Tolerancje wymiarów
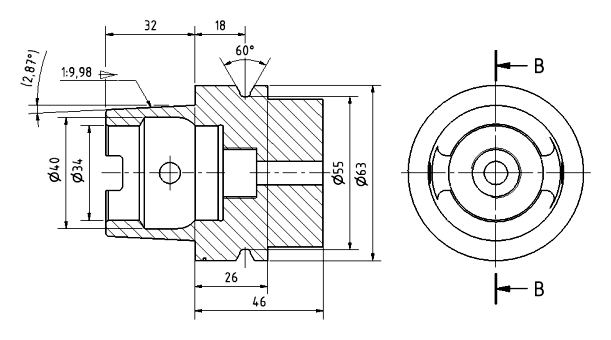
Spis treści
Tolerancja wymiarów to jedno z kluczowych zagadnień w inżynierii i przemyśle, które wpływa na jakość, funkcjonalność oraz koszty produkcji. Każdy element techniczny, od najprostszej śruby po skomplikowane mechanizmy maszynowe, musi być wykonany w określonym zakresie dopuszczalnych odchyłek, aby zapewnić odpowiednie dopasowanie i działanie w gotowym produkcie.
Współczesna produkcja opiera się na precyzyjnych normach tolerancji, które umożliwiają zachowanie równowagi między jakością a efektywnością kosztową. Zastosowanie odpowiednich tolerancji pozwala uniknąć problemów montażowych i zapewnia, że elementy są kompatybilne, niezależnie od producenta.
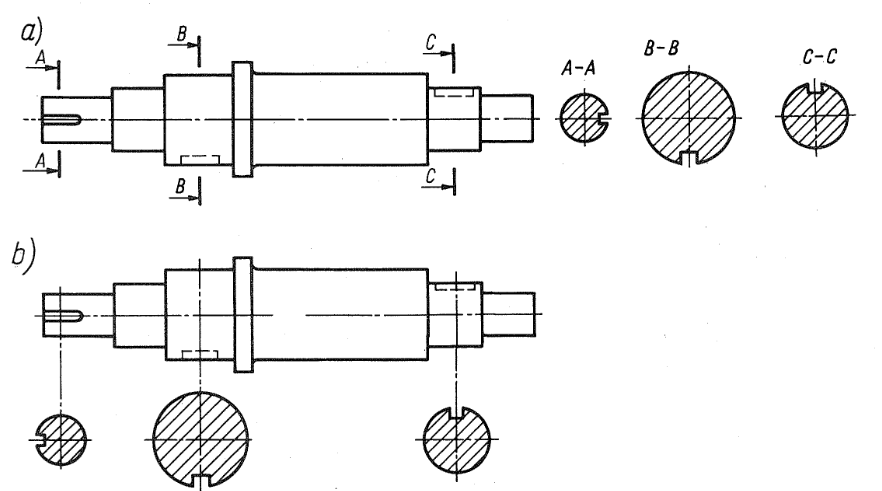
Podstawowe pojęcia tolerancji wymiarów
Tolerancja wymiarów określa dopuszczalne odchylenie wymiarów rzeczywistych od wymiarów nominalnych podanych na rysunku technicznym. Ponieważ procesy produkcyjne nie są idealne, każdy wytwarzany element różni się w pewnym stopniu od założonych wymiarów. Tolerancja określa graniczne wartości, w jakich te różnice są akceptowalne.
Tolerancja jest wyznaczana poprzez dwa kluczowe parametry:
- Wymiar nominalny (N) – wartość, do której odnosi się tolerancja.
- Wymiary graniczne (A i B) – dolna i górna granica, w jakich wymiar rzeczywisty może się mieścić.
- Odchyłki górne i dolne (Es, Ei dla otworów oraz es, ei dla wałków) – różnica między wymiarem nominalnym a wartościami granicznymi.
Normy międzynarodowe, takie jak PN-EN ISO 286-1:2011, określają 20 klas tolerancji, z których każda odpowiada różnym poziomom dokładności, stosowanym w zależności od funkcji danego elementu.
