Alliages résistants à la corrosion dans l’industrie pétrolière
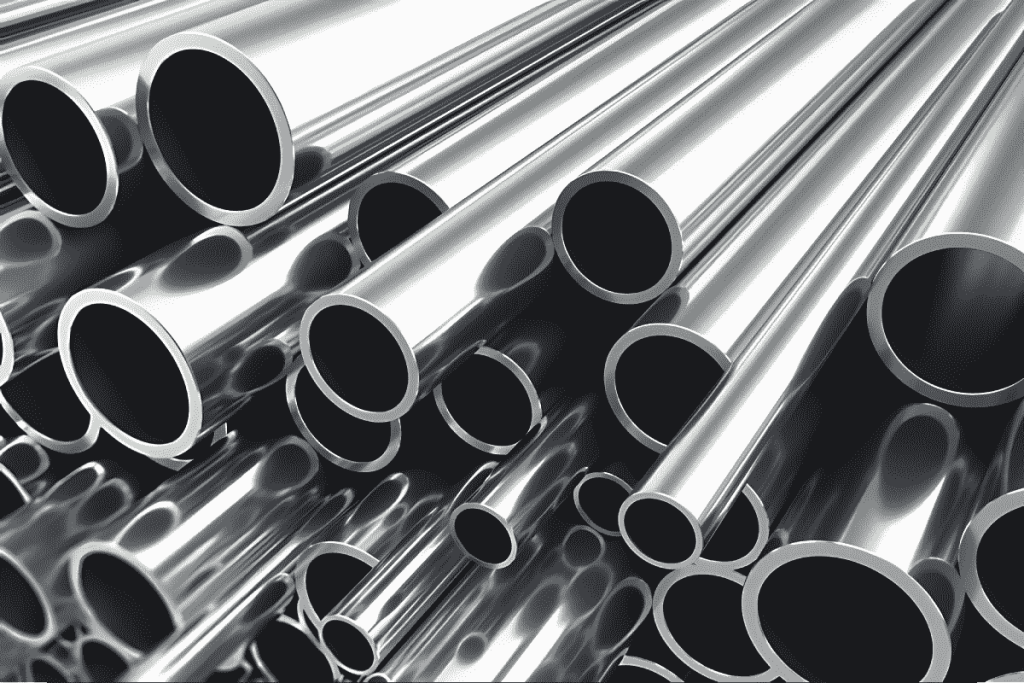
Table des matières
L’industrie du pétrole et du gaz a besoin de matériaux capables de résister à des conditions d’exploitation extrêmes, telles que des pressions élevées, des environnements chimiques agressifs ou même des températures variables. Le choix des bons matériaux pour les pipelines, les réservoirs ou les installations offshore sont critique pour la sécurité, la durabilité et les coûts d’exploitation des infrastructures.
L’acier au carbone, ainsi que les alliages résistants à la corrosion, sont parmi les matériaux les plus couramment utilisés dans ce secteur. L’acier au carbone, en raison de sa grande résistance mécanique et de son coût relativement faible, est largement utilisé dans la construction des pipelines et des structures de soutien. Cependant, sa susceptibilité à la corrosion, dans des environnements agressifs, rend nécessaire dans de nombreuses applications l’utilisation d’alliages résistants à celle-ci, tels que l’acier inoxydable, le nickel ou le titane.
Cet article examine les propriétés de l’acier au carbone et des alliages résistants à la corrosion, leurs avantages et leurs limites, ainsi que leurs principales différences. Cette analyse va permettre de mieux comprendre les conditions dans lesquelles un matériau particulier est le plus efficace ainsi que les tendances en matière de développement de nouvelles technologies de matériaux.
