Metodi di protezione catodica negli oleodotti
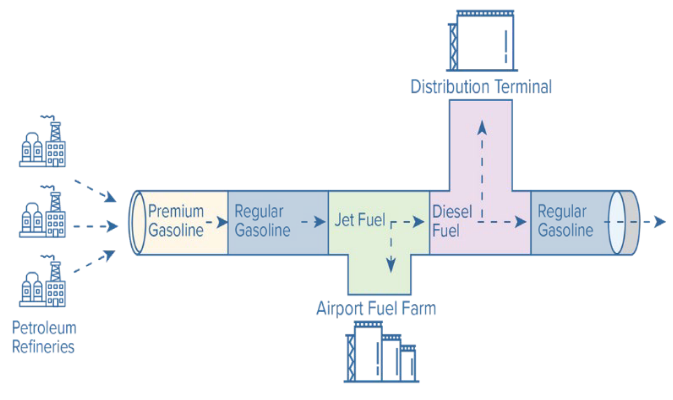
Indice
La corrosione è uno dei problemi più gravi nel funzionamento degli oleodotti. Essa provoca la diminuzione della resistenza strutturale, fuoriuscite di petrolio e guasti con conseguenti costose riparazioni, che rappresentano un rischio sia economico che ambientale. Un’adeguata protezione delle infrastrutture di trasmissione è fondamentale per garantire il funzionamento sicuro a lungo termine degli oleodotti.
Uno dei metodi più efficaci per prevenire la corrosione nelle condutture è la protezione catodica. Questa tecnologia elettrochimica prevede l’erogazione controllata di corrente elettrica alla conduttura, che riduce efficacemente il processo di ossidazione del metallo. Questo metodo viene utilizzato sia nelle condutture sotterranee che in quelle sottomarine, dove la corrosione è particolarmente intensa.
In questo articolo verranno discussi i principi della protezione catodica, i suoi tipi, i componenti del sistema e l’applicazione pratica nell’industria petrolifera. Analizzeremo inoltre i vantaggi di questa tecnologia e le sfide nell’implementazione.
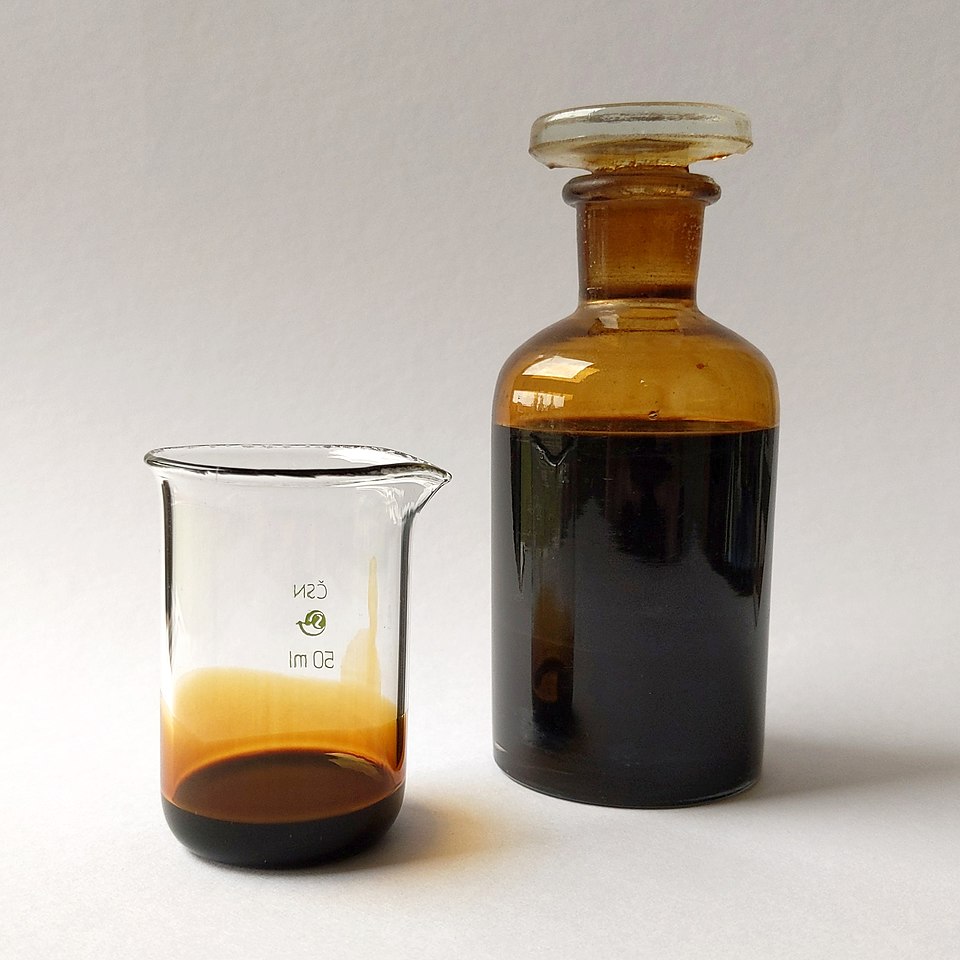
Principio della protezione catodica
Meccanismo della corrosione elettrochimica nelle condutture
La corrosione elettrochimica nelle condutture metalliche deriva dalla differenza di potenziale elettrico tra le diverse parti della struttura. In presenza di umidità ed elettroliti (ad esempio, suolo o acqua di mare), il metallo della conduttura inizia ad agire come una cella galvanica, dove si verificano:
- Anodo – l’area in cui si verifica l’ossidazione e la degradazione del metallo;
- Catodo – l’area in cui gli ioni provenienti dall’ambiente vengono ridotti e il metallo non si corrode.
