Stopy odporne na korozję w przemyśle naftowym
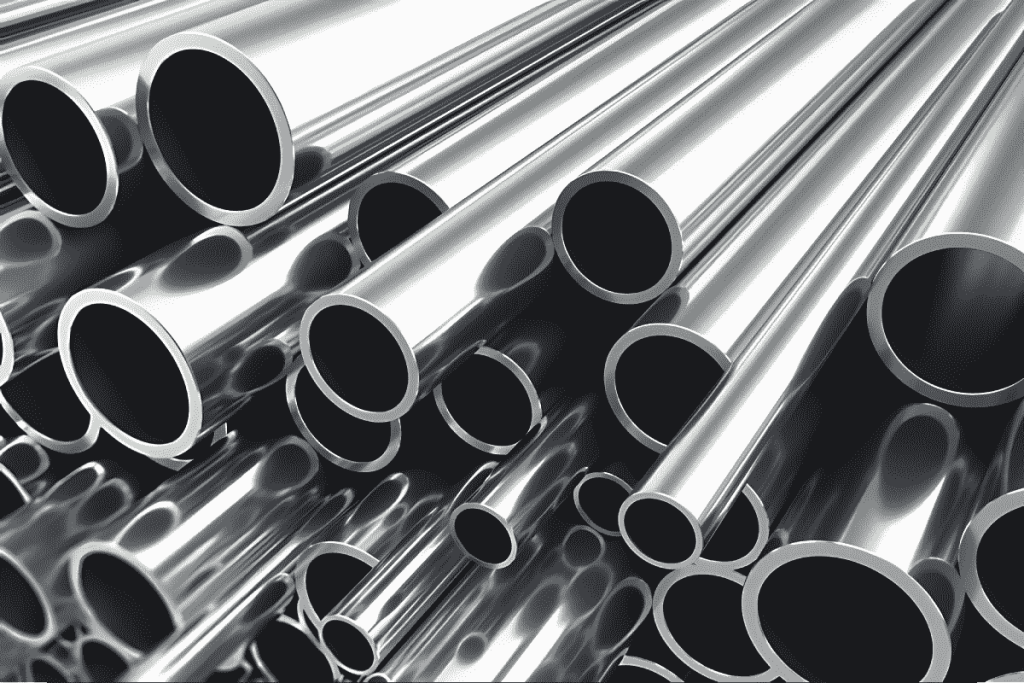
Spis treści
Przemysł naftowy i gazowy wymaga zastosowania materiałów, które są w stanie wytrzymać ekstremalne warunki eksploatacyjne, takie jak wysokie ciśnienia, agresywne środowiska chemiczne oraz zmienne temperatury. Wybór odpowiednich materiałów do budowy rurociągów, zbiorników czy instalacji offshore ma kluczowe znaczenie dla bezpieczeństwa, trwałości oraz kosztów eksploatacji infrastruktury.
Stal węglowa i stopy odporne na korozję należą do najczęściej stosowanych materiałów w tym sektorze. Stal węglowa, ze względu na wysoką wytrzymałość mechaniczną i relatywnie niski koszt, jest szeroko wykorzystywana w budowie rurociągów i konstrukcji wsporczych. Jednak jej podatność na korozję w agresywnych środowiskach sprawia, że w wielu zastosowaniach konieczne jest stosowanie stopów odpornych na korozję, takich jak stale nierdzewne, stopy niklu czy tytanu.
W tym artykule zostaną omówione właściwości stali węglowej oraz stopów odpornych na korozję, ich zalety i ograniczenia, a także kluczowe różnice między nimi. Analiza ta pozwoli lepiej zrozumieć, w jakich warunkach dany materiał jest najbardziej efektywny oraz jakie są trendy w rozwoju nowych technologii materiałowych.
