Tolérances dimensionnelles
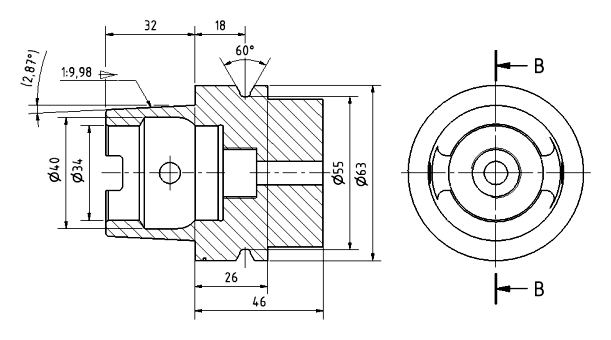
Table des matières
La tolérance dimensionnelle est l’une des plus importantes questions de l’ingénierie et de l’industrie, qui affecte tout à la fois la qualité, la fonctionnalité et les coûts de production. Chaque composant technique, de la vis la plus simple jusqu’aux mécanismes de machines complexes, doit être fabriqué dans une certaine gamme de déviations acceptables, dans le but de garantir, dans le produit fini, un ajustement et un fonctionnement corrects.
La fabrication moderne s’appuie sur des normes de tolérance précises pour équilibrer la qualité et la rentabilité. Des tolérances appropriées permettent d’éviter les problèmes d’assemblage et garantissent que les composants sont compatibles, quel que soit le fabricant.
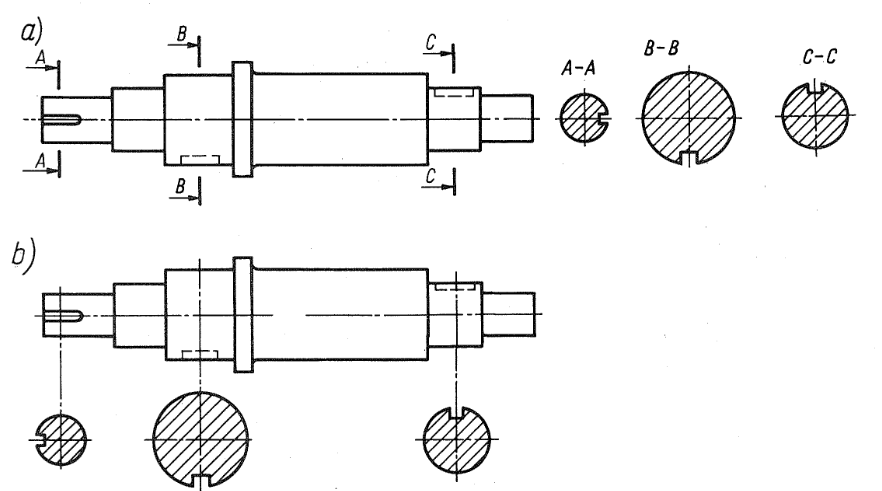
Concepts de base de la tolérance dimensionnelle
La tolérance dimensionnelle définit l’écart admissible des dimensions réelles, par rapport aux dimensions nominales indiquées sur le dessin technique. Les processus de fabrication n’étant pas parfaits, chaque pièce fabriquée diffère, dans une certaine mesure, des dimensions supposées. La tolérance définit les limites dans lesquelles ces différences sont acceptables.
La tolérance est déterminée par deux paramètres clés :
- La dimension nominale (N) – Valeur à laquelle s’applique la tolérance.
- Dimensions ou écarts limites (A et B) – Limites inférieure et supérieure, à l’intérieur desquelles la dimension réelle peut se situer.
- Écarts supérieurs et inférieurs (ES, EI pour les alésages et es, ei pour les arbres) – Différence entre la dimension nominale et les limites.
Les normes internationales, telles que PN-EN ISO 286-1:2011, définissent 20 classes de tolérance, chacune correspondant à différents niveaux de précision, appliqués selon la fonction du composant.
