Aluminium i jego stopy
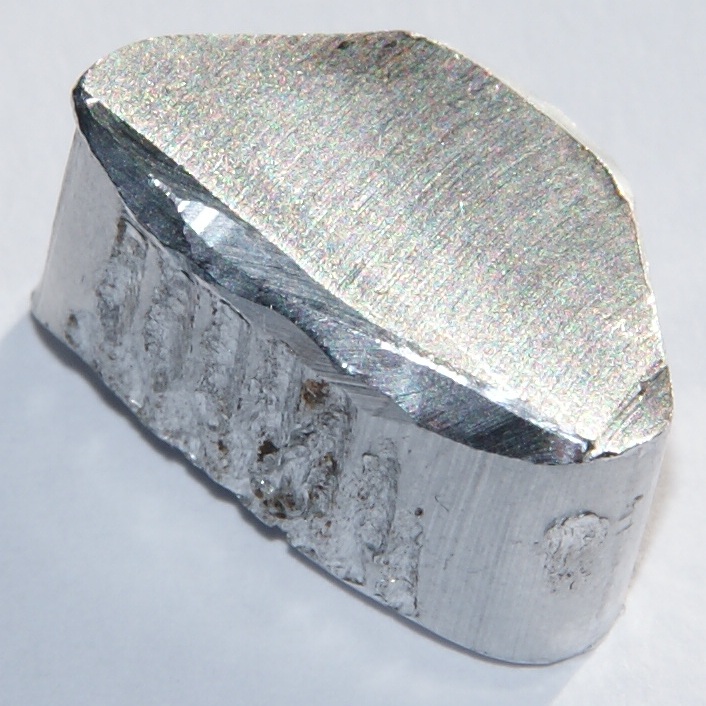
Spis treści
Charakterystyka aluminium jako metalu konstrukcyjnego
Aluminium jest jednym z najczęściej wykorzystywanych metali w przemyśle, a jego znaczenie nieustannie rośnie – zarówno w zastosowaniach inżynierskich, jak i codziennych produktach użytkowych. Jako pierwiastek chemiczny wyróżnia się niską gęstością, dobrą przewodnością cieplną i elektryczną oraz wysoką odpornością na korozję, co czyni go materiałem niezwykle atrakcyjnym w kontekście nowoczesnych konstrukcji.
Jedną z jego najbardziej charakterystycznych cech jest niewielka masa właściwa, wynosząca około 2,7 g/cm³, co sprawia, że jest blisko trzy razy lżejszy od stali. W połączeniu z wystarczającą wytrzymałością mechaniczną, właściwość ta pozwala znacznie zmniejszyć masę konstrukcji bez rezygnacji z jej funkcjonalności. W branżach takich jak transport, lotnictwo, przemysł kosmiczny czy motoryzacja, każdy zaoszczędzony kilogram ma znaczenie – i to właśnie tam aluminium znajduje swoje naturalne zastosowanie.
Czyste aluminium nie odznacza się wysoką wytrzymałością mechaniczną, jednak jego największy potencjał ujawnia się dopiero w postaci stopów, które dzięki dodatkom pierwiastków takich jak miedź, magnez, krzem, mangan czy cynk, uzyskują znacznie lepsze parametry wytrzymałościowe, twardościowe i technologiczne. To właśnie stopy aluminium stanowią podstawę jego przemysłowego sukcesu – umożliwiając produkcję elementów lekkich, trwałych, odpornych na zużycie i łatwych w dalszej obróbce.
Oprócz tego, aluminium jest również materiałem bardzo dobrze podatnym na recykling. Jego ponowne przetwarzanie wymaga zaledwie ułamka energii zużywanej przy produkcji pierwotnej, co czyni go surowcem przyjaznym dla środowiska i opłacalnym ekonomicznie. To połączenie właściwości fizycznych, technologicznych i ekologicznych sprawia, że aluminium pozostaje nie tylko surowcem strategicznym, ale też symbolem nowoczesnego podejścia do inżynierii materiałowej.
Podstawowe cechy i typy technicznego aluminium
W praktyce przemysłowej rzadko wykorzystuje się czyste aluminium w jego chemicznie idealnej postaci. Zamiast tego stosuje się tak zwane aluminium techniczne, które – choć nadal zawiera dominujący udział glinu – zawiera również śladowe ilości innych pierwiastków, takich jak żelazo, krzem, mangan, miedź czy cynk. Te dodatki są efektem ubocznym procesu produkcyjnego lub celowo pozostawionymi składnikami, które wpływają na właściwości materiału.
