Rozměrové tolerance
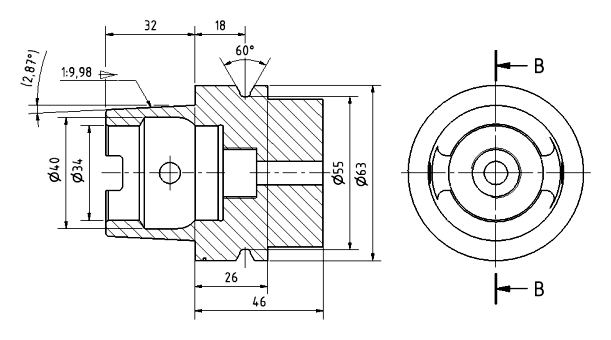
Obsah
Rozměrová tolerance je jedním z klíčových problémů ve strojírenství a průmyslu, který ovlivňuje kvalitu, funkčnost a výrobní náklady. Každá technická součást, od nejjednoduššího šroubku až po složité strojní mechanismy, musí být vyrobena v určitém rozsahu přípustných odchylek, aby bylo zajištěno správné uložení a funkce hotového výrobku.
Moderní výroba se spoléhá na přesné toleranční normy, aby vyvážila kvalitu a nákladovou efektivitu. Vhodné tolerance zabraňují problémům při montáži a zajišťují kompatibilitu komponentů bez ohledu na výrobce.
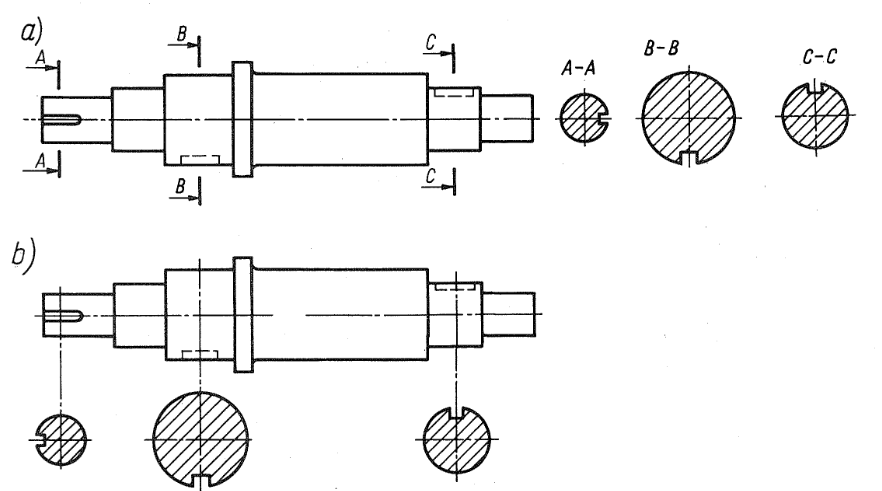
Základní pojmy rozměrové tolerance
Rozměrová tolerance definuje přípustnou odchylku rozměrů od jmenovitých rozměrů technického výkresu, což jsou skutečné rozměry od jmenovitých rozměrů uvedených na technickém výkresu. Protože výrobní procesy nejsou dokonalé, každý vyrobený díl se do určité míry liší od předpokládaných rozměrů. Tolerance definuje meze, v nichž jsou tyto rozdíly přijatelné.
Tolerance je určena dvěma klíčovými parametry:
- Nominální rozměr (N) – hodnota, na kterou se tolerance vztahuje.
- Mezní rozměry (A a B) – dolní a horní mez, do které se může skutečný rozměr vejít.
- Horní a dolní úchylky (Es, Ei pro díry a es, ei pro hřídele) – rozdíl mezi jmenovitým rozměrem a mezními hodnotami.
Mezinárodní normy, například PN-EN ISO 286-1:2011, definují 20 tolerančních tříd, z nichž každá odpovídá různým úrovním přesnosti, které se uplatňují podle funkce součásti.
Metody rozměrového tolerování
Tradičně používané tolerance jsou založeny na hodnotách plus minus, které označují přípustné odchylky od jmenovitého rozměru.
Moderním přístupem k tolerování je systém GD&T (Geometrical Dimensioning and Tolerancing) , který umožňuje specifikovat nejen úchylky rozměrů, ale také geometrické vlastnosti součástí. Jedná se o přesnější a funkčnější systém než tradiční rozměrové tolerance ±, protože zohledňuje lineární rozměry a geometrické parametry rozhodující pro správnou funkci a montáž součástí.
Systém GD&T umožňuje kontrolu takových geometrických prvků, jako jsou:
- Tvar součásti, např.:
- Plochost – určuje, jak moc se povrch může odchýlit od ideální roviny.
