Métodos de protección catódica en oleoductos
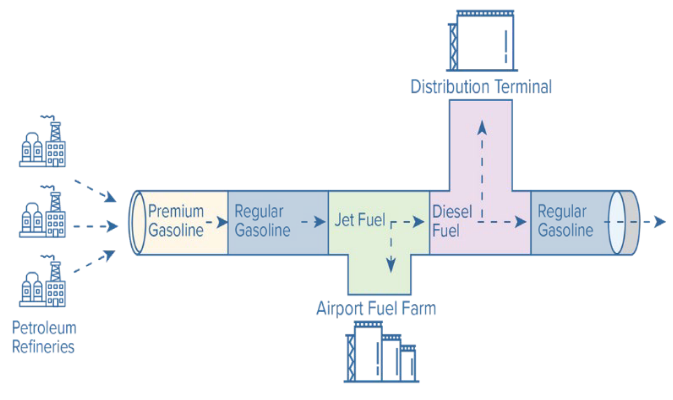
Índice
La corrosión es uno de los problemas más graves en el funcionamiento de los oleoductos. Esto se debe a que provoca una disminución de la resistencia estructural, vertidos de petróleo y costosas reparaciones y averías, que son peligros tanto económicos como medioambientales. La protección adecuada de la infraestructura de transporte es clave para garantizar el funcionamiento seguro y a largo plazo de los oleoductos.
Uno de los métodos más eficaces para prevenir la corrosión en las tuberías es la protección catódica. Esta tecnología electroquímica implica el suministro controlado de corriente eléctrica a la tubería, lo que reduce eficazmente el proceso de oxidación del metal. Este método se utiliza tanto en tuberías subterráneas como submarinas, en las que la corrosión es especialmente intensa.
En este artículo, se tratan los principios de la protección catódica, sus tipos, los componentes del sistema y su aplicación práctica en la industria petrolera. También analizaremos las ventajas de esta tecnología y otros retos de su aplicación.
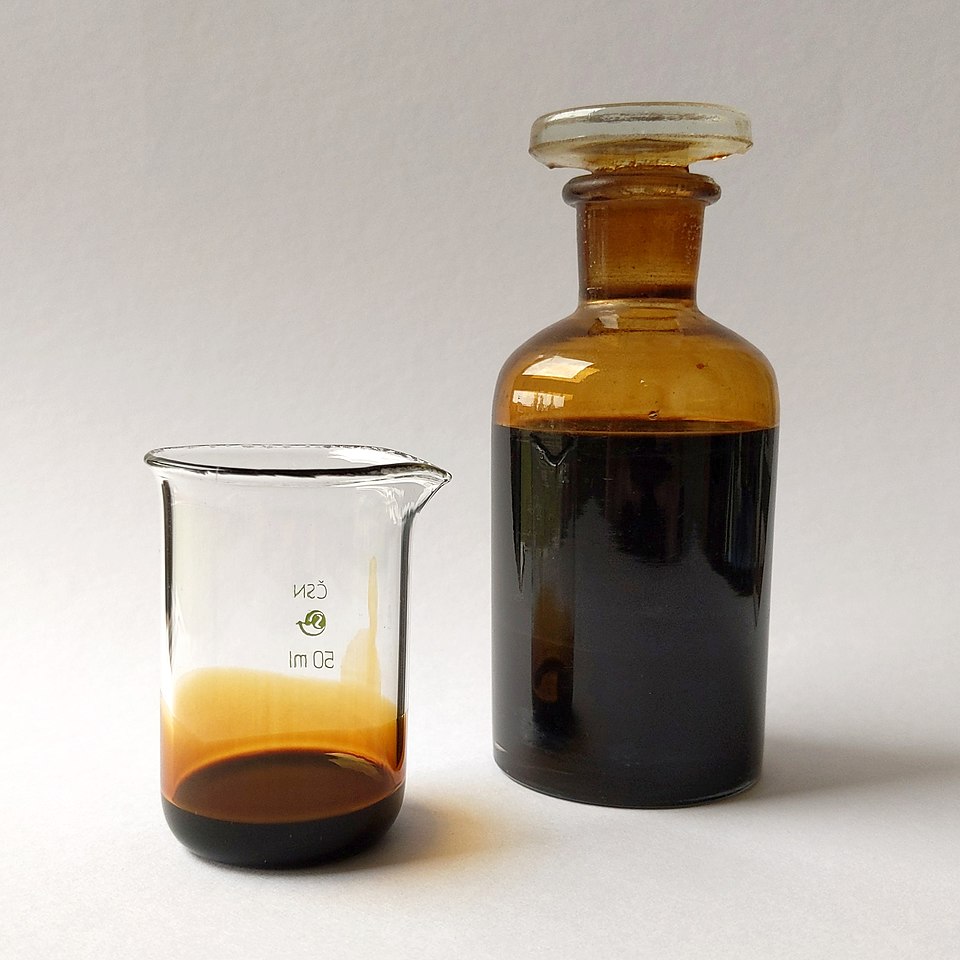
Principio de la protección catódica
Mecanismo de la corrosión electroquímica en tuberías
La corrosión electroquímica en tuberías metálicas es el resultado de la diferencia de potenciales eléctricos entre las distintas partes de la estructura. En presencia de humedad y electrolitos, (por ejemplo, tierra o agua de mar), el metal de la tubería comienza a actuar como una célula galvánica, en la que se producen:
- Ánodo: la zona donde se produce la oxidación y degradación del metal.