Metody tolerowania wymiarowego
Tradycyjnie stosowane tolerancje opierają się na wartościach plus-minus, które oznaczają dopuszczalne odchyłki od wymiaru nominalnego.
Nowoczesnym podejściem do tolerowania jest system GD&T (Geometrical Dimensioning and Tolerancing), który pozwala określać nie tylko odchyłki wymiarowe, ale także cechy geometryczne elementów. Jest to precyzyjniejszy i bardziej funkcjonalny system niż tradycyjne tolerancje wymiarowe ±, ponieważ uwzględnia nie tylko wymiary liniowe, ale również parametry geometryczne kluczowe dla poprawnego działania i montażu komponentów.
System GD&T umożliwia kontrolę takich cech geometrycznych jak:
- Kształt elementu, np.:
- Orientacja elementów względem siebie, np.:
- Prostopadłość – określa maksymalną dopuszczalną odchyłkę od idealnej prostopadłości między dwiema powierzchniami.
- Równoległość – zapewnia, że dwie powierzchnie lub osie są możliwie równoległe.
- Nachylenie – określa, jak bardzo powierzchnia może odbiegać od nominalnego kąta.
- Położenie elementów w układzie, np.:
- Pozycja – kontroluje, czy element (np. otwór) znajduje się w prawidłowym miejscu względem innych części.
- Kołowość bicia – określa, jak bardzo wałek lub otwór może „bić” w stosunku do swojej osi obrotu.
- Bicie elementów w ruchu obrotowym, np.:
- Bicie osiowe – stosowane do wałków i elementów wirujących, określa maksymalne odchylenie osi od ideału podczas obrotu.
- Bicie całkowite – bardziej restrykcyjna forma bicia, obejmująca wszystkie punkty na całej powierzchni obrotowej.
W praktyce stosowanie GD&T ułatwia zapewnienie zgodności części produkowanych w różnych zakładach, zmniejsza ryzyko problemów montażowych i umożliwia efektywne zarządzanie jakością. Dzięki temu system GD&T znajduje zastosowanie w przemyśle motoryzacyjnym, lotniczym, elektronicznym oraz w produkcji urządzeń precyzyjnych.
Znaczenie tolerancji w procesach produkcyjnych
Tolerancja wymiarów odgrywa kluczową rolę w procesie montażu komponentów, ponieważ każda niedokładność może wpłynąć na jakość, trwałość oraz funkcjonalność gotowego produktu. Właściwie dobrane tolerancje zapewniają, że poszczególne elementy pasują do siebie zgodnie z zamierzeniami projektanta. Jeśli tolerancje są zbyt restrykcyjne lub zbyt luźne, mogą wystąpić różnego rodzaju problemy montażowe, które prowadzą do zwiększonych kosztów produkcji, strat materiałowych, a nawet do awarii całych systemów.
Zbyt ciasne pasowanie – problem z montażem elementów
Jednym z głównych problemów wynikających ze źle dobranej tolerancji jest zbyt ciasne pasowanie, które sprawia, że elementy trudno dopasować do siebie lub wręcz uniemożliwia ich montaż. Może to prowadzić do konieczności dodatkowej obróbki mechanicznej, co zwiększa koszty produkcji i wydłuża czas realizacji zamówienia.
Przykładowo, jeśli średnica wałka jest zbyt duża w stosunku do otworu, konieczne może być rozwiercanie otworu lub szlifowanie wałka, aby zapewnić odpowiednie pasowanie. Takie operacje nie tylko generują dodatkowe koszty, ale także mogą wpłynąć na właściwości mechaniczne materiału, osłabiając jego strukturę.
W przypadku montażu elementów z tworzyw sztucznych, zbyt ciasne pasowanie może prowadzić do pęknięć lub odkształceń pod wpływem naprężeń, co znacząco obniża trwałość produktu. W przemyśle motoryzacyjnym lub lotniczym nawet minimalne przekroczenie granic tolerancji może skutkować poważnymi problemami eksploatacyjnymi, np. zwiększonym zużyciem części wskutek nadmiernego tarcia.
