Causas da corrosão na indústria do petróleo e do gás
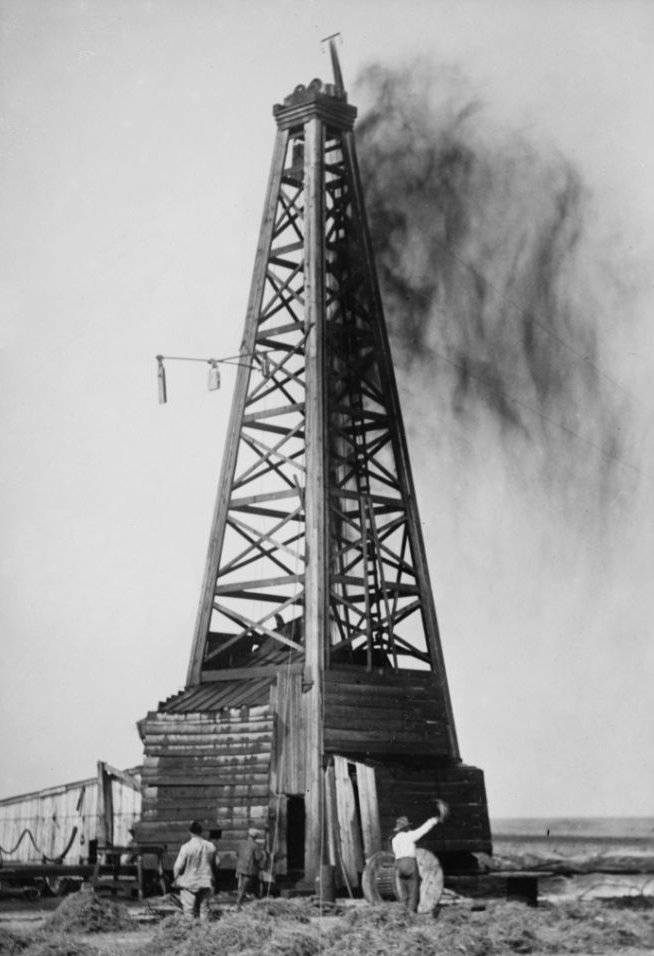
Índice
A corrosão é um dos problemas mais graves na indústria do petróleo e do gás, pois afeta a segurança e os custos operacionais. Ocorre em todas as fases da operação: da extração ao transporte e ao armazenamento de matérias-primas. As perdas anuais relacionadas com a corrosão na indústria estão estimadas em milhares de milhões de dólares, e os eventos de corrosão não controlados podem originar falhas catastróficas nas infraestruturas.
Uma gestão inadequada do risco de corrosão pode resultar no seguinte:
- Danos em tubagens e tanques de armazenamento, aumentando o risco de fugas e explosões.
- Interrupções da produção e elevados custos de reparação.
- A degradação das peças metálicas dos equipamentos de perfuração e refinação reduz a sua vida útil.
- Poluição ambiental, especialmente no caso de derrames de petróleo ou gás.
Compreender as causas da corrosão é fundamental para a controlar eficazmente e evitar efeitos indesejados. Este artigo abordará os principais tipos de corrosão que ocorrem na indústria do petróleo e do gás e os fatores queaceleram este fenómeno.
