Aleaciones resistentes a la corrosión en la industria petrolera
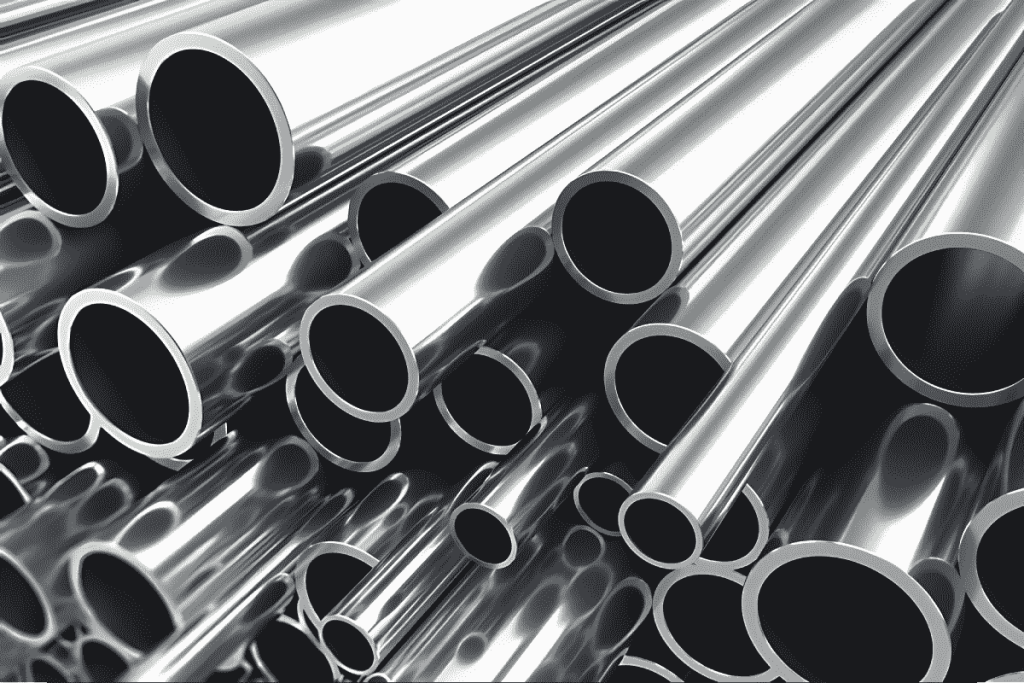
Índice
La industria del petróleo y el gas requiere materiales capaces de soportar condiciones extremas de funcionamiento, como altas presiones, entornos químicos agresivos y temperaturas variables. Elegir los materiales adecuados para las tuberías, depósitos o instalaciones en alta mar es crítico para la seguridad, la durabilidad y los costes de explotación de la infraestructura.
El acero al carbono y las aleaciones resistentes a la corrosión se encuentran entre los materiales más utilizados en este sector. El acero al carbono, debido a su alta resistencia mecánica y coste relativamente bajo, se utiliza ampliamente en la construcción de tuberías y estructuras de soporte. Sin embargo, su susceptibilidad a la corrosión en ambientes agresivos hace necesario el uso de aleaciones resistentes a la corrosión como el acero inoxidable, el níquel o el titanio en muchas aplicaciones.
En este artículo, se analizarán las propiedades del acero al carbono y de las aleaciones resistentes a la corrosión, sus ventajas y limitaciones, y sus principales diferencias. Este análisis permitirá comprender mejor las condiciones en las que un determinado material es más eficaz y las tendencias en el desarrollo de nuevas tecnologías de materiales.