Zbyt luźne pasowanie – brak stabilności połączeń
Z drugiej strony, zbyt luźne pasowanie sprawia, że elementy nie trzymają się stabilnie, co może prowadzić do wibracji, luzów montażowych i przedwczesnego zużycia połączeń. Luźne pasowanie jest szczególnie niebezpieczne w przypadku części, które muszą przenosić obciążenia dynamiczne, takie jak wały napędowe, łożyska czy połączenia śrubowe.
Przykładem może być sytuacja, w której otwór jest wykonany zbyt szeroko w stosunku do wałka, co powoduje, że element nie jest odpowiednio osadzony i może się przesuwać podczas pracy maszyny. W skrajnych przypadkach może to prowadzić do awarii mechanizmu, co skutkuje koniecznością kosztownej wymiany części lub nawet całego urządzenia.
W budownictwie i konstrukcjach stalowych nadmierne luzy mogą powodować osłabienie całej konstrukcji, zwiększając ryzyko jej uszkodzenia pod wpływem sił zewnętrznych, takich jak obciążenia wiatrowe czy sejsmiczne. W takich przypadkach stosuje się precyzyjne pasowania z określonymi normami odchyłek, aby zapewnić trwałość i bezpieczeństwo.
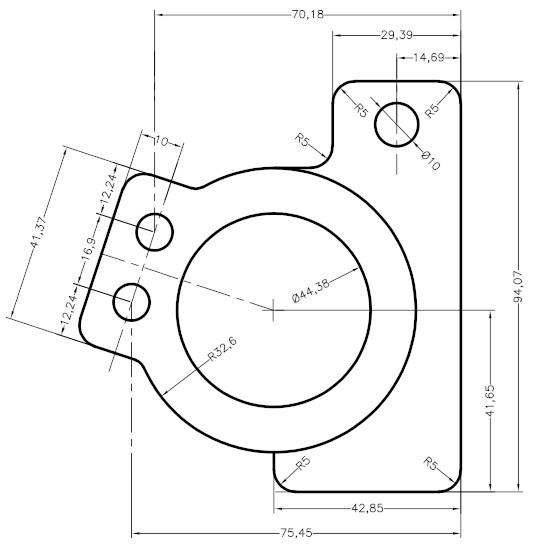
Normy i standardy dotyczące tolerancji wymiarów
Tolerancje wymiarowe są ściśle regulowane przez normy międzynarodowe, które określają dopuszczalne odchyłki wymiarowe oraz sposoby ich oznaczania na rysunkach technicznych. Stosowanie tych norm zapewnia jednolitość i powtarzalność produkcji, ułatwiając współpracę międzynarodową oraz redukując ryzyko błędów montażowych.
W poniższej tabeli przedstawiono najważniejsze normy dotyczące tolerancji wymiarów oraz ich zastosowanie:
Norma 11341_538226-69> |
Opis 11341_5ced7b-5b> |
Zastosowanie 11341_ec8c09-c3> |
---|---|---|
ISO 286 11341_2823f9-3d> |
Określa klasy tolerancji wymiarowych dla pasowań wałków i otworów. Definiuje odchyłki graniczne i zasady pasowania. 11341_b3e510-e7> |
Mechanika precyzyjna, produkcja elementów maszynowych, pasowania otworów i wałków. 11341_2869ff-69> |
ISO 14405 11341_03b161-e6> |
Standaryzuje sposoby określania tolerancji wymiarowych w rysunku technicznym, szczególnie dla wymiarów liniowych. 11341_6fe227-23> |
Inżynieria mechaniczna, przemysł lotniczy, motoryzacyjny. 11341_c4bf0f-9d> |
ISO GPS 11341_493136-84> |
System Geometrical Product Specification – obejmuje całościowe podejście do tolerancji geometrycznych. 11341_60207b-76> |
Produkcja precyzyjna, CAD/CAM, automatyzacja kontroli jakości. 11341_eedb36-05> |
ISO 1101 11341_fc38f6-dd> |
Standaryzuje oznaczenia tolerancji kształtu i położenia, określa symbole i metody oznaczania na rysunkach technicznych. 11341_06a960-e2> |
Kontrola jakości, projektowanie konstrukcji precyzyjnych. 11341_e69fdb-97> |
ISO 8015 11341_0a7556-60> |
Opisuje zasady interpretacji wymiarów i tolerancji w systemie ISO GPS. 11341_0352e7-e2> |
Uniwersalne dla wszystkich gałęzi przemysłu. 11341_cff175-ca> |
ASME Y14.5 11341_f99856-38> |
Amerykańska norma dotycząca tolerancji geometrycznych, podobna do ISO 1101, lecz używana głównie w USA. 11341_32ad1a-e7> |
