Leghe resistenti alla corrosione nell’industria petrolifera
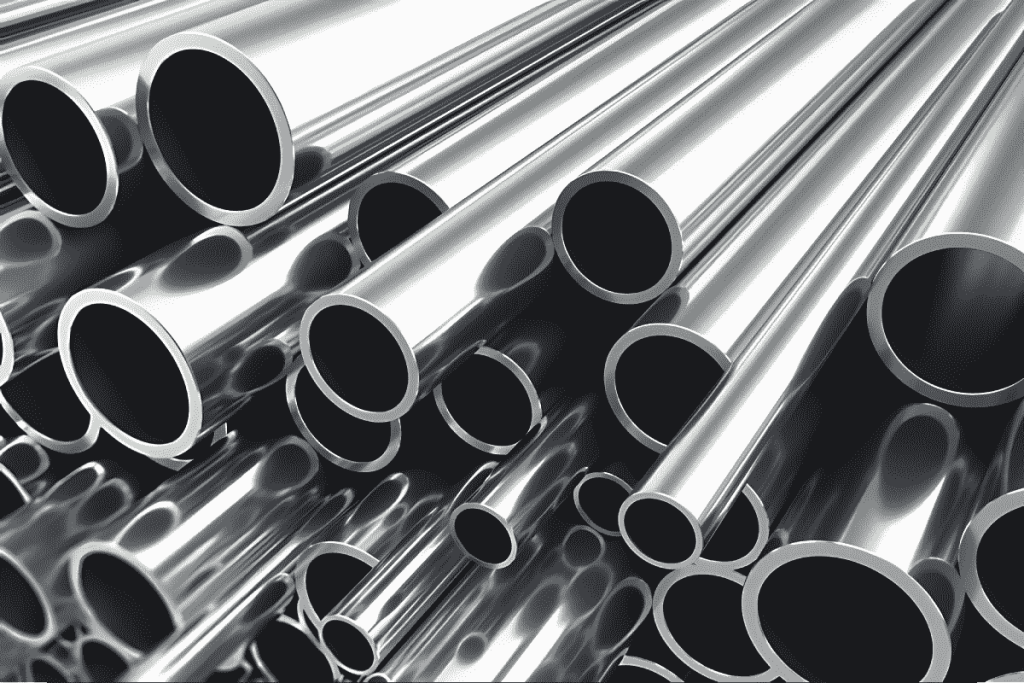
Indice
L’industria petrolifera e del gas richiede materiali in grado di resistere a condizioni operative estreme come alte pressioni, ambienti chimici aggressivi e temperature variabili. La scelta dei materiali giusti per condutture, serbatoi o installazioni offshore è critica per la sicurezza, la durata e i costi operativi dell’infrastruttura.
L’acciaio al carbonio e le leghe resistenti alla corrosione sono tra i materiali più utilizzati in questo settore. L’acciaio al carbonio, grazie alla sua elevata resistenza meccanica e al costo relativamente basso, è ampiamente utilizzato nella costruzione di condutture e strutture di supporto. Tuttavia, la sua suscettibilità alla corrosione in ambienti aggressivi rende necessario l’utilizzo di leghe resistenti alla corrosione come l’acciaio inossidabile, il nichel o il titanio in molte applicazioni.
In questo articolo verranno discusse le proprietà dell’acciaio al carbonio e delle leghe resistenti alla corrosione, i loro vantaggi e limiti e le loro principali differenze. Questa analisi consentirà di comprendere meglio le condizioni in cui un determinato materiale è più efficace e le tendenze nello sviluppo di nuove tecnologie dei materiali.