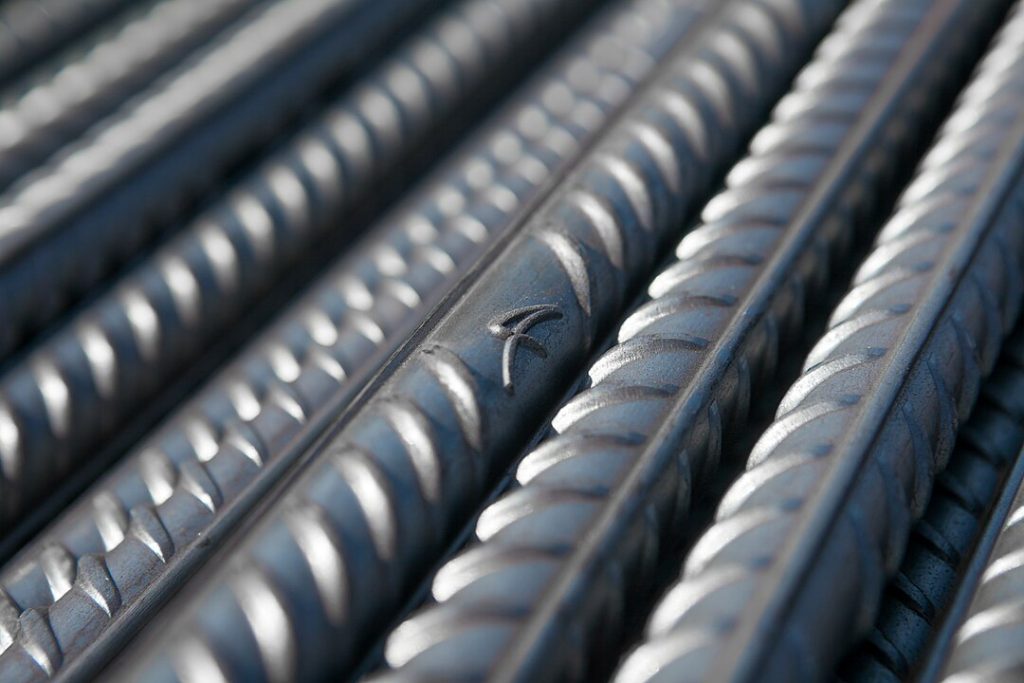
Acier au carbone – Propriétés et applications
L’acier au carbone est un alliage de fer et de carbone, avec une teneur en carbone généralement allant jusqu’à 2 %. En fonction de la quantité de carbone, il existe des aciers à faible teneur, à teneur moyenne et à haute teneur. L’industrie pétrolière utilise principalement des aciers à faible teneur en carbone, qui ont une bonne soudabilité et ductilité, mais qui sont plus sensibles à la corrosion que les alliages ayant une teneur plus élevée en additifs d’alliage protecteurs.
L’acier au carbone est largement utilisé dans l’industrie pétrolière, fondamentalement en raison de son rapport prix/résistance. Ses principaux avantages sont les suivants…
raison de son rapport prix/résistance. Ses principaux avantages sont les suivants…
Un prix bas – L’acier au carbone est beaucoup moins cher à produire que les alliages spécialisés résistants à la corrosion.
Une bonne résistance mécanique – Ce qui permet de l’utiliser dans des structures soumises à de lourdes charges, et pour finir…
Une disponibilité et un traitement faciles – La possibilité de production en masse et la facilité de soudage et de formage font qu’il est largement utilisé dans la construction des oléoducs et des réservoirs de stockage.
Malgré ces avantages, l’acier au carbone présente une résistance limitée à la corrosion, en particulier lorsqu’il est exposé à l’eau de mer, aux acides ou bien aux gaz corrosifs. Dans les environnements riches en sulfure d’hydrogène, la corrosion par le sulfure peut provoquer de graves dommages, entraînant la fragilisation due à l’hydrogène et la fissuration du matériau. Ce problème oblige à recourir à des méthodes de protection supplémentaires, telles que les revêtements anticorrosion, les inhibiteurs de corrosion et la protection cathodique, ce qui a pour effet d’augmenter les coûts d’exploitation.
