Causas de la corrosión en la industria del petróleo y el gas
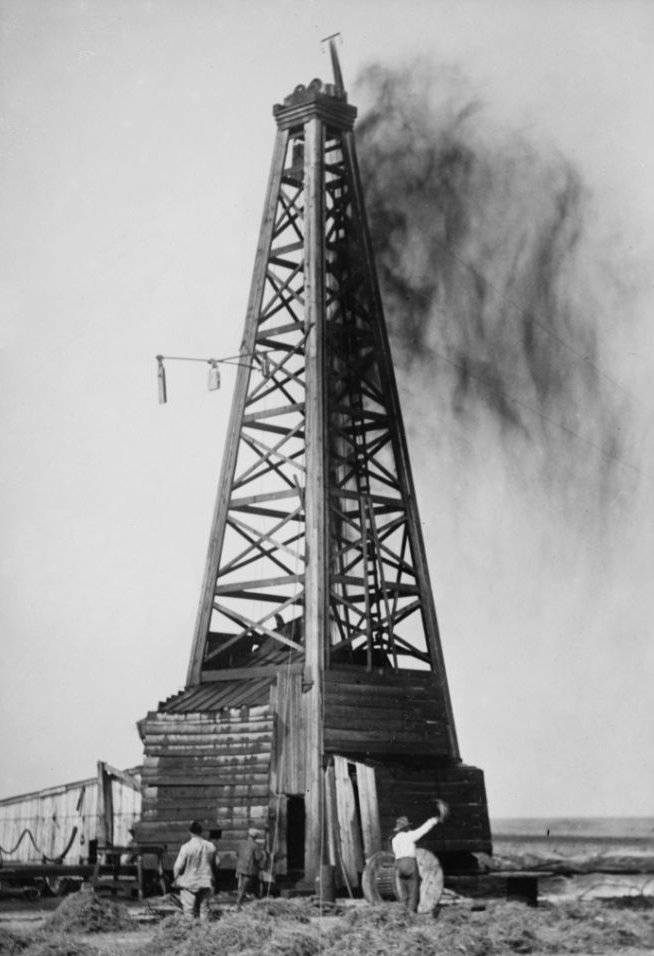
Índice
La corrosión es uno de los problemas más graves de la industria del petróleo y el gas, ya que afecta a la seguridad y a los costes de explotación. Se produce en todas las fases de la explotación, desde la extracción hasta el transporte y el almacenamiento de materias primas. Se calcula que las pérdidas anuales relacionadas con la corrosión en la industria ascienden a miles de millones de dólares, y los episodios de corrosión incontrolados pueden provocar fallos catastróficos en las infraestructuras.
Una gestión inadecuada del riesgo de corrosión puede provocar lo siguiente:
- Daños en tuberías y tanques de almacenamiento que aumentan el riesgo de fugas y explosiones.
- Interrupciones de la producción y elevados costes de reparación.
- Degradación de piezas metálicas en los equipos de perforación y refinado, lo que acorta su vida útil.
- Contaminación ambiental, especialmente, en el caso de vertidos de petróleo o gas.
Comprender las causas de la corrosión es clave para controlarla eficazmente y prevenir efectos no deseados. En este artículo, se analizan los principales tipos de corrosión que se producen en la industria del petróleo y el gas y los factores que la aceleran.