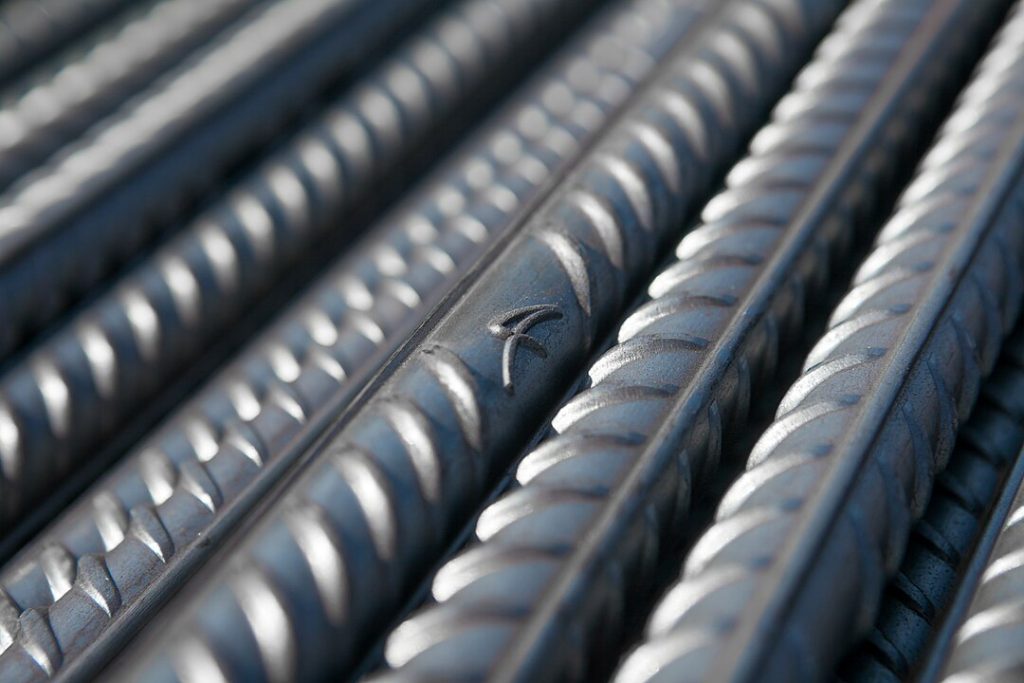
Stal węglowa – właściwości i zastosowanie
Stal węglowa to stop żelaza i węgla, w którym zawartość węgla wynosi zazwyczaj do 2%. W zależności od ilości węgla wyróżnia się stale niskowęglowe, średniowęglowe i wysokowęglowe. W przemyśle naftowym stosuje się głównie stale niskowęglowe, które charakteryzują się dobrą spawalnością i plastycznością, ale są bardziej podatne na korozję niż stopy o podwyższonej zawartości stopowych dodatków ochronnych.
Stal węglowa jest powszechnie stosowana w przemyśle naftowym głównie ze względu na stosunek ceny do wytrzymałości. Jej kluczowe zalety to: niska cena – stal węglowa jest znacznie tańsza w produkcji niż specjalistyczne stopy odporne na korozję, dobra wytrzymałość mechaniczna – umożliwia stosowanie jej w konstrukcjach narażonych na duże obciążenia oraz łatwa dostępność i przetwarzanie – możliwość masowej produkcji oraz łatwość spawania i formowania sprawiają, że jest szeroko wykorzystywana w budowie rurociągów i zbiorników magazynowych.
Mimo tych zalet stal węglowa wykazuje ograniczoną odporność na korozję, szczególnie w kontaktach z wodą morską, kwasami i gazami korozyjnymi. W środowiskach bogatych w siarkowodór może dochodzić do poważnych uszkodzeń wynikających z korozji siarczkowej, prowadzącej do kruchości wodorowej i pękania materiału. Problem ten wymusza stosowanie dodatkowych metod ochrony, takich jak powłoki antykorozyjne, inhibitory korozji oraz ochrona katodowa, co z kolei zwiększa koszty eksploatacyjne.