Méthodes de tolérancement dimensionnel
Traditionnellement, les tolérances utilisées sont basées sur des valeurs plus-moins (±), qui indiquent les écarts acceptables, par rapport à la dimension nominale.
Une approche moderne du tolérancement est le système GD&T, Geometrical Dimensioning and Tolerancing, qui permet de spécifier non seulement les écarts dimensionnels, mais aussi les caractéristiques géométriques des composants. Il s’agit d’un système plus précis et plus fonctionnel que les tolérances dimensionnelles ±, traditionnelles, car il prend en compte les dimensions linéaires et les paramètres géométriques essentiels au bon fonctionnement et à l’assemblage des composants.
Le système GD&T permet de contrôler des caractéristiques géométriques telles que :
- La forme du composant, pour citer quelques exemples :
- La planéité – Détermine jusqu’où une surface peut s’écarter d’un plan idéal.
- La rotondité – Garantit que la section transversale d’un arbre ou d’un alésage reste aussi proche que possible d’un cercle idéal.
- Cylindricité – Appliquée aux arbres et aux alésages cylindriques, définissant l’écart maximal admissible par rapport à la forme cylindrique.
- Orientation des composants les uns par rapport aux autres, par exemple :
- Perpendicularité – Spécifie l’écart maximal admissible par rapport à une perpendicularité parfaite entre deux surfaces.
- Parallélisme – Garantit que deux surfaces ou deux axes sont aussi parallèles que possible.
- L’inclinaison – Détermine dans quelle mesure une surface peut s’écarter de l’angle nominal.
- osition des composants dans une disposition, par exemple :
- La position – Détermine si un composant, tel qu’un alésage, se trouve dans la bonne position par rapport à d’autres pièces.
- La circularité du faux-rond – Détermine le faux-rond d’un arbre, d’un orifice ou alésage, par rapport à son axe de rotation.
- Faux-rond des composants en mouvement rotatif, par exemple :
- Le battement axial – Appliqué aux arbres et aux composants rotatifs, détermine la déviation maximale de l’axe par rapport à l’idéal durant la rotation.
- Le battement total – Forme plus restrictive du battement, couvrant tous les points de l’ensemble de la surface tournante.
En pratique, le système GD&T facilite la compatibilité des pièces produites dans différentes usines, réduit le risque de problèmes d’assemblage et permet une gestion efficace de la qualité. C’est pourquoi le système GD&T est utilisé dans les secteurs de l’automobile, de l’aérospatiale, de l’électronique et de la fabrication d’équipements de précision.
Importance des tolérances dans les processus de fabrication
La tolérance dimensionnelle joue un rôle prépondérant dans le processus d’assemblage des composants, car toute imprécision peut affecter la qualité, la durabilité et la fonctionnalité du produit fini. Des tolérances correctement ajustées garantissent que les composants individuels s’assemblent comme le concepteur l’a prévu. Si les tolérances sont trop restrictives ou trop souples, toutes sortes de problèmes d’assemblage peuvent survenir, entraînant une augmentation des coûts de production, des pertes de matériaux, voire la défaillance entière de systèmes.
Un ajustement trop restrictif – Problème dans l’assemblage des composants
L’un des principaux problèmes résultant de mauvaises tolérances est un ajustement trop restrictif, qui rend difficile, voire impossible, l’assemblage des pièces. Cela peut entraîner la nécessité d’un usinage supplémentaire, ce qui augmente les coûts de production et allonge les délais.
Par exemple, si le diamètre d’un arbre est trop grand par rapport à un orifice, il peut être nécessaire d’aléser celui-ci, ou de rectifier l’arbre afin d’assurer un ajustement correct. Ces opérations génèrent des coûts supplémentaires et peuvent largement affecter les propriétés mécaniques du matériau, affaiblissant sa structure.