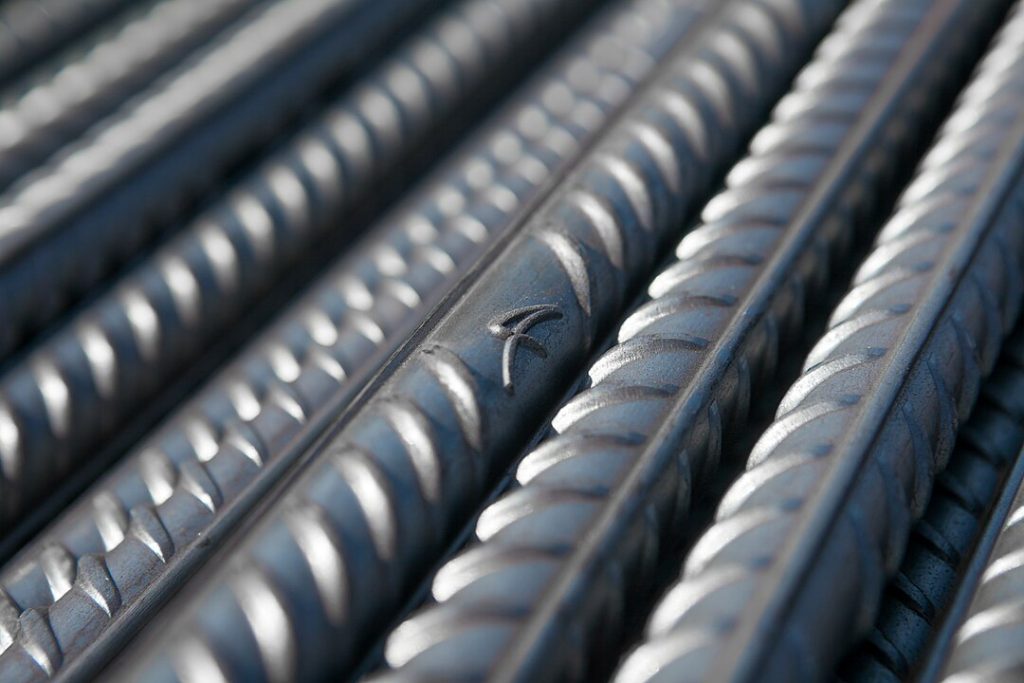
Acciaio al carbonio – proprietà e applicazioni
L’acciaio al carbonio è una lega di ferro e carbonio, con un contenuto di carbonio solitamente non superiore al 2%. A seconda della quantità di carbonio, si distinguono acciai a basso carbonio, a medio carbonio e ad alto carbonio. L’industria petrolifera utilizza principalmente acciai a basso tenore di carbonio, che hanno una buona saldabilità e duttilità, ma sono più suscettibili alla corrosione rispetto alle leghe con un contenuto più elevato di additivi protettivi di lega.
L’acciaio al carbonio è ampiamente utilizzato nell’industria petrolifera soprattutto per il suo rapporto prezzo-resistenza. I suoi vantaggi principali sono: il basso prezzo (l’acciaio al carbonio è molto più economico da produrre rispetto alle leghe specializzate resistenti alla corrosione), la buona resistenza meccanica che ne consente l’utilizzo in strutture sottoposte a carichi pesanti, e la facile reperibilità e lavorazione (la possibilità di una produzione di massa e la facilità di saldatura e formatura lo rendono ampiamente utilizzato nella costruzione di condutture e serbatoi di stoccaggio).
Nonostante questi vantaggi, l’acciaio al carbonio presenta una limitata resistenza alla corrosione, soprattutto se esposto all’acqua di mare, agli acidi e ai gas corrosivi. In ambienti ricchi di idrogeno solforato, la corrosione dei solfuri può causare gravi danni, con conseguente infragilimento da idrogeno e fessurazione del materiale. Questo problema costringe all’uso di metodi di protezione aggiuntivi, come rivestimenti anticorrosione, inibitori di corrosione e protezione catodica, che a loro volta aumentano i costi operativi.
Leghe resistenti alla corrosione – tipi e caratteristiche
Acciai inossidabili
Gli acciai inossidabili sono leghe di ferro, cromo e spesso nichel e molibdeno, che mostrano un’elevata resistenza alla corrosione grazie alla formazione di uno strato protettivo di ossidi di cromo sulla superficie del metallo. Questo strato impedisce l’ulteriore degradazione del materiale, rendendo gli acciai inossidabili adatti all’uso in ambienti chimici aggressivi, ad alte temperature e in condizioni di esposizione all’acqua di mare. L’acciaio inossidabile è utilizzato in:
- Sistemi di trasmissione in ambienti marini dove l’acqua contiene cloruri che accelerano la corrosione;
- Sistemi industriali ad alta temperatura dove l’acciaio al carbonio tradizionale potrebbe degradarsi;
- Serbatoi e sistemi di raffineria esposti a sostanze chimiche aggressive.
L’ampia applicazione degli acciai inossidabili nell’industria petrolifera è dovuta principalmente alla loro versatilità e alle favorevoli proprietà meccaniche. Vengono utilizzati in tubazioni di trasmissione, serbatoi di stoccaggio e apparecchiature utilizzate nei processi di raffinazione dove il contatto con sostanze corrosive è inevitabile.