Stopy odporne na korozję – rodzaje i charakterystyka
Stale nierdzewne
Stale nierdzewne to stopy żelaza, chromu oraz często niklu i molibdenu, które wykazują wysoką odporność na korozję dzięki tworzeniu ochronnej warstwy tlenków chromu na powierzchni metalu. Warstwa ta zapobiega dalszej degradacji materiału, co sprawia, że stale nierdzewne mogą być eksploatowane w agresywnych środowiskach chemicznych, wysokich temperaturach oraz w warunkach narażonych na działanie wody morskiej. Stal nierdzewna wykorzystywana jest w:
- Instalacjach przesyłowych w środowisku morskim, gdzie woda zawiera chlorki przyspieszające korozję.
- Przemysłowych systemach wysokotemperaturowych, gdzie tradycyjna stal węglowa mogłaby ulec degradacji.
- Zbiornikach i instalacjach rafineryjnych, które są narażone na działanie agresywnych substancji chemicznych.
Szerokie zastosowanie stali nierdzewnych w przemyśle naftowym wynika przede wszystkim z ich wszechstronności oraz korzystnych właściwości mechanicznych. Znajdują one zastosowanie w rurociągach przesyłowych, zbiornikach magazynowych oraz aparaturze wykorzystywanej w procesach rafineryjnych, gdzie kontakt z substancjami korozyjnymi jest nieunikniony.
W środowisku morskim stale nierdzewne są często wybieranym materiałem konstrukcyjnym ze względu na ich odporność na chlorki, które przyspieszają korozję wżerową. W systemach wysokotemperaturowych, takich jak wymienniki ciepła czy piece rafineryjne, stale nierdzewne zachowują stabilność i wytrzymałość, co pozwala na ich długotrwałą eksploatację bez ryzyka osłabienia struktury metalu.
Mimo wielu zalet stale nierdzewne mogą być podatne na korozję naprężeniową oraz korozję wżerową, szczególnie w obecności agresywnych jonów chlorkowych. Dlatego w ekstremalnych warunkach przemysłowych często stosuje się dodatkowe zabezpieczenia, takie jak inhibitory korozji czy powłoki ochronne, które dodatkowo wydłużają żywotność materiału.
Stopy niklu i tytanu
Stopy niklu i tytanu należą do najbardziej zaawansowanych materiałów odpornych na korozję, które znajdują zastosowanie w najbardziej wymagających warunkach eksploatacyjnych. Ich unikalne właściwości chemiczne i mechaniczne sprawiają, że są one wykorzystywane w instalacjach pracujących w ekstremalnych temperaturach, środowiskach kwaśnych oraz w warunkach wysokiego ciśnienia.
Stopy niklu, takie jak Inconel, wykazują wyjątkową odporność na działanie siarkowodoru (H₂S), kwasów oraz wysokich temperatur, co czyni je idealnym wyborem do zastosowań w głębokich odwiertach oraz w systemach rafineryjnych. Dzięki swojej strukturze metalurgicznej są również odporne na korozję naprężeniową, co zapobiega powstawaniu pęknięć i awarii w instalacjach na dużych głębokościach.
Tytan i jego stopy wyróżniają się natomiast niezwykle wysoką odpornością na korozję w wodzie morskiej, co sprawia, że są wykorzystywane w konstrukcjach offshore, platformach wiertniczych oraz rurociągach podmorskich. Ich niska gęstość w porównaniu do innych metali pozwala na budowę lekkich, a jednocześnie wytrzymałych struktur, które mogą pracować w ekstremalnych warunkach przez wiele lat bez konieczności konserwacji.
Jednym z głównych ograniczeń stosowania stopów niklu i tytanu jest ich wysoki koszt, który często sprawia, że ich wykorzystanie jest ograniczone jedynie do najbardziej wymagających aplikacji. Z tego powodu w wielu przypadkach stosuje się hybrydowe rozwiązania, łączące elementy ze stopów odpornych na korozję z tańszymi materiałami, takimi jak stal węglowa, które są dodatkowo zabezpieczane przed degradacją.
Mimo wysokiej ceny stopów niklu i tytanu ich niezawodność oraz minimalne potrzeby konserwacyjne sprawiają, że są one niezastąpione w miejscach, gdzie awaria mogłaby prowadzić do katastrofalnych skutków ekologicznych i ekonomicznych.
