Causes de la corrosion dans l’industrie pétrolière et gazière
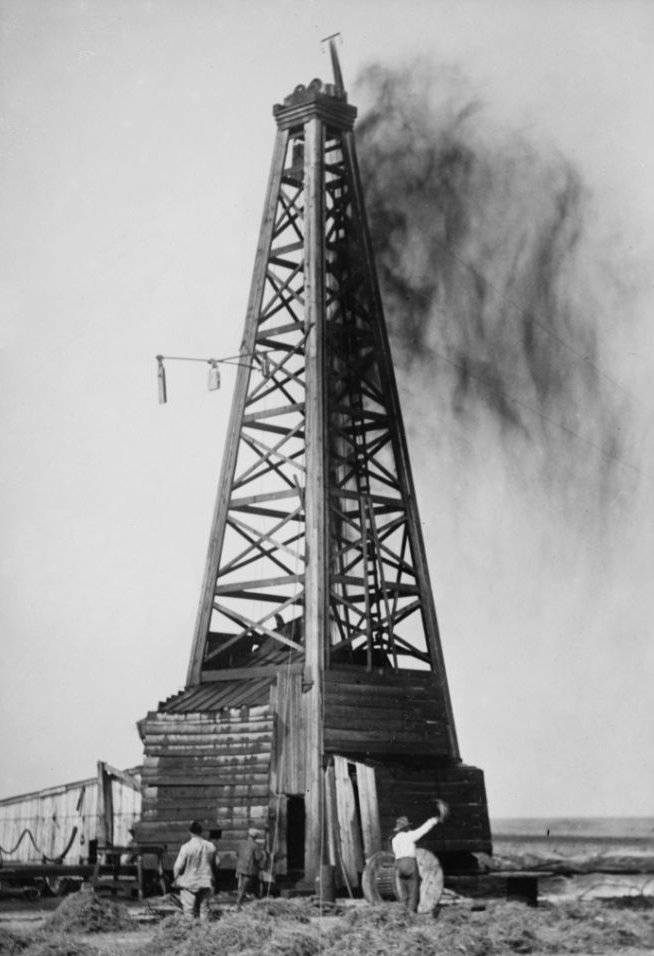
Table des matières
La corrosion est l’un des problèmes les plus graves de l’industrie pétrolière et gazière, car elle affecte la sécurité et les coûts d’exploitation. Elle se produit à tous les stades de l’exploitation, depuis l’extraction jusqu’au stockage des matières premières, en passant par le transport. Les pertes annuelles liées à la corrosion dans l’industrie sont estimées à des milliards de dollars et les événements de corrosion incontrôlés peuvent entraîner des défaillances catastrophiques des infrastructures.
Une gestion inadéquate des risques de corrosion peut avoir les conséquences suivantes…
- des dommages aux pipelines et aux réservoirs de stockage, ce qui accroît le risque de fuites et d’explosions
- des interruptions de la production et des coûts de réparation élevés
- la dégradation des pièces métalliques des équipements de forage et de raffinage réduit leur durée de vie
- la pollution de l’environnement, notamment en cas de déversement de pétrole ou de gaz.
Il est essentiel de comprendre les causes de cette corrosion afin de la contrôler efficacement et de prévenir les effets indésirables. Cet article présente les principaux types de corrosion dans l’industrie pétrolière et gazière et les facteurs qui l’accélèrent.
