Przyczyny korozji w przemyśle naftowym i gazowym
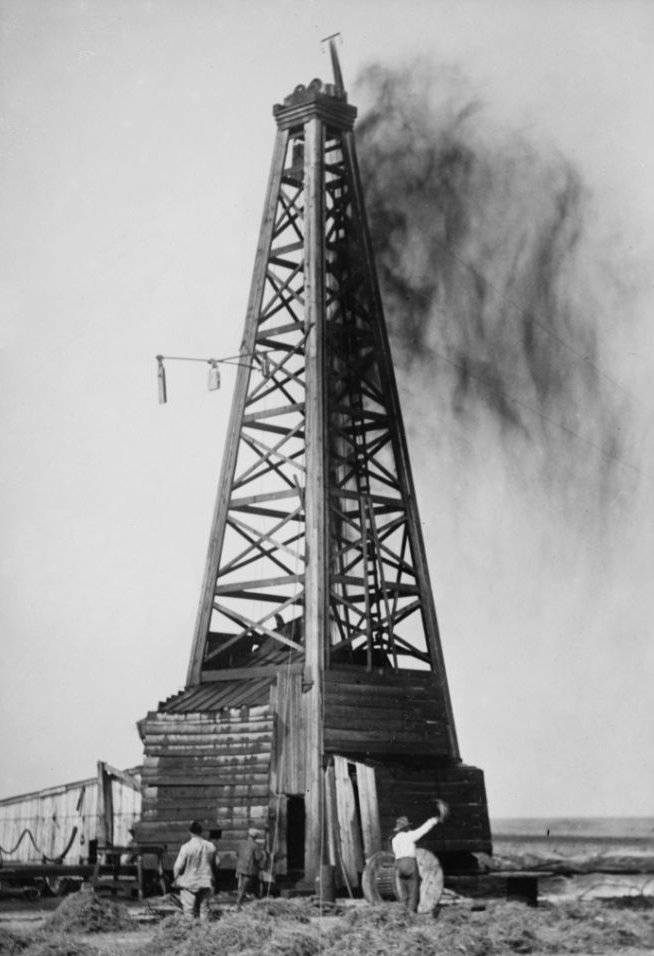
Spis treści
Korozja jest jednym z najpoważniejszych problemów w przemyśle naftowym i gazowym, wpływając zarówno na bezpieczeństwo, jak i koszty operacyjne. Występuje we wszystkich etapach eksploatacji – od wydobycia, przez transport, aż po magazynowanie surowców. Szacuje się, że coroczne straty związane z korozją w tej branży wynoszą miliardy dolarów, a niekontrolowane zjawiska korozyjne mogą prowadzić do katastrofalnych awarii infrastruktury.
Nieodpowiednie zarządzanie ryzykiem korozji może skutkować:
- Uszkodzeniem rurociągów i zbiorników magazynowych, co zwiększa ryzyko wycieków i eksplozji.
- Przerwami w produkcji i wysokimi kosztami napraw.
- Degradacją części metalowych w sprzęcie wiertniczym i rafineryjnym, co skraca jego żywotność.
- Zanieczyszczeniem środowiska, zwłaszcza w przypadku wycieków ropy lub gazu.
Zrozumienie przyczyn korozji jest kluczowe dla jej skutecznej kontroli i zapobiegania niepożądanym skutkom. W niniejszym artykule omówimy główne rodzaje korozji występujące w przemyśle naftowym i gazowym oraz czynniki, które ją przyspieszają.