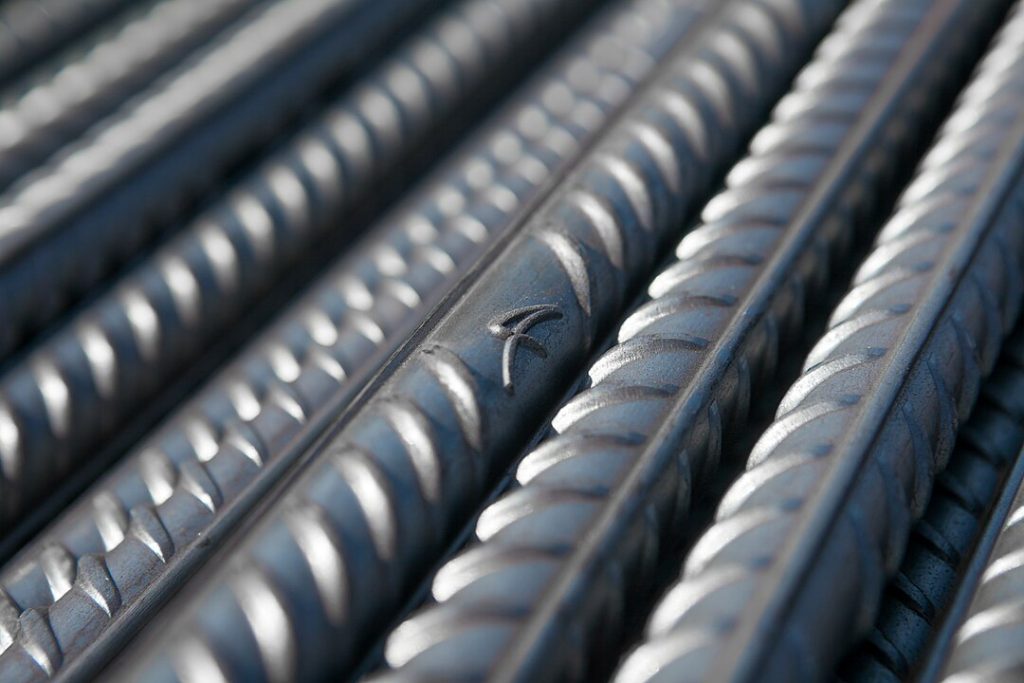
Acero al carbono: propiedades y aplicaciones
Acero al carbono: propiedades y aplicaciones
El acero al carbono es una aleación de hierro y carbono, con un contenido de carbono generalmente de hasta el 2 %. Según la cantidad de carbono, existen aceros de bajo carbono, medio carbono y alto carbono. La industria petrolera utiliza principalmente aceros de bajo contenido en carbono, que tienen buena soldabilidad y ductilidad pero son más susceptibles a la corrosión que las aleaciones con un mayor contenido de aditivos de aleación protectores.
El acero al carbono se utiliza mucho en la industria petrolera, principalmente por su relación precio/resistencia. Sus principales ventajas son: Bajo precio: el acero al carbono es mucho más barato de producir que las aleaciones especializadas resistentes a la corrosión. Buena resistencia mecánica: lo que permite que se utilice en estructuras sometidas a grandes cargas. Fácil disponibilidad y procesamiento: la posibilidad de producción en masa y la facilidad de soldadura y conformado hacen que se utilice ampliamente en la construcción de oleoductos y tanques de almacenamiento.
A pesar de estas ventajas, el acero al carbono tiene una resistencia limitada a la corrosión, especialmente cuando se expone al agua de mar, los ácidos y los gases corrosivos. En entornos ricos en sulfuro de hidrógeno, pueden producirse graves daños por la corrosión del sulfuro, lo que provoca la fragilización por hidrógeno y el agrietamiento del material. Este problema obliga a utilizar métodos adicionales de protección, como revestimientos anticorrosión, inhibidores de corrosión y protección catódica, lo que a su vez aumenta los costes de explotación.
Aleaciones resistentes a la corrosión: tipos y características
Aceros inoxidables
Los aceros inoxidables son aleaciones de hierro, cromo y, a menudo, níquel y molibdeno, que exhiben una alta resistencia a la corrosión debido a la formación de una capa protectora de óxidos de cromo en la superficie del metal. Esta capa impide que se produzca una mayor degradación del material, lo que hace que los aceros inoxidables sean adecuados para su uso en ambientes químicos agresivos, altas temperaturas y condiciones de exposición al agua de mar. El acero inoxidable se utiliza en:
- Sistemas de transmisión en entornos marinos donde el agua contiene cloruros que aceleran la corrosión.
- Sistemas industriales de alta temperatura en los que el acero al carbono tradicional podría degradarse.
- Tanques y sistemas de refinerías que están expuestos a productos químicos agresivos.
La amplia aplicación de los aceros inoxidables en la industria petrolera se debe, principalmente, a su versatilidad y favorables propiedades mecánicas. Se utilizan en tuberías de transporte, tanques de almacenamiento y aparatos utilizados en procesos de refinería en los que el contacto con sustancias corrosivas es inevitable.