Questo processo porta a una graduale decomposizione della conduttura, soprattutto nelle aree esposte ad agenti aggressivi come composti dello zolfo, ossigeno o cloruri.
Come funziona la protezione catodica?
La protezione catodica consiste nell’indirizzare la reazione di corrosione in modo che la conduttura agisca da catodo, eliminando la degradazione del metallo. A tal fine, una fonte esterna di elettroni neutralizza il potenziale elettrochimico della conduttura e ne impedisce l’ossidazione. In pratica, la protezione catodica agisce:
- Abbassando il potenziale elettrochimico del metallo al di sotto del livello in cui si verifica la corrosione;
- Fornendo elettroni esterni alla struttura della conduttura, impedendo così al metallo di ossidarsi;
- Usando anodi sacrificali o di sistemi a corrente continua (ICCP) per controllare il flusso di corrente protettiva.
Grazie all’uso della protezione catodica, i processi di corrosione sono significativamente rallentati o completamente inibiti, consentendo una protezione a lungo termine delle infrastrutture di trasmissione.
Componenti principali del sistema di protezione catodica
Il sistema di protezione catodica è costituito da diversi componenti chiave:
- Anodi – responsabili della fornitura di corrente protettiva e dell’usura graduale al posto della conduttura;
- Sorgenti di corrente continua – utilizzate nella protezione ICCP per l’erogazione controllata di elettroni alla conduttura;
- Sensori e sonde di riferimento – per monitorare il livello di protezione e il potenziale elettrochimico dell’impianto;
- Cavi e sistemi di connessione – per garantire una trasmissione efficace della corrente di protezione.
Questi sistemi devono essere controllati e mantenuti regolarmente per garantirne l’efficacia e l’adattamento alle condizioni operative.
Tipi di protezione catodica
La protezione catodica degli oleodotti può essere realizzata in due modi: utilizzando anodi galvanici (sacrificali) o fornendo corrente continua da una fonte esterna (ICCP – Impressed Current Cathodic Protection). La scelta del metodo appropriato dipende dalle condizioni ambientali, dalla lunghezza della conduttura e dalla conducibilità elettrica del mezzo circostante.
Protezione catodica galvanica
La protezione galvanica prevede l’uso di anodi sacrificali, costituiti da metalli con un potenziale elettrochimico inferiore a quello del materiale della conduttura. Di conseguenza, l’anodo subisce una corrosione controllata, proteggendo il metallo della conduttura dal degrado.
Nei sistemi di protezione galvanica, gli anodi sono solitamente realizzati in zinco, magnesio o alluminio. Questi materiali hanno un potenziale elettrochimico più elevato rispetto all’acciaio delle condutture, per cui donano elettroni alla struttura protetta e si consumano gradualmente.
Tra i vantaggi di questo metodo ricordiamo l’assenza di una fonte di alimentazione esterna, che semplifica l’installazione, buone prestazioni in ambienti a bassa resistività come l’acqua di mare, e minimi requisiti di manutenzione perché il sistema funziona passivamente.
Sfortunatamente, come ogni metodo, anche questo presenta dei limiti: durata più breve degli anodi che si consumano gradualmente e devono essere sostituiti, e minore efficacia in ambienti ad alta resistività (ad esempio, terreni asciutti), dove la corrente protettiva si diffonde più debolmente.
Protezione catodica a corrente esterna (ICCP)
La protezione catodica a corrente impressa (ICCP) utilizza una sorgente esterna di corrente continua per fornire elettroni alla conduttura, eliminando il rischio di corrosione. Si tratta di un metodo più avanzato utilizzato principalmente in tubazioni lunghe e in ambienti ad alta resistività.
