Maßtoleranzen
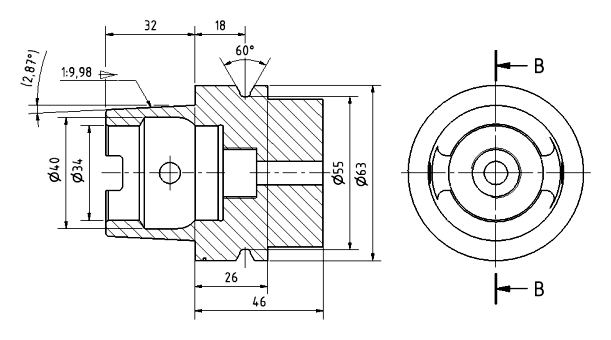
Inhaltsverzeichnis
Maßtoleranzen sind eine der wichtigsten technischen und industriellen Fragen, die Qualität, Funktionalität und Produktionskosten beeinflussen. Jedes technische Bauteil, angefangen von der einfachsten Schraube bis hin zu komplexen Maschinenmechanismen, muss innerhalb eines bestimmten akzeptablen Toleranzbereichs hergestellt werden, um sicherzustellen, dass das Endprodukt die richtige Größe hat und funktioniert.
Um ein Gleichgewicht zwischen Qualität und Kosteneffizienz zu erreichen, ist die moderne Fertigung auf präzise Toleranzvorgaben angewiesen. Angemessene Toleranzen sind eine Voraussetzung für die Vermeidung von Montageproblemen und die Gewährleistung der Kompatibilität von Komponenten unabhängig vom Hersteller.
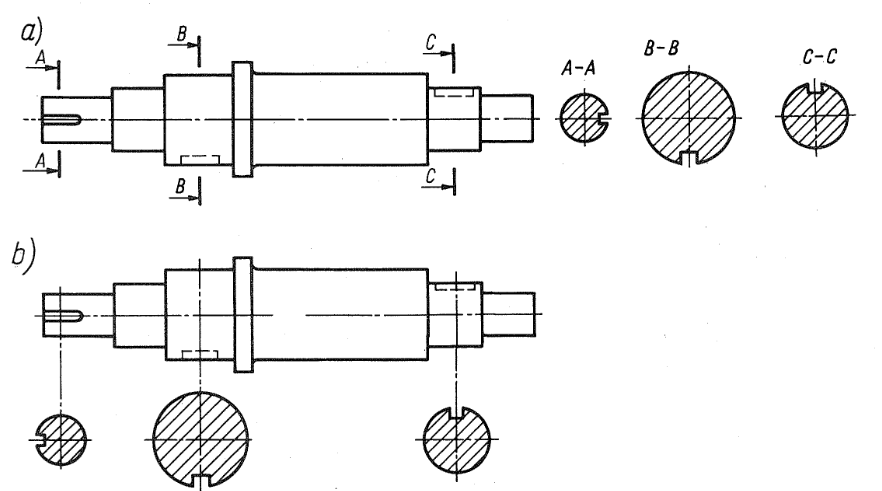
Grundbegriffe der Maßtoleranz
Der Begriff „Maßtoleranz“ bezeichnet eine Abweichung der Maße von den Sollmaßen der technischen Zeichnung, also der Istmaße von den Sollmaßen der technischen Zeichnung. Jedes gefertigte Teil weicht bis zu einem gewissen Grad von den Sollmaßen ab, da die Fertigungsverfahren nicht perfekt sind. Die Grenzen, innerhalb derer diese Abweichungen akzeptabel sind, werden durch die Toleranz festgelegt.
Die Toleranz wird von zwei Schlüsselparametern bestimmt
- Nennmaß (N) – der Wert, für den die Toleranz gilt.
- Grenzabmaße (A und B) – die untere und obere Grenze, innerhalb derer das Istmaß liegen kann.
- Obere und untere Abweichung (Es, Ei für Bohrungen und es, ei für Wellen) – die Differenz zwischen dem Nennmaß und den Grenzwerten.
In internationalen Normen wie PN-EN ISO 286-1:2011 werden 20 Toleranzklassen definiert, die jeweils unterschiedlichen Genauigkeitsstufen entsprechen und je nach Funktion des Bauteils angewendet werden.
Methoden der Maßtoleranz
Traditionell basieren die verwendeten Toleranzen auf Plus-Minus-Werten, die zulässige Abweichungen vom Nennmaß bezeichnen.