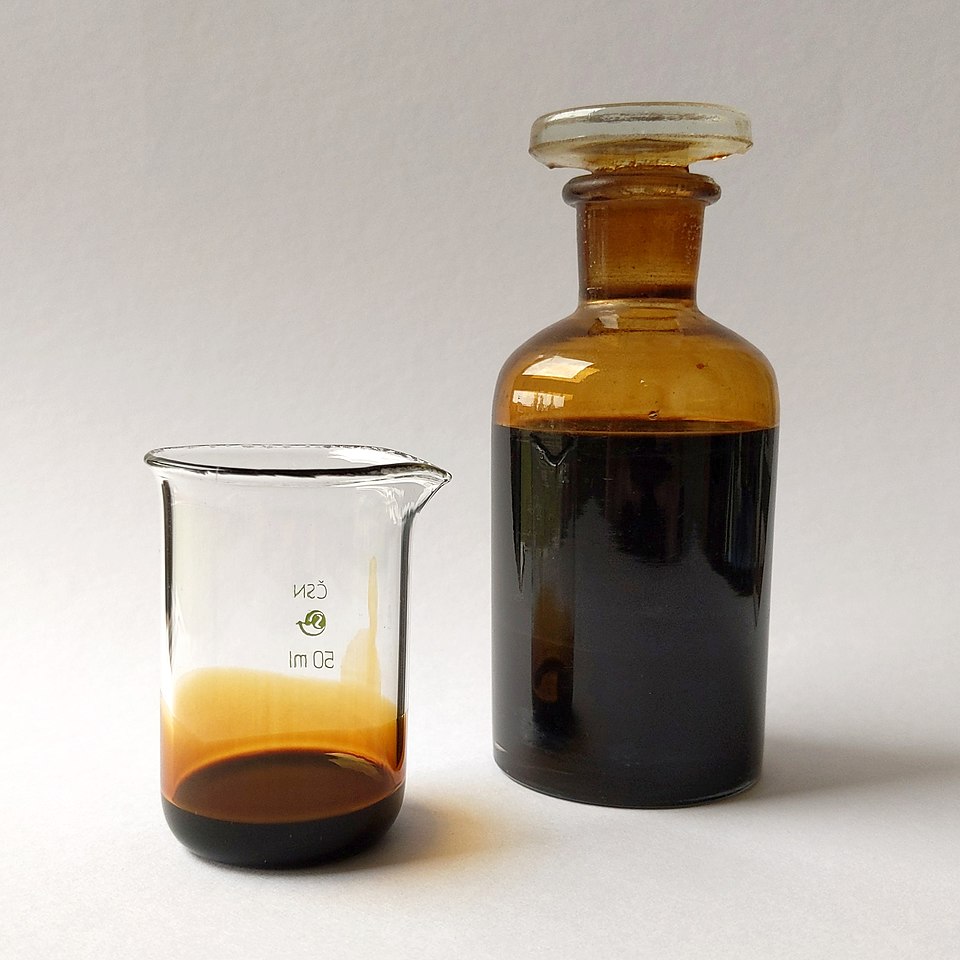
Rodzaje korozji w przemyśle naftowym i gazowym
Korozja w sektorze naftowym i gazowym może przybierać różne formy w zależności od warunków środowiskowych, składu chemicznego medium oraz właściwości materiałów. Rozróżnienie poszczególnych rodzajów korozji jest kluczowe dla skutecznej ochrony infrastruktury i przedłużenia jej żywotności.
- Korozja ogólna – jest to najczęściej występujący typ korozji, w którym metal ulega równomiernemu utlenianiu na całej powierzchni. Zachodzi w obecności tlenu i wilgoci, prowadząc do stopniowej degradacji materiału. W wyniku tego procesu zmniejsza się grubość ścian rurociągów i zbiorników, co obniża ich wytrzymałość. Choć ten rodzaj korozji jest stosunkowo łatwy do monitorowania, wymaga systematycznych działań prewencyjnych, takich jak powłoki ochronne i inhibitory.
- Korozja galwaniczna – występuje, gdy dwa różne metale są w kontakcie elektrycznym w środowisku przewodzącym. Metal mniej szlachetny (anoda) ulega przyspieszonemu utlenianiu, podczas gdy metal bardziej szlachetny (katoda) pozostaje chroniony. Zjawisko to jest szczególnie istotne w systemach rurociągowych i konstrukcjach offshore, gdzie łączenie różnych materiałów jest konieczne. Aby ograniczyć ten typ korozji, stosuje się odpowiedni dobór materiałów oraz izolację elektryczną między nimi.