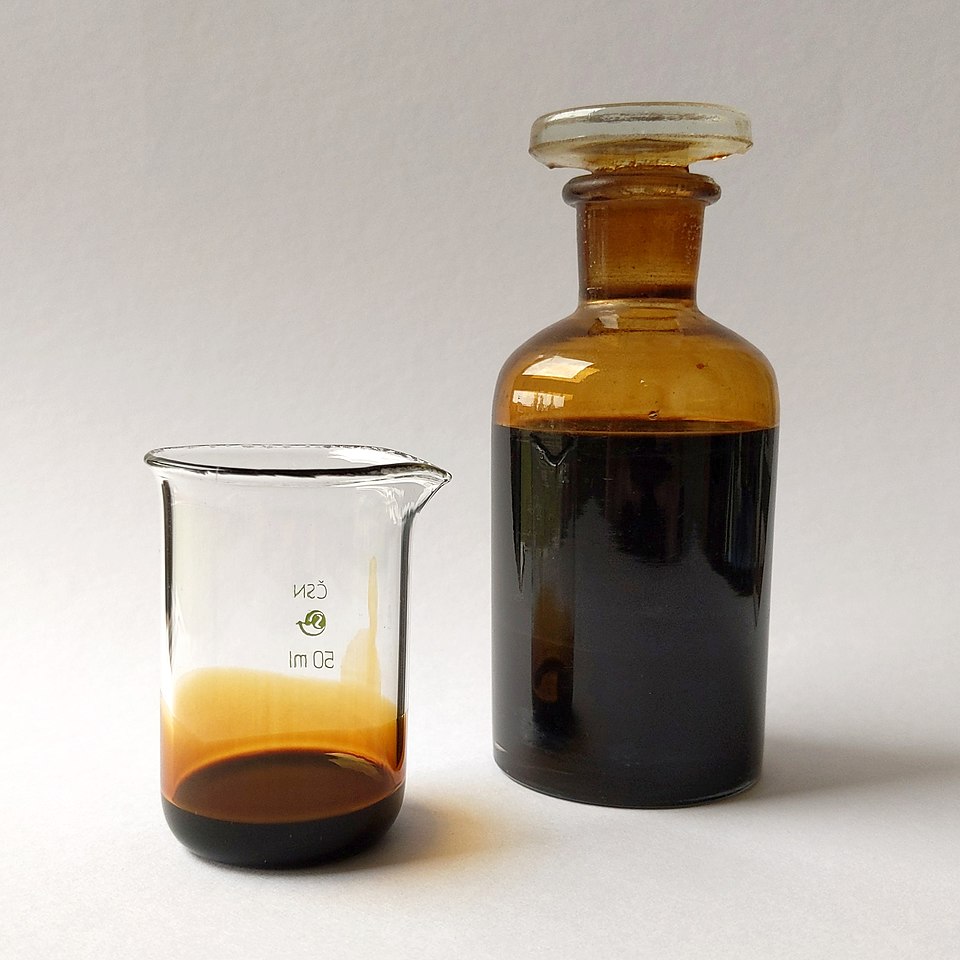
Tipos de corrosión en la industria del petróleo y el gas
La corrosión en el sector del petróleo y el gas puede adoptar distintas formas en función de las condiciones ambientales, la composición química del medio y las propiedades de los materiales. Distinguir entre los distintos tipos de corrosión es clave para proteger eficazmente las infraestructuras y prolongar su vida útil.
- Corrosión general: es el tipo más común de corrosión, en el que el metal sufre una oxidación uniforme en toda la superficie. Se produce en presencia del oxígeno y la humedad, lo que conduce a la degradación gradual del material. Como resultado de este proceso, el espesor de las paredes de las tuberías y los depósitos disminuye, lo que reduce su resistencia. Aunque este tipo de corrosión es relativamente fácil de controlar, requiere medidas preventivas sistemáticas, como el uso de revestimientos protectores e inhibidores.
- Corrosión galvánica: se produce cuando dos metales diferentes están en contacto eléctrico en un entorno conductor. El metal menos noble (ánodo) sufre una oxidación acelerada, mientras que el metal más noble (cátodo) permanece protegido. Este fenómeno es especialmente importante en sistemas de tuberías y estructuras marinas, en los que es necesario unir materiales diferentes. La selección adecuada de los materiales y el aislamiento eléctrico entre ellos sirven para reducir este tipo de corrosión.
- Corrosión por picaduras: es una forma local de corrosión en la que el metal se degrada en puntos pequeños pero profundos. Suele producirse en presencia de iones cloruro, que contribuyen a la formación de picaduras, lo que debilita la estructura del material. A diferencia de la corrosión general, que se distribuye uniformemente, la corrosión por picaduras puede llevar rápidamente a la perforación de componentes estructurales. El uso de materiales resistentes a la corrosión e inhibidores es crucial para reducirla.
- Agrietamiento por corrosión bajo tensión (SCC o Stress Corrosion Cracking): es un proceso en el que un material se agrieta bajo la acción simultánea de una tensión mecánica y un entorno químico agresivo. Las grietas pueden desarrollarse gradualmente, pero las consecuencias graves provocan el fallo repentino del equipo. El SCC se produce especialmente en tuberías y depósitos que funcionan a alta presión y en entornos que contienen sulfuro de hidrógeno.