In ambiente marino, gli acciai inossidabili sono spesso il materiale da costruzione preferito perché resistono ai cloruri, che accelerano la corrosione per vaiolatura. Nei sistemi ad alta temperatura, come gli scambiatori di calore e i forni di raffineria, gli acciai inossidabili mantengono stabilità e resistenza, consentendo di utilizzarli per lunghi periodi di tempo senza il rischio di indebolire la struttura metallica.
Nonostante i loro numerosi vantaggi, gli acciai inossidabili possono essere soggetti a crepe da corrosione sotto sforzo e corrosione per vaiolatura, soprattutto in presenza di ioni cloruro aggressivi; pertanto, in condizioni industriali estreme, si ricorre spesso a una protezione aggiuntiva, come inibitori della corrosione o rivestimenti protettivi, per prolungare ulteriormente la vita del materiale.
Leghe di nichel e titanio
Le leghe di nichel e titanio sono tra i più avanzati materiali resistenti alla corrosione da utilizzare nelle condizioni operative più difficili. Le loro esclusive proprietà chimiche e meccaniche ne consentono l’impiego in installazioni che operano a temperature estreme, in ambienti acidi e in condizioni di alta pressione.
Le leghe di nichel, come l’Inconel, mostrano un’eccezionale resistenza al solfuro di idrogeno (H₂S), agli acidi e alle alte temperature, rendendole ideali per applicazioni in pozzi profondi e sistemi di raffinazione. Grazie alla loro struttura metallurgica, resistono anche alla corrosione da sforzo, prevenendo crepe e guasti nei sistemi di acque profonde.
Il titanio e le sue leghe si distinguono per la loro estremamente elevata resistenza alla corrosione in acqua di mare, che li rende adatti all’uso in strutture offshore, piattaforme petrolifere e condutture sottomarine. La loro bassa densità rispetto ad altri metalli permette di costruire strutture leggere ma robuste, che possono operare in condizioni estreme per molti anni senza manutenzione.
Uno dei principali limiti dell’utilizzo delle leghe di nichel e titanio è il loro costo elevato, che spesso ne limita l’uso solo alle applicazioni più impegnative. Per questo motivo, spesso si ricorre a soluzioni ibride, combinando componenti in leghe resistenti alla corrosione con materiali più economici, come l’acciaio al carbonio, che vengono ulteriormente protetti dal degrado.
Nonostante il prezzo elevato delle leghe di nichel e titanio, la loro affidabilità e le minime esigenze di manutenzione le rendono sostituibili in aree in cui un guasto potrebbe portare a conseguenze ambientali ed economiche catastrofiche.
La scelta tra acciai inossidabili e leghe di nichel e titanio dipende principalmente dalle condizioni ambientali e dalle specificità dell’applicazione. Gli acciai inossidabili offrono un buon equilibrio tra prezzo e resistenza alla corrosione, mentre le leghe di nichel e titanio garantiscono la massima protezione anche negli ambienti più estremi, ma a costi operativi molto più elevati. L’industria petrolifera cerca di ottimizzare l’uso di questi materiali, combinando i loro vantaggi per massimizzare la durata e l’efficienza delle infrastrutture.
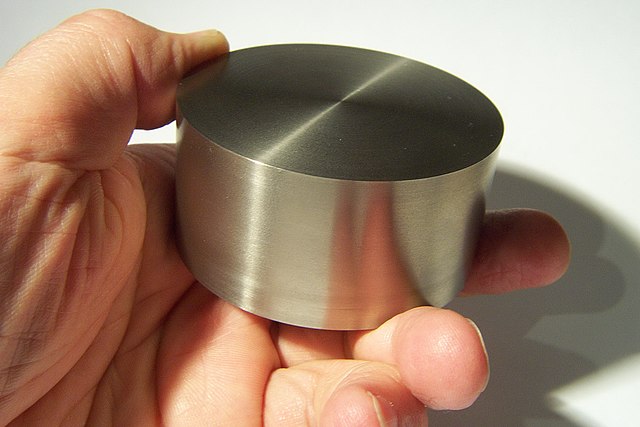
Confronto tra acciaio al carbonio e leghe resistenti alla corrosione
La scelta del materiale giusto nell’industria petrolifera e del gas dipende da molti fattori, come la resistenza alla corrosione, la resistenza meccanica, i costi di produzione e manutenzione e le condizioni operative. Nonostante la sua popolarità, l’acciaio al carbonio non è sempre l’opzione migliore, soprattutto in ambienti chimicamente aggressivi dove sono necessari materiali più resistenti alla degradazione.