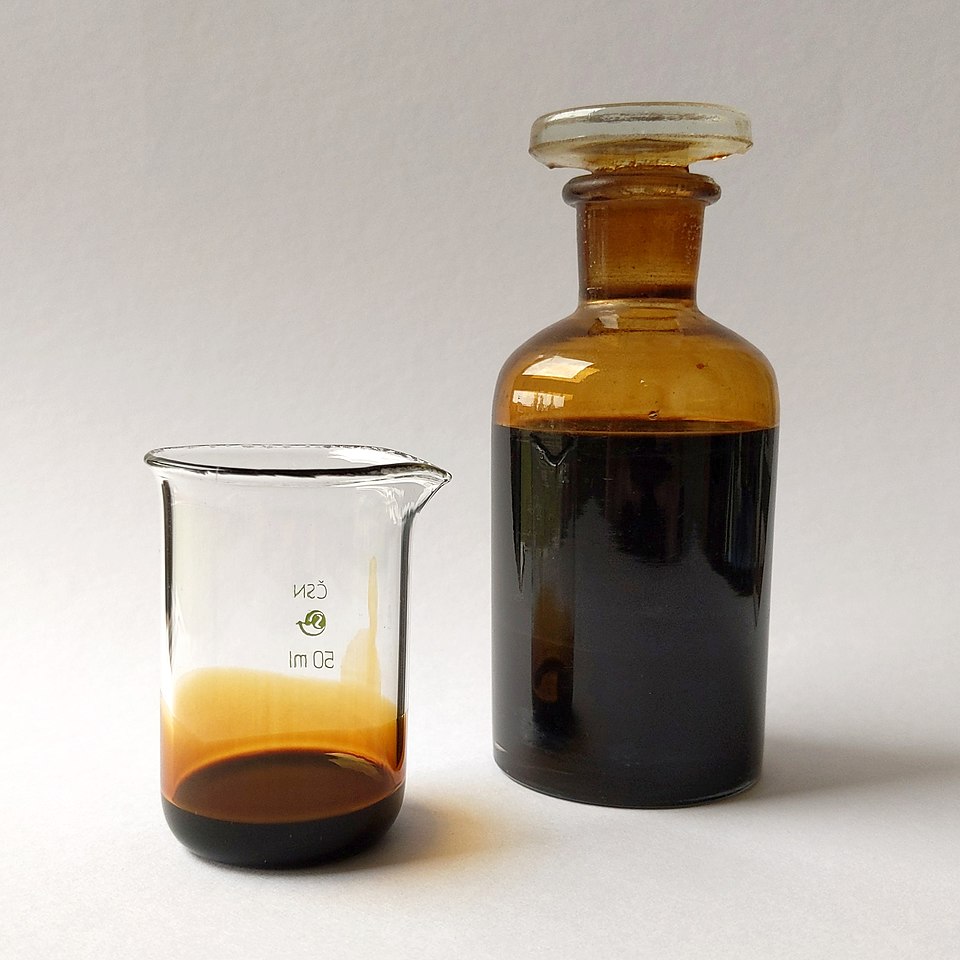
Types de corrosion dans l’industrie pétrolière et gazière
La corrosion dans ces secteurs respectifs peut prendre différentes formes en fonction des conditions environnementales, de la composition chimique du milieu et des propriétés des matériaux. Il est donc important de distinguer les différents types de corrosion afin de protéger efficacement les infrastructures et de prolonger leur durée de vie.
- Corrosion générale – Il s’agit du type de corrosion le plus courant, dans lequel le métal subit une oxydation uniforme sur toute sa surface. Elle se produit en présence d’oxygène et d’humidité, ce qui entraîne une dégradation progressive du matériau. Ce processus entraîne une diminution de l’épaisseur des parois des pipelines et des réservoirs, ce qui en réduit la résistance. Bien que ce type de corrosion soit relativement facile à surveiller, il nécessite des mesures préventives systématiques, consistant en revêtements protecteurs et des inhibiteurs.
- Corrosion galvanique – Se produit lorsque deux métaux différents sont en contact électrique dans un environnement conducteur. Le métal le moins noble (anode) subit une oxydation accélérée, tandis que le métal le plus noble (cathode) reste protégé. Ce phénomène est particulièrement important dans les systèmes de canalisations et les structures offshore, pour lesquels il est nécessaire d’assembler différents matériaux. Une sélection appropriée des matériaux et une isolation électrique entre eux permettent de réduire ce type de corrosion.