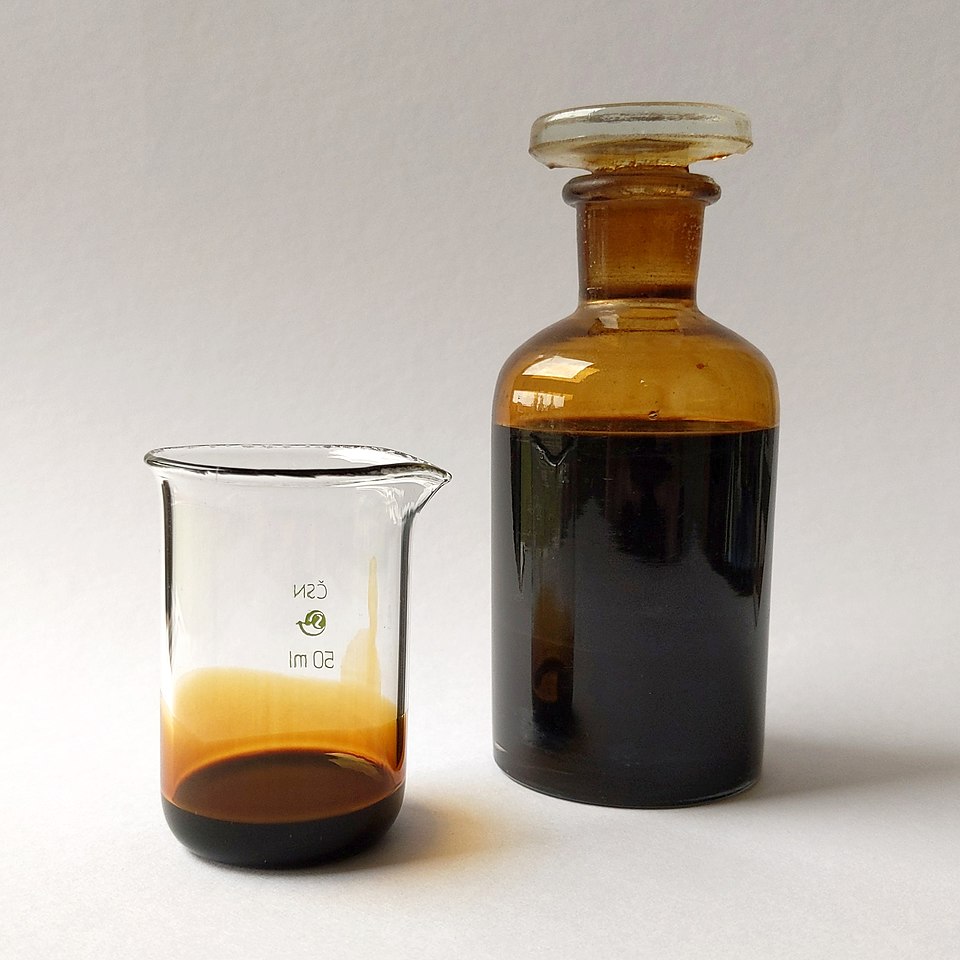
Tipos de corrosão na indústria do petróleo e do gás
A corrosão no setor do petróleo e do gás pode assumir diferentes formas, dependendo das condições ambientais, da composição química do meio e das propriedades dos materiais. É fundamental saber distinguir entre os diferentes tipos de corrosão para proteger eficazmente as infraestruturas e prolongar a sua vida útil.
- Corrosão geral – é o tipo de corrosão mais comum, em que o metal sofre uma oxidação uniforme em toda a sua superfície. Ocorre na presença de oxigénio e humidade, levando à degradação gradual do material. Como resultado deste processo, a espessura das paredes das tubagens e dos tanques diminui, reduzindo a sua resistência. Embora este tipo de corrosão seja relativamente fácil de monitorizar, requer medidas preventivas sistemáticas, tais como revestimentos protectores e inibidores.
- Corrosão galvânica – ocorre quando dois metais diferentes estão em contacto elétrico num ambiente condutor. O metal menos nobre (ânodo) sofre uma oxidação acelerada, enquanto o metal mais nobre (cátodo) permanece protegido. Este fenómeno é particularmente importante em sistemas de condutas e estruturas offshore, onde é necessário unir diferentes materiais. A seleção adequada dos materiais e o isolamento elétrico entre eles são utilizados para reduzir este tipo de corrosão.
- Corrosão por pites – é uma forma local de corrosão em que o metal se degrada em pontos pequenos mas profundos. Ocorre mais frequentemente na presença de iões cloreto, que contribuem para a formação de pites, enfraquecendo a estrutura do material. Ao contrário da corrosão geral, que se distribui uniformemente, a corrosão por pites pode levar rapidamente à perfuração de componentes estruturais. A utilização de materiais resistentes à corrosão e inibidores é crucial para a sua redução.
