Cause della corrosione nell’industria petrolifera e del gas
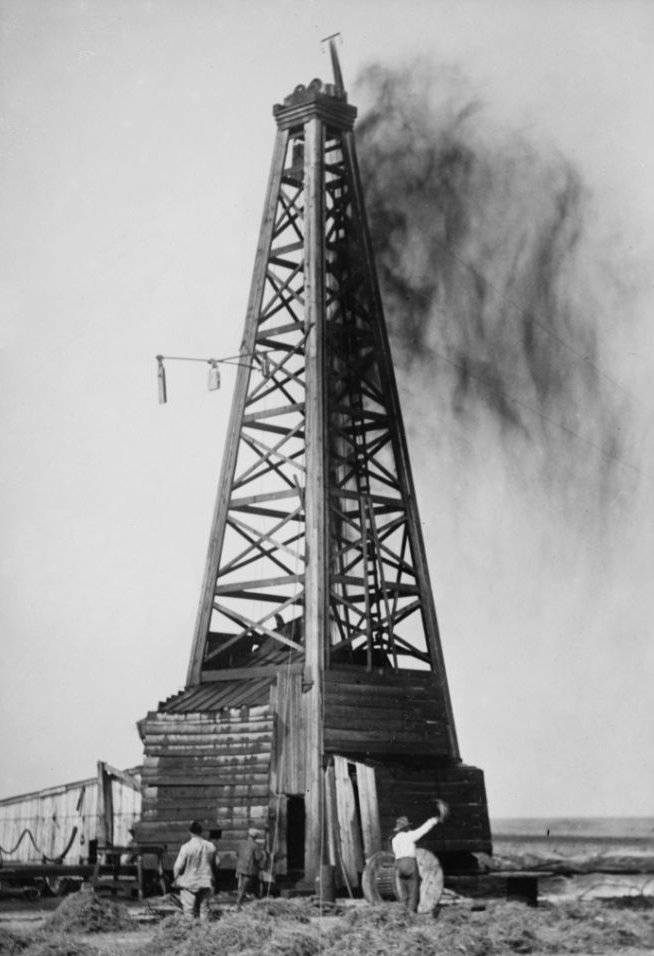
Indice
La corrosione è uno dei problemi più gravi dell’industria petrolifera e del gas, con ripercussioni sulla sicurezza e sui costi operativi. Si verifica in tutte le fasi operative, dall’estrazione al trasporto allo stoccaggio delle materie prime. Le perdite annuali legate alla corrosione nel settore sono stimate in miliardi di dollari e gli eventi di corrosione incontrollata possono portare a guasti catastrofici alle infrastrutture.
Una gestione inadeguata del rischio di corrosione può provocare quanto segue:
- Danni alle condutture e ai serbatoi di stoccaggio, con conseguente aumento del rischio di perdite ed esplosioni;
- Interruzioni della produzione ed elevati costi di riparazione;
- Degrado delle parti metalliche delle attrezzature di perforazione e raffinazione ne riduce la durata;
- Inquinamento ambientale, soprattutto nel caso di fuoriuscite di petrolio o gas.
Comprendere le cause della corrosione è fondamentale per controllarla efficacemente e prevenire gli effetti indesiderati. Questo articolo illustra i principali tipi di corrosione che si verificano nell’industria petrolifera e del gas e i fattori che la accelerano.