- Korozja wżerowa – jest to lokalna forma korozji, w której metal ulega degradacji w niewielkich, ale głębokich punktach. Najczęściej zachodzi w obecności jonów chlorkowych, które przyczyniają się do powstawania wżerów, osłabiając strukturę materiału. W przeciwieństwie do korozji ogólnej, która rozkłada się równomiernie, korozja wżerowa może szybko prowadzić do perforacji elementów konstrukcyjnych. Stosowanie odpornych na korozję materiałów i inhibitorów jest kluczowe w jej ograniczaniu.
- Korozja pod napięciem (SCC – Stress Corrosion Cracking) – jest to proces, w którym materiał ulega pękaniu pod wpływem jednoczesnego działania naprężeń mechanicznych i agresywnego środowiska chemicznego. Pęknięcia mogą rozwijać się stopniowo, ale ich konsekwencje są poważne, ponieważ prowadzą do nagłych awarii sprzętu. SCC występuje szczególnie w rurociągach i zbiornikach pracujących pod wysokim ciśnieniem oraz w środowiskach zawierających siarkowodór.
- Korozja mikrobiologiczna (MIC – Microbially Influenced Corrosion) – powstaje na skutek działania mikroorganizmów, które przyspieszają degradację metalu poprzez produkcję agresywnych substancji chemicznych. Szczególnie problematyczna jest aktywność bakterii redukujących siarczany (SRB), które prowadzą do powstawania siarkowodoru, zwiększając ryzyko korozji i kruchości materiału. Zwalczanie tego rodzaju korozji wymaga regularnej dezynfekcji i stosowania biocydów.
- Korozja erozyjna – zachodzi w wyniku intensywnego przepływu cieczy lub gazu, szczególnie gdy medium zawiera cząstki stałe, takie jak piasek czy osady mineralne. Połączenie czynników mechanicznych i chemicznych powoduje stopniowe ścieranie warstwy ochronnej metalu, prowadząc do przyspieszonego zużycia elementów. Aby ograniczyć ten rodzaj korozji, stosuje się materiały o zwiększonej odporności na ścieranie oraz kontroluje parametry przepływu.
Kluczowe czynniki przyspieszające korozję
Korozja w przemyśle naftowym i gazowym zachodzi pod wpływem wielu czynników, które mogą znacząco przyspieszać tempo degradacji metali. Środowisko chemiczne, warunki fizyczne oraz dynamika przepływu medium mają kluczowy wpływ na rozwój procesów korozyjnych. Znajomość tych czynników jest niezbędna do skutecznego zapobiegania korozji i optymalnego doboru metod ochrony.
Obecność tlenu (O₂)
Tlen jest jednym z głównych czynników przyspieszających korozję, szczególnie w środowisku wodnym. W kontakcie z metalem powoduje jego utlenianie, prowadząc do powstawania produktów korozji, takich jak tlenki i rdza. Nawet niewielkie ilości tlenu mogą znacząco zwiększyć szybkość korozji, zwłaszcza gdy występują w rurociągach czy zbiornikach zawierających wodę lub wilgoć. Ograniczenie dostępu tlenu do powierzchni metalu poprzez uszczelnienia, powłoki ochronne oraz zastosowanie inhibitorów jest kluczowe dla redukcji tego typu korozji.
Obecność siarkowodoru (H₂S) i dwutlenku węgla (CO₂)
Siarkowodór (H₂S) i dwutlenek węgla (CO₂) to dwa najczęściej występujące gazy korozyjne w przemyśle naftowym. CO₂ („słodka korozja”) – w kontakcie z wodą tworzy kwas węglowy (H₂CO₃), który obniża pH i przyspiesza rozpuszczanie metalu, prowadząc do ubytków w rurociągach i zbiornikach. H₂S („kwaśna korozja”) – powoduje powstawanie siarczków żelaza (FeS), które mogą działać ochronnie, ale jednocześnie zwiększają ryzyko korozji pod napięciem i kruchości wodorowej. Wpływ tych gazów na korozję zależy od ich stężenia, temperatury oraz ciśnienia, co sprawia, że w agresywnych środowiskach konieczne jest stosowanie materiałów odpornych na działanie CO₂ i H₂S.

