Titan verwendet, die eine erhöhte Korrosionsbeständigkeit aufweisen.
Zusätzlichen Schutz bieten Korrosionsschutzbeschichtungen, die als Barriere zwischen dem Metall und der aggressiven Umgebung wirken. Zu den am häufigsten verwendeten Lösungen gehören:
- Epoxid- und Polyurethanbeschichtungen – werden in Rohrleitungen und Tanks verwendet.
- Metallschutzbeschichtungen (z. B. Zink, Aluminium) – bieten kathodischen Schutz für lange Zeiträume.
- Schutzbarrieren aus Keramik und Verbundwerkstoffen – werden in extremen Umgebungen eingesetzt, wie z. B. auf Bohrinseln und in Raffinerieanlagen.
Ursachen von Korrosion in der Öl- und Gasindustrie – Zusammenfassung
Korrosion verursacht hohe Kosten, Sicherheitsrisiken und Umweltschäden in der Öl- und Gasindustrie. Wirksamer Schutz der Infrastruktur erfordert Verständnis der Korrosionsmechanismen und geeignete Präventionsstrategien wie kathodischen Schutz, Korrosionsinhibitoren, Schutzbeschichtungen und regelmäßige Überwachung.
Korrosionsschutz ist entscheidend für die Langlebigkeit der Infrastruktur und die Minimierung des Ausfallrisikos. Moderne Technologien ermöglichen eine immer effektivere Kontrolle dieses Prozesses, was angesichts der steigenden Betriebs- und Umweltanforderungen wichtig ist.
Dieser Artikel basiert auf dem Buch „Metallurgy and Corrosion Control in Oil and Gas Production“ von Robert Heidersbach.