- Cátodo: zona donde se reducen los iones del entorno y el metal no se corroe.
Este proceso provoca la descomposición gradual de la tubería, especialmente en zonas expuestas a agentes agresivos como compuestos de azufre, oxígeno o cloruros.
¿Cómo funciona la protección catódica?
La protección catódica consiste en dirigir la reacción de corrosión para que la tubería actúe como cátodo, lo que elimina la degradación del metal. Para ello, una fuente externa de electrones neutraliza el potencial electroquímico de la tubería e impide su oxidación. En la práctica, la protección catódica funciona:
- Reduciendo el potencial electroquímico del metal por debajo del nivel en el que se produce la corrosión.
- Proporcionando electrones externos a la estructura de la tubería, lo que impide que el metal se oxide.
- Usando ánodos de sacrificio o sistemas de corriente continua (PCCI) para controlar el flujo de corriente de protección.
Mediante el uso de la protección catódica, los procesos de corrosión se ralentizan significativamente o se inhiben por completo, lo que permite contar con la protección a largo plazo de la infraestructura de transmisión.
Principales componentes del sistema de protección catódica
El sistema de protección catódica consta de varios componentes clave:
- Ánodos: responsables de proporcionar corriente de protección y desgaste gradual en lugar de la tubería.
- Fuentes de corriente continua: utilizadas en la protección PCCI para el suministro controlado de electrones a la tubería.
- Sensores y sondas de referencia: para controlar el nivel de protección y el potencial electroquímico de la instalación.
- Cables y sistemas de conexión: para garantizar una transmisión eficaz de la corriente de protección.
Estos sistemas deben supervisarse y mantenerse periódicamente para garantizar su eficacia y adaptación a las condiciones de funcionamiento.
Tipos de protección catódica
La protección catódica de los oleoductos puede realizarse de dos maneras: mediante ánodos galvánicos (de sacrificio) o mediante el suministro de corriente continua desde una fuente externa (protección catódica por corriente impresa, PCCI). La elección del método adecuado depende de las condiciones ambientales, la longitud de la tubería y la conductividad eléctrica del medio circundante.
Protección catódica galvánica
La protección galvánica implica el uso de ánodos de sacrificio que están hechos de metales con un potencial electroquímico inferior al del material de la tubería. Como resultado, el ánodo sufre una corrosión controlada y protege el metal de la tubería de la degradación.
En los sistemas de protección galvánica, los ánodos suelen ser de zinc, magnesio o aluminio. Estos materiales tienen un potencial electroquímico superior al del acero de las tuberías, por lo que donan electrones a la estructura protegida y se desgastan gradualmente.
Entre las ventajas de este método se incluyen que no necesita una fuente de energía externa, lo que simplifica la instalación, el buen rendimiento en entornos de baja resistividad como el agua de mar y los mínimos requisitos de mantenimiento porque el sistema funciona de forma pasiva.
Desgraciadamente, como cualquier método, tiene sus limitaciones: menor vida útil de los ánodos, que se desgastan gradualmente y deben sustituirse, y menor eficacia en entornos de alta resistividad (por ejemplo, suelos secos), donde la corriente protectora se propaga de forma más débil.
Protección catódica con corriente externa (PCCI)
La PCCI (protección catódica con corriente impresa) utiliza una fuente externa de corriente continua para suministrar electrones a una tubería, lo que elimina el riesgo de corrosión. Es un método más avanzado que se utiliza principalmente en tuberías largas y entornos de alta resistividad.
