Tolleranze dimensionali
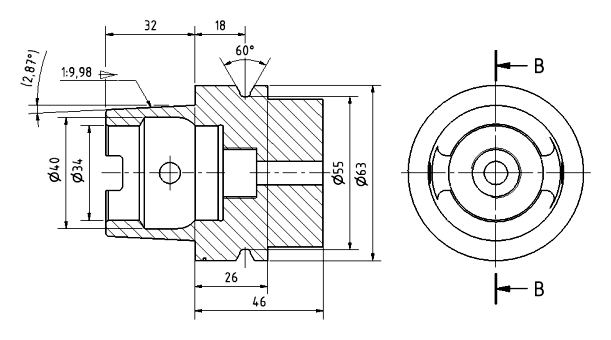
Indice dei contenuti
La tolleranza dimensionale è uno degli aspetti chiave dell’ingegneria e dell’industria che influisce su qualità, funzionalità e costi di produzione. Ogni componente tecnico, dalla vite più semplice ai complessi meccanismi delle macchine, deve essere realizzato entro un certo intervallo di deviazioni accettabili per garantire il corretto adattamento e funzionamento del prodotto finito.
La produzione moderna si basa su precisi standard di tolleranza per bilanciare qualità ed efficienza dei costi. Le tolleranze adeguate evitano problemi di assemblaggio e garantiscono la compatibilità dei componenti indipendentemente dal produttore.
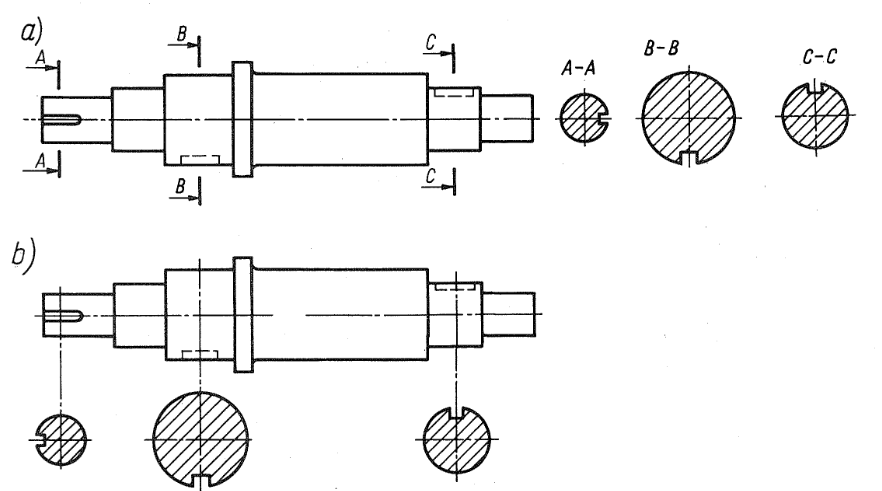
Concetti di base della tolleranza dimensionale
La tolleranza dimensionale definisce lo scostamento ammissibile delle dimensioni dalle dimensioni nominali del disegno tecnico, che sono le dimensioni effettive rispetto alle dimensioni nominali riportate sul disegno tecnico. Poiché i processi di fabbricazione non sono perfetti, ogni pezzo prodotto differisce in qualche misura dalle dimensioni presunte. La tolleranza definisce i limiti entro i quali queste differenze sono accettabili.
La tolleranza è determinata da due parametri chiave:
- Dimensione nominale (N): il valore a cui si applica la tolleranza;
- Dimensioni limite (A e B): i limiti inferiore e superiore entro cui può rientrare la dimensione effettiva;
- Deviazioni superiori e inferiori (Es, Ei per i fori ed es, ei per gli alberi): la differenza tra la dimensione nominale e i limiti.
Gli standard internazionali, come il PN-EN ISO 286-1:2011, definiscono 20 classi di tolleranza, ognuna delle quali corrisponde a diversi livelli di precisione, applicati in base alla funzione del componente.
