Mittatoleranssit
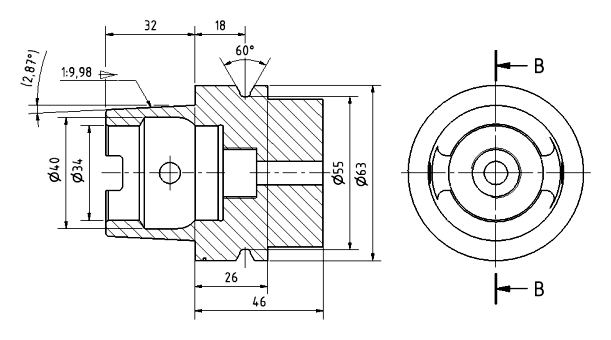
Sisällysluettelo
Mittatoleranssit ovat yksi teknisen suunnittelun ja teollisuuden keskeisimmistä tekijöistä, jotka vaikuttavat laatuun, toiminnallisuuteen ja tuotantokustannuksiin. Jokainen tekninen komponentti yksinkertaisimmasta ruuvista monimutkaisiin konemekanismeihin on valmistettava tietyn hyväksyttävän poikkeaman rajoissa, jotta voidaan varmistaa lopputuotteen asianmukainen istuvuus ja toiminta.
Nykyaikainen valmistus nojaa tarkkoihin toleranssistandardeihin laadun ja kustannustehokkuuden tasapainottamiseksi. Asianmukaisilla toleransseilla vältetään kokoonpano-ongelmat ja varmistetaan, että komponentit ovat yhteensopivia valmistajasta riippumatta.
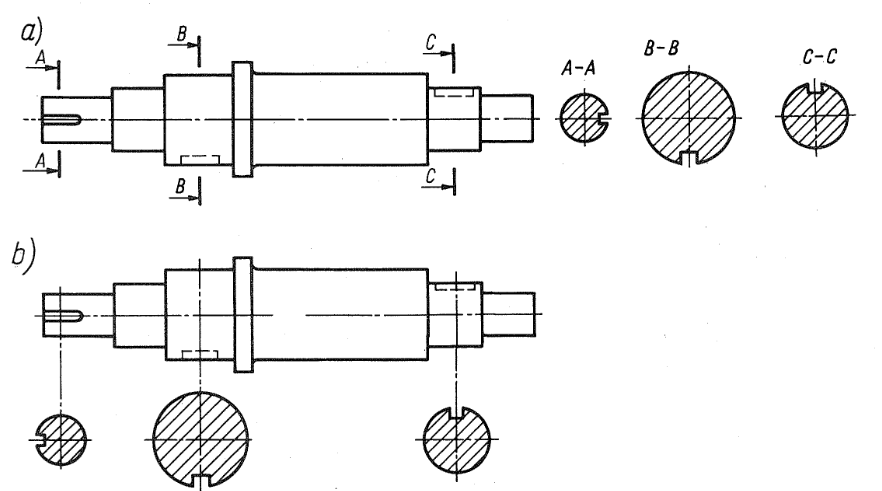
Mittatoleranssin peruskäsitteet
Mittatoleranssi määrittää mittojen sallitun poikkeaman teknisen piirustuksen nimellismitoista, jotka ovat todelliset mitat teknisessä piirustuksessa annetuista nimellismitoista. Koska valmistusprosessit eivät ole täydellisiä, jokainen valmistettu osa poikkeaa jossain määrin oletetuista mitoista. Toleranssi määrittelee rajat, joiden sisällä nämä erot ovat hyväksyttäviä.
Toleranssi määräytyy seuraavien keskeisten parametrin perusteella:
- Nimellismitta (N) – arvo, johon toleranssi kohdistuu.
- Rajamitat (A ja B) – ala- ja ylärajat, joiden sisällä todellinen mitta voi olla.
- Ylempi ja alempi poikkeama (Es, Ei rei’ille ja es, ei akseleille) – nimellismitan ja raja-arvojen välinen ero.
Kansainvälisissä standardeissa, kuten PN-EN ISO 286-1:2011, määritellään 20 toleranssiluokkaa, joista kukin vastaa eri tarkkuusluokkia, joita sovelletaan komponentin toiminnon mukaan.
Mittatoleranssimenetelmät
Perinteisesti käytetyt toleranssit perustuvat plus-miinusarvoihin, jotka kuvaavat hyväksyttäviä poikkeamia nimellismitasta.