Alliages résistant à la corrosion – Types et caractéristiques
Aciers inoxydables
Les aciers inoxydables sont des alliages de fer, de chrome et souvent de nickel ainsi que de molybdène, qui présentent une résistance élevée à la corrosion, en raison de la formation d’une couche protectrice d’oxydes de chrome à la surface du métal. Cette couche empêche la dégradation du matériau, ce qui rend ces aciers inoxydables aptes à être utilisés dans des environnements chimiques agressifs, à des températures élevées et dans des conditions d’exposition à l’eau de mer. L’acier inoxydable est utilisé dans…
- Les systèmes de transmission en milieu marin où l’eau contient des chlorures qui accélèrent la corrosion.
- Les systèmes industriels à haute température où l’acier au carbone traditionnel pourrait se dégrader.
- Les réservoirs et systèmes de raffinerie exposés à des produits chimiques agressifs.
La large application des aciers inoxydables dans l’industrie pétrolière est principalement due à leur versatilité et à leurs propriétés mécaniques favorables. Ils sont utilisés dans les pipelines de transmission, les réservoirs de stockage et les appareils utilisés dans les processus de raffinage, étant donné que le contact avec des substances corrosives est inévitable.
Dans l’environnement marin, les aciers inoxydables sont souvent le matériau de construction de choix parce qu’ils résistent aux chlorures puisqu’ils accélèrent la corrosion par piqûres. Dans les systèmes à haute température tels que les échangeurs de chaleur et les fours de raffinerie, les aciers inoxydables conservent leur stabilité et leur résistance, ce qui leur permet d’être utilisés pendant de longues périodes sans risque d’affaiblissement de la structure métallique.
Malgré leurs nombreux avantages, les aciers inoxydables peuvent être sensibles à la corrosion fissurante sous contrainte et à la corrosion par piqûres, en particulier en présence d’ions chlorure agressifs. Par conséquent, dans des conditions industrielles extrêmes, une protection supplémentaire, tels que des inhibiteurs de corrosion ou des revêtements protecteurs, est fréquemment utilisée pour prolonger la durée de vie du matériau.
Alliages de nickel et de titane
Les alliages de nickel et de titane comptent parmi les matériaux les plus avancés pour résister à la corrosion dans les conditions d’utilisation les plus exigeantes. Leurs propriétés chimiques et mécaniques uniques leur permettent d’être utilisés dans des installations fonctionnant dans des températures extrêmes, des environnements acides et des conditions de haute pression.
Les alliages de nickel, comme Inconel, présentent une résistance exceptionnelle au sulfure d’hydrogène (H₂S), aux acides et aux températures élevées, ce qui les rend idéaux pour les applications dans les puits profonds et les systèmes de raffinerie. Grâce à leur structure métallurgique, ils résistent également à la corrosion sous contrainte, évitant ainsi les fissures et les défaillances dans les systèmes implantés en eaux profondes.
Par ailleurs, le titane et ses alliages se distinguent par leur résistance extrêmement élevée à la corrosion dans l’eau de mer, ce qui les rend aptes à être utilisés dans les structures offshore, les plates-formes pétrolières et les pipelines sous-marins. Leur faible densité, par rapport à d’autres métaux, permet de construire des structures légères, mais solides, qui peuvent fonctionner dans des conditions extrêmes pendant de nombreuses années et sans entretien.
L’une des principales limites de l’utilisation des alliages de nickel et de titane est leur coût élevé, qui limite souvent leur utilisation aux applications les plus exigeantes. C’est pourquoi des solutions hybrides sont fréquemment utilisées, combinant des composants en alliages résistants à la corrosion avec des matériaux moins onéreux, tels que l’acier au carbone, qui sont en outre protégés contre la dégradation.
Malgré le prix élevé des alliages de nickel et de titane, leur fiabilité et leurs besoins d’entretien minimaux les rendent remplaçables dans des domaines dans lesquels une défaillance pourrait avoir des conséquences environnementales et économiques catastrophiques.