Metodi di tolleranza dimensionale
Tradizionalmente, le tolleranze utilizzate si basano su valori più-meno, che indicano le deviazioni accettabili dalla dimensione nominale.
Un approccio moderno alle tolleranze è il sistema GD&T (Geometrical Dimensioning and Tolerancing) che consente di specificare non solo gli scostamenti dimensionali ma anche le caratteristiche geometriche dei componenti. Si tratta di un sistema più preciso e funzionale delle tradizionali tolleranze dimensionali, perché considera le dimensioni lineari e i parametri geometrici fondamentali per il corretto funzionamento e assemblaggio dei componenti.
Il sistema GD&T consente di controllare caratteristiche geometriche quali:
- La forma del componente, ad esempio:
- La planarità – determina quanto una superficie può discostarsi da un piano ideale;
- Rotondità – garantisce che la sezione trasversale di un albero o di un foro si avvicini il più possibile a un cerchio ideale;
- Cilindricità – applicata ad alberi e fori cilindrici, definisce la deviazione massima consentita dalla forma cilindrica.
- Orientamento dei componenti l’uno rispetto all’altro, ad esempio:
- Perpendicolarità – specifica la deviazione massima consentita dalla perfetta perpendicolarità tra due superfici;
- Parallelismo – assicura che due superfici o assi siano il più possibile paralleli;
- Inclinazione – determina quanto una superficie può deviare dall’angolo nominale.
- Posizione dei componenti in un layout, ad esempio:
- Posizione – controlla se un componente (ad esempio un foro) si trova nella posizione corretta rispetto ad altre parti;
- Circolarità della corsa – determina di quanto un albero o un foro può “scorrere” rispetto al suo asse di rotazione;
- Corsa dei componenti in movimento rotatorio, ad esempio:
- Deviazione assiale – applicata agli alberi e ai componenti rotanti, determina la deviazione massima dell’asse rispetto all’ideale durante la rotazione;
- Deviazione totale – una forma più restrittiva di deviazione, che riguarda tutti i punti dell’intera superficie rotante.
In pratica, il GD&T facilita la compatibilità dei pezzi prodotti in stabilimenti diversi, riduce il rischio di problemi di assemblaggio e consente una gestione efficace della qualità. Di conseguenza, il sistema GD&T è utilizzato nell’industria automobilistica, aerospaziale, elettronica e nella produzione di apparecchiature di precisione.
Importanza delle tolleranze nei processi produttivi
Le tolleranze dimensionali svolgono un ruolo fondamentale nel processo di assemblaggio dei componenti, poiché qualsiasi imprecisione può influire sulla qualità, sulla durata e sulla funzionalità del prodotto finito. Le tolleranze regolate in modo corretto assicurano che i singoli componenti si incastrino tra loro come previsto dal progettista. Se le tolleranze sono troppo restrittive o poco rigorose, possono verificarsi problemi di assemblaggio di ogni tipo, con conseguente aumento dei costi di produzione, perdite di materiale e persino il fallimento di interi sistemi.
L’accoppiamento troppo stretto – un problema di assemblaggio dei componenti
Uno dei principali problemi derivanti da tolleranze insufficienti è l’accoppiamento troppo stretto, che rende difficile o addirittura impossibile l’assemblaggio dei pezzi. Ciò può comportare la necessità di ulteriori lavorazioni, con conseguente aumento dei costi di produzione e allungamento dei tempi di consegna.
Ad esempio, se il diametro dell’albero è troppo grande rispetto al foro, può essere necessario alesare il foro o rettificare l’albero per garantire un accoppiamento corretto. Queste operazioni generano costi aggiuntivi e possono anche influire sulle proprietà meccaniche del materiale, indebolendone la struttura.