El sistema PCCI utiliza ánodos insolubles fabricados con materiales resistentes a la degradación, como titanio recubierto de óxidos metálicos mixtos (MMO), grafito o silicio metalúrgico. Un rectificador que suministra tensión a los ánodos genera una corriente de protección que refuerza el flujo de electrones hacia la tubería y la protege de la oxidación.
Las ventajas de este método incluyen: protección a largo plazo porque los ánodos PCCI no se desgastan tan rápidamente como los ánodos galvánicos, intensidad de protección ajustable que permite ajustar el nivel de protección a las cambiantes condiciones de funcionamiento y la capacidad de proteger grandes tuberías e instalaciones en alta mar, donde los ánodos galvánicos serían insuficientes.
Limitaciones de la protección PCCI: requiere energía eléctrica, lo que supone costes adicionales de funcionamiento, protección contra cortes de energía y una instalación más complicada que requiere supervisión y ajuste periódico del sistema.
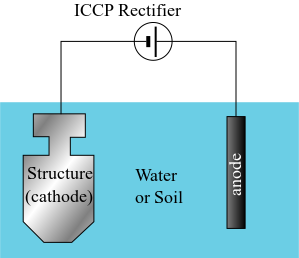
Componentes clave de un sistema de protección catódica
Un sistema de protección catódica consta de varios componentes clave que, juntos, protegen eficazmente las tuberías contra la corrosión. Una selección adecuada y un mantenimiento regular son fundamentales para asegurar la longevidad de la infraestructura de transmisión.
Ánodos
Los ánodos en los sistemas de protección catódica actúan como fuente de electrones que contrarrestan el proceso de corrosión. Dependiendo del tipo de protección catódica, se utilizan diferentes tipos de ánodos:
- Los ánodos galvánicos (de sacrificio) están hechos de metales electroquímicamente más activos que el acero de las tuberías. Los ánodos más comunes están hechos de zinc, magnesio y aluminio, que se disuelven gradualmente y ceden electrones a la instalación protegida. Se utilizan principalmente en tuberías subterráneas e instalaciones marinas.
- Los ánodos insolubles (PCCI) se utilizan en sistemas de protección catódica con corriente externa. Están fabricados con materiales resistentes a la corrosión como el titanio y recubiertos con óxidos metálicos mixtos (MMO), grafito y silicio metalúrgico. Su misión es conducir corriente de protección sin desgastarse, y proporcionar así protección a largo plazo para grandes instalaciones.
La selección adecuada del ánodo es crucial para garantizar la eficacia de la protección catódica. Algunos factores como el entorno operativo, la longitud de la tubería y la conductividad eléctrica del medio determinan la selección de un tipo concreto de ánodo.
Fuentes de energía
En los sistemas de protección catódica PCCI, una fuente de alimentación de corriente continua es un componente indispensable que permite la entrega controlada de electrones a la tubería. Existen dos tipos básicos de fuentes de alimentación:
- Rectificadores de CC: dispositivos que convierten la corriente alterna en corriente continua de un voltaje y amperaje determinados. Permiten ajustar con precisión el nivel de protección catódica a las condiciones de funcionamiento.
- Alimentación eléctrica a partir de fuentes de energía renovables: en lugares alejados de la red eléctrica, se utilizan sistemas de alimentación basados en paneles solares y turbinas eólicas, lo que permite independencia energética y menores costes de explotación.
El correcto funcionamiento de un sistema de protección catódica PCCI requiere una monitorización continua de la tensión y la corriente para garantizar unos niveles óptimos de protección contra la corrosión.
Supervisión y control del sistema
Para garantizar la eficacia de la protección catódica, es necesario controlar continuamente el potencial electroquímico de la tubería. Para ello, se utilizan diversas tecnologías de control:
- Sondas de referencia (electrodos de medición): colocadas cerca de la instalación protegida. Permiten medir el potencial de la tubería en relación con el entorno. Los electrodos más utilizados son Cu/CuSO₄ (sulfato de cobre/cobre) para tuberías subterráneas y Ag/AgCl (cloruro de plata/plata) para instalaciones marinas.
- Sensores de corriente de corrosión: detectan anomalías en el flujo de corriente de protección, lo que permite una ofrecer una respuesta rápida en caso de fallo del sistema.
- Sistemas de monitorización remota: utilizan tecnologías IoT y telemetría para realizar un seguimiento de los parámetros de protección catódica en tiempo real y responder a posibles amenazas.