La differenza principale tra l’acciaio al carbonio e le leghe resistenti alla corrosione è la loro capacità di resistere a condizioni operative difficili. L’acciaio al carbonio, pur essendo economico e ampiamente disponibile, richiede una protezione aggiuntiva per evitare che si degradi rapidamente. Al contrario, le leghe resistenti alla corrosione, come l’acciaio inossidabile e le leghe di nichel, presentano una protezione naturale contro gli agenti corrosivi, prolungando in modo significativo la loro durata e riducendo la manutenzione.
Resistenza alla corrosione in ambienti diversi
Uno dei fattori chiave nella scelta di un materiale è la sua resistenza alla corrosione in un particolare ambiente operativo. L’acciaio al carbonio mostra un’elevata suscettibilità alla corrosione in presenza di umidità, ossigeno, idrogeno solforato (H₂S) e anidride carbonica (CO₂). Soprattutto nelle condutture interrate e nelle installazioni offshore, dove il contatto con l’acqua di mare e i sali minerali è inevitabile, sono necessari metodi di protezione aggiuntivi come rivestimenti protettivi, inibitori di corrosione o protezione catodica.
Gli acciai inossidabili, il nichel e le leghe di titanio presentano una resistenza alla corrosione molto più elevata perché formano strati protettivi naturali che impediscono che si verifichino ulteriori danni alla superficie del metallo. Le leghe di nichel sono particolarmente efficaci in ambienti acidi, mentre il titanio si dimostra ottimo nelle installazioni marine dove l’intensa esposizione all’acqua di mare potrebbe degradare rapidamente l’acciaio al carbonio.
Resistenza meccanica e durata in condizioni operative
I materiali utilizzati nell’industria petrolifera devono avere un’adeguata resistenza meccanica oltre alla resistenza alla corrosione. L’acciaio al carbonio offre un’elevata resistenza ai carichi statici e dinamici, per cui viene spesso utilizzato nelle condutture di trasmissione e nelle strutture di supporto. Tuttavia, in ambienti estremi, come i pozzi in acque profonde o le installazioni soggette a temperature e pressioni elevate, può essere soggetto a corrosione da stress e a cricche da corrosione, limitandone la durata.
Le leghe resistenti alla corrosione, in particolare quelle di nichel e titanio, mantengono le loro proprietà anche in condizioni estremamente difficili. Sono resistenti alle alte temperature, all’idrogeno solforato e agli agenti chimici aggressivi, e quindi durano molto più a lungo del tradizionale acciaio al carbonio. La loro resistenza meccanica è inoltre superiore, consentendo l’utilizzo di pareti di condutture e componenti strutturali più sottili senza il rischio di indebolire la struttura.
Costi di produzione e manutenzione
Il costo dei materiali gioca un ruolo fondamentale nelle decisioni di ingegneria delle infrastrutture petrolifere. L’acciaio al carbonio è relativamente economico da produrre, il che lo rende ampiamente utilizzato nelle condutture e nei serbatoi di stoccaggio. Tuttavia, la sua suscettibilità alla corrosione richiede una protezione aggiuntiva, che genera costi associati a manutenzione, riparazione e ispezione.
Sebbene le leghe resistenti alla corrosione siano molto più costose da produrre, offrono costi operativi più bassi perché non richiedono ispezioni frequenti e costose misure preventive. Il loro utilizzo può far risparmiare denaro nel lungo periodo, soprattutto negli impianti che operano in condizioni estreme con un elevato rischio di guasti e degrado dei materiali.
Esempi di applicazioni nell’industria petrolifera
In pratica, la scelta del materiale dipende dalle specificità dell’applicazione. L’acciaio al carbonio C con protezioni aggiuntive è più spesso utilizzato nelle condutture onshore e sotterranee perché, in queste condizioni, il rischio di corrosione può essere efficacemente controllato con rivestimenti protettivi e protezione catodica.
Nelle installazioni offshore, dove le condizioni sono molto più aggressive, sono più comunemente utilizzati gli acciai inossidabili e le leghe di nichel e titanio. Questi materiali possono funzionare per decenni senza costose riparazioni. Soprattutto nei pozzi profondi e nelle condutture che trasportano sostanze chimiche aggressive, i materiali con una maggiore resistenza sono necessari per l’affidabilità delle infrastrutture.
Applicazione pratica di entrambi i gruppi di materiali
La scelta tra acciaio al carbonio e leghe resistenti alla corrosione dipende dalle condizioni operative e dai requisiti di durata e affidabilità delle infrastrutture. Entrambi i tipi di materiali sono ampiamente utilizzati nell’industria petrolifera, ma la loro efficacia dipende dall’ambiente specifico in cui vengono impiegati.