Nykyaikainen lähestymistapa tolerointiin on GD&T (Geometrical Dimensioning and Tolerancing) järjestelmä, jonka avulla voidaan määrittää paitsi mittapoikkeamat myös komponenttien geometriset ominaisuudet. Se on perinteisiä mittatoleransseja tarkempi ja monipuoleisempi järjestelmä, sillä se ottaa huomioon sekä lineaariset mitat että geometriset parametrit, jotka ovat ratkaisevia komponenttien oikean toiminnan ja kokoonpanon kannalta.
GD&T-järjestelmä mahdollistaa seuraavien geometristen ominaisuuksien valvonnan:
- Komponentin muoto, esimerkiksi:
- Tasaisuus – määrittää, kuinka paljon pinta voi poiketa ideaalitasosta.
- Pyöreys – varmistaa, että akselin tai reiän poikkileikkaus pysyy mahdollisimman lähellä ideaalista ympyrää.
- Sylinterimäisyys – sovelletaan sylinterimäisiin akseleihin ja reikiin, ja sillä määritellään suurin sallittu poikkeama sylinterimäisestä muodosta.
- Osien suuntaus toisiinsa nähden, esim:
- Kohtisuoruus – määrittää suurimman sallitun poikkeaman kahden pinnan välisestä täydellisestä kohtisuoruudesta.
- Rinnakkaisuus – varmistaa, että kaksi pintaa tai akselia ovat mahdollisimman yhdensuuntaisia.
- Kaltevuus – määrittää, kuinka paljon pinta voi poiketa nimelliskulmasta.
- Komponenttien sijainti asettelussa, esim:
- Position – ohjaa, onko komponentti (kuten reikä) oikeassa asennossa suhteessa muihin osiin.
- Liikkuvuuden ympyrämäisyys – määrittää, kuinka paljon akseli tai reikä voi ”liukua” pyörimisakseliinsa nähden.
- Esimerkiksi pyörimisliikkeessä olevien komponenttien pyörimisliike:
- Aksiaalipoikkeama – jota sovelletaan akseleihin ja pyöriviin komponentteihin, määrittää akselin suurimman poikkeaman ideaalista pyörimisen aikana.
- Kokonaisjuoksevuus – rajoittavampi juoksevuuden muoto, joka kattaa koko pyörivän pinnan kaikki kohdat.
Käytännössä GD&T helpottaa eri tehtailla valmistettujen osien yhteensopivuuden varmistamista, vähentää kokoonpano-ongelmien riskiä ja mahdollistaa tehokkaan laadunhallinnan. Tämän vuoksi GD&T-järjestelmää käytetään autoteollisuudessa, ilmailu- ja avaruusteollisuudessa, elektroniikassa ja tarkkuuslaitteiden valmistuksessa.
Toleranssien merkitys valmistusprosesseissa
Mittatoleranssit ovat keskeinen osa komponenttien kokoonpanoprosessissa, sillä pienetkin epätarkkuudet voivat vaikuttaa valmiin tuotteen laatuun, kestävyyteen ja toiminnallisuuteen. Oikein säädetyillä toleransseilla varmistetaan, että yksittäiset komponentit sopivat yhteen suunnittelijan tarkoittamalla tavalla. Jos toleranssit ovat liian tiukat tai löysät, voi syntyä kaikenlaisia kokoonpano-ongelmia, jotka johtavat tuotantokustannusten kasvuun, materiaalihäviöihin ja jopa kokonaisten järjestelmien epäonnistumiseen.
Liian tiukka sovitus – ongelma komponenttien kokoonpanossa
Yksi yleisimmistä toleranssivirheistä on liian tiukka sovitus, joka vaikeuttaa tai estää osien kokoamista. Tämä voi johtaa lisätyöstön tarpeeseen, mikä lisää tuotantokustannuksia ja pidentää toimitusaikaa.
Jos esimerkiksi akselin halkaisija on liian suuri reikään nähden, reiän hionta tai akselin hionta voi olla tarpeen sopivan istuvuuden varmistamiseksi. Tällaiset toimenpiteet luovat lisäkustannuksia ja voivat myös vaikuttaa materiaalin mekaanisiin ominaisuuksiin heikentäen sen rakennetta.
Muoviosia koottaessa liian tiukka sovitus voi johtaa jännityssäröihin tai muodonmuutoksiin, jolloin tuotteen käyttöikä lyhenee merkittävästi. Autoteollisuudessa tai lentokoneteollisuudessa toleranssirajojen vähäisetkin ylitykset voivat johtaa vakaviin toimintaongelmiin, kuten osien lisääntyneeseen kulumiseen liiallisen kitkan vuoksi.