Wybór między stalami nierdzewnymi a stopami niklu i tytanu zależy przede wszystkim od warunków środowiskowych oraz specyfiki danego zastosowania. Stale nierdzewne oferują korzystny balans między ceną a odpornością na korozję, podczas gdy stopy niklu i tytanu zapewniają maksymalną ochronę nawet w najbardziej ekstremalnych środowiskach, ale przy znacznie wyższych kosztach eksploatacji. W przemyśle naftowym dąży się do optymalizacji wykorzystania tych materiałów, łącząc ich zalety w celu osiągnięcia jak największej trwałości i efektywności infrastruktury.
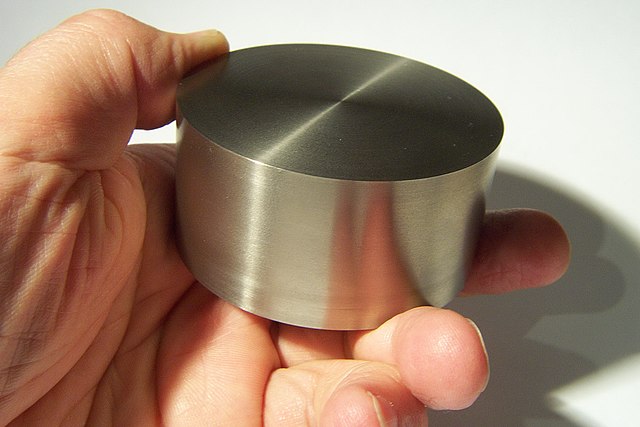
Porównanie stali węglowej i stopów odpornych na korozję
Wybór odpowiedniego materiału w przemyśle naftowym i gazowym zależy od wielu czynników, takich jak odporność na korozję, wytrzymałość mechaniczna, koszty produkcji i konserwacji oraz warunki eksploatacyjne. Stal węglowa, mimo swojej popularności, nie zawsze jest najlepszym rozwiązaniem, zwłaszcza w środowiskach agresywnych chemicznie, gdzie konieczne jest zastosowanie materiałów bardziej odpornych na degradację.
Zasadnicza różnica między stalą węglową a stopami odpornymi na korozję wynika z ich zdolności do przetrwania w trudnych warunkach eksploatacyjnych. Stal węglowa, choć tania i szeroko dostępna, wymaga dodatkowych zabezpieczeń, aby uniknąć szybkiej degradacji. W przeciwieństwie do niej stopy odporne na korozję, takie jak stale nierdzewne czy stopy niklu, cechują się naturalną ochroną przed czynnikami korozyjnymi, co znacząco wydłuża ich żywotność i ogranicza konieczność konserwacji.
Odporność na korozję w różnych środowiskach
Jednym z kluczowych czynników decydujących o wyborze materiału jest jego odporność na korozję w określonym środowisku eksploatacyjnym. Stal węglowa wykazuje dużą podatność na korozję w obecności wilgoci, tlenu, siarkowodoru (H₂S) oraz dwutlenku węgla (CO₂). W szczególności w rurociągach podziemnych oraz instalacjach offshore, gdzie kontakt z wodą morską i solami mineralnymi jest nieunikniony, konieczne jest stosowanie dodatkowych metod ochrony, takich jak powłoki ochronne, inhibitory korozji czy ochrona katodowa.
Stale nierdzewne oraz stopy niklu i tytanu wykazują znacznie wyższą odporność na korozję, ponieważ tworzą naturalne warstwy ochronne, które uniemożliwiają dalsze uszkodzenia powierzchni metalu. Stopy niklu są szczególnie skuteczne w środowiskach kwaśnych, natomiast tytan sprawdza się doskonale w instalacjach morskich, gdzie intensywne działanie wody morskiej mogłoby szybko doprowadzić do degradacji stali węglowej.