Il sistema ICCP utilizza anodi insolubili realizzati con materiali resistenti al degrado, come il titanio rivestito con ossidi metallici misti (MMO), grafite o silicio metallurgico. Il raddrizzatore che fornisce tensione agli anodi genera una corrente di protezione, costringendo gli elettroni a fluire nella conduttura e proteggendola dall’ossidazione.
I vantaggi di questo metodo sono: protezione a lungo termine perché gli anodi ICCP non si consumano così rapidamente come gli anodi galvanici, intensità di protezione regolabile che consente di adattare il livello di protezione alle mutevoli condizioni operative e la capacità di proteggere condotte di grandi dimensioni e installazioni offshore dove gli anodi galvanici sarebbero insufficienti.
Limitazioni della protezione ICCP: richiede energia elettrica, il che significa costi operativi aggiuntivi, protezione contro le interruzioni di corrente e installazione più complicata che richiede il monitoraggio e la regolazione periodica del sistema.
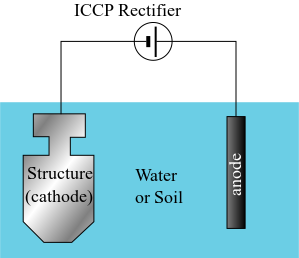
Componenti principali di un sistema di protezione catodica
Un sistema di protezione catodica è costituito da diversi componenti chiave che, insieme, proteggono efficacemente le condutture dalla corrosione. La scelta corretta e la manutenzione regolare sono fondamentali per la longevità dell’infrastruttura di trasmissione.
Anodi
Gli anodi nei sistemi di protezione catodica agiscono come fonte di elettroni che contrastano il processo di corrosione. A seconda del tipo di protezione catodica, vengono utilizzati diversi tipi di anodi:
- Anodi galvanici (sacrificali): sono costituiti da metalli elettrochimicamente più attivi dell’acciaio delle condutture. Gli anodi più comuni sono costituiti da zinco, magnesio e alluminio, che si dissolvono gradualmente, cedendo elettroni all’impianto protetto. Sono utilizzati principalmente nelle condotte sotterranee e nelle installazioni marine.
- Anodi insolubili (ICCP): utilizzati nei sistemi di protezione catodica a corrente esterna. Sono realizzati in materiali resistenti alla corrosione come il titanio e rivestiti con ossidi metallici misti (MMO), grafite e silicio metallurgico. Il loro compito è quello di condurre la corrente di protezione senza usurarsi, fornendo una protezione a lungo termine per le grandi installazioni.
La corretta selezione degli anodi è fondamentale per l’efficacia della protezione catodica. Fattori come l’ambiente operativo, la lunghezza della conduttura e la conducibilità elettrica del mezzo determinano la scelta di un particolare tipo di anodo.
Fonti di alimentazione
Nei sistemi di protezione catodica ICCP, una fonte di alimentazione in corrente continua è un componente indispensabile che consente l’erogazione controllata di elettroni alla conduttura. Esistono due tipi fondamentali di fonti di alimentazione:
- Raddrizzatori di corrente continua: dispositivi che convertono la corrente alternata in corrente continua di una determinata tensione e amperaggio. Permettono di adattare con precisione il livello di protezione catodica alle condizioni operative.
- Alimentazione da fonti di energia rinnovabili: in località lontane dalla rete elettrica, vengono utilizzati sistemi di alimentazione basati su pannelli solari e turbine eoliche, che consentono l’indipendenza energetica e costi di gestione inferiori.
Il corretto funzionamento di un sistema di protezione catodica ICCP richiede un continuo monitoraggio della tensione e della corrente per garantire livelli ottimali di protezione dalla corrosione.
Monitoraggio e controllo del sistema
Per garantire l’efficacia della protezione catodica, è necessario controllare costantemente il potenziale elettrochimico della conduttura. A tal fine, vengono utilizzate diverse tecnologie di monitoraggio:
- Sonde di riferimento (elettrodi di misura): collocate in prossimità dell’impianto protetto, consentono di misurare il potenziale della conduttura rispetto all’ambiente. Gli elettrodi più comunemente utilizzati sono Cu/CuSO₄ (solfato di rame/rame) per le condutture interrate e Ag/AgCl (cloruro di argento/argento) per le installazioni marine.
- Sensori di corrente di corrosione: rilevano le anomalie nel flusso di corrente di protezione, consentendo una risposta rapida in caso di guasto del sistema.