Liian löysä sovitus – epävakaat liitokset
Toisaalta liian löysä sovitus tarkoittaa, että osat eivät pysy tukevasti paikoillaan, mikä voi johtaa tärinään, kokoonpanopeliin ja liitosten ennenaikaiseen kulumiseen. Löysä sovitus on erityisen vaarallinen osille, joiden on kestettävä dynaamisia kuormituksia, kuten vetoakseleille, laakereille tai ruuviliitoksille.
Esimerkki mekanismin pettämisestä on, kun reikä on tehty liian leveäksi akseliin nähden. Tämä johtaa siihen, että komponentti ei istu kunnolla paikalleen ja mahdollisesti liukuu koneen käytön aikana. Pahimmassa tapauksissa tämä voi johtaa mekanismin vikaantumiseen, mikä edellyttää osan tai jopa koko koneen kallista vaihtamista.
Rakennus- ja teräsrakenteissa liialliset välykset voivat heikentää koko rakennetta, mikä lisää ulkoisten voimien, kuten tuuli- tai seismisten kuormien, aiheuttaman vikaantumisen riskiä. Tällaisissa tapauksissa kestävyyden ja turvallisuuden varmistamiseksi käytetään tarkkuussovituksia, joissa on määritellyt poikkeamastandardit.
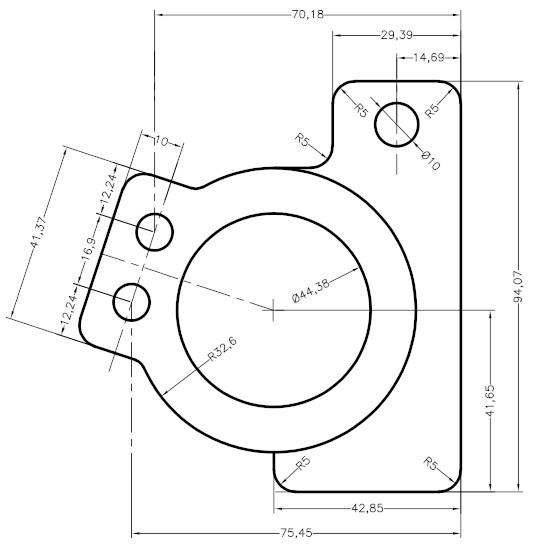
Mittatoleranssistandardit ja normit
Kansainväliset standardit säätelevät tiukasti mittatoleransseja. Näissä standardeissa määritellään sallitut mittapoikkeamat ja se, miten ne merkitään teknisiin piirustuksiin. Näiden standardien käyttö varmistaa tuotannon yhdenmukaisuuden ja toistettavuuden, helpottaa kansainvälistä yhteistyötä ja vähentää kokoonpanovirheiden riskiä.
Seuraavassa taulukossa esitetään tärkeimmät mittatoleranssistandardit ja niiden soveltaminen:
Standardi 11572_544905-d6> |
Kuvaus 11572_5c195a-26> |
Sovellus 11572_ad6aad-1e> |
---|---|---|
ISO 286 11572_83662d-6a> |
Määrittelee akselin ja reiän sovitusten mittatoleranssiluokat. Määrittää rajapoikkeamat ja sovitussäännöt. 11572_5e3d48-f2> |
Tarkkuusmekaniikka, koneen osien valmistus, reikien ja akselien sovitukset. 11572_96f574-d1> |
ISO 14405 11572_30cea6-b1> |
Vakioidaan tavat määrittää mittatoleranssit teknisissä piirustuksissa, erityisesti lineaaristen mittojen osalta. 11572_fb4e9e-e5> |
Konetekniikka, ilmailu- ja avaruustekniikka, autoteollisuus. 11572_2beff0-29> |
ISO GPS 11572_2c0114-f0> |
Geometrical Product Specification System – sisältää kokonaisvaltaisen lähestymistavan geometrisiin toleransseihin. 11572_0b7a90-a4> |
Tarkkuusvalmistus, CAD/CAM, laadunvalvonnan automatisointi. 11572_85b146-e9> |
ISO 1101 11572_d67bb0-81> |
Standardoi muoto- ja sijaintitoleranssimerkinnät ja määrittelee symbolit ja merkintätavat teknisissä piirustuksissa. 11572_5d1947-7c> |
Laadunvalvonta, tarkkuusrakenteiden suunnittelu. 11572_9c1501-09> |
ISO 8015 11572_3d942f-ad> |
Kuvailee mittojen ja toleranssien tulkintasäännöt ISO GPS:ssä. 11572_b29839-5f> |
Yleispätevä kaikille teollisuudenaloille. 11572_ba158b-a6> |
ASME Y14.5 11572_4ac05f-a3> |
Amerikkalainen geometrisia toleransseja koskeva standardi on samanlainen kuin ISO 1101, mutta sitä käytetään pääasiassa Yhdysvalloissa. 11572_2daf4a-88> |