- Corrosión por influencia microbiana (MIC o Microbially Influenced Corrosion): se produce debido a la actividad de microorganismos que aceleran la degradación del metal mediante la producción de sustancias químicas agresivas. La actividad de las bacterias reductoras de sulfato (BRS) es particularmente problemática, ya que conduce a la formación de sulfuro de hidrógeno y aumenta el riesgo de corrosión y fragilización del material. La lucha contra este tipo de corrosión requiere una desinfección periódica y el uso de biocidas.
- Corrosión por erosión: se produce debido al flujo intensivo de líquido o gas, principalmente, cuando el medio contiene partículas sólidas como arena o depósitos minerales. La combinación de factores mecánicos y químicos provoca una abrasión gradual de la capa protectora del metal, lo que conduce a un desgaste acelerado de los componentes. Para reducir este tipo de corrosión, se utilizan materiales con mayor resistencia a la abrasión y se controlan los parámetros de flujo.
Factores clave que aceleran la corrosión
La corrosión en la industria del petróleo y el gas se produce bajo la influencia de muchos factores que pueden acelerar significativamente la degradación del metal. El entorno químico, las condiciones físicas y la dinámica del flujo de fluidos tienen una influencia clave en el desarrollo de los procesos de corrosión. El conocimiento de estos factores es esencial para una prevención eficaz de la corrosión y una selección óptima de los métodos de protección.
La presencia de oxígeno (O₂)
El oxígeno es uno de los principales factores que aceleran la corrosión, especialmente, en medios acuosos. Cuando entra en contacto con un metal, provoca su oxidación y da lugar a la formación de productos de corrosión como óxidos y herrumbre. De hecho, incluso pequeñas cantidades de oxígeno pueden aumentar significativamente la velocidad de corrosión, especialmente, cuando está presente en tuberías o depósitos que contienen agua o humedad. Restringir el acceso de oxígeno a la superficie metálica mediante juntas, revestimientos protectores y el uso de inhibidores es clave para reducir este tipo de corrosión.
La presencia de sulfuro de hidrógeno (H₂S) y dióxido de carbono (CO₂)
El sulfuro de hidrógeno (H₂S) y el dióxido de carbono (CO₂) son los dos gases corrosivos más comunes en la industria petrolera. CO₂ («corrosión dulce»): cuando entra en contacto con el agua, forma ácido carbónico (H₂CO₃), que reduce el pH y acelera la disolución del metal, lo que provoca cavidades en tuberías y depósitos. H₂S («corrosión ácida»): provoca la formación de sulfuros de hierro (FeS), que pueden tener un efecto protector, pero también aumentan el riesgo de corrosión viva y fragilización por hidrógeno.
El efecto de estos gases sobre la corrosión depende de su concentración, temperatura y presión, por lo que es necesario utilizar materiales resistentes al CO₂ y al H₂S en ambientes agresivos.

La humedad y la presencia de agua
El agua es clave en la mayoría de los procesos de corrosión porque actúa como electrolito. Es decir, permite que la corriente fluya entre el ánodo y el cátodo de la superficie metálica. Dependiendo de su composición química, puede acelerar la corrosión en distintos grados.
- Agua dulce: contiene oxígeno, que favorece la oxidación del metal.
- Agua de mar: rica en iones cloruro (Cl-), que intensifican la corrosión por picaduras.
- Agua de yacimiento: puede contener sulfatos, carbonatos y bacterias reductoras de sulfatos, lo que provoca corrosión microbiana.
La gestión del contenido de agua en los sistemas petrolíferos incluye su separación, la eliminación de compuestos corrosivos y el uso de inhibidores.
La temperatura y la presión
La alta temperatura y la presión son algunos de los factores clave que influyen en la velocidad y la naturaleza de los procesos de corrosión en la industria del petróleo y el gas. Su impacto es especialmente significativo en entornos extremos como pozos profundos, tuberías de alta presión e instalaciones en alta mar.