Ein moderner Ansatz für die Tolerierung ist das GD&T (Geometrical Dimensioning and Tolerancing) System, mit dem man nicht nur Maßabweichungen, sondern auch geometrische Merkmale von Bauteilen angeben kann. Dieses System ist präziser und funktioneller als die traditionellen Maßtoleranzen. Es berücksichtigt lineare Abmessungen und geometrische Parameter, die für die korrekte Funktion und Montage der Komponenten entscheidend sind.
Das GD&T-System ermöglicht die Kontrolle von geometrischen Merkmalen wie:
- Die Form des Bauteils, z.B.:
- Ebenheit – bestimmt, wie weit eine Fläche von einer idealen Ebene abweichen kann.
- Rundheit – stellt sicher, dass der Querschnitt einer Welle oder eines Lochs so nahe wie möglich an einem idealen Kreis bleibt.
- Zylindrizität – gilt für zylindrische Wellen und Bohrungen und definiert die maximal zulässige Abweichung von der zylindrischen Form.
- Orientierung der Komponenten relativ zueinander, zum Beispiel:
- Rechtwinkligkeit – gibt die maximal zulässige Abweichung von der perfekten Rechtwinkligkeit zwischen zwei Flächen an.
- Parallelität – stellt sicher, dass zwei Flächen oder Achsen so parallel wie möglich sind.
- Neigung – bestimmt, wie stark eine Fläche vom Sollwinkel abweichen darf.
- Position von Komponenten in einem Layout, zum Beispiel:
- Position – steuert, ob sich ein Bauteil (z. B. eine Bohrung) in der richtigen Position im Verhältnis zu anderen Teilen befindet.
- Rundlauf – bestimmt, wie weit eine Welle oder Bohrung relativ zu ihrer Drehachse „ausschlagen“ kann.
- Rundlauf von Bauteilen in Drehbewegung, zum Beispiel:
- Planlauf – wird bei Wellen und rotierenden Bauteilen angewendet und bestimmt die maximale Abweichung der Achse vom Ideal während der Rotation.
- Gesamtrundlauf – eine restriktivere Form des Rundlaufs, die alle Punkte auf der gesamten Drehfläche erfasst.
In der Praxis erleichtert GD&T die Kompatibilität von in verschiedenen Werken gefertigten Teilen, die Verringerung des Risikos von Montageproblemen und die Durchführung eines wirksamen Qualitätsmanagements. Aus diesem Grund wird das GD&T-System in der Automobil-, der Luft- und Raumfahrt-, der Elektronik- und der Präzisionsindustrie eingesetzt.
Die Bedeutung von Toleranzen in Fertigungsprozessen
Maßtoleranzen spielen bei der Montage von Bauteilen eine wichtige Rolle, da jede Ungenauigkeit die Qualität, Haltbarkeit und Funktionalität des fertigen Produkts beeinträchtigen kann. Genau angepasste Toleranzen stellen sicher, dass die einzelnen Komponenten so zusammenpassen, wie es der Konstrukteur beabsichtigt hat. Wenn die Toleranzen zu eng oder zu locker sind, können alle möglichen Montageprobleme auftreten, die zu erhöhten Produktionskosten, Materialverlusten und sogar zum Ausfall ganzer Systeme führen.
Zu enger Sitz – ein Problem bei der Montage von Bauteilen
Ein Hauptproblem, das aus schlechten Toleranzen resultiert, ist eine zu enge Passung, die die Montage erschwert oder unmöglich macht. Dies kann zu zusätzlichen Bearbeitungen führen, die die Produktionskosten erhöhen und die Durchlaufzeiten verlängern.
Wenn beispielsweise der Durchmesser der Welle im Verhältnis zur Bohrung zu groß ist, kann ein Aufbohren der Bohrung oder ein Schleifen der Welle erforderlich sein, um eine korrekte Passform zu gewährleisten. Solche Arbeiten verursachen zusätzliche Kosten und können auch die mechanischen Eigenschaften des Materials beeinträchtigen und seine Struktur schwächen.
Bei der Montage von Kunststoffteilen kann eine zu enge Passung zu Spannungsrissen oder Verformungen und damit zu einer erheblichen Verkürzung der Lebensdauer des Produktes führen. In der Automobil- oder Flugzeugindustrie können selbst minimale Überschreitungen der Toleranzgrenzen zu schwerwiegenden Betriebsproblemen führen, wie z.B. erhöhter Verschleiß der Teile durch übermäßige Reibung.