- Kulatost – zajišťuje, aby průřez hřídele nebo otvoru zůstal co nejblíže ideálnímu kruhu.
- Válcovitost – uplatňuje se u válcových hřídelí a děr a definuje maximální přípustnou odchylku od válcového tvaru.
- Orientace součástí vůči sobě, např:
- Kolmost – určuje maximální přípustnou odchylku od dokonalé kolmosti mezi dvěma povrchy.
- Rovnoběžnost – zajišťuje, aby dvě plochy nebo osy byly co nejvíce rovnoběžné.
- Sklon – určuje, jak moc se může plocha odchýlit od jmenovitého úhlu.
- Poloha součástí v rozvržení, např:
- Pozice – kontroluje, zda je součást (například otvor) ve správné poloze vzhledem k ostatním dílům.
- Kruhovitost vybíhání – určuje, jak moc může hřídel nebo otvor „vybíhat“ vzhledem k ose otáčení.
- Běžkování součástí při rotačním pohybu, např:
- Axiální házivost – aplikovaná na hřídele a rotační součásti, určuje maximální odchylku osy od ideálu během rotace.
- Celková házivost – přísnější forma házivosti, která zahrnuje všechny body na celé rotující ploše.
V praxi GD&T usnadňuje zajištění kompatibility dílů vyráběných v různých závodech, snižuje riziko problémů při montáži a umožňuje efektivní řízení kvality. Díky tomu se systém GD&T používá v automobilovém, leteckém a kosmickém průmyslu, při výrobě elektroniky a přesných zařízení.
Význam tolerancí ve výrobních procesech
Rozměrové tolerance hrají v procesu montáže součástí klíčovou roli, protože jakákoli nepřesnost může ovlivnit kvalitu, trvanlivost a funkčnost hotového výrobku. Vhodně nastavené tolerance zajišťují, že jednotlivé součásti do sebe zapadají tak, jak konstruktér zamýšlel. Pokud jsou tolerance příliš omezující nebo volné, může dojít k nejrůznějším problémům při montáži, což vede ke zvýšení výrobních nákladů, materiálovým ztrátám, a dokonce k selhání celých systémů.
Příliš těsné uložení – problém při montáži součástí
Jedním z hlavních problémů vyplývajících ze špatných tolerancí je příliš těsné lícování, které ztěžuje nebo dokonce znemožňuje montáž dílů. To může vést k nutnosti dodatečného obrábění, což zvyšuje výrobní náklady a prodlužuje dodací lhůty.
Pokud je například průměr hřídele vzhledem k otvoru příliš velký, může být nutné otvor vystružit nebo hřídel vybrousit, aby se zajistilo správné uložení. Takové operace vyvolávají dodatečné náklady a mohou také ovlivnit mechanické vlastnosti materiálu a oslabit jeho strukturu.
Při montáži plastových dílů může příliš těsné uložení vést k praskání nebo deformaci pod napětím, což výrazně snižuje životnost výrobku. V automobilovém nebo leteckém průmyslu může i minimální překročení tolerančních mezí vést k vážným provozním problémům, například ke zvýšenému opotřebení dílů v důsledku nadměrného tření.
Příliš volné uložení – nestabilní spoje
Příliš volné uložení naopak znamená, že díly nedrží pevně, což může vést k vibracím, montážním vůlím a předčasnému opotřebení spojů. Volné uložení je nebezpečné zejména u dílů, které musí přenášet dynamické zatížení, jako jsou hnací hřídele, ložiska nebo šroubové spoje.
Příkladem selhání mechanismu je příliš široký otvor vzhledem k hřídeli. To má za následek, že součást není správně usazena a může během provozu stroje sklouznout. V extrémních případech to může vést k selhání mechanismu, což má za následek nutnost nákladné výměny součásti nebo dokonce celého stroje.
U stavebních a ocelových konstrukcí mohou nadměrné vůle oslabit celou konstrukci a zvýšit riziko selhání při působení vnějších sil, jako je vítr nebo seismické zatížení. V takových případech se k zajištění trvanlivosti a bezpečnosti používají přesná uložení se stanovenými normami úchylek.