Jednym z najbardziej rozpoznawalnych walorów technicznego aluminium jest jego łatwość formowania i obróbki, zarówno plastycznej, jak i mechanicznej. Materiał ten można walcować, tłoczyć, ciągnąć i giąć bez istotnego ryzyka pękania czy utraty ciągłości strukturalnej. To właśnie dlatego znajduje zastosowanie w produkcji cienkościennych elementów konstrukcyjnych, profili, rur oraz komponentów o skomplikowanych kształtach.
Ważną cechą aluminium technicznego jest również jego stosunkowo niska temperatura topnienia, mieszcząca się w przedziale od około 650°C do 660°C. W porównaniu do stali czy innych metali konstrukcyjnych jest to wartość relatywnie niska, co ułatwia przetwarzanie cieplne i odlewanie, ale jednocześnie narzuca ograniczenia przy pracy w warunkach wysokotemperaturowych.
Aluminium wykazuje także bardzo dobrą przewodność cieplną i elektryczną, co sprawia, że oprócz funkcji mechanicznych, pełni często również rolę materiału przewodzącego – szczególnie tam, gdzie waga i odporność na korozję mają znaczenie większe niż ekstremalna przewodność, jak ma to miejsce w liniach wysokiego napięcia czy radiatorach.
Typy technicznego aluminium można podzielić ze względu na stopień czystości. Aluminium o czystości powyżej 99% zachowuje większość cech fizycznych aluminium pierwotnego – jak wysoka plastyczność, niska wytrzymałość i doskonała odporność korozyjna. Niższe klasy czystości – na przykład zawierające ok. 98% glinu – mają nieco niższe parametry antykorozyjne, ale mogą być bardziej atrakcyjne z punktu widzenia ekonomii produkcji i dostępności surowców wtórnych.
Należy podkreślić, że techniczne aluminium stanowi bazę dla dalszego stopowania. Jego czystość, struktura i domieszki są punktem wyjścia do opracowywania stopów specjalistycznych, w których aluminium przestaje być jedynie tłem dla dodatków, a staje się fundamentem nowej klasy materiałów konstrukcyjnych o rozszerzonym zastosowaniu.
Właściwości i zastosowanie stopów aluminium
To właśnie w postaci stopów aluminium ukazuje swój pełny potencjał jako materiał konstrukcyjny – nie tylko lekki i odporny na korozję, ale też wytrzymały, podatny na obróbkę cieplną i możliwy do dostosowania do bardzo zróżnicowanych warunków pracy. Dodanie do aluminium innych pierwiastków – takich jak miedź, krzem, cynk, magnez czy mangan – pozwala radykalnie zmienić jego właściwości, czyniąc ze stopów glinu grupę materiałów o niemal nieograniczonych możliwościach inżynierskich.
Najważniejszym osiągnięciem w zakresie stopów aluminium jest możliwość kontrolowania ich struktury przez odpowiednie procesy obróbki cieplnej. Dzięki hartowaniu, przesycaniu, starzeniu i wyżarzaniu można regulować ich twardość, sprężystość, odporność na pełzanie i plastyczność. Stop, który w stanie surowym może być miękki i łatwo odkształcalny, po starzeniu staje się materiałem o właściwościach zbliżonych do niektórych stali węglowych.
Wyjątkową cechą stopów aluminium jest także ich naturalna odporność na korozję atmosferyczną. Cienka warstwa tlenku glinu, tworząca się na powierzchni niemal natychmiast po kontakcie z tlenem, chroni materiał przed głębszym utlenieniem. W połączeniu z niską gęstością sprawia to, że stopy aluminium są szeroko stosowane wszędzie tam, gdzie ważna jest jednocześnie trwałość, lekkość i długowieczność – na przykład w lotnictwie, budowie statków, w konstrukcjach mostowych, a także w nowoczesnych pojazdach elektrycznych.