Wytrzymałość mechaniczna i trwałość w warunkach eksploatacyjnych
Oprócz odporności na korozję, materiały stosowane w przemyśle naftowym muszą charakteryzować się odpowiednią wytrzymałością mechaniczną. Stal węglowa oferuje wysoką wytrzymałość na obciążenia statyczne i dynamiczne, co sprawia, że jest często wykorzystywana w rurociągach przesyłowych oraz konstrukcjach wsporczych. Jednak w środowiskach ekstremalnych, takich jak odwierty głębinowe czy instalacje poddane działaniu wysokich temperatur i ciśnień, może być podatna na korozję naprężeniową oraz pękanie korozyjne, co ogranicza jej trwałość.
Stopy odporne na korozję, w szczególności stopy niklu i tytanu, zachowują swoje właściwości nawet w skrajnie trudnych warunkach. Są one odporne na wysokie temperatury, działanie siarkowodoru i agresywnych substancji chemicznych, co sprawia, że ich eksploatacja jest znacznie dłuższa niż w przypadku tradycyjnej stali węglowej. Ich wytrzymałość mechaniczna również jest wyższa, co pozwala na stosowanie cieńszych ścianek rurociągów i elementów konstrukcyjnych bez ryzyka osłabienia struktury.
Koszty produkcji i konserwacji
Koszt materiału odgrywa kluczową rolę w decyzjach inżynieryjnych dotyczących infrastruktury naftowej. Stal węglowa jest relatywnie tania w produkcji, co sprawia, że jest powszechnie stosowana w rurociągach i zbiornikach magazynowych. Jednak jej podatność na korozję wymaga stosowania dodatkowych zabezpieczeń, co z kolei generuje koszty związane z konserwacją, naprawami i inspekcjami.
Stopy odporne na korozję, mimo że znacznie droższe w produkcji, oferują mniejsze koszty eksploatacyjne, ponieważ nie wymagają częstych przeglądów i kosztownych działań prewencyjnych. Ich zastosowanie może w dłuższej perspektywie przynieść oszczędności, zwłaszcza w instalacjach pracujących w ekstremalnych warunkach, gdzie ryzyko awarii i degradacji materiału jest wysokie.
Przykłady zastosowań w przemyśle naftowym
W praktyce wybór materiału zależy od specyfiki danego zastosowania. W rurociągach lądowych i podziemnych najczęściej stosuje się stal węglową z dodatkowymi zabezpieczeniami, ponieważ w tych warunkach ryzyko korozji można skutecznie kontrolować za pomocą powłok ochronnych i ochrony katodowej.
W instalacjach offshore, gdzie warunki są znacznie bardziej agresywne, częściej stosuje się stale nierdzewne oraz stopy niklu i tytanu, które mogą pracować przez dekady bez konieczności kosztownych napraw. Szczególnie w głębokich odwiertach oraz rurociągach transportujących agresywne substancje chemiczne, materiały o podwyższonej odporności są niezbędne dla zapewnienia niezawodności infrastruktury.
Praktyczne zastosowanie obu grup materiałów
Wybór pomiędzy stalą węglową a stopami odpornymi na korozję zależy od warunków eksploatacyjnych oraz wymagań dotyczących trwałości i niezawodności infrastruktury. Oba typy materiałów znajdują szerokie zastosowanie w przemyśle naftowym, jednak ich efektywność jest uzależniona od specyfiki środowiska, w którym są wykorzystywane.
Zastosowanie stali węglowej w rurociągach i zbiornikach
Stal węglowa jest najczęściej stosowanym materiałem konstrukcyjnym w przemyśle naftowym, głównie ze względu na swoją wytrzymałość mechaniczną i niską cenę. Wykorzystuje się ją przede wszystkim do budowy rurociągów transportujących ropę naftową i gaz ziemny, a także w zbiornikach magazynowych i konstrukcjach wsporczych.
W rurociągach lądowych stal węglowa sprawdza się dobrze, ponieważ jej podatność na korozję można kontrolować za pomocą ochrony katodowej, powłok antykorozyjnych oraz inhibitorów korozji. W instalacjach podziemnych stosuje się izolacyjne powłoki polietylenowe lub epoksydowe, które ograniczają kontakt metalu z wilgocią i glebą.