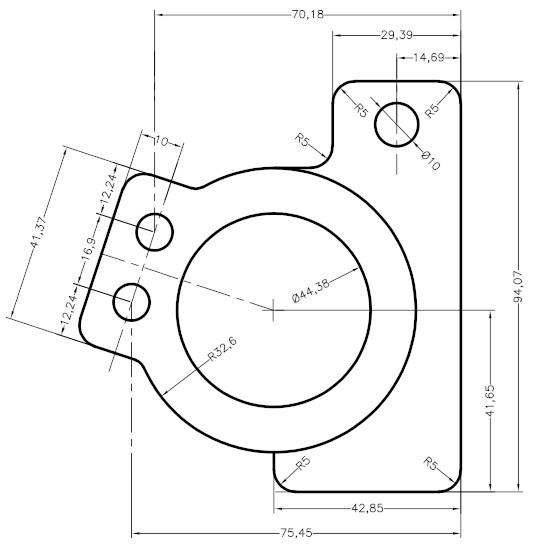
Rozměrové tolerance a normy
Mezinárodní normy přísně upravují rozměrové tolerance. Tyto normy určují přípustné odchylky rozměrů a způsob jejich vyznačení na technických výkresech. Používání těchto norem zajišťuje jednotnost a opakovatelnost výroby, usnadňuje mezinárodní spolupráci a snižuje riziko montážních chyb.
V následující tabulce jsou uvedeny nejdůležitější normy pro rozměrové tolerance a jejich použití:
Norma 11590_058580-12> |
Popis 11590_2efa50-4f> |
Aplikace 11590_462d7c-00> |
---|---|---|
ISO 286 11590_b74c1a-82> |
Definuje třídy rozměrových tolerancí pro uložení hřídelů a otvorů. Definuje mezní úchylky a pravidla uložení 11590_ca8dbc-6b> |
Přesná mechanika, výroba strojních součástí, díry a uložení hřídelí 11590_3f16ef-f9> |
ISO 14405 11590_939da2-89> |
Normalizuje způsoby uvádění rozměrových tolerancí v technických výkresech, zejména pro lineární rozměry 11590_53bae7-23> |
Strojírenství, letectví, automobilový průmysl 11590_d64f75-42> |
ISO GPS 11590_a623ff-a5> |
Systém geometrické specifikace výrobku – zahrnuje holistický přístup ke geometrickým tolerancím 11590_640a39-98> |
Přesná výroba, CAD/CAM, automatizace kontroly kvality 11590_3f2ee2-1b> |
ISO 1101 11590_02ad3d-74> |
Standardizuje značení tolerance tvaru a polohy a definuje symboly a metody značení na technických výkresech 11590_cde4f3-2e> |
Kontrola kvality, navrhování přesných konstrukcí 11590_a0fa5f-4d> |
ISO 8015 11590_42fe5a-88> |
Popisuje pravidla pro interpretaci rozměrů a tolerancí v ISO GPS 11590_065273-0f> |
Univerzální pro všechna průmyslová odvětví 11590_a0d1cd-b5> |
ASME Y14.5 11590_f73a97-dc> |
Americká norma pro geometrické tolerance je podobná normě ISO 1101, ale používá se hlavně v USA 11590_05c4b6-2f> |
Letecký a kosmický průmysl, automobilový průmysl, letecká technika 11590_592908-a3> |
ISO 2768 11590_22b0bb-37> |
Definuje obecné rozměrové a úhlové tolerance pro středně přesné součásti 11590_8e1ae0-c4> |
Sériová výroba, automobilový průmysl, stavebnictví 11590_9427cc-6e> |
Příklad použití normy ISO 286
Norma ISO 286 definuje systém uložení otvorů a hřídelů, který je široce používán ve strojírenství. To znamená, že každá hřídel a díra může mít určitou toleranci v závislosti na požadované přesnosti. Tento systém používá písmenné a číselné označení, např:
- H7/g6 – běžně používané prokluzové uložení.
- H6/h5 – tlačné uložení pro přesné spoje.
- H8/f7 – volné uložení, používá se pro díly vyžadující volný pohyb.
Rozměrové toleranční normy hrají klíčovou roli ve strojírenství a výrobě. Jejich používání umožňuje vyrábět kvalitnější výrobky, snižuje náklady spojené s výrobními chybami a zajišťuje, že součásti do sebe budou zapadat, i když pocházejí od různých dodavatelů. Moderní systémy kontroly kvality, jako je ISO GPS, umožňují ještě větší přesnost při navrhování a výrobě součástí, což je v moderním průmyslu nezbytné.
Praktické aspekty používání tolerancí
Rozměrové a geometrické tolerance jsou nedílnou součástí konstrukce a výrobního procesu mechanických součástí. Správná definice a kontrola zajišťují, že součásti do sebe zapadají tak, jak konstruktéři zamýšleli a že celý výrobní proces je optimalizován z hlediska nákladů a kvality. Tato kapitola pojednává o tom, jak správně určit tolerance na technických výkresech a jaké metody měření se používají k jejich kontrole.
Jak určit tolerance na technickém výkresu?