La temperatura afecta directamente a la velocidad de las reacciones químicas y electroquímicas que conducen a la corrosión. Así pues, un aumento de la temperatura acelera la oxidación del metal y las reacciones con los gases corrosivos, lo que aumenta su agresividad. Al mismo tiempo, puede desestabilizar las capas protectoras, como la capa de óxido pasiva en los aceros inoxidables y hacer que el metal sea más susceptible a la corrosión. Una temperatura elevada también afecta a la solubilidad de los gases en el agua: el CO₂ y el H₂S pueden reaccionar más intensamente con el agua y formar ácidos agresivos que atacan a las superficies metálicas.
Las altas temperaturas también pueden provocar la descomposición de los inhibidores de la corrosión, que son sustancias que se utilizan para ralentizar la degradación del metal. Algunos inhibidores pierden sus propiedades protectoras en condiciones térmicas extremas, lo que requiere el uso de productos químicos más resistentes. También pueden producirse tipos específicos de corrosión en determinadas condiciones, como la corrosión a alta temperatura, que es la oxidación del metal sin agua líquida y se produce en calderas e intercambiadores de calor, por ejemplo. Otro tipo es la corrosión por sulfuro, que se produce en entornos ricos en azufre, especialmente importante en los procesos de refinado del petróleo.
Las temperaturas elevadas también pueden favorecer el agrietamiento por corrosión bajo tensión (SCC), que es la formación de grietas en la estructura de un material causada por una combinación de tensión mecánica y un entorno químico agresivo. Este tipo de daño es especialmente peligroso porque puede desarrollarse de forma imperceptible y provocar un fallo repentino.
La presión afecta a la intensidad de la corrosión al cambiar las propiedades fisicoquímicas de los gases y líquidos presentes en el sistema. La alta presión aumenta la solubilidad del CO₂ y el H₂S en el agua y hace que el medio sea más agresivo con los materiales estructurales. Estos gases, combinados con la humedad, forman ácidos que aceleran la degradación de los metales, lo que resulta especialmente problemático en los sistemas que funcionan a alta presión.
Otro factor importante es el efecto de la alta presión sobre la durabilidad de los materiales. En pozos profundos y tuberías de transmisión, la presión extrema provoca impactos químicos y mecánicos más intensos en las superficies metálicas. Esto puede debilitar la estructura del material y aumentar la susceptibilidad a la cavitación, es decir, a la formación y colapso de burbujas de vapor que pueden dañar la superficie metálica mediante impactos violentos y acelerar su degradación.
Ejemplos de lugares típicos expuestos a la corrosión
La corrosión en la industria del petróleo y el gas se produce en muchos componentes de las infraestructuras, especialmente allí donde los metales están expuestos a entornos químicos agresivos, alta presión y temperatura. Sus efectos pueden dañar tuberías, tanques y equipos de proceso, lo que provoca costosos tiempos de inactividad y riesgos para la seguridad.
Tuberías, tanques y sistemas de transmisión
Las tuberías y los tanques de almacenamiento se encuentran entre los componentes de las infraestructuras que se corroen con más frecuencia, ya que sus paredes están en contacto constante con un medio que contiene agua, CO₂, H₂S e impurezas mecánicas. La corrosión interna puede provocar picaduras y perforaciones, mientras que la corrosión externa, causada por la humedad, el oxígeno y las corrientes parásitas, debilita la estructura del material. Las tuberías y depósitos subterráneos expuestos a cambios de temperatura, que provocan condensación y el desarrollo de corrosión atmosférica, corren un riesgo especial. La prevención de la corrosión se basa en la protección catódica, el uso de inhibidores y revestimientos protectores.
Infraestructuras marinas y equipos de perforación
Las plataformas de perforación de alta mar y las tuberías operan en un entorno extremadamente agresivo en el que el agua salada, las fuertes corrientes y la elevada humedad aceleran la corrosión. La corrosión galvánica se produce en la interfaz de varios metales, lo que resulta especialmente peligroso, al igual que la corrosión por erosión, que provoca daños en la superficie bajo la influencia de fuertes corrientes de agua y partículas en suspensión. Los equipos de perforación, incluidas las tuberías y válvulas, están sujetos además a la corrosión bajo tensión y a la fragilización por hidrógeno, especialmente, en presencia de H₂S. Para reducir la degradación, se utilizan materiales resistentes a la alta presión, protección catódica anódica y revestimientos anticorrosión especializados.