Kolejną istotną cechą jest wysoka podatność stopów aluminium na obróbkę plastyczną. Niezależnie od tego, czy materiał jest walcowany, tłoczony, ciągniony czy kształtowany metodami objętościowymi – odpowiednio dobrane stopy zachowują wymaganą ciągliwość i odporność na pękanie, umożliwiając produkcję cienkościennych, złożonych elementów, których wykonanie z innych metali byłoby trudniejsze lub mniej ekonomiczne.
Kluczowe układy fazowe stopów aluminium
Zrozumienie właściwości i zachowania stopów aluminium nie jest możliwe bez odwołania się do ich układów fazowych, które opisują relacje między temperaturą, składem chemicznym i strukturą wewnętrzną materiału. To właśnie te układy decydują o tym, jakie fazy mogą powstać w stopie, w jakich warunkach następują przemiany fazowe i jaką strukturę końcową uzyska się po zakończeniu procesu technologicznego.
W przypadku aluminium, kluczowe znaczenie mają układy fazowe dwu- i trójskładnikowe, w których glin jest łączony z takimi pierwiastkami jak miedź, krzem, cynk, magnez czy mangan. Te kombinacje tworzą charakterystyczne strefy przemian fazowych, w których można wyróżnić obszary roztworów stałych, mieszanin dwu- lub wielofazowych oraz strefy eutektyczne lub perytektyczne.
Jednym z najważniejszych układów jest układ aluminium–miedź, będący podstawą wielu stopów utwardzanych wydzieleniowo. W tym przypadku najistotniejszą fazą wtórną jest Al₂Cu, która powstaje w wyniku kontrolowanego starzenia i odpowiada za znaczny wzrost twardości oraz wytrzymałości na rozciąganie. Układ ten znajduje zastosowanie w stopach typu duraluminium, używanych powszechnie w przemyśle lotniczym.
Podobnie istotny jest układ aluminium–krzem, który dominuje w stopach odlewniczych. Obecność krzemu poprawia lejność i odporność na ścieranie, a przy odpowiednim rozdrobnieniu eutektyki Al–Si umożliwia uzyskanie bardzo korzystnego kompromisu między wytrzymałością a przetwarzalnością. Takie stopy są często używane w odlewach silnikowych, elementach maszyn i obudowach mechanicznych.
Równie ważny jest układ aluminium–magnez, który odpowiada za powstanie stopów o bardzo dobrej odporności korozyjnej i jednocześnie stosunkowo niskiej masie właściwej. Stopy tego typu, choć mniej wytrzymałe od układów z miedzią czy cynkiem, są idealnym materiałem do zastosowań morskich i konstrukcji lekkich narażonych na działanie wilgoci i soli.
Z kolei układ aluminium–cynk pozwala na uzyskanie bardzo wysokiej wytrzymałości mechanicznej, szczególnie po obróbce cieplnej. W połączeniu z magnezem i miedzią tworzy bazę dla najbardziej zaawansowanych technologicznie stopów, które – mimo mniejszej odporności korozyjnej – są stosowane tam, gdzie kluczowa jest maksymalna wytrzymałość przy minimalnej masie.
Każdy z tych układów stanowi naukową mapę przemian strukturalnych, której znajomość jest niezbędna nie tylko dla metalurga, ale również dla każdego inżyniera pracującego z materiałami konstrukcyjnymi. To właśnie układy fazowe pozwalają przewidywać, modelować i projektować zachowanie stopu nie tylko w laboratorium, ale przede wszystkim w warunkach rzeczywistych, przemysłowych zastosowań.