Nell’assemblaggio di parti in plastica, un accoppiamento troppo stretto può portare a cricche o deformazioni da stress, riducendo significativamente la durata del prodotto. Nell’industria automobilistica o aeronautica, un superamento anche minimo dei limiti di tolleranza può causare gravi problemi operativi, come una maggiore usura delle parti dovuta a un attrito eccessivo.
Un accoppiamento troppo lasco – collegamenti instabili
D’altra parte, un accoppiamento troppo lasco significa che le parti non si tengono saldamente, il che può portare a vibrazioni, giochi di montaggio e usura prematura dei collegamenti. Un accoppiamento troppo lasco è particolarmente pericoloso per le parti che devono sopportare carichi dinamici, come gli alberi di trasmissione, i cuscinetti o le connessioni bullonate.
Un esempio di cedimento di un meccanismo si ha quando un foro è realizzato troppo largo rispetto all’albero. Ciò fa sì che il componente non sia posizionato correttamente e che possa scivolare durante il funzionamento della macchina. In casi estremi, questo può portare al guasto del meccanismo, con la conseguente necessità di una costosa sostituzione del pezzo o addirittura dell’intera macchina.
Nelle costruzioni e nelle strutture in acciaio, i giochi eccessivi possono indebolire l’intera struttura, aumentando il rischio di cedimento sotto l’azione di forze esterne come il vento o i carichi sismici. In questi casi, per garantire la durata e la sicurezza, si utilizzano accoppiamenti di precisione con standard di deviazione specifici.
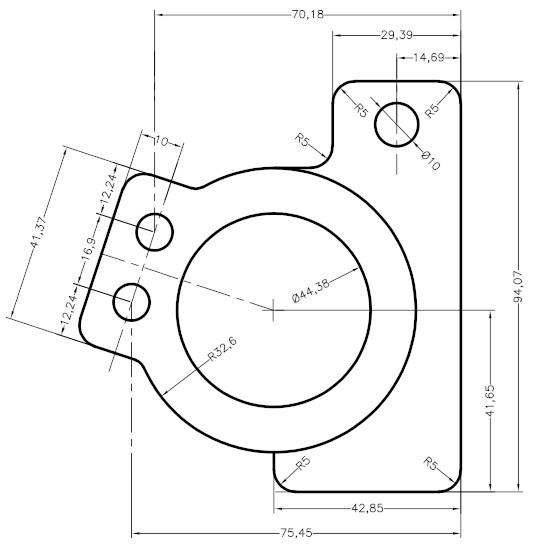
Norme e standard di tolleranza dimensionale
Gli standard internazionali regolano rigorosamente le tolleranze dimensionali. Questi standard specificano le deviazioni dimensionali ammesse e le modalità di marcatura sui disegni tecnici. L’uso di questi standard garantisce l’uniformità e la ripetibilità della produzione, facilita la cooperazione internazionale e riduce il rischio di errori di assemblaggio.