La inspección y monitorización periódicas permiten detectar rápidamente posibles fallos y ajustar los parámetros del sistema, lo que aumenta la eficiencia de la protección y reduce los costes de mantenimiento.
Cables y sistemas de conexión
En los sistemas de protección catódica, es extremadamente importante disponer de los cables y conexiones eléctricas adecuados para que la corriente de protección fluya eficazmente. Los componentes clave del sistema incluyen: cables resistentes a la corrosión y a los daños mecánicos recubiertos de una capa aislante para protegerlos de la humedad y los productos químicos, conectores anódicos y catódicos que deben estar adecuadamente aislados para minimizar la pérdida de corriente y cajas y puntos de prueba que permitan comprobar la eficacia del sistema en varios puntos a lo largo de la tubería.
Las conexiones mal realizadas pueden provocar la pérdida de la corriente protectora y una protección anticorrosiva ineficaz, por lo que la selección y la calidad de la instalación eléctrica son cruciales para la eficacia de todo el sistema. Un sistema de protección catódica consta de muchos componentes que cooperan entre sí y cuyo correcto funcionamiento garantiza una protección eficaz contra la corrosión. Los ánodos, las fuentes de energía, los sistemas de monitorización y los cables y conexiones deben dimensionarse adecuadamente e inspeccionarse con regularidad para garantizar la protección a largo plazo de los oleoductos.
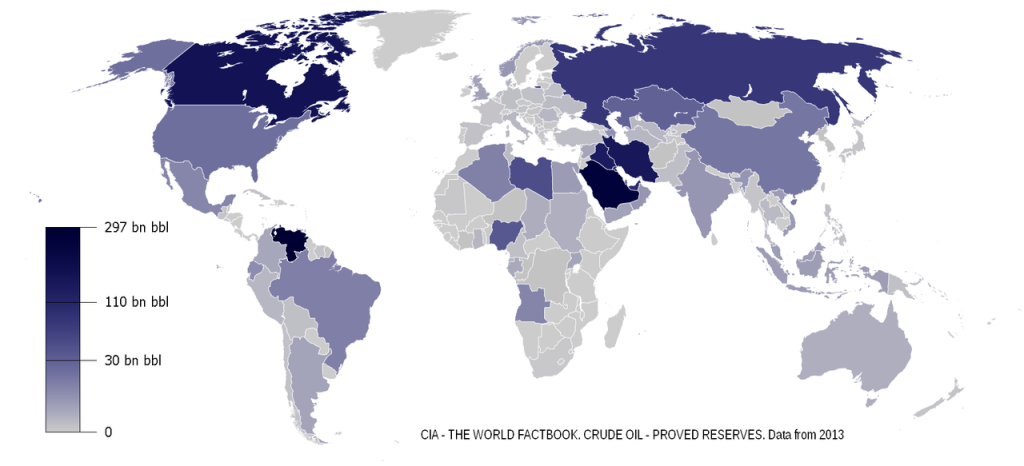
Aplicación práctica de la protección catódica en oleoductos
La protección catódica es uno de los métodos de protección contra la corrosión más utilizados en oleoductos. Su eficacia ha quedado demostrada en numerosos proyectos de todo el mundo, tanto en instalaciones subterráneas como submarinas. En esta sección, analizaremos casos reales de uso de la protección catódica, los retos para su aplicación y las normativas clave del sector.
Aplicación de la protección catódica en diversas condiciones
En los oleoductos que transportan petróleo crudo y sus productos, la protección catódica se utiliza para evitar la corrosión causada por el contacto del metal con el suelo húmedo y las aguas subterráneas. En entornos con baja resistividad del suelo (por ejemplo, zonas húmedas y pantanosas), se utilizan ánodos galvánicos, mientras que en zonas con alta resistividad (por ejemplo, zonas desérticas, suelos secos), debe utilizarse protección PCCI porque el flujo natural de corriente protectora es limitado.
Las tuberías de transmisión en alta mar están expuestas a agua de mar fuerte, que contiene un electrolito fuerte que acelera los procesos de corrosión. En este tipo de entorno, la protección catódica galvánica con ánodos de aluminio o zinc es la solución estándar, ya que proporciona protección a largo plazo sin necesidad de una fuente de alimentación externa. Para grandes estructuras en alta mar, como plataformas petrolíferas y terminales marinas, es más habitual utilizar sistemas PCCI, ya que permiten un control preciso del nivel de protección.