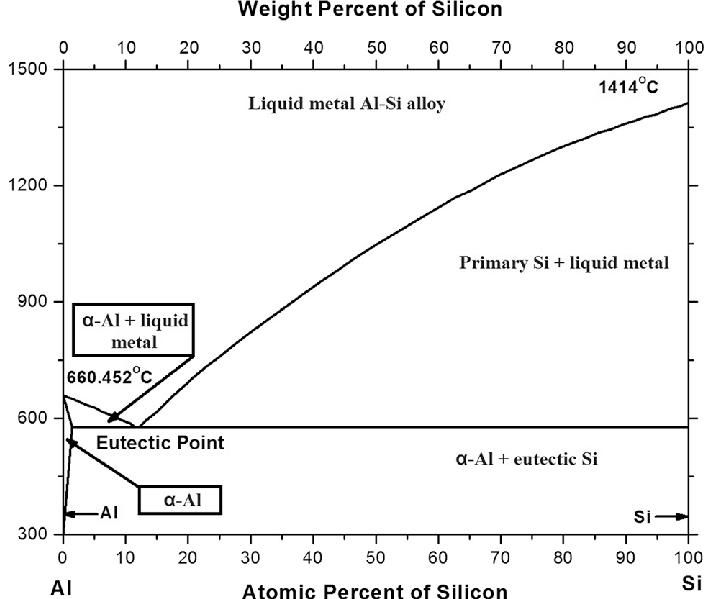
Odlewnicze stopy aluminium i ich modyfikacja
Wśród różnych typów stopów aluminium szczególne miejsce zajmują stopy odlewnicze, które znajdują zastosowanie tam, gdzie kluczowe jest uzyskanie złożonych kształtów bez konieczności obróbki mechanicznej. Ich popularność wynika nie tylko z właściwości samego aluminium, ale także z możliwości precyzyjnego sterowania strukturą podczas procesu krzepnięcia.
Podstawowym składnikiem większości odlewniczych stopów glinu jest krzem, który pełni kilka niezwykle istotnych funkcji. Przede wszystkim znacząco obniża temperaturę topnienia stopu, co poprawia jego lejność, umożliwiając wypełnienie nawet skomplikowanych form odlewniczych. Jednocześnie krzem wpływa korzystnie na odporność na ścieranie oraz stabilność wymiarową odlewów. Jednak surowa struktura eutektyki aluminium–krzem, powstająca w wyniku swobodnego krzepnięcia, nie zawsze gwarantuje optymalne właściwości mechaniczne.
Dlatego właśnie w przemyśle odlewniczym szeroko stosuje się modyfikację tych stopów – czyli kontrolowane wprowadzanie dodatków, które wpływają na kształt i rozdrobnienie wydzieleń fazowych. Kluczowym celem modyfikacji jest przekształcenie igiełkowatej, ostrej struktury krzemowej w postać bardziej kulistą i drobną, co poprawia ciągliwość, udarność oraz ogólną wytrzymałość materiału. Do najczęściej stosowanych modyfikatorów należą pierwiastki takie jak sód, stront czy tytan – każdy z nich działa na innym etapie procesu krzepnięcia, ale wszystkie mają jeden wspólny cel: uczynić strukturę odlewu bardziej jednorodną i mechaniczną.
Warto zauważyć, że odlewnicze stopy aluminium są materiałem silnie zależnym od technologii przetwórstwa. Nawet najlepiej zaprojektowany skład chemiczny nie przyniesie oczekiwanych efektów bez odpowiedniego prowadzenia procesu topienia, oczyszczania ciekłego metalu, zalewania formy i chłodzenia. Każdy z tych etapów może wpływać na rozmieszczenie faz, wielkość ziarna i poziom porowatości, co w konsekwencji przekłada się na właściwości użytkowe gotowego wyrobu.
Stopy odlewnicze, odpowiednio zmodyfikowane i przetworzone, stają się materiałami nie tylko funkcjonalnymi, ale też efektywnymi ekonomicznie – pozwalając na szybkie, masowe wytwarzanie elementów o skomplikowanej geometrii i wysokich wymaganiach eksploatacyjnych. Ich rola w przemyśle motoryzacyjnym, elektrotechnicznym czy budowlanym jest dziś nie do przecenienia, a dalszy rozwój technologii modyfikacji i obróbki tylko wzmacnia ich pozycję wśród nowoczesnych materiałów konstrukcyjnych.
Hydronalium i duraluminium
Obok stopów odlewniczych, równie ważną grupę materiałów aluminiowych stanowią stopy przeznaczone do przeróbki plastycznej. Ich skład chemiczny i struktura są dostosowane do warunków walcowania, tłoczenia, kucia czy ciągnienia, co pozwala na formowanie materiału w żądany kształt bez jego przetopienia. Spośród nich szczególną rolę odgrywają hydronalium i duraluminium – dwa rodzaje stopów, które przez dekady wyznaczały standardy nowoczesnej inżynierii materiałowej.