Wilgoć i obecność wody
Woda pełni kluczową rolę w większości procesów korozyjnych, ponieważ działa jako elektrolit, umożliwiający przepływ prądu między anodą a katodą na powierzchni metalu. W zależności od jej składu chemicznego może przyspieszać korozję w różnym stopniu.
- Świeża woda – zawiera tlen, co sprzyja utlenianiu metalu.
- Woda morska – bogata w jony chlorkowe (Cl⁻), które intensyfikują korozję wżerową.
- Woda złożowa – może zawierać siarczany, węglany oraz bakterie redukujące siarczany, prowadzące do korozji mikrobiologicznej.
Zarządzanie zawartością wody w systemach naftowych obejmuje jej separację, usuwanie związków korozyjnych oraz stosowanie inhibitorów.
Temperatura i ciśnienie
Wysoka temperatura i ciśnienie to jedne z kluczowych czynników wpływających na tempo i charakter procesów korozyjnych w przemyśle naftowym i gazowym. Ich oddziaływanie jest szczególnie istotne w środowiskach ekstremalnych, takich jak głębokie odwierty, wysokociśnieniowe rurociągi oraz instalacje offshore.
Temperatura bezpośrednio wpływa na szybkość reakcji chemicznych i elektrochemicznych prowadzących do korozji. Wzrost temperatury przyspiesza utlenianie metalu oraz reakcje z gazami korozyjnymi, zwiększając ich agresywność. Jednocześnie może powodować destabilizację warstw ochronnych, np. pasywnej warstwy tlenków na stalach nierdzewnych, co czyni metal bardziej podatnym na korozję. Podwyższona temperatura wpływa także na rozpuszczalność gazów w wodzie – CO₂ i H₂S mogą intensywniej reagować z wodą, tworząc agresywne kwasy, które atakują powierzchnie metalowe.
Wysoka temperatura może również prowadzić do rozkładu inhibitorów korozji, czyli substancji stosowanych w celu spowolnienia procesu degradacji metalu. Niektóre inhibitory tracą swoje właściwości ochronne w ekstremalnych warunkach termicznych, co wymaga stosowania bardziej odpornych związków chemicznych. W określonych warunkach mogą występować także specyficzne typy korozji, takie jak korozja wysokotemperaturowa, czyli utlenianie metalu bez obecności ciekłej wody, występujące np. w kotłach i wymiennikach ciepła. Inny typ to korozja siarczkowa, pojawiająca się w środowiskach bogatych w siarkę, co jest szczególnie istotne w procesach rafinacji ropy naftowej.
Podwyższona temperatura może również sprzyjać korozji naprężeniowej (SCC), czyli powstawaniu pęknięć w strukturze materiału w wyniku połączenia naprężeń mechanicznych i agresywnego środowiska chemicznego. Tego rodzaju uszkodzenia są szczególnie niebezpieczne, ponieważ mogą rozwijać się niezauważalnie, prowadząc do nagłej awarii.
Ciśnienie wpływa na intensywność korozji poprzez zmianę właściwości fizykochemicznych gazów i cieczy obecnych w instalacji. Wysokie ciśnienie zwiększa rozpuszczalność CO₂ i H₂S w wodzie, co sprawia, że medium staje się bardziej agresywne wobec materiałów konstrukcyjnych. Gazy te, w połączeniu z wilgocią, tworzą kwasy przyspieszające degradację metalu, co jest szczególnie problematyczne w instalacjach eksploatowanych w warunkach wysokiego ciśnienia.