Przemysł lotniczy, motoryzacyjny, inżynieria kosmiczna. 11341_5b3379-31> |
ISO 2768 11341_1c2123-7e> |
Definiuje ogólne tolerancje wymiarowe i kątowe dla elementów o średniej dokładności. 11341_583681-21> |
Produkcja masowa, przemysł motoryzacyjny, budownictwo. 11341_dbc4a7-96> |
Przykład zastosowania normy ISO 286
Norma ISO 286 definiuje system pasowań otworów i wałków, który jest szeroko stosowany w inżynierii mechanicznej. W praktyce oznacza to, że każdy wałek i otwór może mieć określoną tolerancję, zależnie od wymaganej precyzji. System ten wykorzystuje oznaczenia literowe i liczbowe, np.:
- H7/g6 – powszechnie stosowane pasowanie suwliwe.
- H6/h5 – pasowanie wciskowe dla precyzyjnych połączeń.
- H8/f7 – pasowanie luźne, używane w przypadku elementów wymagających swobodnego ruchu.
Normy dotyczące tolerancji wymiarowych odgrywają kluczową rolę w inżynierii i produkcji. Ich stosowanie pozwala na lepszą jakość produktów, ogranicza koszty związane z błędami produkcyjnymi i zapewnia, że elementy będą do siebie pasować, nawet jeśli pochodzą od różnych dostawców. Współczesne systemy kontroli jakości, takie jak ISO GPS, umożliwiają jeszcze większą precyzję w projektowaniu i wytwarzaniu elementów, co jest niezbędne w nowoczesnym przemyśle.
Praktyczne aspekty stosowania tolerancji
Tolerancja wymiarowa i geometryczna są nieodłącznym elementem procesu projektowania i produkcji elementów mechanicznych. Ich prawidłowe określenie oraz kontrolowanie zapewnia, że elementy będą pasować do siebie zgodnie z zamierzeniami inżynierów, a cały proces produkcyjny będzie zoptymalizowany pod względem kosztów i jakości. W tym rozdziale omówimy, jak poprawnie określać tolerancje na rysunkach technicznych oraz jakie metody pomiarowe stosuje się do ich kontroli.
Jak określać tolerancje na rysunku technicznym?
Rysunek techniczny to kluczowy dokument w procesie produkcji, dlatego musi jednoznacznie określać zarówno wymiary nominalne, jak i dopuszczalne odchyłki. Właściwe oznaczenie tolerancji pozwala na jednoznaczne odczytanie specyfikacji oraz uniknięcie błędów interpretacyjnych, które mogłyby prowadzić do problemów montażowych lub dodatkowych kosztów obróbki.
Podstawowe zasady określania tolerancji na rysunku technicznym
- Stosowanie odpowiednich oznaczeń zgodnych z normami ISO i ASME
- Określanie tolerancji geometrycznych dla kluczowych elementów
- Zamiast używać klasycznych tolerancji ± dla każdego wymiaru, warto stosować tolerancje geometryczne, które lepiej odwzorowują funkcjonalność elementu.
- Na przykład tolerancja płaskości jest istotna dla powierzchni stycznych, a równoległość jest kluczowa dla prowadnic i łożysk ślizgowych.
- Wymiary ważne dla montażu powinny być oznaczone jako wymiary kontrolne (np. K, C w dokumentacji technicznej).
- Unikanie nadmiernego zaostrzania tolerancji, jeśli nie jest to konieczne
- Częstym błędem w projektowaniu jest przyjmowanie bardzo małych tolerancji, które zwiększają koszty produkcji.