- Fissuração por corrosão sob tensão (SCC) – é um processo em que um material fissura sob a ação simultânea de tensão mecânica e de um ambiente químico agressivo. As fissuras podem desenvolver-se gradualmente, mas as consequências graves podem levar à falha súbita do equipamento. A SCC ocorre especialmente em condutas e tanques que operam a alta pressão e em ambientes que contêm sulfureto de hidrogénio.
- A corrosão por influência microbiana (MIC – Microbially Influenced Corrosion) ocorre devido à atividade de microrganismos que acelera a degradação do metal através da produção de produtos químicos agressivos. Particularmente problemática é a atividade das bactérias redutoras de sulfato (SRB), que leva à formação de sulfureto de hidrogénio, aumentando o risco de corrosão e fragilização do material. O combate a este tipo de corrosão exige uma desinfeção regular e a utilização de biocidas.
- Corrosão por erosão – ocorre devido ao fluxo intenso de líquido ou gás, principalmente quando o meio contém partículas sólidas como areia ou depósitos minerais. A combinação de fatores mecânicos e químicos provoca a abrasão gradual da camada protetora do metal, levando ao desgaste acelerado dos componentes. São utilizados materiais com maior resistência à abrasão e os parâmetros de fluxo são controlados para reduzir este tipo de corrosão.
Principais fatores que aceleram a corrosão
A corrosão na indústria do petróleo e do gás ocorre sob a influência de muitos fatores que podem acelerar significativamente a degradação do metal. O ambiente químico, as condições físicas e a dinâmica do fluxo de fluidos têm uma influência fundamental no desenvolvimento dos processos de corrosão. Conhecer estes fatores é essencial para uma prevenção eficaz da corrosão e para uma seleção óptima dos métodos de proteção.
A presença de oxigénio (O₂)
O oxigénio é um dos principais fatores que aceleram a corrosão, especialmente em ambientes aquosos. Quando entra em contacto com um metal, provoca a sua oxidação, levando à formação de produtos de corrosão, como óxidos e ferrugem. Mesmo pequenas quantidades de oxigénio podem aumentar significativamente a taxa de corrosão, especialmente quando presentes em condutas ou tanques que contenham água ou humidade. Restringir o acesso do oxigénio à superfície metálica através de vedações, revestimentos protetores e a utilização de inibidores é fundamental para reduzir este tipo de corrosão.
Presença de sulfureto de hidrogénio (H₂S) e dióxido de carbono (CO₂)
O sulfureto de hidrogénio (H₂S) e o dióxido de carbono (CO₂) são os dois gases corrosivos mais comuns na indústria petrolífera. CO₂ (“corrosão doce”) – quando entra em contacto com a água, forma ácido carbónico (H₂CO₃), que baixa o pH e acelera a dissolução de metais, originando cavidades em tubagens e tanques. H₂S (“corrosão ácida”) – provoca a formação de sulfuretos de ferro (FeS), que pode ter um efeito protetor, mas também aumenta o risco de corrosão viva e fragilização por hidrogénio. O efeito destes gases na corrosão depende da sua concentração, temperatura e pressão, tornando necessária a utilização de materiais resistentes ao CO₂ e ao H₂S em ambientes agressivos.

Humidade e presença de água
A água é fundamental na maioria dos processos de corrosão porque atua como um eletrólito, permitindo que a corrente flua entre o ânodo e o cátodo na superfície do metal. Dependendo da sua composição química, pode acelerar a corrosão em diferentes graus.
- Água doce – contém oxigénio, que promove a oxidação do metal.
- Água do mar – rica em iões cloreto (Cl-), que intensificam a corrosão por pites.
- Água de reservatório – pode conter sulfatos, carbonatos e bactérias redutoras de sulfatos, levando à corrosão microbiana.
A gestão do teor de água nos sistemas petrolíferos inclui a sua separação, a remoção de compostos corrosivos e a utilização de inibidores.
Temperatura e pressão
A temperatura e a pressão elevadas são alguns dos principais fatores que influenciam a taxa e a natureza dos processos de corrosão na indústria do petróleo e do gás. O seu impacto é particularmente significativo em ambientes extremos, como poços profundos, condutas de alta pressão e instalações offshore.