Ilmailu- ja avaruustekniikka, autoteollisuus, avaruustekniikka. 11572_e54a4f-5f> |
ISO 2768 11572_9a929f-72> |
Määrittelee keskitarkkojen komponenttien yleiset mitta- ja kulmatoleranssit. 11572_17f5f1-09> |
Massatuotanto, autoteollisuus, rakentaminen. 11572_cfa5f0-22> |
ISO 286 -standardin soveltaminen käytännössä
ISO 286 -standardissa määritellään reikien ja akselien sovitusjärjestelmä, jota käytetään laajalti koneenrakennuksessa. Tämä tarkoittaa, että jokaisella akselilla ja reiällä voi olla tietty toleranssi vaaditun tarkkuuden mukaan. Tässä järjestelmässä käytetään kirjain- ja numeromerkintöjä, kuten:
- H7/g6 – yleisesti käytetty liukusovitus.
- H6/h5 – tarkkuusliitos, jossa osat kiinnittyvät paineella.
- H8/f7 – löysä sovitus, jota käytetään osissa, jotka vaativat vapaata liikettä.
Mittatoleranssistandardit ovat keskeisiä suunnittelussa ja valmistuksessa. Niiden avulla saadaan laadukkaampia tuotteita, vähennetään valmistusvirheistä aiheutuvia kustannuksia ja varmistetaan, että osat sopivat yhteen, vaikka ne olisivat peräisin eri toimittajilta. Nykyaikaiset laadunvalvontajärjestelmät, kuten ISO GPS, mahdollistavat entistäkin suuremman tarkkuuden komponenttien suunnittelussa ja valmistuksessa, mikä on välttämätöntä nykyaikaisessa teollisuudessa.
Toleranssien käyttöön liittyvät käytännön näkökohdat
Mitta- ja geometriset toleranssit ovat olennainen osa mekaanisten komponenttien suunnittelu- ja valmistusprosessia. Korrekti määrittely ja valvonta varmistavat, että komponentit sopivat toisiinsa niin kuin insinöörit ovat suunnitelleet ja että koko valmistusprosessi on kustannuksiltaan ja laadultaan optimaalinen. Tässä luvussa käsitellään sitä, miten toleranssit määritetään oikein teknisissä piirustuksissa ja mitä mittausmenetelmiä niiden valvonnassa käytetään.
Toleranssien määrittäminen teknisessä piirustuksessa
Tekniset piirustukset ovat valmistusprosessin keskeisiä asiakirjoja, joissa nimellismitat ja sallitut poikkeamat on määriteltävä selkeästi. Toleranssien asianmukainen merkitseminen mahdollistaa eritelmien yksiselitteisen lukemisen ja auttaa vähentämään virheitä, jotka voivat johtaa kokoonpano-ongelmiin tai ylimääräisiin koneistuskustannuksiin.
Perussäännöt toleranssien määrittämiseksi teknisessä piirustuksessa
- Asianmukaisten merkintöjen käyttö ISO- ja ASME-standardien mukaisesti.
- Mitat on esitettävä luettavasti ilman tarpeetonta toistoa.
- Geometristen toleranssimerkintöjen on oltava standardin ISO 1101 tai ASME Y14.5 mukaisia.
- Mitat ja niiden toleranssit on sijoitettava piirustukseen sopiviin kohtiin, jotta ne eivät haittaa luettavuutta.
- Määritä keskeisten osien geometriset toleranssit.
- Sen sijaan, että käytettäisiin klassisia ±-toleransseja kullekin ulottuvuudelle, on hyödyllistä käyttää geometrisia toleransseja, jotka kuvaavat paremmin komponentin toiminnallisuutta.
- Esimerkiksi tasaisuuden toleranssi on tärkeä tangentiaalisille pinnoille, ja rinnakkaisuus on ratkaisevan tärkeä liukupinnoille ja liukulaakereille.