W zbiornikach na produkty naftowe stal węglowa jest zabezpieczana powłokami ochronnymi oraz regularnie monitorowana pod kątem ubytków materiału. W środowiskach, gdzie występują agresywne związki chemiczne, konieczne jest stosowanie dodatkowych zabezpieczeń lub stosowanie stopów bardziej odpornych na korozję w krytycznych miejscach konstrukcji.
Stopy odporne na korozję w instalacjach offshore i środowiskach kwaśnych
W warunkach, gdzie stal węglowa szybko ulega degradacji, stosuje się stale nierdzewne oraz stopy niklu i tytanu, które charakteryzują się wysoką odpornością na korozję oraz ekstremalne temperatury i ciśnienia. Przykładem takich środowisk są platformy wiertnicze, rurociągi podmorskie oraz instalacje transportujące agresywne chemikalia.
Na platformach wiertniczych stale nierdzewne stosowane są w systemach rurowych oraz konstrukcjach nośnych, które są narażone na działanie wody morskiej oraz zmienne temperatury. W tych warunkach szczególnie dobrze sprawdzają się stale nierdzewne zawierające molibden i nikiel, które chronią materiał przed korozją wżerową oraz naprężeniową.
W rurociągach podmorskich często stosuje się stopy tytanu, które cechują się odpornością na wodę morską oraz niską masą własną, co ułatwia ich instalację i transport. Dzięki swojej trwałości, rurociągi wykonane z tytanu mogą być eksploatowane przez dziesięciolecia bez konieczności intensywnej konserwacji.
W środowiskach kwaśnych, gdzie obecne są H₂S i CO₂, tradycyjna stal węglowa ulega szybkiej degradacji w wyniku korozji siarczkowej i dwutlenkowej. W takich przypadkach stosuje się stopy niklu, takie jak Inconel, które zapewniają ochronę przed agresywnymi związkami chemicznymi i są odporne na korozję naprężeniową.
Wykorzystanie materiałów hybrydowych
Ze względu na różnice w kosztach i właściwościach, w praktyce inżynieryjnej często stosuje się rozwiązania hybrydowe, polegające na łączeniu stali węglowej z materiałami odpornymi na korozję w miejscach najbardziej narażonych na degradację.
W rurociągach naftowych można spotkać się z systemami, w których wnętrze rur pokryte jest warstwą stopu odpornego na korozję, a zewnętrzna konstrukcja pozostaje wykonana ze stali węglowej. Takie podejście pozwala na redukcję kosztów, jednocześnie zapewniając wysoką trwałość elementów narażonych na działanie agresywnych substancji.
Podobnie w zbiornikach magazynowych stosuje się powłoki ze stopów niklu i tytanu w miejscach styku z substancjami chemicznymi, natomiast pozostałe elementy konstrukcyjne wykonane są ze stali węglowej. Dzięki temu możliwe jest uzyskanie trwałej i jednocześnie ekonomicznie opłacalnej konstrukcji.
Stopy odporne na korozję w przemyśle naftowym – podsumowanie
Wybór materiałów w przemyśle naftowym wpływa na trwałość infrastruktury, bezpieczeństwo i koszty eksploatacji. Stal węglowa, choć tania i szeroko stosowana, wymaga dodatkowej ochrony przed korozją. Stopy odporne na korozję, takie jak stale nierdzewne, niklowe i tytanowe, oferują większą trwałość, ale wiążą się z wyższymi kosztami.
Przemysł naftowy rozwija nowoczesne powłoki, systemy monitorowania i nowe stopy metali, aby zwiększyć odporność na korozję i optymalizować koszty. Coraz częściej stosuje się rozwiązania hybrydowe, łączące ekonomiczne zalety stali węglowej z trwałością stopów odpornych na korozję.
Artykuł ten powstał na podstawie książki „Metallurgy and Corrosion Control in Oil and Gas Production” autorstwa Roberta Heidersbacha.