La tabella seguente mostra gli standard più importanti per le tolleranze dimensionali e la loro applicazione:
Standard 11534_ed412a-af> |
Descrizione 11534_7d1792-b2> |
Applicazione 11534_f2b370-02> |
---|---|---|
ISO 286 11534_2d6b2d-ad> |
Definisce le classi di tolleranza dimensionale per gli accoppiamenti di alberi e fori. Definisce le deviazioni limite e le regole di accoppiamento. 11534_acdc4a-6c> |
Meccanica di precisione, produzione di componenti di macchine, accoppiamenti di fori e alberi. 11534_f9a308-63> |
ISO 14405 11534_22e9af-9c> |
Standardizza le modalità di specificazione delle tolleranze dimensionali nel disegno tecnico, in particolare per le dimensioni lineari. 11534_bf30dd-4e> |
Ingegneria meccanica, aerospaziale, automobilistica. 11534_641505-e0> |
ISO GPS 11534_10e3bb-5d> |
Geometrical Product Specification System – include un approccio olistico alle tolleranze geometriche. 11534_87ac35-ce> |
Produzione di precisione, CAD/CAM, automazione del controllo qualità. 11534_1418c2-21> |
ISO 1101 11534_f5ee40-5e> |
Standardizza le marcature di tolleranza di forma e posizione e definisce i simboli e i metodi di marcatura sui disegni tecnici. 11534_b887f9-49> |
Controllo qualità, progettazione di strutture di precisione. 11534_38f425-eb> |
ISO 8015 11534_328166-f0> |
Descrive le regole di interpretazione delle dimensioni e delle tolleranze in ISO GPS. 11534_3b5493-ac> |
Universale per tutti i settori industriali. 11534_d64a89-72> |
ASME Y14.5 11534_91634b-cc> |
Lo standard americano per le tolleranze geometriche è simile all’ISO 1101, ma è utilizzato principalmente negli Stati Uniti. 11534_9ef70b-17> |
Aerospaziale, automobilistico, ingegneria aerospaziale. 11534_33da3d-2e> |
ISO 2768 11534_536c26-01> |
Definisce le tolleranze dimensionali e angolari generali per i componenti di media precisione. 11534_1b67e6-61> |
Produzione di massa, industria automobilistica, edilizia. 11534_0e0937-e5> |
Un esempio di applicazione della norma ISO 286
Lo standard ISO 286 definisce un sistema di accoppiamenti per fori e alberi, ampiamente utilizzato nell’ingegneria meccanica. Ciò significa che ogni albero e foro può avere una tolleranza specifica, a seconda della precisione richiesta. Questo sistema utilizza denominazioni letterali e numeriche, come ad esempio:
- H7/g6 – attacco a scorrimento comunemente utilizzato;
- H6/h5 – innesto a pressione per connessioni di precisione;
- H8/f7 – accoppiamento libero, utilizzato per parti che richiedono un movimento libero.
Gli standard di tolleranza dimensionale svolgono un ruolo fondamentale nella progettazione e nella produzione. Il loro utilizzo consente di ottenere prodotti di migliore qualità, di ridurre i costi associati agli errori di produzione e di garantire che i componenti si adattino tra loro, anche se provenienti da fornitori diversi. I moderni sistemi di controllo della qualità, come l’ISO GPS, consentono una precisione ancora maggiore nella progettazione e nella produzione dei componenti, essenziale nell’industria moderna.
Aspetti pratici dell’utilizzo delle tolleranze
Le tolleranze dimensionali e geometriche sono parte integrante del processo di progettazione e produzione dei componenti meccanici. Una definizione e un controllo corretti assicurano che i componenti si incastrino come previsto dagli ingegneri e che l’intero processo di produzione sia ottimizzato in termini di costi e qualità. In questo capitolo verrà illustrato come determinare correttamente le tolleranze sui disegni tecnici e quali sono i metodi di misura utilizzati per controllarle.
Come si determinano le tolleranze in un disegno tecnico?
I disegni tecnici sono documenti fondamentali nella produzione, quindi devono specificare chiaramente le dimensioni nominali e le deviazioni ammesse. Una corretta marcatura delle tolleranze consente una lettura univoca delle specifiche ed evita errori di interpretazione che potrebbero causare problemi di assemblaggio o costi di lavorazione aggiuntivi.
Regole di base per la determinazione delle tolleranze su un disegno tecnico
- Usare marcature appropriate in conformità alle norme ISO e ASME
- Le dimensioni devono essere indicate in modo leggibile, senza inutili ripetizioni;
- Le marcature delle tolleranze geometriche devono essere conformi alla norma ISO 1101 o alla norma ASME Y14.5;
- Le dimensioni e le relative tolleranze devono essere collocate in posizioni appropriate sul disegno per non interferire con la leggibilità.