- La corrosion par piqûres – Cette forme locale de corrosion, dans laquelle le métal se dégrade en des points petits, mais profonds, se produit le plus souvent en présence d’ions chlorure, qui contribuent à la formation de ces piqûres, affaiblissant la structure du matériau. Contrairement à la corrosion générale, qui se répartit uniformément, la corrosion par piqûres peut rapidement conduire à la perforation des éléments de structure. L’utilisation de matériaux résistants à la corrosion et d’inhibiteurs est donc indispensable pour réduire ceci.
- La corrosion sous contrainte, SCC – Ce processus, dans lequel un matériau se fissure sous l’action simultanée d’une contrainte mécanique et d’un environnement chimique agressif, développe progressivement des fissures. Mais les conséquences graves entraînent une défaillance soudaine de l’équipement. La CSC se produit surtout dans les pipelines et les réservoirs fonctionnant à haute pression ou dans les environnements contenant du sulfure d’hydrogène.
- La corrosion sous influence microbienne, MIC, Microbially Influenced Corrosion – Cette dernière est due à l’activité des micro-organismes qui accélèrent la dégradation des métaux en produisant des produits chimiques agressifs. L’activité des bactéries sulfato-réductrices, les SRB, est particulièrement problématique, car elle entraîne la formation de sulfure d’hydrogène, ce qui accroît le risque de corrosion et de fragilisation des matériaux. La lutte contre ce type de corrosion nécessite une désinfection régulière et l’utilisation de biocides.
- Corrosion par érosion – Ceci se produit en raison d’un écoulement intensif de liquide ou de gaz, principalement lorsque le milieu contient des particules solides telles que du sable ou des dépôts minéraux. La combinaison de facteurs mécaniques et chimiques entraîne une abrasion progressive de la couche protectrice du métal, ce qui accélère l’usure des composants. Pour réduire ce type de corrosion, sont utilisés des matériaux plus résistants à l’abrasion tandis que les paramètres d’écoulement sont contrôlés.
Principaux facteurs d’accélération de la corrosion
La corrosion dans l’industrie du pétrole et du gaz se produit sous l’influence de nombreux facteurs qui peuvent accélérer de manière notable la dégradation du métal. L’environnement chimique, les conditions physiques et la dynamique de l’écoulement des fluides ont une influence certaine sur le développement des processus de corrosion, quels qu’ils soient. La connaissance de ces facteurs est donc primordiale, tant pour une prévention efficace de la corrosion que pour une sélection optimale des méthodes de protection.
La présence d’oxygène (O₂)
L’oxygène est l’un des principaux facteurs d’accélération de la corrosion, surtout en milieu aqueux. Lorsqu’il entre en contact avec un métal, il provoque son oxydation, ce qui entraîne la formation de produits de corrosion tels que les oxydes et la rouille. Même de petites quantités d’oxygène peuvent augmenter de manière significative le taux de corrosion, en particulier lorsqu’elles sont présentes dans des canalisations ou des réservoirs contenant de l’eau ou de l’humidité. Dans le but de réduire ce type de corrosion, il est nécessaire de limiter l’accès de l’oxygène à la surface du métal concerné grâce à des joints, des revêtements protecteurs et l’utilisation d’inhibiteurs.
Présence de sulfure d’hydrogène (H₂S) et de dioxyde de carbone (CO₂)
Le sulfure d’hydrogène (H₂S) et le dioxyde de carbone (CO₂) sont les deux gaz corrosifs les plus courants à trouver dans l’industrie pétrolière.
CO₂, « corrosion douce » – Au contact de l’eau, se forme de l’acide carbonique (H₂CO₃), qui abaisse le pH et accélère la dissolution des métaux, ce qui provoque des cavités dans les pipelines et les réservoirs.