Zu lockere Passung – instabile Verbindungen
Auf der anderen Seite ist eine zu lockere Passung ein Anziehen der Teile, was zu Schwingungen, Montagespiel und vorzeitigem Verschleiß der Verbindungen führen kann. Bei dynamisch belasteten Teilen wie Antriebswellen, Lagern oder Schraubverbindungen ist eine zu lockere Passung besonders gefährlich.
Ein Beispiel für ein mechanisches Versagen ist eine Bohrung, die im Verhältnis zur Welle zu groß ist. Dies führt dazu, dass das Teil nicht richtig sitzt und während des Betriebs der Maschine rutschen kann. Im Extremfall kann dies dazu führen, dass der gesamte Mechanismus versagt, was dazu führt, dass man das Teil oder die gesamte Maschine austauschen muss.
Im Bauwesen und bei Stahlkonstruktionen kann ein zu großes Spiel zur Schwächung der gesamten Konstruktion und zur Erhöhung des Risikos eines Versagens bei Einwirkung äußerer Kräfte wie Wind oder Erdbeben führen. In solchen Fällen werden Präzisionspassungen mit festgelegten Toleranzwerten verwendet, um Dauerhaftigkeit und Sicherheit zu gewährleisten.
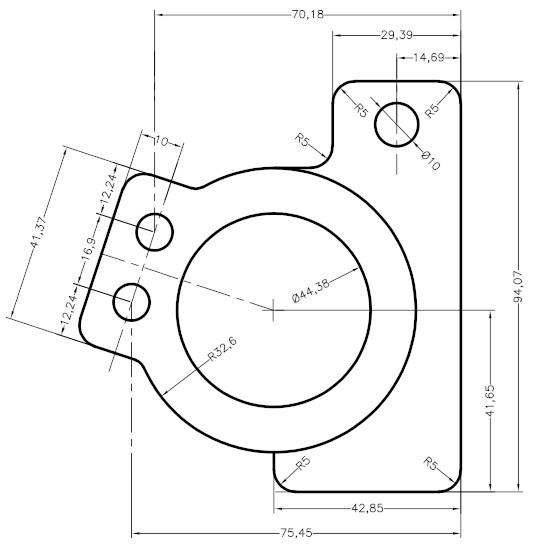
Maßtoleranzstandards und -normen
In den internationalen Normen sind die Maßtoleranzen streng geregelt. In diesen Normen sind die zulässigen Maßabweichungen und die Art und Weise ihrer Kennzeichnung in technischen Zeichnungen festgelegt. Die Anwendung dieser Normen gewährleistet die Einheitlichkeit und Wiederholbarkeit der Produktion, die Erleichterung der internationalen Zusammenarbeit und die Verringerung des Risikos von Montagefehlern.
Die folgende Tabelle zeigt die wichtigsten Normen für Maßtoleranzen und ihre Anwendung:
Norm 11520_77df9a-2b> |
Beschreibung 11520_61554c-89> |
Anwendungsbereiche 11520_5368a6-f1> |
---|---|---|
ISO 286 11520_22726c-21> |
Legt Maßtoleranzklassen für Wellen- und Bohrungspassungen fest. Definiert Grenzabweichungen und Passungsregeln. 11520_3b4a23-d1> |
Feinmechanik, Herstellung von Maschinenteilen, Bohrungen und Wellenpassungen. 11520_287769-b9> |
ISO 14405 11520_aa4ac5-68> |
Standardisiert die Art und Weise, wie Maßtoleranzen in technischen Zeichnungen angegeben werden, insbesondere für lineare Abmessungen. 11520_32a3fe-a9> |
Maschinenbau, Luft- und Raumfahrt, Automobilindustrie. 11520_b8e4b9-5a> |
ISO GPS 11520_e2b02d-66> |
Geometrical Product Specification System – beinhaltet einen ganzheitlichen Ansatz für geometrische Toleranzen. 11520_4d5ab6-8a> |
Präzisionsfertigung, CAD/CAM, Automatisierung der Qualitätskontrolle. 11520_ffece8-e2> |
ISO 1101 11520_40fc4c-f8> |
Normiert Form- und Lagetoleranzmarkierungen und definiert Symbole und Markierungsmethoden auf technischen Zeichnungen. 11520_6ca6ee-2f> |
Qualitätskontrolle, Entwurf von Präzisionsstrukturen. 11520_a9b124-88> |
ISO 8015 11520_997511-6a> |
Beschreibt die Regeln für die Interpretation von Maßen und Toleranzen in ISO GPS. 11520_54a551-72> |
Universell für alle Branchen. 11520_50cd1c-01> |
ASME Y14.5 11520_451825-d7> |
Die amerikanische Norm für geometrische Toleranzen ähnelt der ISO 1101, wird aber hauptsächlich in den USA verwendet. 11520_c8bef2-fb> |
Luft- und Raumfahrt, Automobilindustrie, Luft- und Raumfahrttechnik. 11520_749161-e7> |