A temperatura afeta diretamente a taxa de reações químicas e eletroquímicas que conduzem à corrosão. O aumento da temperatura acelera a oxidação dos metais e as reações com os gases corrosivos, aumentando a sua agressividade. Ao mesmo tempo, pode desestabilizar camadas protectoras, como a camada passiva de óxido nos aços inoxidáveis, tornando o metal mais suscetível à corrosão. A temperatura elevada também afeta a solubilidade dos gases na água – o CO₂ e o H₂S podem reagir mais intensamente com a água, formando ácidos agressivos que atacam as superfícies metálicas.
As altas temperaturas também podem levar à quebra dos inibidores de corrosão, que são substâncias utilizadas para retardar a degradação do metal. Alguns inibidores perdem as suas propriedades protetoras em condições térmicas extremas, exigindo a utilização de produtos químicos mais resistentes. Tipos específicos de corrosão também podem ocorrer sob certas condições, como a corrosão de alta temperatura, que é a oxidação do metal sem água líquida, ocorrendo em caldeiras e trocadores de calor, por exemplo. Outro tipo é a corrosão por sulfureto, que ocorre em ambientes ricos em enxofre, o que é particularmente importante nos processos de refinação de petróleo.
As temperaturas elevadas também podem promover a fissuração por corrosão sob tensão (SCC), que é a formação de fissuras na estrutura de um material causada por uma combinação de tensão mecânica e um ambiente químico agressivo. Este tipo de dano é particularmente perigoso porque pode desenvolver-se impercetivelmente, levando a uma falha súbita.
A pressão afeta a intensidade da corrosão ao alterar as propriedades físico-químicas dos gases e líquidos presentes no sistema. A alta pressão aumenta a solubilidade do CO₂ e do H₂S na água, tornando o meio mais agressivo para os materiais estruturais. Estes gases, combinados com a humidade, formam ácidos que aceleram a degradação do metal, o que é particularmente problemático em sistemas operados a alta pressão.
Outro fator importante é o efeito da alta pressão na durabilidade dos materiais. Em poços profundos e condutas de transmissão, a pressão extrema causa impactos químicos e mecânicos mais intensos nas superfícies metálicas. Isto pode enfraquecer a estrutura do material e aumentar a suscetibilidade à cavitação: a formação e colapso de bolhas de vapor, que podem danificar a superfície metálica através de impactos violentos, acelerando a sua degradação.
Exemplos de locais típicos expostos à corrosão
A corrosão na indústria do petróleo e do gás ocorre em muitos componentes da infraestrutura, especialmente quando os metais são expostos a ambientes químicos agressivos, alta pressão e temperatura. Os seus efeitos podem danificar condutas, tanques e equipamento de processamento, causando paragens dispendiosas e riscos de segurança.
Condutas, tanques e sistemas de transmissão
As condutas e os tanques de armazenamento estão entre os componentes de infraestruturas que mais frequentemente sofrem corrosão, uma vez que as suas paredes estão em constante contacto com um meio que contém água, CO₂, H₂S e impurezas mecânicas. A corrosão interna pode levar a picadas e perfurações, enquanto a corrosão externa, causada pela humidade, oxigénio e correntes parasitas, enfraquece a estrutura do material. As condutas e os reservatórios subterrâneos expostos a mudanças de temperatura, que provocam a condensação e o desenvolvimento da corrosão atmosférica, estão particularmente expostos a esse risco. A prevenção da corrosão baseia-se na proteção catódica, na utilização de inibidores e em revestimentos protetores.
Infraestruturas offshore e equipamento de perfuração
As plataformas de perfuração e os oleodutos offshore operam num ambiente extremamente agressivo, onde a água salgada, as fortes correntes e a elevada humidade aceleram a corrosão. A corrosão galvânica ocorre na interface de vários metais, o que é particularmente perigoso, e a corrosão por erosão, que provoca danos na superfície sob a influência de um forte fluxo de água e de partículas em suspensão. O equipamento de perfuração, incluindo tubos e válvulas, está adicionalmente sujeito a corrosão sob tensão e fragilização por hidrogénio, especialmente na presença de H₂S. Para reduzir a degradação, são utilizados materiais resistentes a alta pressão, proteção catódica anódica e revestimentos anticorrosivos especializados.