En el entorno marino, los aceros inoxidables suelen ser el material de construcción preferido porque resisten los cloruros, que aceleran la corrosión por picaduras. En sistemas de alta temperatura, como intercambiadores de calor y hornos de refinería, los aceros inoxidables mantienen su estabilidad y resistencia, lo que permite que se puedan utilizar durante largos periodos de tiempo sin riesgo de debilitar la estructura metálica.
A pesar de sus muchas ventajas, los aceros inoxidables pueden ser susceptibles al agrietamiento por corrosión bajo tensión y a la corrosión por picaduras, especialmente en presencia de iones cloruro agresivos. Por ello, en condiciones industriales extremas, se suele utilizar protección adicional, como inhibidores de la corrosión o revestimientos protectores para prolongar aún más la vida útil del material.
Aleaciones de níquel y titanio
Las aleaciones de níquel y titanio se encuentran entre los materiales más avanzados resistentes a la corrosión para su uso en las condiciones de funcionamiento más exigentes. Sus propiedades químicas y mecánicas únicas hacen que se utilicen en instalaciones que operan en temperaturas extremas, entornos ácidos y condiciones de alta presión.
Las aleaciones de níquel, como el Inconel, muestran una excepcional resistencia al sulfuro de hidrógeno (H₂S), a los ácidos y a las altas temperaturas, lo que las hace ideales para aplicaciones en pozos profundos y sistemas de refinería. Gracias a su estructura metalúrgica, también resisten la corrosión bajo tensión, lo que evita grietas y fallos en sistemas de aguas profundas.
Por su parte, el titanio y sus aleaciones se distinguen por su extrema resistencia a la corrosión en agua de mar, lo que los hace idóneos para su uso en estructuras marinas, plataformas petrolíferas y tuberías submarinas. Su baja densidad en comparación con otros metales permite construir estructuras ligeras pero resistentes que pueden funcionar en condiciones extremas durante muchos años sin mantenimiento.
Una de las principales limitaciones del uso de aleaciones de níquel y titanio es su elevado coste, que a menudo limita su uso a las aplicaciones más exigentes. Por este motivo, normalmente se utilizan soluciones híbridas, que combinan componentes fabricados con aleaciones resistentes a la corrosión con materiales más baratos, como el acero al carbono, que además están protegidos contra la degradación.
A pesar del elevado precio de las aleaciones de níquel y titanio, su fiabilidad y sus mínimas necesidades de mantenimiento las hacen reemplazables en zonas donde un fallo podría tener consecuencias medioambientales y económicas catastróficas.
La elección entre aceros inoxidables y aleaciones de níquel y titanio depende, principalmente, de las condiciones medioambientales y de las características específicas de la aplicación. Los aceros inoxidables ofrecen un equilibrio favorable entre precio y resistencia a la corrosión, mientras que las aleaciones de níquel y titanio proporcionan la máxima protección incluso en los entornos más extremos, pero a un coste operativo mucho mayor. La industria petrolera busca optimizar el uso de estos materiales al combinar sus ventajas para maximizar la durabilidad y eficiencia de las infraestructuras.
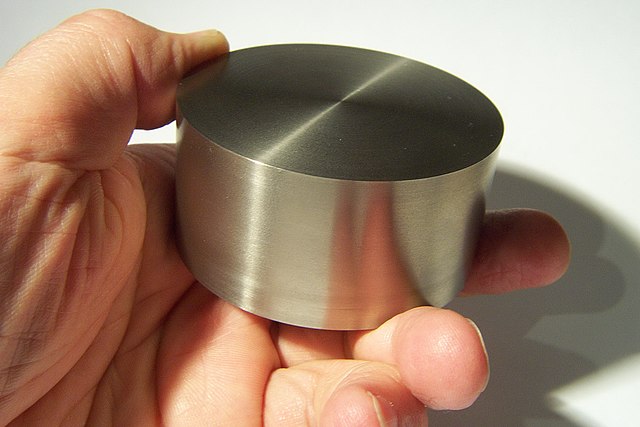
Comparación del acero al carbono y las aleaciones resistentes a la corrosión
La elección del material adecuado en la industria del petróleo y el gas depende de muchos factores, como la resistencia a la corrosión, la resistencia mecánica, los costes de producción y mantenimiento y las condiciones de funcionamiento. A pesar de su popularidad, el acero al carbono no siempre es la mejor opción, especialmente, en entornos químicamente agresivos donde se necesitan materiales más resistentes a la degradación.