- Sistemi di monitoraggio remoto: utilizzano le tecnologie IoT e di telemetria per tenere traccia dei parametri della protezione catodica in tempo reale e rispondere a potenziali minacce.
Eseguendo ispezioni e monitoraggi periodici è possibile individuare rapidamente potenziali guasti e di regolare i parametri del sistema, aumentando l’efficienza della protezione e riducendo i costi di manutenzione.
Cavi e sistemi di connessione
Nei sistemi di protezione catodica è estremamente importante disporre di cavi e collegamenti elettrici adeguati per far fluire efficacemente la corrente di protezione. I componenti chiave del sistema includono: cavi resistenti alla corrosione e ai danni meccanici e ricoperti da uno strato isolante che li protegga dall’umidità e dagli agenti chimici, connettori anodici e catodici che devono essere adeguatamente isolati per ridurre al minimo la perdita di corrente, e cassette di prova e punti di prova che consentono di verificare l’efficacia del sistema in vari punti della conduttura.
Collegamenti non eseguiti correttamente possono portare alla perdita di corrente protettiva e a una protezione dalla corrosione inefficace, pertanto la scelta e la qualità dell’impianto elettrico sono fondamentali per l’efficacia dell’intero sistema. Un sistema di protezione catodica è costituito da molti componenti cooperanti il cui corretto funzionamento garantisce un’efficace protezione dalla corrosione. Anodi, fonti di alimentazione, sistemi di monitoraggio, cavi e connessioni devono essere dimensionati correttamente e ispezionati regolarmente per garantire la protezione a lungo termine degli oleodotti.
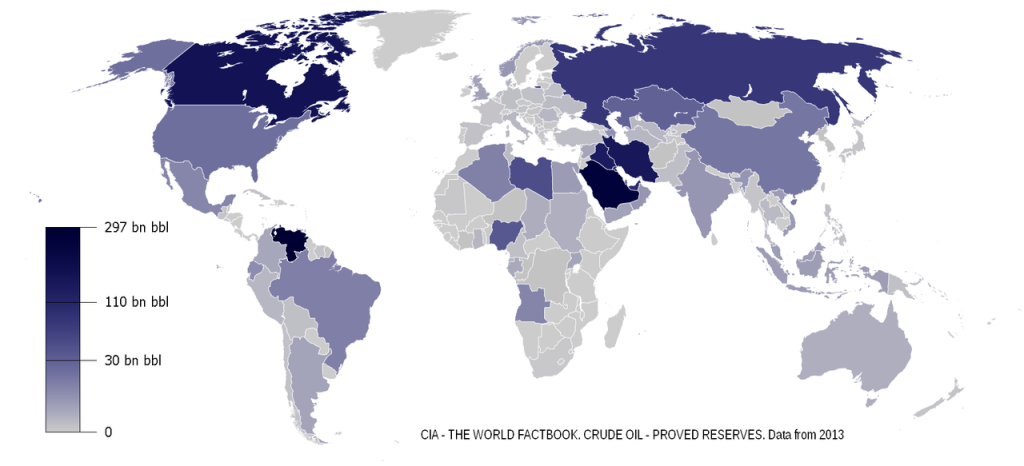
Applicazione pratica della protezione catodica negli oleodotti
La protezione catodica è uno dei metodi più utilizzati per la protezione dalla corrosione negli oleodotti. La sua efficacia è stata dimostrata in molti progetti in tutto il mondo, sia in installazioni sotterranee che sottomarine. In questa sezione, discuteremo i casi d’uso reali della protezione catodica, le sfide alla sua implementazione e le principali normative del settore.
Applicazione della protezione catodica in varie condizioni
Negli oleodotti che trasportano petrolio greggio e prodotti derivati, la protezione catodica viene utilizzata per prevenire la corrosione causata dal contatto del metallo con il terreno umido e le acque sotterranee. In ambienti con bassa resistività del terreno (ad esempio, aree umide e paludose), si utilizzano anodi galvanici, mentre in aree con alta resistività (ad esempio, aree desertiche, terreni asciutti), è necessario utilizzare una protezione ICCP perché il flusso naturale di corrente protettiva è limitato.
Le condotte di trasmissione offshore sono esposte ad acqua di mare forte, che è un elettrolita potente che accelera i processi di corrosione. In questo tipo di ambiente, la protezione catodica galvanica con anodi di alluminio o zinco è la soluzione standard, in quanto fornisce una protezione duratura senza la necessità di un’alimentazione esterna. Per le grandi strutture offshore, come le piattaforme petrolifere e i terminali marini, è più comune utilizzare sistemi ICCP che consentono un controllo preciso del livello di protezione.