Sistemas de arrefecimento e permutadores de calor
Os sistemas de refrigeração e os permutadores de calor são suscetíveis à corrosão resultante de altas temperaturas, condições de funcionamento variáveis e produtos químicos agressivos utilizados nos processos tecnológicos. Entre os problemas mais comuns estão a corrosão por erosão, causada pelo rápido escoamento do fluido, a corrosão microbiana, associada ao crescimento bacteriano, e a corrosão por vibração, que enfraquece os componentes metálicos sob tensões mecânicas e ambientais. A seleção adequada dos materiais, o controlo regular da composição da água e a limpeza cíclica dos sistemas são medidas preventivas fundamentais.
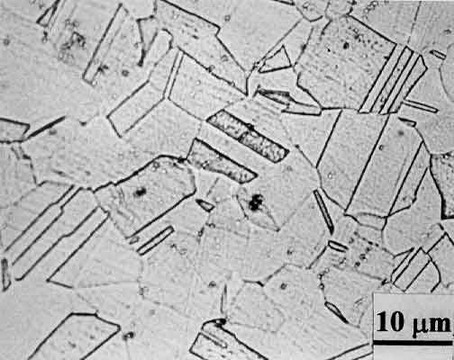
Efeitos da corrosão na indústria do petróleo e do gás
A corrosão no setor do petróleo e do gás tem graves consequências económicas, ambientais e operacionais. A degradação das infraestruturas conduz a paragens não planeadas, a um aumento dos custos de manutenção e a riscos para a segurança humana e ambiental.
Aumento dos custos de funcionamento e manutenção
A corrosão é um dos principais fatores que afectam os custos de exploração na indústria do petróleo e do gás. A reparação de condutas danificadas, a substituição de componentes corroídos e a implementação de sistemas de proteção contra a corrosão geram enormes despesas. Além disso, as inspeções frequentes e a monitorização do estado da infraestrutura exigem despesas financeiras significativas. A nível mundial, os custos anuais relacionados com a corrosão nesta indústria alcançam os milhares de milhões de dólares.
A corrosão progressiva pode levar a falhas de equipamento, fugas e danos em condutas e tanques, resultando na necessidade de parar a produção. As interrupções não só reduzem a eficiência operacional, como também geram perdas financeiras adicionais relacionadas com reparações e atrasos nas entregas. Em casos extremos, a corrosão pode causar a paragem total da infraestrutura, o que é particularmente problemático para instalações offshore e poços em águas profundas.
A corrosão das infraestruturas de petróleo e gás pode levar a falhas catastróficas, como rupturas de condutas, derrames de inflamáveis e explosões, que ameaçam diretamente a vida e a saúde dos trabalhadores e das comunidades circundantes. As fugas de gás ou de petróleo podem causar incêndios e, em casos extremos, explosões em plataformas petrolíferas ou em instalações de refinação. A prevenção e o controlo adequados da corrosão são fundamentais para minimizar o risco de acidentes.
Impacto ambiental
A corrosão que conduz a derrames de petróleo, gás ou produtos químicos tem efeitos catastróficos nos ecossistemas aquáticos e terrestres. A fuga destas substâncias para o solo e as águas subterrâneas causa contaminação que pode persistir durante décadas. Os derrames de petróleo nos oceanos causam grandes perdas nas populações marinhas e a destruição dos habitats costeiros. Os incidentes ambientais resultantes de acidentes de corrosão conduzem frequentemente a danos multimilionários e a sanções para as empresas responsáveis pelos derrames.
Um dos casos mais notáveis de corrosão que conduziu a um desastre ambiental foi o derrame de petróleo de Prudhoe Bay no Alasca, em 2006. O oleoduto de transporte de petróleo perfurou-se em resultado da corrosão interna causada pela acumulação de sedimentos e por um controlo insuficiente dos inibidores de corrosão. Devido aos danos na infraestrutura, mais de 200 000 galões de petróleo derramaram-se na tundra árctica, contaminando uma área de vários hectares. O derrame teve um impacto catastrófico no ecossistema local, destruindo o habitat dos animais e provocando consequências ecológicas a longo prazo. Foi necessária uma operação de descontaminação dispendiosa, e a empresa que geria a infraestrutura foi penalizada financeiramente e obrigada a efetuar melhorias na infraestrutura.