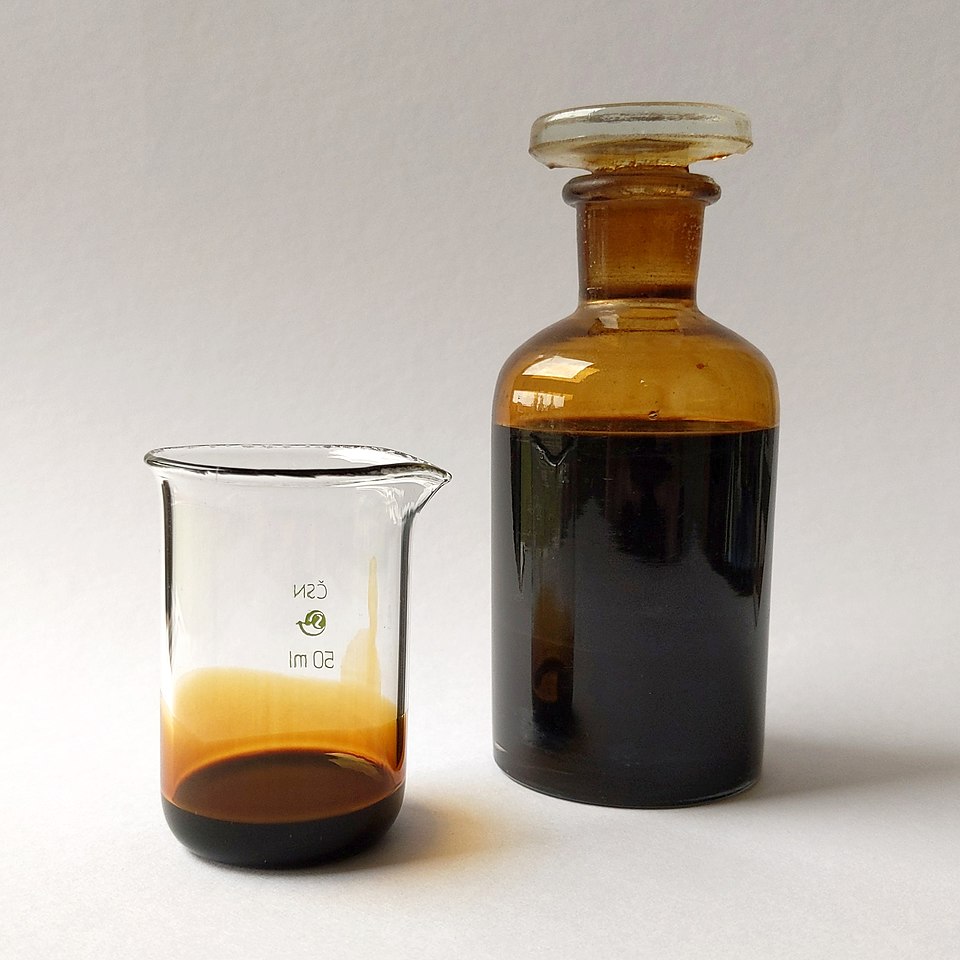
Tipi di corrosione nell’industria petrolifera e del gas
La corrosione nel settore petrolifero e del gas può assumere forme diverse a seconda delle condizioni ambientali, della composizione chimica del mezzo e delle proprietà dei materiali. Distinguere tra i diversi tipi di corrosione è fondamentale per proteggere efficacemente le infrastrutture e prolungarne la durata.
- Corrosione generale: è il tipo di corrosione più comune, in cui il metallo subisce un’ossidazione uniforme su tutta la superficie. Si verifica in presenza di ossigeno e umidità, portando alla graduale degradazione del materiale. Come risultato di questo processo, lo spessore delle pareti di tubazioni e serbatoi diminuisce, riducendone la resistenza. Sebbene questo tipo di corrosione sia relativamente facile da monitorare, richiede misure preventive sistematiche, come rivestimenti protettivi e inibitori.
- Corrosione galvanica: si verifica quando due metalli diversi sono in contatto elettrico in un ambiente conduttivo. Il metallo meno nobile (anodo) subisce un’ossidazione accelerata, mentre il metallo più nobile (catodo) rimane protetto. Questo fenomeno è particolarmente importante nei sistemi di tubazioni e nelle strutture offshore, dove è necessario unire materiali diversi. Per ridurre questo tipo di corrosione è necessario scegliere correttamente i materiali e l’isolamento elettrico tra di essi.
- Corrosione per vaiolatura: è una forma locale di corrosione in cui il metallo si degrada in punti piccoli ma profondi. Il più delle volte si verifica in presenza di ioni cloruro, che contribuiscono alla formazione di buche, indebolendo la struttura del materiale. A differenza della corrosione generale, che si distribuisce uniformemente, la corrosione per vaiolatura può portare rapidamente alla perforazione dei componenti strutturali. L’uso di materiali resistenti alla corrosione e di inibitori è fondamentale per ridurla.
- Stress Corrosion Cracking (SCC): è un processo in cui il materiale si rompe sotto l’azione simultanea di una sollecitazione meccanica e di un ambiente chimico aggressivo. Le crepe possono svilupparsi gradualmente, ma le conseguenze più gravi portano a un guasto improvviso dell’apparecchiatura. La SCC si verifica soprattutto in tubazioni e serbatoi che operano ad alta pressione e in ambienti contenenti idrogeno solforato.