Le choix entre les aciers inoxydables et les alliages de nickel et de titane dépend principalement des conditions environnementales et des spécificités de l’application. Les aciers inoxydables offrent un équilibre favorable entre le prix et la résistance à la corrosion, tandis que les alliages de nickel et de titane assurent une protection maximale, y compris et surtout dans les environnements les plus extrêmes, mais à un coût d’exploitation beaucoup plus élevé. L’industrie pétrolière cherche à optimiser l’utilisation de ces matériaux, en combinant leurs avantages pour maximiser la durabilité et l’efficacité des infrastructures.
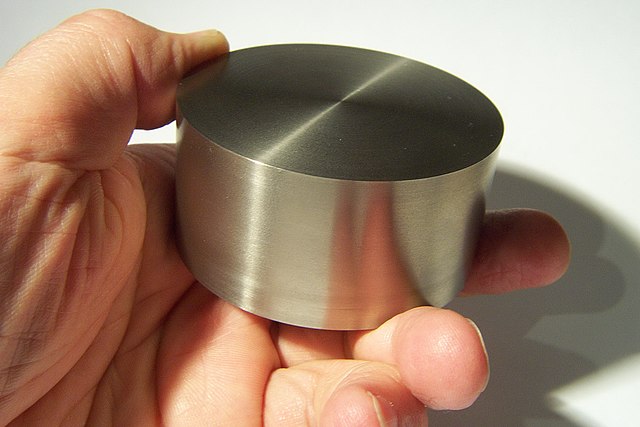
Comparaison de l’acier au carbone et des alliages résistants à la corrosion
Le choix du bon matériau, dans l’industrie du pétrole et du gaz, dépend, comme nous venons de le voir, de nombreux facteurs, tels que la résistance à la corrosion, la résistance mécanique, les coûts de production et de maintenance, et les conditions d’exploitation. Malgré sa popularité, l’acier au carbone n’est toutefois pas toujours la meilleure option, en particulier dans les environnements chimiquement agressifs alors que des matériaux plus résistants à la dégradation deviennent nécessaires.
La principale différence entre l’acier au carbone et les alliages résistants à la corrosion est leur capacité à résister à des conditions de fonctionnement difficiles. L’acier au carbone, bien que bon marché et largement disponible, nécessite une protection supplémentaire pour éviter une dégradation rapide. En revanche, les alliages résistants à la corrosion, tels que l’acier inoxydable et les alliages de nickel, bénéficient d’une protection naturelle contre les agents corrosifs, ce qui prolonge considérablement leur durée de vie et réduit leur entretien.
Résistance à la corrosion dans différents environnements
L’un des facteurs clé dans le choix d’un matériau est sa résistance à la corrosion dans un environnement particulier. L’acier au carbone est très sensible à la corrosion en présence d’humidité, d’oxygène, de sulfure d’hydrogène (H₂S) et de dioxyde de carbone (CO₂). En particulier dans les pipelines souterrains et les installations offshore, tandis que le contact avec l’eau de mer et les sels minéraux est inévitable, s’imposent alors des méthodes de protection supplémentaires telles que les revêtements protecteurs, les inhibiteurs de corrosion ou la protection cathodique sont nécessaires.
Toutefois… Les aciers inoxydables, les alliages de nickel et de titane présentent une résistance à la corrosion beaucoup plus élevée, car ils forment des couches protectrices naturelles qui empêchent d’autres dommages se produire à la surface du métal. Les alliages de nickel sont particulièrement efficaces dans les environnements acides, tandis que le titane donne de bons résultats dans les installations marines dans lesquelles l’exposition intense à l’eau de mer pourrait rapidement dégrader l’acier au carbone.