Lors de l’assemblage de pièces en plastique, un ajustement trop restrictif peut entraîner des fissures ou des déformations sous contrainte, ce qui réduit considérablement la durée de vie du produit. Dans l’industrie automobile ou aérienne, un dépassement, même minime, des limites de tolérance peut entraîner de graves problèmes de fonctionnement, tels qu’une usure accrue des pièces, due à un frottement excessif.
Ajustement trop lâche – Connexions instables
En revanche, un ajustement trop souple signifie que les pièces ne tiennent pas fermement, ce qui peut entraîner des vibrations, un jeu dans l’assemblage et une usure prématurée des connexions. Un ajustement trop lâche est particulièrement dangereux pour les pièces qui doivent supporter des charges dynamiques, telles que les arbres de transmission, les roulements ou les assemblages boulonnés.
Un exemple de mécanisme défaillant est celui d’un alésage trop large par rapport à l’arbre. Il en résulte que le composant n’est pas correctement placé et qu’il risque de glisser pendant le fonctionnement de la machine. Dans les cas extrêmes, cela peut entraîner la défaillance du mécanisme, ce qui nécessite le remplacement coûteux de la pièce, voire de la machine entière.
Dans la construction et les structures en acier, des jeux excessifs peuvent affaiblir l’ensemble de la structure, augmentant le risque de défaillance sous l’effet de forces externes, telles que du vent ou des charges sismiques. Dans de tels cas, des ajustements de précision, avec des normes d’écart parfaitement spécifiées, sont utilisés pour garantir la durabilité et la sécurité.
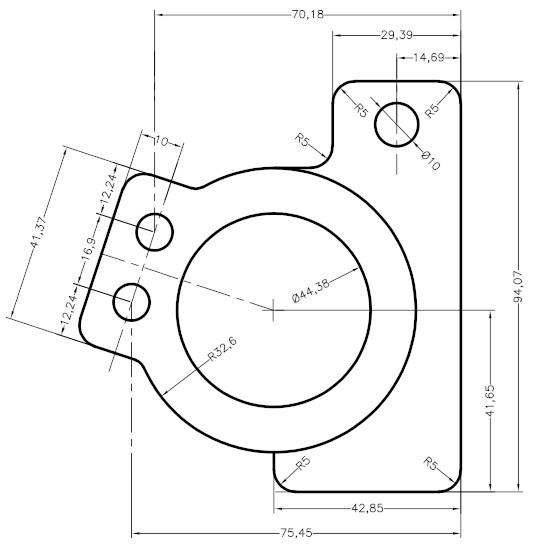
Normes et standards de tolérance dimensionnelle
Les normes internationales réglementent strictement ces tolérances dimensionnelles, précisant les écarts dimensionnels admissibles et la manière dont ils sont indiqués sur les dessins techniques. L’utilisation de ces normes garantit l’uniformité et la répétabilité de la production, facilite la coopération internationale et réduit le risque d’erreurs d’assemblage.
Le tableau suivant présente les normes les plus importantes en matière de tolérances dimensionnelles et leur application :
Norme 11527_3456df-b3> |
Description de l’application 11527_0258ba-79> |
Application 11527_ef5c60-6f> |
---|---|---|
ISO 286 11527_2a2d85-32> |
Définit les classes de tolérance dimensionnelle pour les ajustements d’arbres et d’alésages. Définit les écarts limites et les règles d’ajustement. 11527_a797e3-d4> |
Mécanique de précision, fabrication de composants de machines, ajustements d’alésages et d’arbres. 11527_fe0e0b-22> |
ISO 14405 11527_7a940a-f1> |
Normalise les méthodes de spécification des tolérances dimensionnelles dans les dessins techniques, en particulier pour les dimensions linéaires. 11527_3d20a7-c5> |
Ingénierie mécanique, aérospatiale, automobile. 11527_d14014-20> |
ISO GPS 11527_5ed485-25> |
Système de spécification géométrique des produits. Comprend une approche globale des tolérances géométriques. 11527_74049a-f7> |
Fabrication de précision, CAO/FAO, automatisation du contrôle de la qualité. 11527_4a16d5-94> |
ISO 1101 11527_a0d87d-c7> |
Normalise les marquages de tolérance de forme et de position et définit les symboles et les méthodes de marquage sur les dessins techniques. 11527_490d27-35> |
Contrôle de la qualité, conception de structures de précision. 11527_e3e051-40> |
ISO 8015 11527_7f21fe-db> |
Décrit les règles d’interprétation des dimensions et des tolérances dans l’ISO GPS. 11527_037275-81> |