Sistemas de refrigeración e intercambiadores de calor
Los sistemas de refrigeración y los intercambiadores de calor son susceptibles a la corrosión resultante de las altas temperaturas, las condiciones de funcionamiento variables y los productos químicos agresivos que se utilizan en los procesos tecnológicos. Entre los problemas más comunes, se encuentran la corrosión por erosión, causada por el rápido flujo de fluidos, la corrosión microbiana, asociada al crecimiento bacteriano, y la corrosión por vibración, que debilita los componentes metálicos bajo tensiones mecánicas y ambientales. La selección adecuada de los materiales, el control periódico de la composición del agua y la limpieza cíclica de los sistemas son medidas preventivas clave.
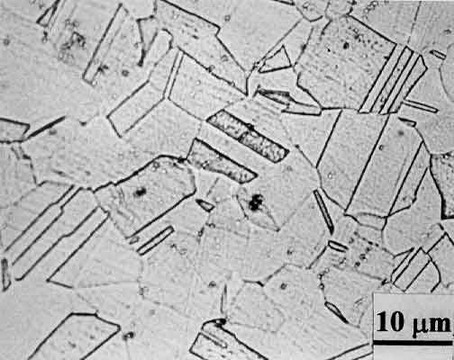
Efectos de la corrosión en la industria del petróleo y el gas
La corrosión en el sector del petróleo y el gas tiene graves consecuencias económicas, medioambientales y operativas. La degradación de las infraestructuras provoca paradas imprevistas, mayores costes de mantenimiento y riesgos para la seguridad humana y medioambiental.
Aumento de los costes de explotación y mantenimiento
La corrosión es uno de los principales factores que afectan a los costes de explotación en la industria del petróleo y el gas. La reparación de tuberías dañadas, la sustitución de componentes corroídos y la implantación de sistemas de protección contra la corrosión generan enormes gastos. Además, las inspecciones frecuentes y la supervisión del estado de la infraestructura requieren importantes desembolsos financieros. En todo el mundo, los costes anuales relacionados con la corrosión en esta industria alcanzan los miles de millones de dólares.
La corrosión progresiva puede provocar fallos en los equipos, fugas y daños en las tuberías y los depósitos, lo que obliga a detener la producción. Las interrupciones no solo reducen la eficiencia operativa, sino que también generan pérdidas financieras adicionales relacionadas con las reparaciones y los retrasos en las entregas. En casos extremos, la corrosión puede provocar la paralización total de la infraestructura, lo que resulta especialmente problemático en instalaciones en alta mar y pozos en aguas profundas.
La corrosión de las infraestructuras de petróleo y gas puede provocar fallos catastróficos, como roturas de tuberías, vertidos inflamables y explosiones, que amenazan directamente la vida y la salud de los trabajadores y las comunidades circundantes. Las fugas de gas o petróleo pueden provocar incendios y, en casos extremos, explosiones en las plataformas petrolíferas o las plantas de refinado. La prevención y el control adecuados de la corrosión son fundamentales para minimizar el riesgo de accidentes.
Impacto medioambiental
La corrosión que provoca vertidos de petróleo, gas o productos químicos tiene efectos catastróficos en los ecosistemas acuáticos y terrestres. La filtración de estas sustancias en el suelo y las aguas subterráneas provoca una contaminación que puede persistir durante décadas. Los vertidos de petróleo en los océanos provocan enormes pérdidas en las poblaciones marinas y la destrucción de los hábitats costeros. Los incidentes medioambientales derivados de accidentes por corrosión suelen acarrear daños multimillonarios y sanciones para las empresas responsables de los vertidos.
Uno de los casos más notables de corrosión que provocó un desastre medioambiental fue el vertido de petróleo de Prudhoe Bay, en Alaska, en 2006. El oleoducto de transporte de petróleo se perforó como consecuencia de la corrosión interna causada por la acumulación de sedimentos y un control insuficiente de los inhibidores de corrosión. Debido a los daños sufridos por la infraestructura, se vertieron más de 200 000 galones de petróleo en la tundra ártica que contaminaron una superficie de varias hectáreas.