- Kokoonpanon kannalta tärkeät mitat on nimettävä ohjausmitoiksi (esim. K, C teknisissä asiakirjoissa).
- Vältä toleranssien ylikiristämistä, jos se ei ole välttämätöntä.
- Yleinen suunnitteluvirhe on ottaa käyttöön erittäin tiukkoja toleransseja, jotka lisäävät valmistuskustannuksia.
- Käytä toleranssiluokkia, jotka on sovitettu osan käyttötarkoitukseen – tarkkuusosille (kuten laakereille) kannattaa käyttää IT6-luokkia ja rakenneosille IT10-IT12-luokat riittävät.
- ISO 2768:n mukaan yleistoleransseja voidaan käyttää osissa, jotka eivät vaadi suurta tarkkuutta valmistuksessa.
- Varmista yhteensopivuus mittausmenetelmien kanssa
- Toleranssit olisi valittava siten, että niitä voidaan valvoa käytettävissä olevilla mittausvälineillä.
- Jos toleranssi on esimerkiksi alle 0,01 mm, tavallisilla mittasakseleilla ei ehkä saavuteta riittävää tarkkuutta, vaan tarvitaan koordinaattimittakone (CMM).
Mittatarkastusmenetelmät
Mittausmenetelmä 11572_9e33f0-80> |
Kuvaus 11572_3e93cc-e5> |
Soveltamisala 11572_ee0831-e8> |
---|---|---|
Työntömitta 11572_1b3e85-37> |
Yksinkertainen työkalu pituuden, halkaisijan ja syvyyden mittaamiseen (tarkkuus 0,02 mm). 11572_d401a3-0a> |
Yleinen tuotanto, nopea mittatarkastus 11572_1620b0-da> |
Mikrometri 11572_20adbf-b1> |
Työkalu läpimittojen tarkkaan mittaamiseen 0,001 mm:n tarkkuudella. 11572_1973f5-0b> |
Kriittisten mittojen valvonta. 11572_7eb632-37> |
Mittakello (indeksimittari) 11572_62e3f3-0e> |
Käytetään aksiaalipoikkeaman ja pintojen kohtisuoruuden tarkistamiseen. 11572_9cc15a-c4> |
Akselien, hammaspyörien ja laakereiden tarkastus. 11572_ca8220-c8> |
Koordinaattimittauskone (CMM) 11572_b6df73-ce> |
Kehittynyt 3D-skannausjärjestelmä, joka mittaa tarkasti geometriset ja sijaintitoleranssit. 11572_e0b9bd-f8> |
Ilmailu- ja avaruustekniikka, hienomekaniikka, autoteollisuus. 11572_b22109-26> |
Mittausprojektori (profilometri) |
Optinen menetelmä pinnan ääriviivojen ja profiilien mittaamiseen. 11572_04950b-9f> |
Monimutkaisen muotoisten työkappaleiden tarkastus. 11572_13d63b-a9> |
3D-laserskanneri 11572_1db64f-27> |
Kosketuksetonta skannausjärjestelmää käytetään kohteen koko pinnan analysointiin. 11572_55d67b-d6> |
Poikkeama-analyysi CAD-tekniikassa, 3D-tulostuksessa. 11572_7dae89-23> |
Toleranssien käytön käytännön näkökohtia ovat mm. teknisten piirustusten sallittujen poikkeamien tarkka määrittäminen ja tehokkaat menetelmät niiden valvomiseksi. Oikeita standardeja ja mittaustyökaluja käyttämällä voidaan minimoida tuotantovirheiden riski, varmistaa oikea kokoonpano, ja optimoida tuotantokustannukset. Nykytekniikat, kuten tilastollinen prosessianalyysi ja kehittyneet mittausjärjestelmät, mahdollistavat entistä tarkemman mittojen ja toleranssien valvonnan, mikä on nykyaikaiselle teollisuudelle ratkaisevan tärkeää.
Mittatoleranssit – yhteenveto
Oikein valitut mittatoleranssit ovat olennaisia komponenttien onnistuneen kokoonpanon kannalta eri teollisuudenaloilla. Epäsopivat toleranssit voivat johtaa sovitusongelmiin, jotka lisäävät kustannuksia, materiaalihäviöitä ja heikentävät tuotteen laatua. Siksi insinöörien on analysoitava toleranssivaatimukset huolellisesti ottaen huomioon sekä toiminnalliset että taloudelliset näkökohdat kokoonpanoprosessien luotettavuuden ja tehokkuuden varmistamiseksi.