Uso dell’acciaio al carbonio in condutture e serbatoi
L’acciaio al carbonio è il materiale da costruzione più utilizzato nell’industria petrolifera, soprattutto grazie alla sua resistenza meccanica e al prezzo contenuto. Viene utilizzato principalmente nella costruzione di oleodotti che trasportano petrolio greggio e gas naturale, nonché in cisterne di stoccaggio e strutture di supporto.
L’acciaio al carbonio si comporta bene nelle condutture terrestri perché la sua suscettibilità alla corrosione può essere controllata con protezione catodica, rivestimenti anticorrosione e inibitori della corrosione. Le installazioni sotterranee utilizzano rivestimenti isolanti in polietilene o epossidici per ridurre il contatto del metallo con l’umidità e il terreno.
L’acciaio al carbonio nei serbatoi di prodotti petroliferi viene protetto con rivestimenti protettivi e monitorato regolarmente per verificare l’eventuale perdita di materiale. Negli ambienti in cui sono presenti sostanze chimiche aggressive, è necessario applicare una protezione aggiuntiva o leghe più resistenti alla corrosione nelle aree critiche della struttura.
Leghe resistenti alla corrosione in impianti offshore e ambienti acidi
Negli ambienti in cui l’acciaio al carbonio si degrada rapidamente, vengono utilizzati acciai inossidabili e leghe di nichel e titanio . Questi materiali sono altamente resistenti alla corrosione e a temperature e pressioni estreme. Esempi di tali ambienti sono le piattaforme di perforazione, le condutture sottomarine e le installazioni che trasportano sostanze chimiche aggressive.
Sulle piattaforme offshore, gli acciai inossidabili sono utilizzati nei sistemi di tubazioni e nelle strutture di supporto esposte all’acqua di mare e a temperature variabili. Gli acciai inossidabili contenenti molibdeno e nichel, che proteggono il materiale dalla vaiolatura e dalla tensocorrosione, si comportano particolarmente bene in queste condizioni.
Le condutture offshore utilizzano spesso leghe di titanio, caratterizzate dalla resistenza all’acqua di mare e da un basso peso morto, che ne facilita l’installazione e il trasporto. Grazie alla loro durata, le condutture in titanio possono essere utilizzate per decenni senza bisogno di grandi interventi di manutenzione.
L’acciaio al carbonio tradizionale si degrada rapidamente per corrosione da solfuro e biossido in ambienti acidi, dove sono presenti H₂S e CO₂. In questi casi, le leghe di nichel come l’Inconel sono utilizzate per proteggere dagli agenti chimici aggressivi e resistere alle cricche da tensocorrosione.
Uso di materiali ibridi
A causa delle differenze di costo e proprietà, nella pratica ingegneristica si ricorre spesso a soluzioni ibride. Queste prevedono la combinazione di acciaio al carbonio con materiali resistenti alla corrosione nelle aree più vulnerabili al degrado.
Negli oleodotti si possono trovare sistemi in cui l’interno dei tubi è rivestito con uno strato di lega resistente alla corrosione, mentre la struttura esterna rimane in acciaio al carbonio. Questo approccio consente di ridurre i costi, garantendo al contempo un’elevata durata dei componenti esposti a sostanze aggressive.
Analogamente, i serbatoi di stoccaggio utilizzano rivestimenti in lega di nichel e titanio nei punti di contatto con le sostanze chimiche, mentre gli altri componenti strutturali sono realizzati in acciaio al carbonio. In questo modo si ottiene un design durevole ma economicamente vantaggioso.
Leghe resistenti alla corrosione nell’industria petrolifera – riassunto
La scelta dei materiali nell’industria petrolifera influisce sulla durata delle infrastrutture, sulla sicurezza e sui costi operativi. L’acciaio al carbonio, pur essendo economico e ampiamente utilizzato, richiede una protezione aggiuntiva contro la corrosione. Le leghe resistenti alla corrosione, come gli acciai inossidabili, al nichel e al titanio, offrono una maggiore durata, ma hanno un costo più elevato.
L’industria petrolifera sta sviluppando rivestimenti moderni, sistemi di monitoraggio e nuove leghe metalliche per migliorare la resistenza alla corrosione e ottimizzare i costi. Sempre più spesso vengono utilizzate soluzioni ibride che combinano i vantaggi economici dell’acciaio al carbonio con la durata delle leghe resistenti alla corrosione.
L’articolo si basa sul libro “Metallurgy and Corrosion Control in Oil and Gas Production” di Robert Heidersbach.