El vertido tuvo un impacto catastrófico en el ecosistema local: destruyó el hábitat animal y provocó consecuencias ecológicas a largo plazo. Fue necesaria una costosa operación de descontaminación, y la empresa que gestionaba la infraestructura se vio afectada por sanciones económicas y obligada a realizar mejoras en la infraestructura.
Estrategias para minimizar y prevenir la corrosión
La corrosión en la industria del petróleo y el gas es inevitable, pero puede controlarse y mitigarse eficazmente mediante estrategias de protección adecuadas. Una gestión eficaz del riesgo de corrosión no sólo prolonga la vida útil de las infraestructuras, sino que también reduce los costes de explotación y el riesgo de averías.
CathProtección catódicaodic protection
Uno de los métodos más eficaces para proteger los metales contra la corrosión es la protección catódica, que se utiliza principalmente en tuberías, depósitos y estructuras subterráneas y marinas. Consiste en la aplicación de corriente eléctrica o ánodos activos para reducir el potencial electroquímico del metal protegido, de forma que se inhibe el proceso de corrosión.
Existen dos tipos principales de protección catódica:
- Protección galvánica (mediante ánodos de sacrificio): utiliza metales con un potencial electroquímico inferior, como el zinc, el magnesio o el aluminio, que sufren un desgaste controlado y protegen así el material estructural real.
- Protección catódica por corriente impresa (PCCI): consiste en conectar una fuente de corriente continua a la estructura que se desea proteger, lo que evita la corrosión mediante el suministro controlado de electrones.
Los sistemas de protección catódica son esenciales en las tuberías de transmisión, las estructuras marinas y los tanques de almacenamiento, donde la corrosión es especialmente intensa.
Aplicación de los inhibidores de la corrosión
Los inhibidores de la corrosión son productos químicos especiales que se añaden al medio de trabajo para ralentizar o inhibir completamente las reacciones de corrosión. Actúan formando una capa protectora en la superficie del metal o modificando las propiedades corrosivas del medio.
La división de los inhibidores de corrosión incluye:
- Inhibidores anódicos: reducen la velocidad de la reacción de oxidación del metal.
- Inhibidores catódicos: reducen la velocidad de la reacción de reducción del oxígeno o del hidrógeno.
- Inhibidores mixtos: actúan simultáneamente sobre el ánodo y el cátodo y ralentizan todo el proceso electroquímico.
Los inhibidores de corrosión se utilizan ampliamente en la industria del petróleo y el gas, especialmente en tuberías, sistemas de transmisión de agua y equipos de perforación, donde es difícil aplicar la protección mecánica o catódica.
Selección de materiales resistentes y revestimientos protectores
La selección adecuada de los materiales es clave para reducir el riesgo de corrosión. Los entornos con alta agresividad química utilizan aceros inoxidables, aleaciones de níquel, aceros aleados de alta resistencia y titanio, que presentan una mayor resistencia a la corrosión.
Los revestimientos anticorrosión proporcionan una protección adicional, ya que actúan como barrera entre el metal y el medio agresivo. Entre las soluciones más utilizadas, se encuentran:
- Revestimientos epoxídicos y de poliuretano: utilizados en tuberías y depósitos.
- Recubrimientos protectores metálicos (por ejemplo, zinc, aluminio): proporcionan protección catódica durante largos periodos de tiempo.
- Barreras protectoras cerámicas y compuestas: se utilizan en entornos extremos, como plataformas petrolíferas e instalaciones de refinerías.
Causas de la corrosión en la industria del petróleo y el gas – resumen
La corrosión en la industria del petróleo y el gas genera costes elevados, riesgos para la seguridad y daños medioambientales. La protección eficaz de las infraestructuras exige comprender los mecanismos de corrosión y aplicar estrategias de prevención adecuadas, como la protección catódica, los inhibidores de corrosión, los revestimientos protectores y la vigilancia periódica.
La prevención de la corrosión es crítica para aumentar la longevidad de las infraestructuras y minimizar el riesgo de fallos. Las tecnologías modernas permiten tener un control cada vez más eficaz de este proceso, lo cual es importante dados los crecientes requisitos operativos y medioambientales.
Este artículo está basado en el libro Metallurgy and Corrosion Control in Oil and Gas Production de Robert Heidersbach.