Hydronalium to nazwa handlowa obejmująca stopy aluminium z dodatkiem magnezu i niewielkich ilości manganu. Główną zaletą tego materiału jest wyjątkowa odporność na korozję, także w środowiskach morskich i chemicznych. To właśnie ta cecha, w połączeniu z dobrą ciągliwością i możliwością spawania, uczyniła hydronalium jednym z ulubionych materiałów w przemyśle okrętowym, budowie zbiorników oraz elementów narażonych na działanie wilgoci i soli. Choć jego wytrzymałość mechaniczna jest umiarkowana, jest ona wystarczająca w zastosowaniach, w których ważniejsza jest trwałość chemiczna niż sztywność konstrukcyjna.
Z kolei duraluminium to stop o zupełnie innym charakterze. Głównym dodatkiem stopowym jest tu miedź, a czasem również magnez, mangan i krzem. Dzięki odpowiednio prowadzonemu hartowaniu i starzeniu, duraluminium osiąga bardzo wysoką wytrzymałość mechaniczną – porównywalną z niektórymi stalami konstrukcyjnymi – przy zachowaniu znacznie niższej gęstości. To sprawia, że stopy te są szeroko wykorzystywane w przemyśle lotniczym, gdzie każdy gram masy ma znaczenie, a jednocześnie materiał musi sprostać wysokim obciążeniom.
Warto jednak pamiętać, że duraluminium ma ograniczoną odporność na korozję, szczególnie w obecności wilgoci i związków chemicznych. Z tego powodu często stosuje się dodatkowe zabezpieczenia powierzchniowe – anodowanie, lakierowanie lub powlekanie innymi stopami glinu, które poprawiają jego trwałość w środowisku agresywnym. Takie połączenie wytrzymałości i odpowiednio dobranej ochrony powierzchni pozwala wykorzystywać durale w strukturach nośnych samolotów, mostów kompozytowych czy elementów ramowych pojazdów specjalnych.
Oba typy stopów – zarówno hydronalium, jak i duraluminium – są dowodem na to, jak różnorodne może być zastosowanie aluminium, jeśli odpowiednio dobierzemy skład chemiczny i technologię przetwarzania. To nie sam glin decyduje o właściwościach materiału, lecz sposób, w jaki nauka i technika wykorzystują jego potencjał.
Aluminium i jego stopy – podsumowanie
Aluminium, choć przez długi czas pozostawało w cieniu żelaza i jego stopów, dziś znajduje się w centrum uwagi inżynierów, projektantów i technologów na całym świecie. Jego unikalne połączenie niskiej masy, odporności na korozję, przewodności cieplnej oraz możliwości kształtowania struktury poprzez dodatki stopowe czyni z niego materiał nie tylko wszechstronny, ale wręcz niezastąpiony w wielu gałęziach przemysłu.
Współczesna inżynieria materiałowa nie ogranicza się już do wykorzystywania aluminium jako metalu lekkiego – traktuje je jako platformę do tworzenia materiałów funkcjonalnych, dostosowanych do ekstremalnie różnorodnych wymagań. Dzięki możliwościom obróbki cieplnej, plastycznej i powierzchniowej, stopy aluminium mogą być optymalizowane pod kątem konkretnych parametrów: wytrzymałości, plastyczności, odporności chemicznej, przewodności czy trwałości zmęczeniowej.
Co więcej, recykling aluminium stanowi wzór dla zrównoważonego rozwoju w przemyśle materiałowym. Ponowne wykorzystanie tego metalu wiąże się z minimalnym zużyciem energii i nie powoduje istotnej utraty jego właściwości, co czyni go materiałem w pełni zgodnym z ideą gospodarki obiegu zamkniętego.
Rola aluminium i jego stopów nie ogranicza się do przemysłu lotniczego, motoryzacji czy budownictwa. Znajduje ono również zastosowanie w elektronice, energetyce, medycynie, transporcie publicznym, a nawet w architekturze nowoczesnych miast. Niezależnie od branży, aluminium oferuje połączenie lekkości z siłą, odporności z łatwością przetwarzania, i to właśnie ta elastyczność czyni je materiałem przyszłości.
Zrozumienie jego właściwości, technologii przetwarzania i wpływu dodatków stopowych pozwala inżynierom świadomie projektować komponenty, które nie tylko spełniają wymogi techniczne, ale również odpowiadają na rosnące oczekiwania związane z efektywnością energetyczną, trwałością i ekologicznym śladem produkcji. Aluminium nie jest już alternatywą – jest standardem nowoczesnego projektowania.