Estratégias para minimizar e prevenir a corrosão
A corrosão na indústria do petróleo e do gás é inevitável, mas pode ser eficazmente controlada e atenuada através de estratégias de proteção adequadas. A gestão eficaz do risco de corrosão não só prolonga a vida útil das infraestruturas, como também reduz os custos de funcionamento e o risco de falhas.
Proteção catódica
Um dos métodos mais eficazes de proteção dos metais contra a corrosão é a proteção catódica, que é utilizada principalmente em condutas, tanques e estruturas subterrâneas e offshore. Envolve a aplicação de corrente elétrica ou de ânodos ativos para reduzir o potencial eletroquímico do metal protegido, de modo a inibir o processo de corrosão.
Existem dois tipos principais de proteção catódica:
- Proteção galvânica (com recurso a ânodos de sacrifício) – utiliza metais de menor potencial eletroquímico, como o zinco, o magnésio ou o alumínio, que sofrem um desgaste controlado, protegendo assim o próprio material estrutural.
- Proteção catódica por corrente impressa (ICCP) – consiste na ligação de uma fonte de corrente contínua à estrutura a proteger, que impede a corrosão através do fornecimento controlado de eletrões.
Os sistemas de proteção catódica são essenciais em condutas de transporte, estruturas offshore e tanques de armazenamento onde a corrosão é particularmente intensa.
Aplicação de inibidores de corrosão
Os inibidores de corrosão são produtos químicos especiais adicionados ao meio de trabalho para retardar ou inibir completamente as reações de corrosão. Atuam formando uma camada protetora na superfície do metal ou modificando as propriedades corrosivas do ambiente.
A divisão dos inibidores de corrosão inclui:
- Inibidores anódicos – reduzem a velocidade da reação de oxidação do metal.
- Inibidores catódicos – reduzem a velocidade da reação de redução do oxigénio ou do hidrogénio.
- Inibidores mistos – atuam simultaneamente no ânodo e no cátodo, abrandando todo o processo eletroquímico.
Os inibidores de corrosão são amplamente utilizados na indústria do petróleo e do gás, especialmente em condutas, sistemas de transmissão de água e equipamento de perfuração, onde a proteção mecânica ou catódica é difícil de implementar.
Seleção de materiais resistentes e revestimentos protetores
A seleção adequada dos materiais é a chave para reduzir o risco de corrosão. Os ambientes com elevada agressividade química utilizam aços inoxidáveis, ligas de níquel, aços de liga de alta resistência e titânio que apresentam uma maior resistência à corrosão.
Uma proteção adicional é proporcionada por revestimentos anticorrosão, que atuam como uma barreira entre o metal e o ambiente agressivo. Entre as soluções mais comummente utilizadas contam-se:
- Revestimentos de epóxi e poliuretano – utilizados em tubagens e tanques.
- Revestimentos protetores de metal (por exemplo, zinco, alumínio) – fornecem proteção catódica durante períodos prolongados.
- Barreiras de proteção cerâmicas e compósitas – utilizadas em ambientes extremos, como plataformas petrolíferas e instalações de refinarias.
Causas da corrosão na indústria do petróleo e do gás – resumo
A corrosão na indústria do petróleo e do gás conduz a custos elevados, riscos de segurança e danos ambientais. A proteção eficaz das infraestruturas exige a compreensão dos mecanismos de corrosão e a aplicação de estratégias de prevenção adequadas, como a proteção catódica, os inibidores de corrosão, os revestimentos protetores e a monitorização regular.
A prevenção da corrosão é fundamental para aumentar a longevidade das infraestruturas e minimizar o risco de falhas. As tecnologias modernas permitem um controlo cada vez mais eficaz deste processo, o que é importante face às crescentes exigências operacionais e ambientais.operational and environmental requirements.
Este artigo é baseado no livro “Metallurgy and Corrosion Control in Oil and Gas Production”, de Robert Heidersbach.