La principal diferencia entre el acero al carbono y las aleaciones resistentes a la corrosión es su capacidad para soportar las duras condiciones de funcionamiento. El acero al carbono, aunque barato y ampliamente disponible, requiere protección adicional para evitar su rápida degradación. En cambio, las aleaciones resistentes a la corrosión, como el acero inoxidable y las aleaciones de níquel, presentan protección natural contra los agentes corrosivos, lo que prolonga considerablemente su vida útil y reduce el mantenimiento.
Resistencia a la corrosión en distintos entornos
Uno de los factores clave a la hora de seleccionar un material es su resistencia a la corrosión en un entorno operativo concreto. El acero al carbono muestra una alta susceptibilidad a la corrosión en presencia de humedad, oxígeno, sulfuro de hidrógeno (H₂S) y dióxido de carbono (CO₂). Especialmente en tuberías subterráneas e instalaciones en alta mar, donde el contacto con el agua de mar y las sales minerales es inevitable, son necesarios métodos de protección adicionales como revestimientos protectores, inhibidores de corrosión o protección catódica.
Los aceros inoxidables, el níquel y las aleaciones de titanio presentan una resistencia a la corrosión mucho mayor porque forman capas protectoras naturales que impiden que se produzcan más daños en la superficie del metal. Las aleaciones de níquel son especialmente eficaces en ambientes ácidos, mientras que el titanio funciona bien en instalaciones marinas donde la exposición intensa al agua de mar podría degradar rápidamente el acero al carbono.
Resistencia mecánica y durabilidad en condiciones operativas
Los materiales que se utilizan en la industria petrolera deben tener una resistencia mecánica adecuada, además de la resistencia a la corrosión. El acero al carbono ofrece alta resistencia a las cargas estáticas y dinámicas, lo que hace que se utilice a menudo en tuberías de transmisión y estructuras de soporte. Sin embargo, en entornos extremos, como pozos de aguas profundas o instalaciones sometidas a altas temperaturas y presiones, puede ser susceptible a la corrosión bajo tensión y al agrietamiento por corrosión, lo que limita su durabilidad.
Las aleaciones resistentes a la corrosión, especialmente las de níquel y titanio, conservan sus propiedades incluso en condiciones extremadamente duras. Son resistentes a las altas temperaturas, al sulfuro de hidrógeno y a los productos químicos agresivos, por lo que duran mucho más que el acero al carbono tradicional. Su resistencia mecánica también es mayor, lo que permite utilizar paredes de tuberías y componentes estructurales más finos sin riesgo de debilitar la estructura.
Costes de producción y mantenimiento
El coste de los materiales desempeña un papel clave en las decisiones de ingeniería de las infraestructuras petrolíferas. El acero al carbono es relativamente barato de producir, por lo que se utiliza ampliamente en tuberías y tanques de almacenamiento. Sin embargo, su susceptibilidad a la corrosión requiere una protección adicional, lo que genera costes asociados al mantenimiento, la reparación y la inspección.
Aunque las aleaciones resistentes a la corrosión son mucho más caras de producir, ofrecen menores costes de explotación porque no requieren inspecciones frecuentes ni costosas medidas preventivas. Su uso puede ahorrar dinero a largo plazo, especialmente, en instalaciones que operan en condiciones extremas con alto riesgo de fallos y degradación del material.
Ejemplos de aplicaciones en la industria petrolera
En la práctica, la elección del material depende de las características específicas de la aplicación. El acero al carbono con protecciones adicionales es el más utilizado en tuberías terrestres y subterráneas porque, en estas condiciones, el riesgo de corrosión puede controlarse eficazmente con revestimientos protectores y protección catódica.
En las instalaciones en alta mar, donde las condiciones son mucho más agresivas, se suelen utilizar aceros inoxidables y aleaciones de níquel y titanio. Estos materiales pueden funcionar durante décadas sin costosas reparaciones. Especialmente, en pozos profundos y tuberías que transportan productos químicos agresivos, los materiales con mayor resistencia son necesarios para garantizar la fiabilidad de las infraestructuras.