- Corrosione microbica (MIC – Microbially Influenced Corrosion): si verifica a causa dell’attività di microrganismi che accelerano la degradazione del metallo producendo sostanze chimiche aggressive. Particolarmente problematica è l’attività dei batteri solfato-riduttori (SRB), che porta alla formazione di idrogeno solforato, aumentando il rischio di corrosione e infragilimento dei materiali. La lotta a questo tipo di corrosione richiede una disinfezione regolare e l’uso di biocidi.
- Corrosione per erosione: si verifica a causa di un intenso flusso di liquidi o gas, soprattutto quando il mezzo contiene particelle solide come sabbia o depositi minerali. La combinazione di fattori meccanici e chimici provoca la graduale abrasione dello strato protettivo del metallo, con conseguente accelerazione dell’usura dei componenti. Per ridurre questo tipo di corrosione si utilizzano materiali con una maggiore resistenza all’abrasione e si controllano i parametri di flusso.
Fattori chiave che accelerano la corrosione
La corrosione nell’industria petrolifera e del gas avviene sotto l’influenza di molti fattori che possono accelerare in modo significativo la degradazione del metallo. L’ambiente chimico, le condizioni fisiche e la dinamica del flusso dei fluidi esercitano un’influenza fondamentale sullo sviluppo dei processi di corrosione. Conoscere questi fattori è essenziale per prevenire efficacemente la corrosione e scegliere i metodi di protezione ottimali.
Presenza di ossigeno (O₂)
L’ossigeno è uno dei principali fattori che accelerano la corrosione, soprattutto in ambienti acquosi. Quando entra in contatto con un metallo, ne provoca l’ossidazione, portando alla formazione di prodotti di corrosione come ossidi e ruggine. Bastano piccole quantità di ossigeno possono aumentare significativamente il tasso di corrosione, soprattutto se presenti in tubazioni o serbatoi contenenti acqua o umidità. Limitare l’accesso dell’ossigeno alla superficie metallica attraverso guarnizioni, rivestimenti protettivi e l’uso di inibitori è fondamentale per ridurre questo tipo di corrosione.
Presenza di idrogeno solforato (H₂S) e anidride carbonica (CO₂)
L’idrogeno solforato (H₂S) e l’anidride carbonica (CO₂) sono i due gas corrosivi più comuni nell’industria petrolifera. Il CO₂ (“corrosione dolce”), a contatto con l’acqua, forma acido carbonico (H₂CO₃), che abbassa il pH e accelera la dissoluzione dei metalli, provocando cavità in tubazioni e serbatoi. L’H₂S (“corrosione acida”) provoca la formazione di solfuri di ferro (FeS), che può avere un effetto protettivo, ma aumenta anche il rischio di corrosione viva e infragilimento da idrogeno. L’effetto di questi gas sulla corrosione dipende dalla loro concentrazione, temperatura e pressione, rendendo necessario l’utilizzo di materiali resistenti alla CO₂ e all’H₂S in ambienti aggressivi.

Umidità e presenza di acqua
L’acqua è fondamentale nella maggior parte dei processi di corrosione perché agisce come elettrolita, consentendo il passaggio di corrente tra l’anodo e il catodo sulla superficie del metallo. A seconda della sua composizione chimica, può accelerare la corrosione in misura variabile.
- Acqua dolce: contiene ossigeno, che favorisce l’ossidazione dei metalli;
- Acqua di mare: ricca di ioni cloruro (Cl-), che intensificano la corrosione per vaiolatura;
- Acqua di giacimento: può contenere solfati, carbonati e batteri solfato-riduttori, che portano alla corrosione microbica;
La gestione del contenuto di acqua nei sistemi petroliferi comprende la sua separazione, la rimozione dei composti corrosivi e l’uso di inibitori.
Temperatura e pressione
L’alta temperatura e la pressione sono alcuni dei fattori chiave che influenzano la velocità e la natura dei processi di corrosione nell’industria petrolifera e del gas. Il loro impatto è particolarmente significativo in ambienti estremi come pozzi profondi, condotte ad alta pressione e installazioni offshore.