ISO 2768 11520_763afc-14> |
Legt allgemeine Maß- und Winkeltoleranzen für Bauteile mittlerer Genauigkeit fest. 11520_b5cd37-00> |
Massenproduktion, Automobilindustrie, Bauwesen. 11520_329967-c7> |
Ein Beispiel für die Anwendung der ISO 286
Die Norm ISO 286 definiert ein System von Passungen für Bohrungen und Wellen, das im Maschinenbau weit verbreitet ist. Das bedeutet, dass jede Welle und jede Bohrung eine bestimmte Toleranz haben kann, je nach der erforderlichen Genauigkeit. Dieses System verwendet Buchstaben- und Zahlenbezeichnungen, wie z.B.:
- H7/g6 – üblicher Gleitsitz.
- H6/h5 – Presspassung für Präzisionsverbindungen.
- H8/f7 – Lose Passung, verwendet für Teile, die frei beweglich sein müssen.
Maßtoleranzen spielen eine wichtige Rolle in der Konstruktion und Fertigung. Ihre Anwendung führt zu qualitativ hochwertigeren Produkten, zu einer Verringerung der durch Fertigungsfehler verursachten Kosten und zur Gewährleistung der Kompatibilität von Bauteilen, auch wenn diese von verschiedenen Lieferanten stammen. Moderne Qualitätskontrollsysteme, wie z. B. ISO GPS, ermöglichen eine noch größere Präzision bei der Entwicklung und Herstellung von Bauteilen, die in der modernen Industrie unerlässlich ist.
Praktische Aspekte der Nutzung von Toleranzen
Maß- und Geometrietoleranzen sind ein wesentlicher Bestandteil der Konstruktion und des Herstellungsprozesses mechanischer Bauteile. Eine korrekte Definition und Kontrolle ist der Garant dafür, dass die Komponenten so zusammenpassen, wie es von den Ingenieuren geplant wurde, und dass der gesamte Herstellungsprozess im Hinblick auf Kosten und Qualität optimiert wird. In diesem Kapitel wird erörtert, wie man Toleranzen auf technischen Zeichnungen korrekt festlegt und welche Messmethoden zu ihrer Kontrolle verwendet werden.
Wie bestimmt man Toleranzen auf einer technischen Zeichnung?
Technische Zeichnungen sind die Schlüsseldokumente in der Fertigung und müssen daher eine klare Angabe der Nennmaße und der zulässigen Abweichungen enthalten. Eine korrekte Kennzeichnung der Toleranzen ermöglicht ein eindeutiges Ablesen der Spezifikationen. Fehlinterpretationen, die zu Montageproblemen oder zusätzlichen Bearbeitungskosten führen können, werden vermieden.
Grundregeln für die Bestimmung von Toleranzen auf einer technischen Zeichnung
- Verwendung geeigneter Kennzeichnungen gemäß den ISO- und ASME-Normen
- die Abmessungen sollten gut lesbar und ohne unnötige Wiederholungen angegeben werden.
- Geometrische Toleranzmarkierungen müssen der ISO 1101 oder ASME Y14.5 entsprechen.
- die Abmessungen und ihre Toleranzen müssen an den geeigneten Stellen der Zeichnung angebracht werden, um die Lesbarkeit nicht zu beeinträchtigen.
- Geometrische Toleranzen für Schlüsselkomponenten festlegen
- Anstatt die klassischen ± Toleranzen für jedes Maß zu verwenden, ist es sinnvoll, geometrische Toleranzen zu verwenden, die die Funktionalität der Komponente besser darstellen.
- zum Beispiel ist die Toleranz der Ebenheit wichtig für tangentiale Oberflächen, und Parallelität ist entscheidend für Gleitführungen und Gleitlager.