Technické výkresy jsou klíčovým dokumentem ve výrobě, proto musí jasně specifikovat jmenovité rozměry a přípustné odchylky. Správné označení tolerancí umožňuje jednoznačné čtení specifikací a zabraňuje interpretačním chybám, které by mohly vést k problémům při montáži nebo dodatečným nákladům na obrábění.
Základní pravidla pro určování tolerancí na technickém výkresu
- Používání vhodných značek v souladu s normami ISO a ASME
- Rozměry by měly být uvedeny čitelně, bez zbytečného opakování.
- Označení geometrických tolerancí musí být v souladu s normou ISO 1101 nebo ASME Y14.5.
- Rozměry a jejich tolerance musí být umístěny na vhodných místech výkresu tak, aby nenarušovaly čitelnost.
- Uveďte geometrické tolerance pro klíčové součásti.
- Místo klasických tolerancí ± pro jednotlivé rozměry je užitečné použít geometrické tolerance, které lépe vystihují funkčnost komponenty.
- Například tolerance plochosti je důležitá pro tečné plochy a rovnoměrnost je rozhodující pro kluzné dráhy a kluzná ložiska.
- Rozměry důležité pro montáž by měly být označeny jako kontrolní rozměry (např. K, C v technické dokumentaci).
- Vyhněte se nadměrnému utahování tolerancí, pokud to není nutné
- Častou konstrukční chybou je přijetí velmi přísných tolerancí, které zvyšují výrobní náklady.
- Používejte toleranční třídy odpovídající funkci dílu – pro přesné díly (např. ložiska) se vyplatí použít třídy IT6 a pro konstrukční díly postačí třídy IT10-IT12.
- Podle normy ISO 2768 lze pro díly, které nevyžadují vysokou přesnost výroby, použít obecné tolerance.
- Zajištění kompatibility s metodami měření
- Tolerance by měly být zvoleny tak, aby je bylo možné kontrolovat pomocí dostupných měřicích nástrojů.
- Pokud je například tolerance menší než 0,01 mm, standardní třmeny nemusí poskytovat dostatečnou přesnost a bude zapotřebí souřadnicový měřicí stroj (CMM).
Metody kontroly rozměrů
Metoda měření 11590_ea5744-5c> |
Popis 11590_7da794-d8> |
Rozsah použití 11590_39b051-ca> |
---|---|---|
Třmen 11590_95391d-eb> |
Jednoduchý nástroj pro měření délky, průměru a hloubky s přesností 0,02 mm 11590_ada8e9-0b> |
Obecná výroba, rychlá kontrola rozměrů 11590_334824-08> |
Mikrometr 11590_85d852-4e> |
Nástroj pro přesné měření průměrů s přesností na 0,001 mm 11590_010b74-e6> |
Kontrola kritických rozměrů 11590_f1914e-5a> |
Číslicové měřidlo 11590_e342bf-e4> |
Používá se ke kontrole axiální házivosti a kolmosti povrchů 11590_197bb3-e0> |
Kontrola hřídelí, ozubených kol a ložisek 11590_39519e-7a> |
Souřadnicový měřicí stroj (CMM) 11590_3835d5-21> |
Pokročilý 3D skenovací systém, který přesně měří geometrické a polohové tolerance 11590_1f309f-8d> |
Letectví, přesná mechanika, automobilový průmysl 11590_4980c2-ab> |
Měřicí projektor (profilometr) 11590_20a20e-f9> |
Optická metoda měření obrysů a profilů povrchu 11590_3688ec-94> |
Kontrola obrobků složitých tvarů 11590_3bf408-56> |
3D laserový skener 11590_165205-65> |
Bezkontaktní skenovací systém slouží k analýze celého povrchu objektu 11590_68d857-41> |
Analýza odchylek v technologiiCAD, 3D tisk 11590_1c7bea-98> |
Praktické aspekty využití tolerancí zahrnují přesné určení přípustných odchylek na technických výkresech a účinné metody jejich kontroly. Používání správných norem a měřicích nástrojů může minimalizovat riziko výrobních chyb, zajistit správnou montáž,a optimalizovat výrobní náklady. Dnešní technologie, jako je statistická analýza procesů a pokročilé měřicí systémy, umožňují ještě přesnější kontrolu rozměrů a tolerancí, což je pro moderní průmysl klíčové.
Rozměrové tolerance – shrnutí
Správná volba rozměrových tolerancí má zásadní význam pro zajištění správné montáže součástí v různých průmyslových odvětvích. Neodpovídající tolerance mohou vést k problémům s uložením, které zvyšují náklady, materiálové ztráty a zhoršují kvalitu výrobků. Proto musí konstruktéři pečlivě analyzovat požadavky na tolerance s přihlédnutím k funkčním i ekonomickým aspektům, aby zajistili spolehlivost a efektivitu montážních procesů.