La temperatura influisce direttamente sulla velocità delle reazioni chimiche ed elettrochimiche che portano alla corrosione. L’aumento della temperatura accelera l’ossidazione del metallo e le reazioni con i gas corrosivi, aumentandone l’aggressività. Allo stesso tempo, essa può destabilizzare gli strati protettivi, come lo strato di ossido passivo sugli acciai inossidabili, rendendo il metallo più suscettibile alla corrosione. Le temperature elevate influiscono anche sulla solubilità dei gas in acqua: CO₂ e H₂S possono reagire più intensamente con l’acqua, formando acidi aggressivi che attaccano le superfici metalliche.
Le alte temperature possono anche portare alla rottura degli inibitori di corrosione, ovvero le sostanze utilizzate per rallentare la degradazione del metallo. Alcuni inibitori perdono le loro proprietà protettive in condizioni termiche estreme, richiedendo l’uso di sostanze chimiche più resistenti. In determinate condizioni possono verificarsi anche tipi specifici di corrosione, come la corrosione ad alta temperatura, che consiste nell’ossidazione del metallo in assenza di acqua liquida, che si verifica ad esempio nelle caldaie e negli scambiatori di calore. Un altro tipo è la corrosione da solfuri, che si verifica in ambienti ricchi di zolfo, particolarmente importante nei processi di raffinazione del petrolio.
Le temperature elevate possono anche favorire la comparsa di crepe da corrosione sotto sforzo (SCC), ovvero la formazione di fenditure nella struttura di un materiale causate dalla combinazione di sollecitazioni meccaniche e di un ambiente chimico aggressivo. Questo tipo di danno è particolarmente pericoloso perché può svilupparsi in modo impercettibile, portando a un cedimento improvviso.
La pressione influisce sull’intensità della corrosione modificando le proprietà fisico-chimiche dei gas e dei liquidi presenti nel sistema. L’alta pressione aumenta la solubilità di CO₂ e H₂S nell’acqua, rendendo il mezzo più aggressivo nei confronti dei materiali strutturali. Questi gas, combinati con l’umidità, formano acidi che accelerano la degradazione dei metalli, particolarmente problematica nei sistemi operanti ad alta pressione.
Un altro fattore importante è l’effetto dell’alta pressione sulla durata dei materiali. Nei pozzi profondi e nelle condutture di trasmissione, la pressione estrema provoca impatti chimici e meccanici più intensi sulle superfici metalliche. Ciò può indebolire la struttura del materiale e aumentare la suscettibilità alla cavitazione, ossia la formazione e il collasso di bolle di vapore, che possono danneggiare la superficie metallica attraverso impatti violenti, accelerandone il degrado.
Esempi di siti tipici esposti alla corrosione
La corrosione nell’industria petrolifera e del gas si verifica in molti componenti delle infrastrutture, soprattutto quando i metalli sono esposti ad ambienti chimici aggressivi, alta pressione e temperatura. I suoi effetti possono danneggiare condotte, serbatoi e apparecchiature di processo, causando costosi tempi di inattività e rischi per la sicurezza.
Condotte, serbatoi e sistemi di trasmissione
Le condutture e i serbatoi di stoccaggio sono tra i componenti infrastrutturali che si corrodono più frequentemente, poiché le loro pareti sono in costante contatto con un mezzo contenente acqua, CO₂, H₂S e impurità meccaniche. La corrosione interna può portare a vaiolature e perforazioni, mentre la corrosione esterna, causata da umidità, ossigeno e correnti vaganti, indebolisce la struttura del materiale. Particolarmente a rischio sono le condutture e i serbatoi sotterranei esposti a sbalzi di temperatura, che causano la condensazione e lo sviluppo della corrosione atmosferica. La prevenzione della corrosione si basa sulla protezione catodica, sull’uso di inibitori e rivestimenti protettivi.
Infrastrutture offshore e attrezzature di perforazione
Le piattaforme e le condutture di perforazione offshore operano in un ambiente estremamente aggressivo, dove l’acqua salata, le forti correnti e l’elevata umidità accelerano la corrosione. La corrosione galvanica si verifica all’interfaccia di vari metalli, che è particolarmente pericolosa, e la corrosione per erosione, che porta a danni superficiali sotto l’influenza di un forte flusso d’acqua e di particelle in sospensione. Le attrezzature di perforazione, compresi tubi e valvole, sono inoltre soggette a corrosione da sforzo e infragilimento da idrogeno, soprattutto in presenza di H₂S. Per ridurre il degrado, si utilizzano materiali resistenti alle alte pressioni, protezione anodica catodica e rivestimenti anticorrosione specializzati.