Résistance mécanique et durabilité dans les conditions d’exploitation
Les matériaux utilisés dans l’industrie pétrolière doivent présenter une résistance mécanique adéquate, en plus de la résistance à la corrosion. L’acier au carbone offre une grande résistance aux charges statiques et dynamiques, ce qui fait qu’il est souvent utilisé dans les pipelines de transport et les structures de support. Cependant, dans des environnements extrêmes, tels que les puits en eau profonde ou les installations soumises à des températures et des pressions élevées, celui-ci peut être sensible à la corrosion sous contrainte et à la fissuration par corrosion, ce qui, en conséquence, limite sa durabilité.
Les alliages résistants à la corrosion, en particulier les alliages de nickel et de titane, conservent leurs propriétés, même dans des conditions extrêmement difficiles. Ils résistent aux températures élevées, au sulfure d’hydrogène et aux produits chimiques agressifs, ce qui induit une durée de vie beaucoup plus longue que l’acier au carbone traditionnel. Leur résistance mécanique est également plus élevée, ce qui permet d’utiliser des parois de pipelines et des composants structurels moins épais, sans risquer d’affaiblir les structures concernées.
Coûts de production et d’entretien
Le coût des matériaux joue un rôle évidemment très important dans les décisions relatives à l’ingénierie des infrastructures pétrolières. L’acier au carbone est relativement bon marché à produire, ce qui le rend largement utilisé dans les pipelines et les réservoirs de stockage, comme nous l’avons vu précédemment, cependant, sa susceptibilité à la corrosion nécessite une protection supplémentaire, ce qui engendre des coûts liés à l’entretien, à la réparation et à l’inspection, en étapes obligatoires.
Bien que les alliages résistants à la corrosion soient beaucoup plus chers à produire, ils offrent des coûts d’exploitation plus faibles, car ils ne nécessitent pas d’inspections fréquentes ni de mesures préventives coûteuses. Leur utilisation permet donc d’économiser des fonds, à long terme, en particulier dans les installations fonctionnant dans des conditions extrêmes, présentant un risque élevé de défaillance et de dégradation des matériaux.
Exemples d’applications dans l’industrie pétrolière
Dans la pratique, le choix du matériau dépend des spécificités de l’application. L’acier au carbone C, avec des protections supplémentaires, est le plus souvent utilisé dans les pipelines terrestres et souterrains car, dans ces conditions, le risque de corrosion peut être efficacement contrôlé par des revêtements protecteurs et une protection cathodique.
Dans les installations offshore, alors que les conditions sont naturellement beaucoup plus agressives, les aciers inoxydables et les alliages de nickel et de titane sont plus couramment utilisés. Ces matériaux peuvent fonctionner pendant des décennies sans nécessiter de réparations coûteuses. En particulier dans les puits profonds et les pipelines transportant des produits chimiques agressifs, des matériaux plus résistants sont nécessaires pour assurer la fiabilité de l’infrastructure.
Application pratique des deux groupes de matériaux
Le choix entre l’acier au carbone et les alliages résistants à la corrosion dépend des conditions d’exploitation et des exigences de durabilité et de fiabilité des infrastructures. Les deux types de matériaux sont largement utilisés dans l’industrie pétrolière, mais leur efficacité dépend de l’environnement spécifique dans lequel ils sont utilisés.
Utilisation de l’acier au carbone dans les pipelines et les réservoirs
L’acier au carbone est le matériau de construction le plus utilisé dans l’industrie pétrolière, principalement en raison de sa résistance mécanique et de son faible prix. Il est principalement utilisé dans la construction des pipelines transportant le pétrole brut et le gaz naturel, ainsi que dans les réservoirs de stockage et les structures de soutien.
En revanche, l’acier au carbone donne de bons résultats dans les pipelines terrestres, car sa susceptibilité à la corrosion peut être contrôlée grâce à la protection cathodique, aux revêtements anticorrosion et aux inhibiteurs de corrosion. Les installations souterraines, quant à elles, utilisent des revêtements isolants en polyéthylène ou en époxy, dans le but de réduire le contact du métal avec l’humidité et le sol.