H₂S, la « corrosion acide » – Provoque la formation de sulfures de fer, FeS, qui peuvent avoir un effet protecteur, mais augmentent également le risque de corrosion vive et de fragilisation par l’hydrogène. L’effet de ces gaz sur la corrosion dépend de leur concentration, de la température et de la pression, d’où la nécessité d’utiliser des matériaux résistants au CO₂ et au H₂S, dans tous les environnements agressifs.

Humidité et présence d’eau
L’eau joue un rôle prépondérant dans la plupart des processus de corrosion, car elle agit comme un électrolyte, permettant au courant de circuler entre l’anode et la cathode à la surface du métal. En fonction de sa composition chimique, elle peut accélérer la corrosion à divers degrés.
- Eau douce – Contient de l’oxygène, ce qui favorise l’oxydation des métaux.
- Eau de mer – Riche en ions chlorure, Cl-, qui intensifient la corrosion par piqûres.
- Eau de réservoir – Peut contenir des sulfates, des carbonates et des bactéries réduisant les sulfates, ce qui entraîne une corrosion microbienne.
La gestion de l’eau, dans les systèmes pétroliers, comprend sa séparation, l’élimination des composés corrosifs et l’utilisation d’inhibiteurs.
Température et pression
La température et la pression élevées sont certains des facteurs clés qui influencent la vitesse et la nature des processus de corrosion, surtout dans l’industrie du pétrole et du gaz. Leur impact est particulièrement important dans les environnements extrêmes tels que les puits profonds, les pipelines à haute pression et les installations offshore.
La température affecte directement la vitesse des réactions chimiques et électrochimiques conduisant à la corrosion. Une augmentation de la température accélère l’oxydation du métal et les réactions s’enchaînent avec les gaz corrosifs, augmentant ainsi leur agressivité. En même temps, elle peut déstabiliser les couches protectrices, comme la couche d’oxyde passive sur les aciers inoxydables, rendant le métal plus sensible à la corrosion. Une température élevée affecte également la solubilité des gaz dans l’eau. Ainsi, le CO₂ et le H₂S peuvent réagir plus intensément avec de l’eau, formant des acides agressifs qui attaquent les surfaces métalliques.
Les températures élevées peuvent par ailleurs entraîner la dégradation des inhibiteurs de corrosion, qui sont des substances utilisées pour ralentir la dégradation du métal. Certains inhibiteurs perdent leurs propriétés protectrices dans des conditions thermiques extrêmes, ce qui nécessite l’utilisation de produits chimiques plus résistants. Des types spécifiques de corrosion peuvent tout autant se produire dans certaines conditions. Nous pensons ici à la corrosion à haute température, qui est une oxydation du métal sans eau liquide, se produisant dans les chaudières et les échangeurs de chaleur, pour citer exemple. Un autre type de corrosion est celle induite par les sulfures, à trouver dans des environnements riches en soufre, ce qui est particulièrement important dans les processus de raffinage du pétrole.
Les températures élevées peuvent également favoriser la fissuration par corrosion sous contrainte, FCC, c’est-à-dire la formation de fissures dans la structure d’un matériau, qui se produisent sous l’effet combiné d’une contrainte mécanique et d’un environnement chimique agressif. Ce type de dommage est particulièrement dangereux, car il peut se développer imperceptiblement et entraîner une défaillance soudaine.
Par ailleurs, la pression affecte l’intensité de la corrosion en modifiant les propriétés physico-chimiques des gaz et des liquides présents dans un système. La haute pression augmente la solubilité du CO₂ et du H₂S dans l’eau, ce qui rend le milieu plus agressif pour les matériaux structurels. Ces gaz, combinés à l’humidité, forment des acides qui accélèrent la dégradation des métaux, ce qui est particulièrement problématique dans les systèmes fonctionnant à haute pression.