Kolejnym istotnym czynnikiem jest wpływ wysokiego ciśnienia na trwałość materiałów. W głębokich odwiertach oraz rurociągach przesyłowych ekstremalne ciśnienie powoduje intensywniejsze oddziaływanie chemiczne i mechaniczne na powierzchnie metalowe. Może to prowadzić do osłabienia struktury materiału oraz zwiększenia podatności na zjawisko kawitacji – powstawania i zapadania się pęcherzyków pary, które w wyniku gwałtownych uderzeń mogą uszkadzać powierzchnię metalu, przyspieszając jego degradację.
Przykłady typowych miejsc narażonych na korozję
Korozja w przemyśle naftowym i gazowym występuje w wielu elementach infrastruktury, zwłaszcza tam, gdzie metale są narażone na agresywne środowiska chemiczne, wysokie ciśnienie i temperaturę. Jej skutki mogą prowadzić do uszkodzeń rurociągów, zbiorników i sprzętu technologicznego, powodując kosztowne przestoje i zagrożenia dla bezpieczeństwa.
Rurociągi, zbiorniki i instalacje przesyłowe
Rurociągi i zbiorniki magazynowe należą do najczęściej korodujących elementów infrastruktury, ponieważ ich ściany mają ciągły kontakt z medium zawierającym wodę, CO₂, H₂S oraz zanieczyszczenia mechaniczne. Wewnętrzna korozja może prowadzić do wżerów i perforacji, natomiast zewnętrzna, spowodowana działaniem wilgoci, tlenu i prądów błądzących, osłabia strukturę materiału. Szczególnie zagrożone są rurociągi podziemne i zbiorniki narażone na zmiany temperatury, które powodują skraplanie się wody i rozwój korozji atmosferycznej. Zapobieganie korozji opiera się na ochronie katodowej, stosowaniu inhibitorów oraz powłok ochronnych.
Infrastruktura offshore i sprzęt wiertniczy
Platformy wiertnicze oraz rurociągi podmorskie funkcjonują w niezwykle agresywnym środowisku, gdzie słona woda, silne prądy morskie i wysoka wilgotność przyspieszają korozję. Szczególnie niebezpieczna jest korozja galwaniczna, powstająca na styku różnych metali, oraz korozja erozyjna, która prowadzi do uszkodzeń powierzchni pod wpływem silnego przepływu wody i zawieszonych w niej cząstek. Sprzęt wiertniczy, w tym rury i zawory, jest dodatkowo narażony na korozję naprężeniową i kruchość wodorową, szczególnie w obecności H₂S. Aby ograniczyć degradację, stosuje się materiały odporne na wysokie ciśnienie, anodową ochronę katodową oraz specjalistyczne powłoki antykorozyjne.
Systemy chłodzenia i wymienniki ciepła
Instalacje chłodzące i wymienniki ciepła są podatne na korozję wynikającą z wysokich temperatur, zmiennych warunków pracy i agresywnych chemikaliów stosowanych w procesach technologicznych. Do najczęstszych problemów należą korozja erozyjna, powodowana szybkim przepływem medium, korozja mikrobiologiczna, związana z rozwojem bakterii, oraz korozja pod napięciem, która osłabia metalowe elementy pod wpływem naprężeń mechanicznych i środowiskowych. Odpowiedni dobór materiałów, regularna kontrola składu wody oraz cykliczne czyszczenie systemów to kluczowe działania prewencyjne.
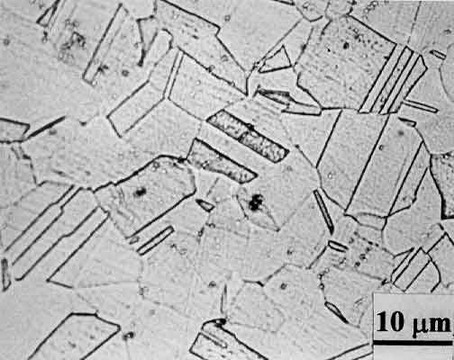
Skutki korozji w przemyśle naftowym i gazowym
Korozja w sektorze naftowym i gazowym ma poważne konsekwencje zarówno ekonomiczne, jak i środowiskowe oraz operacyjne. Degradacja infrastruktury prowadzi do nieplanowanych przestojów, zwiększonych kosztów utrzymania oraz zagrożenia dla bezpieczeństwa ludzi i środowiska.