- Maße, die für die Montage wichtig sind, sollten als Kontrollmaße bezeichnet werden (z.B. K, C in den technischen Unterlagen).
- Vermeiden Sie zu enge Toleranzen, wenn dies nicht notwendig ist.
- ein häufiger Konstruktionsfehler ist die Annahme sehr enger Toleranzen, die die Herstellungskosten erhöhen.
- Toleranzklassen verwenden, die auf die Funktion des Teils abgestimmt sind – für Präzisionsteile (z. B. Lager) lohnt es sich, IT6-Klassen zu verwenden, und für Strukturteile reichen IT10-IT12 aus.
- nach ISO 2768 können allgemeine Toleranzen für Teile verwendet werden, die keine hohe Fertigungsgenauigkeit erfordern.
- Kompatibilität mit Messverfahren sicherstellen
- die Toleranzen sollten so gewählt werden, dass sie mit den verfügbaren Messwerkzeugen kontrolliert werden können.
- beträgt die Toleranz beispielsweise weniger als 0,01 mm, bieten Standardmessschieber möglicherweise keine ausreichende Genauigkeit, und es wird eine Koordinatenmessmaschine (KMG) benötigt.
Methoden der Dimensionsprüfung
Messverfahren 11520_927c12-18> |
Beschreibung 11520_8be6ef-e7> |
Anwendungsbereich 11520_7ad99f-97> |
---|---|---|
Messschieber 11520_d2f1e3-d9> |
Einfaches Werkzeug zum Messen von Länge, Durchmesser und Tiefe, Genauigkeit von 0,02 mm. 11520_3ddee5-45> |
Allgemeine Produktion, schnelle Maßkontrolle. 11520_d16406-0b> |
Mikrometer 11520_a99605-3a> |
Ein Werkzeug zur präzisen Messung von Durchmessern bis auf 0,001 mm genau. 11520_708498-cb> |
Kontrolle von kritischen Abmessungen. 11520_79a7b6-95> |
Messuhr (Indexlehre) 11520_30e329-07> |
Dient zur Überprüfung des Planlaufs und der Rechtwinkligkeit von Oberflächen. 11520_55f057-16> |
Inspektion von Wellen, Zahnrädern und Lagern. 11520_dae2af-54> |
Koordinatenmessmaschine (CMM) 11520_2002e2-23> |
Ein fortschrittliches 3D-Scansystem, das geometrische und Positionstoleranzen genau misst. 11520_fda560-86> |
Luft- und Raumfahrt, Feinmechanik, Automobilindustrie. 11520_6e3370-79> |
Messprojektor (Profilometer) 11520_23c52f-a2> |
Optisches Verfahren zur Messung von Oberflächenkonturen und Profilen. 11520_e7792a-11> |
Inspektion von Werkstücken mit komplexen Formen. 11520_601c51-43> |
3D-Laserscanner 11520_16b46a-ee> |
Ein berührungsloses Scansystem wird eingesetzt, um die gesamte Oberfläche eines Objekts zu analysieren. 11520_87814c-07> |
Abweichungsanalyse in CAD-Technik, 3D-Druck. 11520_f556f4-fd> |
Zu den praktischen Aspekten der Nutzung von Toleranzen gehören die genaue Bestimmung zulässiger Abweichungen auf technischen Zeichnungen und wirksame Methoden zu deren Kontrolle. Die Verwendung der richtigen Normen und Messwerkzeuge kann das Risiko von Produktionsfehlern minimieren, eine korrekte Montage sicherstellen, und die Produktionskosten optimieren. Heutige Technologien, wie die statistische Prozessanalyse und fortschrittliche Messsysteme, ermöglichen eine noch genauere Kontrolle der Maße und Toleranzen, was für die moderne Industrie von entscheidender Bedeutung ist.
Maßtoleranzen – eine Zusammenfassung
Für die korrekte Montage von Bauteilen in verschiedenen Industriezweigen ist die richtige Wahl der Maßtoleranzen von entscheidender Bedeutung. Ungeeignete Toleranzen können zu Passungsproblemen führen, die eine Erhöhung der Kosten, einen Materialverlust und eine Beeinträchtigung der Produktqualität zur Folge haben. Um die Zuverlässigkeit und Effizienz von Montageprozessen zu gewährleisten, müssen Ingenieure die Toleranzanforderungen sorgfältig analysieren und dabei sowohl funktionale als auch wirtschaftliche Aspekte berücksichtigen.