Un autre facteur important est l’effet de la haute pression sur la durabilité des matériaux. Dans les puits profonds ainsi que dans les pipelines de transport, la pression extrême provoque des impacts chimiques et mécaniques plus intenses sur les surfaces métalliques. Ceci peut donc affaiblir la structure du matériau et augmenter la susceptibilité à la cavitation, c’est-à-dire la formation et l’effondrement de bulles de vapeur, qui peuvent endommager la surface métallique par des impacts violents, accélérant ainsi sa dégradation.
Exemples de sites typiques exposés à la corrosion
Dans l’industrie pétrolière et gazière, la corrosion se produit dans de nombreux composants de l’infrastructure, en particulier lorsque les métaux sont exposés à des environnements chimiques agressifs, à des pressions élevées et à des températures, comme nous l’avons vu précédemment. Les effets délétères peuvent endommager les pipelines, les réservoirs, les équipements de traitement, entraînant des temps d’arrêt coûteux et des risques, notamment en matière de sécurité.
Pipelines, réservoirs et systèmes de transmission
Les pipelines et les réservoirs de stockage sont parmi les éléments d’infrastructure qui se corrodent le plus fréquemment, car leurs parois sont en contact permanent avec un milieu contenant de l’eau, du CO₂, du H₂S ainsi que des impuretés mécaniques. La corrosion interne peut entraîner des piqûres et des perforations, tandis que la corrosion externe, causée par l’humidité, l’oxygène et les courants vagabonds, affaiblit la structure du matériau. Les pipelines et les réservoirs souterrains exposés aux changements de température, ce qui provoquent la condensation et le développement de la corrosion atmosphérique, sont particulièrement menacés. La prévention de la corrosion repose sur la protection cathodique, l’utilisation d’inhibiteurs et de revêtements de protection.
Infrastructure offshore et équipement de forage
Les plates-formes de forage offshore ainsi que les pipelines fonctionnent dans un environnement extrêmement agressif, dans lequel l’eau salée, les courants forts et l’humidité élevée accélèrent tous la corrosion. La corrosion galvanique se produit à l’interface de divers métaux, ce qui est particulièrement dangereux, et la corrosion par érosion entraîne des dommages à la surface, sous l’influence d’un fort débit d’eau et de particules en suspension.
Les équipements de forage, y compris les tuyaux et les vannes, sont également sujets à la corrosion sous contrainte et à la fragilisation par l’hydrogène, en particulier en présence de H₂S. Pour réduire ce type de dégradation, sont utilisés des matériaux résistants aux hautes pressions, une protection cathodique anodique ainsi que des revêtements anticorrosion spécialisés.
Systèmes de refroidissement et échangeurs de chaleur
Les systèmes de refroidissement, tout comme les échangeurs de chaleur, sont sensibles à la corrosion résultant des températures élevées, des conditions de fonctionnement variables et des produits chimiques agressifs utilisés dans les processus technologiques. Parmi les problèmes les plus courants figurent la corrosion par érosion, causée par l’écoulement rapide des fluides, la corrosion microbienne, associée à la croissance bactérienne, et la corrosion par vibration, qui affaiblit les composants métalliques sous l’effet des contraintes mécaniques et environnementales. La sélection appropriée des matériaux, le contrôle régulier de la composition de l’eau et le nettoyage régulier des systèmes sont des mesures préventives essentielles.
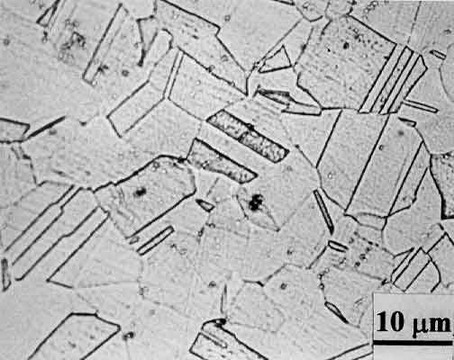
Effets de la corrosion dans l’industrie du pétrole et du gaz
La corrosion dans ces secteurs a de graves conséquences économiques, environnementales et opérationnelles. La dégradation des infrastructures entraîne des temps d’arrêt imprévus, une augmentation des coûts de maintenance et des risques pour la sécurité humaine et environnementale.