Universelle pour toutes les industries. 11527_e06a45-4e> |
ASME Y14.5 11527_06fa26-50> |
La norme américaine sur les tolérances géométriques est similaire à la norme ISO 1101, mais elle est principalement utilisée aux États-Unis. 11527_c251c8-aa> |
Aérospatiale, automobile, ingénierie aérospatiale. 11527_9acb44-f0> |
ISO 2768 11527_e799c5-17> |
Définit les tolérances dimensionnelles et angulaires générales pour les composants de précision moyenne. 11527_af4561-dc> |
Production de masse, industrie automobile, construction. 11527_713091-b6> |
Un exemple d’application de la norme ISO 286
La norme ISO 286 définit un système d’ajustements pour les alésages et les arbres, qui est largement utilisé dans l’ingénierie mécanique. Cela signifie que chaque arbre et chaque orifice peut avoir une tolérance spécifique, en fonction de la précision requise. Ce système utilise des désignations sous forme de lettres et de chiffres, telles que :
- H7/g6 – raccord glissant couramment utilisé.
- H6/h5 – ajustement restrictif pour les connexions de précision.
- H8/f7 – ajustement libre, utilisé pour les pièces nécessitant un mouvement libre.
Les normes de tolérance dimensionnelle jouent donc un rôle essentiel dans l’ingénierie et la fabrication. Leur utilisation permet d’obtenir des produits de meilleure qualité, de réduire les coûts associés aux erreurs de fabrication et de garantir que les composants s’emboîteront, même s’ils proviennent de fournisseurs différents. Les systèmes modernes de contrôle de la qualité, tels que ISO GPS, permettent une précision encore plus grande dans la conception et la fabrication des composants, ce qui est indispensable dans l’industrie moderne.
Aspects pratiques de l’utilisation des tolérances
Les tolérances dimensionnelles et géométriques font partie intégrante de la conception et du processus de fabrication de tous les composants mécaniques. Une définition et un contrôle corrects garantissent que ces composants s’assemblent, tels que les ingénieurs l’ont prévu et que l’ensemble du processus de fabrication est optimisé, en termes de coût et de qualité. Ce chapitre explique comment déterminer correctement les tolérances sur les dessins techniques et quelles sont les méthodes de mesure utilisées pour les contrôler.
Comment déterminer les tolérances sur un dessin technique ?
Les dessins techniques sont des documents clés dans la fabrication. Ils doivent donc spécifier clairement les dimensions nominales et les écarts admissibles. Un marquage correct des tolérances permet une lecture sans ambiguïté des spécifications et évite les erreurs d’interprétation qui pourraient entraîner des problèmes d’assemblage ou des coûts d’usinage supplémentaires.
Règles de base pour la détermination des tolérances sur un dessin technique
- Utilisation de marquages appropriés conformément aux normes ISO et ASME
- Les dimensions doivent être indiquées lisiblement, sans répétition inutile.
- Les marques de tolérance géométrique doivent être conformes à la norme ISO 1101 ou ASME Y14.5.
- Les dimensions et leurs tolérances doivent être placées aux endroits appropriés sur le dessin de manière à ne pas gêner la lisibilité.
- Spécifier des tolérances géométriques pour les composants clés
- Au lieu d’utiliser les tolérances classiques ± pour chaque dimension, il est utile d’utiliser des tolérances géométriques qui représentent mieux la fonctionnalité du composant.
- Par exemple, la tolérance de planéité est importante pour les surfaces tangentielles, et le parallélisme est crucial pour les glissières et les paliers lisses.