Aplicación práctica de ambos grupos de materiales
La elección entre el acero al carbono y las aleaciones resistentes a la corrosión depende de las condiciones de funcionamiento y de los requisitos de durabilidad y fiabilidad de la infraestructura. Ambos tipos de materiales se utilizan mucho en la industria petrolera, pero su eficacia depende del entorno específico en el que se empleen.
Uso del acero al carbono en tuberías y tanques
El acero al carbono es el material de construcción más utilizado en la industria petrolera, sobre todo, por su resistencia mecánica y bajo precio. Se utiliza principalmente en la construcción de tuberías de transporte de crudo y gas natural, así como en tanques de almacenamiento y estructuras de soporte.
El acero al carbono funciona bien en tuberías terrestres porque su susceptibilidad a la corrosión puede controlarse con protección catódica, revestimientos anticorrosión e inhibidores de corrosión. Las instalaciones subterráneas utilizan revestimientos aislantes de polietileno o epoxi para reducir el contacto del metal con la humedad y el suelo.
El acero al carbono de los depósitos de productos petrolíferos se protege con revestimientos protectores y se controla periódicamente para detectar pérdidas de material. En entornos con presencia de productos químicos agresivos, debe aplicarse protección adicional o aleaciones más resistentes a la corrosión en las zonas críticas de la estructura.
Aleaciones resistentes a la corrosión en instalaciones marinas y entornos ácidos
En entornos en los que el acero al carbono se degrada rápidamente, se utilizan aceros inoxidables y aleaciones de níquel y titanio. Estos materiales son muy resistentes a la corrosión y a temperaturas y presiones extremas. Algunos ejemplos de estos entornos son las plataformas de perforación, las tuberías submarinas y las instalaciones que transportan productos químicos agresivos.
En las plataformas marinas, los aceros inoxidables se utilizan en los sistemas de tuberías y estructuras de soporte expuestas al agua de mar y a temperaturas variables. Los aceros inoxidables que contienen molibdeno y níquel, que protegen el material de las picaduras y las fisuras por corrosión bajo tensión, funcionan especialmente bien en estas condiciones.
Las tuberías de alta mar suelen utilizar aleaciones de titanio, que se caracterizan por su resistencia al agua de mar y su bajo peso propio, lo que facilita su instalación y transporte. Gracias a su durabilidad, las tuberías de titanio pueden funcionar durante décadas sin necesidad de mucho mantenimiento.
El acero al carbono tradicional se degrada rápidamente por corrosión de sulfuro y dióxido en entornos ácidos, donde están presentes H₂S y CO₂. En estos casos, se utilizan aleaciones de níquel como el Inconel para ofrecer protección contra los productos químicos agresivos y resistir el agrietamiento por corrosión bajo tensión.
Uso de materiales híbridos
Debido a las diferencias de coste y propiedades, en la práctica de la ingeniería se utilizan, a menudo, soluciones híbridas. Se trata de combinar acero al carbono con materiales resistentes a la corrosión en las zonas más vulnerables a la degradación.
En los oleoductos, se pueden encontrar sistemas en los que el interior de las tuberías se recubre con una capa de aleación resistente a la corrosión, mientras que la estructura exterior sigue siendo de acero al carbono. Este enfoque permite reducir costes al tiempo que garantiza una gran durabilidad de los componentes expuestos a sustancias agresivas.
Del mismo modo, los tanques de almacenamiento utilizan revestimientos de aleación de níquel y titanio en los puntos de contacto con los productos químicos, mientras que otros componentes estructurales son de acero al carbono. Así se consigue un diseño duradero y económicamente viable.
Aleaciones resistentes a la corrosión en la industria petrolera – resumen
La elección de los materiales en la industria petrolera afecta a la durabilidad de las infraestructuras, la seguridad y los costes de explotación. El acero al carbono, aunque barato y muy utilizado, requiere una protección adicional contra la corrosión. Las aleaciones resistentes a la corrosión, como los aceros inoxidables, al níquel y al titanio, ofrecen una mayor durabilidad, pero tienen un coste más elevado.
La industria petrolera está desarrollando revestimientos modernos, sistemas de control y nuevas aleaciones metálicas para mejorar la resistencia a la corrosión y optimizar los costes. Cada vez se utilizan más soluciones híbridas, que combinan las ventajas económicas del acero al carbono con la durabilidad de las aleaciones resistentes a la corrosión.
El artículo se basa en el libro Metallurgy and Corrosion Control in Oil and Gas Production, de Robert Heidersbach.