Zwiększone koszty operacyjne i konserwacyjne
Korozja jest jednym z głównych czynników wpływających na koszty eksploatacyjne w przemyśle naftowym i gazowym. Naprawy uszkodzonych rurociągów, wymiana skorodowanych komponentów oraz wdrażanie systemów ochrony przed korozją generują ogromne wydatki. Dodatkowo, częste inspekcje i monitorowanie stanu infrastruktury wymagają znacznych nakładów finansowych. W skali globalnej roczne koszty związane z korozją w tej branży sięgają miliardów dolarów.
Postępująca korozja może prowadzić do awarii sprzętu, wycieków oraz uszkodzeń rurociągów i zbiorników, co skutkuje koniecznością zatrzymania produkcji. Przerwy w eksploatacji nie tylko zmniejszają wydajność operacyjną, ale również generują dodatkowe straty finansowe związane z naprawami oraz opóźnieniami w dostawach. W skrajnych przypadkach korozja może spowodować całkowite wyłączenie infrastruktury, co jest szczególnie problematyczne w przypadku instalacji offshore i odwiertów głębinowych.
Korozja infrastruktury naftowej i gazowej może prowadzić do katastrofalnych awarii, takich jak pęknięcia rurociągów, wycieki substancji palnych oraz eksplozje, które stanowią bezpośrednie zagrożenie dla życia i zdrowia pracowników oraz okolicznych społeczności. Wyciek gazu czy ropy może spowodować pożary, a w ekstremalnych przypadkach – eksplozje na platformach wiertniczych lub w zakładach rafineryjnych. Odpowiednia prewencja i kontrola korozji jest kluczowa dla minimalizacji ryzyka wypadków.
Wpływ na środowisko naturalne
Korozja prowadząca do wycieków ropy naftowej, gazu lub substancji chemicznych ma katastrofalne skutki dla ekosystemów wodnych i lądowych. Przedostanie się tych substancji do gleby i wód gruntowych powoduje ich skażenie, które może utrzymywać się przez dekady. Wyciek ropy do oceanów powoduje ogromne straty w populacjach morskich oraz niszczenie siedlisk przybrzeżnych. Incydenty ekologiczne wynikające z awarii spowodowanych korozją często prowadzą do wielomilionowych odszkodowań i sankcji dla firm odpowiedzialnych za wycieki.
Jednym z najbardziej znaczących przypadków korozji prowadzącej do katastrofy ekologicznej był wyciek ropy naftowej w Prudhoe Bay na Alasce w 2006 roku. Rurociąg transportujący ropę uległ perforacji w wyniku korozji wewnętrznej, spowodowanej nagromadzeniem osadów i niewystarczającą kontrolą inhibitorów korozji. Przez uszkodzenie infrastruktury do tundry arktycznej wyciekło ponad 200 tysięcy galonów ropy, powodując skażenie obszaru o powierzchni kilku hektarów. Wyciek ten miał katastrofalny wpływ na lokalny ekosystem, niszcząc siedliska zwierząt i prowadząc do długotrwałych konsekwencji ekologicznych. Konieczna była kosztowna operacja dekontaminacji, a zarządzająca infrastrukturą firma została obciążona karami finansowymi i zmuszona do przeprowadzenia modernizacji infrastruktury.
Strategie minimalizacji i zapobiegania korozji
Korozja w przemyśle naftowym i gazowym jest nieunikniona, ale może być skutecznie kontrolowana i ograniczana poprzez odpowiednie strategie ochrony. Skuteczne zarządzanie ryzykiem korozji pozwala nie tylko na wydłużenie żywotności infrastruktury, ale także na zmniejszenie kosztów operacyjnych i ograniczenie ryzyka awarii.