Sistemi di raffreddamento e scambiatori di calore
I sistemi di raffreddamento e gli scambiatori di calore sono soggetti a corrosione a causa di elevate temperature, condizioni operative variabili e sostanze chimiche aggressive utilizzate nei processi tecnologici. Tra i problemi più comuni vi sono la corrosione da erosione, causata dal rapido flusso del fluido, la corrosione microbica, associata alla crescita batterica, e la corrosione da vibrazione, che indebolisce i componenti metallici sotto le sollecitazioni meccaniche e ambientali. La scelta corretta dei materiali, il controllo regolare della composizione dell’acqua e la pulizia ciclica dei sistemi sono misure preventive fondamentali.
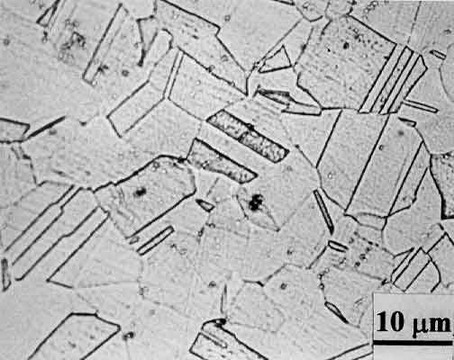
Effetti della corrosione nell’industria petrolifera e del gas
La corrosione nel settore petrolifero e del gas comporta gravi conseguenze economiche, ambientali e operative. Il degrado delle infrastrutture porta a tempi di inattività non pianificati, un aumento dei costi di manutenzione e rischi per la sicurezza umana e ambientale.
Aumento dei costi operativi e di manutenzione
La corrosione è uno dei principali fattori che incidono sui costi operativi nell’industria del petrolio e del gas. La riparazione di condotte danneggiate, la sostituzione di componenti corrosi e l’implementazione di sistemi di protezione dalla corrosione generano spese enormi. Inoltre, le frequenti ispezioni e il monitoraggio delle condizioni dell’infrastruttura richiedono un notevole esborso finanziario. A livello globale, i costi annuali legati alla corrosione in questo settore raggiungono miliardi di dollari.
La corrosione progressiva può portare a guasti alle apparecchiature, perdite e danni a tubazioni e serbatoi, con conseguente necessità di interrompere la produzione. Le interruzioni non solo riducono l’efficienza operativa, ma generano anche ulteriori perdite finanziarie legate alle riparazioni e ai ritardi nelle consegne. In casi estremi, la corrosione può causare l’arresto completo dell’infrastruttura, particolarmente problematico per gli impianti offshore e i pozzi in acque profonde.
La corrosione delle infrastrutture per il petrolio e il gas può portare a guasti catastrofici, come rotture di condotte, fuoriuscite di sostanze infiammabili ed esplosioni, che minacciano direttamente la vita e la salute dei lavoratori e delle comunità circostanti. Le perdite di gas o di petrolio possono causare incendi e, in casi estremi, esplosioni sulle piattaforme petrolifere o negli impianti di raffinazione. Un’adeguata prevenzione e controllo della corrosione è fondamentale per ridurre al minimo il rischio di incidenti.
Impatto ambientale
La corrosione che porta a fuoriuscite di petrolio, gas o sostanze chimiche ha effetti catastrofici sugli ecosistemi acquatici e terrestri. La fuoriuscita di queste sostanze nel suolo e nelle acque sotterranee provoca contaminazioni che possono persistere per decenni. Le fuoriuscite di petrolio negli oceani causano enormi perdite di esemplari di specie marine e la distruzione degli habitat costieri. Gli incidenti ambientali dovuti alla corrosione spesso comportano danni multimilionari e a sanzioni per le aziende responsabili delle fuoriuscite.
Uno dei casi più significativi di corrosione che ha portato a un disastro ambientale è stata la fuoriuscita di petrolio di Prudhoe Bay in Alaska nel 2006. L’oleodotto per il trasporto del petrolio si è perforato conseguentemente alla corrosione interna causata dall’accumulo di sedimenti e dall’insufficiente controllo degli inibitori di corrosione. A causa dei danni all’infrastruttura, oltre 200.000 galloni di petrolio sono fuoriusciti nella tundra artica, contaminando un’area di diversi ettari. La fuoriuscita ha avuto un impatto catastrofico sull’ecosistema locale, distruggendo l’habitat degli animali e portando a conseguenze ecologiche a lungo termine. È stata necessaria una costosa operazione di decontaminazione e l’azienda che gestiva l’infrastruttura è stata colpita da sanzioni finanziarie e costretta a effettuare aggiornamenti dell’infrastruttura.