- Należy stosować klasy tolerancji dopasowane do funkcji elementu – dla części precyzyjnych (np. łożyska) warto stosować klasy IT6, a dla części konstrukcyjnych wystarczą IT10-IT12.
- Można zastosować tolerancje ogólne według ISO 2768 dla elementów, które nie wymagają dużej dokładności wykonania.
- Zapewnienie kompatybilności z metodami pomiarowymi
- Tolerancje powinny być dobrane w taki sposób, aby możliwe było ich kontrolowanie za pomocą dostępnych narzędzi pomiarowych.
- Przykładowo, jeśli tolerancja jest mniejsza niż 0,01 mm, to standardowe suwmiarki mogą nie zapewniać wystarczającej dokładności i konieczne będzie użycie maszyny współrzędnościowej (CMM).
Metody kontroli wymiarowej
Metoda pomiarowa 11341_1e4faf-2a> |
Opis 11341_dd1a29-36> |
Zakres zastosowania 11341_0ab3ae-63> |
---|---|---|
Suwmiarka 11341_efc4cf-99> |
Proste narzędzie do pomiaru długości, średnicy i głębokości, dokładność rzędu 0,02 mm. 11341_29e9ca-ec> |
Produkcja ogólna, szybka kontrola wymiarów. 11341_dfd57b-3c> |
Mikrometr 11341_86731d-12> |
Narzędzie do precyzyjnego pomiaru średnic z dokładnością do 0,001 mm. 11341_fc9a30-a4> |
Kontrola wymiarów krytycznych. 11341_660197-08> |
Czujnik zegarowy (indikator) 11341_cebaab-7c> |
Stosowany do sprawdzania bicia osiowego i prostopadłości powierzchni. 11341_5fc588-72> |
Kontrola wałów, kół zębatych, łożysk. 11341_8ce3f5-d4> |
Maszyna współrzędnościowa (CMM) 11341_2547fb-4d> |
Zaawansowany system skanujący 3D, który precyzyjnie mierzy tolerancje geometryczne i położeniowe. 11341_8f8d3a-9a> |
Lotnictwo, precyzyjna mechanika, motoryzacja. 11341_b19329-02> |
Projektor pomiarowy (profilometr) 11341_ac0a1e-6c> |
Optyczna metoda do pomiaru konturów i profili powierzchni. 11341_0a1ba4-cb> |
Kontrola detali o skomplikowanych kształtach. 11341_d2142b-ba> |
Skaner laserowy 3D 11341_574b45-50> |
Bezkontaktowy system skanujący umożliwiający analizę całej powierzchni obiektu. 11341_70486b-46> |
Analiza odchyłek w technologii CAD, druk 3D. 11341_3f5045-05> |
Praktyczne aspekty stosowania tolerancji obejmują zarówno precyzyjne określanie dopuszczalnych odchyłek na rysunkach technicznych, jak i skuteczne metody ich kontroli. Stosowanie właściwych norm i narzędzi pomiarowych pozwala zminimalizować ryzyko błędów produkcyjnych, zapewnić poprawność montażu oraz zoptymalizować koszty produkcji. Współczesne technologie, takie jak analiza statystyczna procesu oraz zaawansowane systemy pomiarowe, umożliwiają jeszcze dokładniejszą kontrolę wymiarów i tolerancji, co jest kluczowe dla nowoczesnego przemysłu.
Tolerancje wymiarów – podsumowanie
Właściwy dobór tolerancji wymiarowych jest kluczowy dla zapewnienia prawidłowego montażu elementów w różnych gałęziach przemysłu. Niewłaściwe tolerancje mogą prowadzić do problemów związanych z pasowaniem, które skutkują zwiększonymi kosztami, stratami materiałowymi oraz pogorszoną jakością produktu. Dlatego też inżynierowie muszą dokładnie analizować wymagania dotyczące tolerancji, uwzględniając zarówno aspekty funkcjonalne, jak i ekonomiczne, aby zapewnić niezawodność i efektywność procesów montażowych.