Ochrona katodowa
Jedną z najskuteczniejszych metod ochrony metali przed korozją jest ochrona katodowa, stosowana głównie w rurociągach, zbiornikach i konstrukcjach podziemnych oraz offshore. Polega ona na zastosowaniu prądu elektrycznego lub aktywnych anod w celu zmniejszenia potencjału elektrochemicznego chronionego metalu, dzięki czemu proces korozji zostaje zahamowany.
Istnieją dwa główne rodzaje ochrony katodowej:
- Ochrona galwaniczna (z użyciem anod protektorowych) – wykorzystuje metale o niższym potencjale elektrochemicznym, takie jak cynk, magnez czy aluminium, które ulegają kontrolowanemu zużyciu, chroniąc tym samym właściwy materiał konstrukcyjny.
- Ochrona katodowa z zastosowaniem prądu zewnętrznego (ICCP – Impressed Current Cathodic Protection) – polega na podłączeniu źródła prądu stałego do chronionej konstrukcji, co zapobiega korozji poprzez kontrolowane dostarczanie elektronów.
Systemy ochrony katodowej są niezbędne w rurociągach przesyłowych, konstrukcjach offshore oraz zbiornikach magazynowych, gdzie korozja jest szczególnie intensywna.
Zastosowanie inhibitorów korozji
Inhibitory korozji to specjalne substancje chemiczne dodawane do medium roboczego w celu spowolnienia lub całkowitego zahamowania reakcji korozyjnych. Działają one poprzez tworzenie warstwy ochronnej na powierzchni metalu lub modyfikację właściwości korozyjnych środowiska.
Podział inhibitorów korozji obejmuje:
- Inhibitory anodowe – ograniczają szybkość reakcji utleniania metalu.
- Inhibitory katodowe – zmniejszają szybkość reakcji redukcji tlenu lub wodoru.
- Inhibitory mieszane – działają jednocześnie na anodzie i katodzie, spowalniając cały proces elektrochemiczny.
Inhibitory korozji są szeroko stosowane w przemyśle naftowym i gazowym, szczególnie w rurociągach, systemach przesyłu wody oraz w urządzeniach wiertniczych, gdzie ochrona mechaniczna lub katodowa jest trudna do wdrożenia.
Wybór odpornych materiałów i powłok ochronnych
Odpowiedni dobór materiałów ma kluczowe znaczenie dla ograniczenia ryzyka korozji. W środowiskach o wysokiej agresywności chemicznej stosuje się stale nierdzewne, stopy niklu, stopowe stale wysokowytrzymałe oraz tytan, które wykazują podwyższoną odporność na korozję.
Dodatkową ochronę stanowią powłoki antykorozyjne, które działają jako bariera między metalem a agresywnym środowiskiem. Wśród najczęściej stosowanych rozwiązań znajdują się:
- Powłoki epoksydowe i poliuretanowe – stosowane w rurociągach i zbiornikach.
- Metalowe powłoki ochronne (np. cynkowe, aluminiowe) – zapewniają ochronę katodową przez długi czas.
- Ceramiczne i kompozytowe bariery ochronne – wykorzystywane w środowiskach ekstremalnych, takich jak platformy wiertnicze i instalacje rafineryjne.
Przyczyny korozji w przemyśle naftowym i gazowym – podsumowanie
Korozja w przemyśle naftowym i gazowym prowadzi do wysokich kosztów, zagrożeń bezpieczeństwa i szkód środowiskowych. Skuteczna ochrona infrastruktury wymaga zrozumienia mechanizmów korozji oraz wdrożenia odpowiednich strategii prewencyjnych, takich jak ochrona katodowa, inhibitory korozji, powłoki ochronne i regularny monitoring.
Zapobieganie korozji jest kluczowe dla zwiększenia trwałości infrastruktury i minimalizacji ryzyka awarii. Nowoczesne technologie pozwalają na coraz skuteczniejszą kontrolę tego procesu, co jest istotne w kontekście rosnących wymagań operacyjnych i ekologicznych.
Artykuł ten powstał na podstawie książki „Metallurgy and Corrosion Control in Oil and Gas Production” autorstwa Roberta Heidersbacha.