Strategie per ridurre e prevenire la corrosione
La corrosione nell’industria petrolifera e del gas è inevitabile, ma può essere efficacemente controllata e mitigata attraverso adeguate strategie di protezione. Una gestione efficace del rischio di corrosione non solo allunga la vita delle infrastrutture, ma riduce anche i costi operativi e il rischio di guasti.
Protezione catodica
Uno dei metodi più efficaci per proteggere i metalli dalla corrosione è la protezione catodica, utilizzata principalmente in tubazioni, serbatoi e strutture sotterranee e offshore. Essa prevede l’applicazione di corrente elettrica o di anodi attivi per ridurre il potenziale elettrochimico del metallo protetto, in modo da inibire il processo di corrosione.
Esistono due tipi principali di protezione catodica:
- Protezione galvanica (con anodi sacrificali): utilizza metalli con un potenziale elettrochimico più basso, come zinco, magnesio o alluminio, che subiscono un’usura controllata, proteggendo così il materiale strutturale vero e proprio;
- Protezione catodica a corrente impressa (ICCP): prevede il collegamento di una sorgente di corrente continua alla struttura da proteggere, che previene la corrosione attraverso l’erogazione controllata di elettroni.
I sistemi di protezione catodica sono essenziali nelle condotte di trasmissione, nelle strutture offshore e nei serbatoi di stoccaggio, dove la corrosione è particolarmente intensa.
Applicazione degli inibitori di corrosione
Gli inibitori di corrosione sono speciali sostanze chimiche aggiunte al mezzo di lavoro per rallentare o inibire completamente le reazioni di corrosione. Agiscono formando uno strato protettivo sulla superficie del metallo o modificando le proprietà corrosive dell’ambiente.
La divisione degli inibitori della corrosione comprende:
- Inibitori anodici: riducono la velocità della reazione di ossidazione del metallo;
- Inibitori catodici: riducono la velocità della reazione di riduzione dell’ossigeno o dell’idrogeno;
- Inibitori misti: agiscono contemporaneamente sull’anodo e sul catodo, rallentando l’intero processo elettrochimico.
Gli inibitori di corrosione sono ampiamente utilizzati nell’industria petrolifera e del gas, soprattutto nelle condutture, nei sistemi di trasmissione dell’acqua e nelle attrezzature di perforazione, dove la protezione meccanica o catodica è difficile da implementare.
Scelta dei materiali resistenti e dei rivestimenti protettivi
La scelta corretta dei materiali è chiave per ridurre il rischio di corrosione. In ambienti ad alta aggressività chimica si utilizzano acciai inossidabili, leghe di nichel, acciai legati ad alta resistenza e titanio che presentano una maggiore resistenza alla corrosione.
Un’ulteriore protezione è fornita dai rivestimenti anticorrosione, che fungono da barriera tra il metallo e l’ambiente aggressivo. Tra le soluzioni più comunemente utilizzate vi sono:
- Rivestimenti epossidici e poliuretanici: utilizzati in tubazioni e serbatoi;
- Rivestimenti protettivi metallici (ad esempio, zinco, alluminio): forniscono protezione catodica per lunghi periodi di tempo;
- Barriere protettive ceramiche e composite: utilizzate in ambienti estremi, come le piattaforme petrolifere e gli impianti di raffinazione.
Cause della corrosione nell’industria petrolifera e del gas – riassunto
La corrosione nell’industria petrolifera e del gas comporta costi elevati, rischi per la sicurezza e danni ambientali. Per garantire una protezione efficace delle infrastrutture è indispensabile comprendere i meccanismi di corrosione e attuare strategie di prevenzione adeguate, come la protezione catodica, gli inibitori della corrosione, i rivestimenti protettivi e il monitoraggio regolare.
La prevenzione della corrosione è fondamentale per aumentare la longevità delle infrastrutture e ridurre al minimo il rischio di guasti. Le moderne tecnologie consentono un controllo sempre più efficace di questo processo, importante alla luce dei crescenti requisiti operativi e ambientali.
Questo articolo si basa sul libro “Metallurgy and Corrosion Control in Oil and Gas Production” di Robert Heidersbach.