L’acier au carbone des réservoirs de produits pétroliers est protégé par des revêtements protecteurs et fait l’objet d’une surveillance régulière pour détecter toute perte de matériau. Dans les environnements dans lesquels des produits chimiques agressifs sont présents, une protection supplémentaire ou des alliages plus résistants encore à la corrosion doivent être appliqués dans et sur les zones critiques de la structure.
Alliages résistant à la corrosion dans les installations offshore et les environnements acides
Dans les environnements où l’acier au carbone se dégrade rapidement, il est donc utilisé des aciers inoxydables et des alliages de nickel et de titane. Ces matériaux sont très résistants à la corrosion et aux températures et aux pressions extrêmes. Parmi les exemples de tels environnements, nous pouvons citer les plateformes de forage, les pipelines sous-marins et les installations transportant des produits chimiques agressifs.
Sur les plates-formes offshore, les aciers inoxydables sont impliqués dans les systèmes de tuyauterie et les structures de support qui sont exposés à l’eau de mer et à des températures variables. Les aciers inoxydables contenant du molybdène et du nickel, qui protègent le matériau contre les piqûres et la corrosion fissurante sous contrainte, sont particulièrement performants dans ce genre de conditions.
Les pipelines offshore utilisent souvent des alliages de titane, qui se caractérisent par leur résistance à l’eau de mer et leur faible poids propre, ce qui facilite leur installation et leur transport. En raison de leur durabilité, les pipelines en titane peuvent être exploités durant des décennies, sans nécessiter d’entretien important.
L’acier au carbone traditionnel se dégrade rapidement, essentiellement à cause de la corrosion par le sulfure et le dioxyde dans les environnements acides, où H₂S et CO₂ sont présents. Dans de tels cas, les alliages de nickel tels que l’Inconel sont utilisés pour protéger contre les produits chimiques agressifs et résister à la corrosion fissurante sous contrainte.
Utilisation de matériaux hybrides
Tout ce qui précède, et en raison des différences de coût et de propriétés, a permis de réfléchir à des solutions hybrides sont souvent utilisées dans la pratique de l’ingénierie. Elles consistent à combiner l’acier au carbone avec des matériaux résistants à la corrosion dans les zones les plus vulnérables à la dégradation.
Dans les oléoducs, il est donc possible de rencontrer des systèmes dans lesquels l’intérieur des tuyaux est revêtu d’une couche d’alliage résistant à la corrosion, tandis que la structure extérieure reste en acier au carbone. Cette approche permet ainsi de réduire les coûts tout en assurant une grande durabilité des composants exposés à des substances agressives.
De même, les réservoirs de stockage utilisent des revêtements en alliage de nickel et de titane aux points de contact avec les produits chimiques, tandis que les autres composants structurels sont en acier au carbone. Cette conception est à la fois durable et économiquement viable.
Alliages résistants à la corrosion dans l’industrie pétrolière – Résumé
Le choix des matériaux dans l’industrie pétrolière a une incidence sur la durabilité des infrastructures, la sécurité et les coûts d’exploitation. L’acier au carbone, bien que bon marché et largement utilisé, nécessite une protection supplémentaire contre la corrosion. Les alliages résistants à la corrosion, tels que les aciers inoxydables, les aciers au nickel et au titane, offrent une plus grande durabilité, mais leur coût est plus élevé.
L’industrie pétrolière développe des revêtements modernes, des systèmes de surveillance et de nouveaux alliages métalliques dans le but d’améliorer la résistance à la corrosion et optimiser les coûts. De plus en plus, des solutions hybrides sont donc utilisées, combinant les avantages économiques de l’acier au carbone avec la durabilité des alliages résistants à la corrosion.
Cet article est basé sur le livre « Metallurgy and Corrosion Control in Oil and Gas Production » de Robert Heidersbach.