Sfide nell’implementazione della protezione catodica
Nonostante l’efficacia della protezione catodica, la sua attuazione è associata a varie sfide tecniche e operative. Tra i problemi più comuni vi sono:
- Progettazione inadeguata del sistema: il posizionamento improprio degli anodi o l’errata definizione dei parametri della corrente di protezione possono portare a una protezione inefficace della conduttura o addirittura accelerare i danni locali.
- Variabilità delle condizioni ambientali: differenze nella composizione del terreno, nella salinità dell’acqua o nella temperatura possono richiedere una regolazione continua del sistema di protezione ICCP per adeguare il livello di protezione alle condizioni operative.
- Interferenza con altri impianti: in aree con un gran numero di condutture, cavi o infrastrutture elettriche, possono verificarsi interferenze con il flusso di corrente di protezione, che richiedono uno studio dettagliato e l’ottimizzazione del sistema.
- Manutenzione e monitoraggio: i sistemi di protezione catodica richiedono ispezioni e misurazioni regolari per garantire l’efficacia a lungo termine. La mancanza di un monitoraggio adeguato può portare a guasti inosservati e a un più rapido degrado della conduttura.
Norme e regolamenti per la protezione catodica
La protezione catodica nell’industria petrolifera è strettamente regolata da norme e standard internazionali che specificano i requisiti per la progettazione, l’installazione e il monitoraggio dei sistemi di protezione. Tra gli standard più importanti vi sono i seguenti:
- NACE SP0169 – standard internazionale sviluppato dalla National Association of Corrosion Engineers (NACE) che specifica le regole per la progettazione e la manutenzione dei sistemi di protezione catodica per le condutture interrate.
- ISO 15589-1 – standard internazionale che disciplina la protezione catodica delle gasdotti in acciaio, considerando sia i sistemi ICCP che gli anodi galvanici.
- DNV-RP-F103 – linee guida per la protezione catodica di condotte e strutture sottomarine applicabili all’industria offshore.
- EN 12954 – standard europeo che specifica i requisiti per la protezione catodica delle condotte che trasportano idrocarburi e acqua.
La conformità a queste norme è fondamentale per garantire sicurezza operativa e un’efficace protezione dalla corrosione.
Vantaggi della protezione catodica
La protezione catodica svolge un ruolo fondamentale nella protezione degli oleodotti dalla corrosione, garantendone la durata e l’affidabilità a lungo termine. Può efficacemente ridurre il rischio di guasti, ridurre i costi di manutenzione e soddisfare i requisiti normativi, rendendola uno dei metodi più convenienti per proteggere le infrastrutture di trasmissione.
Le condutture soggette a corrosione richiedono ispezioni e riparazioni frequenti, che generano costi operativi significativi e il rischio di interruzioni nella trasmissione di materie prime. Con la protezione catodica, i processi di corrosione vengono notevolmente rallentati o completamente inibiti, consentendo di prolungare la vita dell’impianto fino a diversi decenni. Ciò si traduce in una minore necessità di sostituire le sezioni della conduttura, in una riduzione dei guasti e delle spese di manutenzione.
Una protezione anticorrosione inadeguata può portare a perdite di petrolio e di gas, che rappresentano una grave minaccia per l’ambiente e possono comportare pesanti sanzioni finanziarie per i gestori dei gasdotti. I sistemi di protezione catodica minimizzano il rischio di perforazione delle condotte e di perdite incontrollate, prevenendo i disastri ambientali e aumentando la sicurezza del trasporto del greggio.
Oltre agli aspetti tecnici, la protezione catodica è necessaria anche per soddisfare gli standard di sicurezza internazionali, come NACE SP0169 e ISO 15589-1, che regolano l’uso di misure di prevenzione della corrosione. L’implementazione di questa tecnologia evita problemi di non conformità e riduce i rischi finanziari di possibili sanzioni e danni.
Metodi di protezione catodica negli oleodotti – sintesi
La protezione catodica è un metodo indispensabile per proteggere gli oleodotti dalla corrosione, garantendone la longevità e l’affidabilità. Riduce efficacemente il degrado del metallo, riduce il rischio di guasti e abbassa i costi di manutenzione.
Gli attuali sistemi di protezione catodica, supportati da moderne tecnologie di monitoraggio e regolazione, consentono di adattare efficacemente il livello di protezione alle mutevoli condizioni. Il loro utilizzo non è solo raccomandato, ma anche richiesto dalle norme internazionali e dagli standard di sicurezza, rendendoli una parte indispensabile della gestione delle infrastrutture petrolifere.
L’articolo si basa sul libro “Metallurgy and Corrosion Control in Oil and Gas Production” di Robert Heidersbach.