- Les dimensions importantes pour le montage doivent être désignées comme des cotes de contrôle (par exemple, K, C dans la documentation technique).
- Éviter de trop restreindre les tolérances si ce n’est pas nécessaire
- Une erreur de conception courante consiste à adopter des tolérances très restrictives, qui augmentent les coûts de fabrication.
- Utiliser des classes de tolérance adaptées à la fonction de la pièce. Pour les pièces de précision, telles que les roulements, il est utile d’utiliser les classes IT6, et pour les pièces structurelles, les classes IT10-IT12 suffisent.
- Selon la norme ISO 2768, des tolérances générales peuvent être utilisées pour les pièces qui ne nécessitent pas une grande précision de fabrication.
- Assurer la compatibilité avec les méthodes de mesure
- Les tolérances doivent être choisies de manière à pouvoir être contrôlées avec les outils de mesure disponibles.
- Par exemple, si la tolérance est inférieure à 0,01 mm, les pieds à coulisse standard risquent de ne pas offrir une précision suffisante et une machine à mesurer tridimensionnellement (MMT) sera nécessaire.
Méthodes de contrôle dimensionnel
Méthode de mesure 11527_1dad69-22> |
Description de la méthode 11527_e13747-a1> |
Champ d’application 11527_39b059-30> |
---|---|---|
Pied à coulisse 11527_599122-bc> |
Outil simple pour mesurer la longueur, le diamètre et la profondeur, avec une précision de 0,02 mm. 11527_7f35ae-20> |
Production générale, contrôle dimensionnel rapide. 11527_101278-75> |
Micromètre 11527_61cb77-e9> |
Outil permettant de mesurer avec précision des diamètres à 0,001 mm près. 11527_1203cf-e4> |
Contrôle des dimensions critiques. 11527_c0ffdc-0f> |
Jauge à cadran (jauge d’indexation) 11527_5665f3-0e> |
Utilisé pour vérifier le battement axial et la perpendicularité des surfaces. 11527_16f11b-18> |
Inspection des arbres, des engrenages et des roulements. 11527_6cd46b-ae> |
Machine à mesurer tridimensionnelle (MMT) 11527_023c03-f3> |
Système de numérisation 3D avancé qui mesure avec précision les tolérances géométriques et de position. 11527_e1b5e0-b2> |
Aérospatiale, mécanique de précision, automobile. 11527_bf86af-a2> |
Projecteur de mesure (profilomètre) 11527_997029-7a> |
Méthode optique de mesure des contours et des profils de surface. 11527_8acb5c-d2> |
Inspection de pièces de forme complexe. 11527_fed4c1-24> |
Scanner laser 3D 11527_6105d8-27> |
Un système de balayage sans contact est utilisé pour analyser la surface entière d’un objet. 11527_c6d3ae-66> |
Analyse des écarts dans la technologie CAO, l’impression 3D. 11527_c03325-8e> |
Les aspects pratiques de l’utilisation des tolérances comprennent la détermination précise des écarts admissibles sur les dessins techniques, ainsi que des méthodes efficaces pour les contrôler. L’utilisation des bonnes normes et des bons outils de mesure peut minimiser le risque d’erreurs de production, garantir un assemblage correct, et optimiser les coûts de production. Les technologies actuelles, telles que l’analyse statistique des processus et les systèmes de mesure avancés, permettent un contrôle encore plus précis des dimensions et des tolérances.
Tolérances dimensionnelles – Résumé
La sélection appropriée des tolérances dimensionnelles est cruciale pour garantir un assemblage correct des composants dans diverses industries. Des tolérances inappropriées peuvent entraîner des problèmes d’ajustement qui augmentent les coûts, des pertes de matériaux et une qualité de produit qui est compromise. Les ingénieurs doivent donc analyser soigneusement les exigences en matière de tolérance, en tenant compte des aspects fonctionnels et économiques, afin de garantir la fiabilité et l’efficacité des processus d’assemblage.