Desafíos en la aplicación de la protección catódica
A pesar de la eficacia de la protección catódica, su implantación está asociada a varios retos técnicos y operativos. Entre los problemas más comunes, se encuentran:
- Diseño inadecuado del sistema: una colocación incorrecta de los ánodos o una especificación errónea de los parámetros de la corriente de protección pueden dar lugar a una protección ineficaz de las tuberías o incluso acelerar los daños locales.
- Variabilidad de las condiciones ambientales: las diferencias en la composición del suelo, la salinidad del agua o la temperatura pueden requerir un ajuste continuo del sistema de protección PCCI para adaptar el nivel de protección a las condiciones de funcionamiento.
- Interferencias con otras instalaciones: en zonas con un gran número de tuberías, cables o infraestructuras eléctricas, puede haber interferencias con el flujo de corriente de protección, lo que requiere un estudio detallado y la optimización del sistema.
- Mantenimiento y supervisión: los sistemas de protección catódica requieren inspecciones y mediciones periódicas para garantizar su eficacia a largo plazo. La falta de una supervisión adecuada puede provocar fallos que pasen inadvertidos y una degradación más rápida de las tuberías.
Normas y reglamentos sobre la protección catódica
La protección catódica en la industria petrolera está estrictamente regulada por normas y estándares internacionales que especifican los requisitos para el diseño, instalación y supervisión de los sistemas de protección. Entre las normas más importantes, se encuentran las siguientes:
- NACE SP0169: una norma internacional desarrollada por la Asociación Nacional de Ingenieros de la Corrosión (NACE) que especifica las reglas para el diseño y mantenimiento de los sistemas de protección catódica para tuberías subterráneas.
- ISO 15589-1: norma internacional que regula la protección catódica de las tuberías de acero y tiene en cuenta tanto los sistemas PCCI como los ánodos galvánicos.
- DNV-RP-F103 – directrices para la protección catódica de tuberías y estructuras submarinas aplicables a la industria offshore.
- EN 12954 – norma europea que especifica los requisitos para la protección catódica de tuberías que transportan hidrocarburos y agua.
El cumplimiento de esta normativa es clave para garantizar la seguridad operativa y una protección eficaz contra la corrosión.
Ventajas de la protección catódica
La protección catódica desempeña un papel clave en la protección de los oleoductos contra la corrosión al garantizar su durabilidad y fiabilidad a largo plazo. Puede reducir eficazmente el riesgo de averías, disminuir los costes de mantenimiento y cumplir los requisitos reglamentarios, lo que la convierte en uno de los métodos más rentables para proteger las infraestructuras de transporte.
Las tuberías propensas a la corrosión requieren inspecciones y reparaciones frecuentes, lo que genera costes de explotación significativos y el riesgo de tiempos de inactividad en el transporte de materias primas. Con la protección catódica, los procesos de corrosión se ralentizan considerablemente o se inhiben por completo, lo que permite prolongar la vida útil de la instalación hasta varias décadas. Esto se traduce en una menor necesidad de sustituir tramos de tuberías, una reducción de las averías y una disminución de los gastos de mantenimiento.
Una protección inadecuada contra la corrosión puede provocar fugas de petróleo y gas, que suponen una grave amenaza para el medio ambiente y pueden acarrear graves sanciones económicas a los operadores de oleoductos. Los sistemas de protección catódica minimizan el riesgo de perforaciones y fugas incontroladas en las tuberías, lo que evita desastres medioambientales y aumenta la seguridad del transporte de crudo.
Además de los aspectos técnicos, la protección catódica también es necesaria para cumplir las normas internacionales de seguridad, como NACE SP0169 e ISO 15589-1, que regulan el uso de medidas de prevención de la corrosión. La aplicación de esta tecnología evita problemas de incumplimiento y reduce los riesgos financieros de posibles sanciones y daños.
Métodos de protección catódica en oleoductos – resumen
La protección catódica es un método indispensable para proteger los oleoductos de la corrosión, ya que garantiza su longevidad y fiabilidad. Reduce eficazmente la degradación del metal, disminuye el riesgo de averías y reduce los costes de mantenimiento.
Los sistemas actuales de protección catódica, apoyados por modernas tecnologías de control y regulación, permiten ajustar eficazmente el nivel de protección a las condiciones cambiantes. Su uso no solo se recomienda, sino que también lo exigen las normas internacionales y los estándares de seguridad, lo que los convierte en una parte indispensable de la gestión de las infraestructuras petrolíferas.
El artículo se basa en el libro Metallurgy and Corrosion Control in Oil and Gas Production, de Robert Heidersbach.