Augmentation des coûts d’exploitation et de maintenance
La corrosion est l’un des principaux facteurs affectant les coûts d’exploitation dans l’industrie du pétrole et du gaz. La réparation des pipelines endommagés, le remplacement des composants corrodés et la mise en place de systèmes de protection contre la corrosion génèrent d’énormes dépenses. En outre, les inspections fréquentes obligatoires et la surveillance de l’état de l’infrastructure nécessitent des dépenses importantes. Globalement, les seuls coûts annuels liés à la corrosion, dans cette industrie, atteignent des milliards de dollars.
La corrosion progressive peut entraîner des pannes d’équipement, des fuites et des dommages aux pipelines ainsi qu’aux réservoirs, ce qui oblige généralement à interrompre la production. Ces dernières réduisent l’efficacité opérationnelle, mais génèrent en outre des pertes financières supplémentaires liées aux réparations et aux retards de livraison. Dans les cas extrêmes, la corrosion peut entraîner un arrêt complet de l’infrastructure, ce qui est particulièrement dramatique pour les installations offshore et les puits en eaux profondes.
La corrosion des infrastructures pétrolières et gazières peut entraîner des défaillances catastrophiques, telles que des ruptures de pipelines, des déversements de produits inflammables et des explosions, qui menacent directement la vie et la santé des travailleurs et des communautés environnantes. Les fuites de gaz ou de pétrole peuvent provoquer des incendies et, dans des cas extrêmes, des explosions sur les plates-formes pétrolières ou dans les usines de raffinage. Une prévention et un contrôle adéquats de la corrosion sont essentiels pour minimiser le risque d’accident.
Impact sur l’environnement
La corrosion entraînant des déversements de pétrole, de gaz ou de produits chimiques a des effets catastrophiques sur les écosystèmes aquatiques et terrestres. La fuite de ces substances dans le sol et dans les eaux souterraines provoque une contamination qui peut persister durant des décennies. Les déversements de pétrole dans les océans provoquent des pertes considérables dans les populations marines et la destruction des habitats côtiers. Les incidents environnementaux résultant d’accidents dus à la corrosion entraînent souvent des dommages et des sanctions de plusieurs millions de dollars pour les entreprises responsables des déversements.
L’un des cas les plus terribles de corrosion ayant entraîné une catastrophe environnementale est la marée noire de la baie de Prudhoe en Alaska en 2006. L’oléoduc s’est perforé à la suite d’une corrosion interne causée par l’accumulation de sédiments et un contrôle insuffisant des inhibiteurs de corrosion. En raison des dommages causés à l’infrastructure, plus de 200 000 gallons de pétrole, environ 760 000 litres, ont fui dans la toundra arctique, contaminant une zone de plusieurs hectares.
Le déversement a eu un impact catastrophique sur l’écosystème local, détruisant l’habitat des animaux et entraînant des conséquences écologiques à long terme. Une opération de décontamination coûteuse a été nécessaire et l’entreprise qui gérait l’infrastructure a été frappée par des pénalités financières et contrainte de procéder à des améliorations de l’infrastructure.
Stratégies pour minimiser et prévenir la corrosion
La corrosion dans l’industrie du pétrole et du gaz est inévitable, mais elle peut être contrôlée et atténuée efficacement grâce à la mise en place de stratégies de protection appropriées, et rigoureusement respectées !
Une gestion efficace des risques de corrosion permet donc de prolonger la durée de vie des infrastructures, mais aussi de réduire les coûts d’exploitation et le risque de défaillance.
Protection cathodique
L’une des méthodes les plus efficaces pour protéger les métaux contre la corrosion est la protection cathodique. C’est cette dernière qui est principalement utilisée dans les pipelines, les réservoirs et les structures souterraines et offshore. Elle implique l’application d’un courant électrique ou d’anodes actives permettant de réduire le potentiel électrochimique du métal protégé, de manière à inhiber le processus de corrosion.
Il existe deux types principaux de protection cathodique, que voici…
- La protection galvanique, à l’aide d’anodes sacrificielles – En utilisant des métaux ayant un potentiel électrochimique inférieur, tels que le zinc, le magnésium ou l’aluminium, qui subissent une usure contrôlée, ceci protège le matériau structurel proprement dit.
- Protection cathodique par courant imposé, ICCP – Ceci implique la connexion d’une source de courant continu à la structure à protéger, ce qui empêche la corrosion par l’apport contrôlé d’électrons.
Les systèmes de protection cathodique sont indispensables dans les pipelines de transport, les structures offshore et les réservoirs de stockage, la corrosion y étant particulièrement intense.
Application des inhibiteurs de corrosion
Les inhibiteurs de corrosion sont des produits chimiques spéciaux ajoutés au milieu de travail pour ralentir ou inhiber complètement les réactions de corrosion. Ils agissent en formant une couche protectrice sur la surface du métal ou en modifiant les propriétés corrosives de l’environnement.
Les inhibiteurs de corrosion se répartissent en plusieurs catégories, dont voici les détails…
- Les inhibiteurs anodiques réduisent la vitesse de la réaction d’oxydation du métal.
- Les inhibiteurs cathodiques réduisent la vitesse de la réaction de réduction de l’oxygène ou de l’hydrogène.
- Les inhibiteurs mixtes agissent simultanément sur l’anode et la cathode, ralentissant l’ensemble du processus électrochimique.
Les inhibiteurs de corrosion sont largement utilisés dans l’industrie du pétrole et du gaz, en particulier dans les pipelines, les systèmes de transmission d’eau et les équipements de forage, pour lesquels la protection mécanique ou cathodique est particulièrement difficile à mettre en œuvre.
Sélection des matériaux résistants et des revêtements de protection
Une sélection appropriée des matériaux est l’approche fondamentale qui permet de réduire le risque de corrosion. Les environnements à forte agressivité chimique utilisent des aciers inoxydables, des alliages de nickel, des aciers alliés à haute résistance ainsi que du titane, car tous présentent une résistance accrue à la corrosion.
Une protection supplémentaire est fournie par les revêtements anticorrosion, qui agissent en barrière entre le métal et l’environnement agressif. Les solutions les plus couramment utilisées sont ici…
- Les revêtements époxy et polyuréthane, utilisés dans les pipelines et les réservoirs.
- Les revêtements protecteurs métalliques tels que zinc et aluminium, qui assurent une protection cathodique durant de longues périodes.
- Les barrières de protection céramiques et composites, qui sont utilisées dans des environnements extrêmes, tels que les plates-formes pétrolières et les installations de raffinage.
Causes de la corrosion dans l’industrie pétrolière et gazière – Résumé
La corrosion dans l’industrie pétrolière et gazière entraîne des coûts élevés, des risques pour la sécurité et des dommages environnementaux. Pour protéger efficacement les infrastructures, il faut parfaitement comprendre les mécanismes de la corrosion et mettre en œuvre des stratégies de prévention appropriées, telles que la protection cathodique, les inhibiteurs de corrosion, les revêtements protecteurs et une surveillance régulière.
La prévention de la corrosion est indispensable pour augmenter la longévité des infrastructures et minimiser le risque de défaillance. Les technologies modernes permettent un contrôle de plus en plus efficace de ce processus, ce qui est important compte tenu des exigences opérationnelles et environnementales croissantes.
Cet article est basé sur le livre « Metallurgy and Corrosion Control in Oil and Gas Production » de Robert Heidersbach.