- Specificare le tolleranze geometriche per i componenti chiave
- Invece di utilizzare le classiche tolleranze ± per ogni dimensione, è utile utilizzare tolleranze geometriche che rappresentino meglio la funzionalità del componente;
- Ad esempio, la tolleranza di piattezza è importante per le superfici tangenziali, mentre parallelismo è fondamentale per le guide di scorrimento e i cuscinetti a strisciamento;
- Le dimensioni importanti per il montaggio devono essere indicate come dimensioni di controllo (ad esempio, K, C nella documentazione tecnica).
- Evitare di stringere eccessivamente le tolleranze se non è necessario
- Un errore comune nella progettazione è l’adozione di tolleranze molto strette, che aumentano i costi di produzione;
- Utilizzare classi di tolleranza adeguate alla funzione del pezzo – per i pezzi di precisione (come i cuscinetti) è opportuno utilizzare le classi IT6, mentre per i pezzi strutturali sono sufficienti le classi IT10-IT12;
- Secondo la norma ISO 2768, le tolleranze generali possono essere utilizzate per i pezzi che non richiedono un’elevata precisione di fabbricazione.
- Garantire la compatibilità con i metodi di misura
- Le tolleranze devono essere scelte in modo da poter essere controllate con gli strumenti di misura disponibili;
- Ad esempio, se la tolleranza è inferiore a 0,01 mm, i calibri standard potrebbero non fornire una precisione sufficiente e sarà necessaria una macchina di misura a coordinate (CMM).
Metodi di ispezione dimensionale
Metodo di misurazione 11534_c29f11-95> |
Descrizione 11534_a098c0-5b> |
Ambito di applicazione 11534_e47271-91> |
---|---|---|
Calibro 11534_b029f0-92> |
Strumento semplice per la misurazione di lunghezza, diametro e profondità, precisione di 0,02 mm. 11534_063d0f-04> |
Produzione generale, controllo dimensionale rapido. 11534_adf7a2-fd> |
Micrometro 11534_dab098-4f> |
Strumento per la misurazione precisa dei diametri con un’approssimazione di 0,001 mm. 11534_dd1019-7f> |
Controllo di dimensioni critiche. 11534_a82151-a3> |
Calibro a quadrante (calibro a indice) 11534_403259-04> |
Utilizzato per il controllo dell’oscillazione assiale e della perpendicolarità delle superfici. 11534_ac82ca-9a> |
Ispezione di alberi, ingranaggi e cuscinetti. 11534_de9ac8-de> |
Macchina di misura a coordinate (CMM) 11534_b2a033-76> |
Un sistema avanzato di scansione 3D che misura con precisione le tolleranze geometriche e posizionali. 11534_4b2167-5d> |
Aerospaziale, meccanica di precisione, automotive. 11534_ff7449-e1> |
Proiettore di misura (profilometro) 11534_a2b499-8b> |
Metodo ottico per la misurazione dei contorni e dei profili delle superfici. 11534_7aacd6-d5> |
Ispezione di pezzi con forme complesse. 11534_922125-1a> |
Scanner laser 3D 11534_6af0d3-5f> |
Un sistema di scansione senza contatto viene utilizzato per analizzare l’intera superficie di un oggetto. 11534_fb46c8-2b> |
Analisi degli scostamenti nella tecnologia CAD, stampa 3D. 11534_1c2a85-d1> |
Gli aspetti pratici dell’uso delle tolleranze comprendono la determinazione precisa delle deviazioni consentite sui disegni tecnici e i metodi efficaci per controllarle. Utilizzando i giusti standard e strumenti di misura si può ridurre al minimo il rischio di errori di produzione, garantire un assemblaggio corretto,e ottimizzare i costi di produzione. Le tecnologie odierne, come l’analisi statistica dei processi e i sistemi di misura avanzati, consentono un controllo ancora più accurato delle dimensioni e delle tolleranze, fondamentale per l’industria moderna.
Tolleranze dimensionali in sintesi
La scelta corretta delle tolleranze dimensionali è fondamentale per garantire il corretto assemblaggio dei componenti in vari settori industriali. Tolleranze inadeguate possono portare a problemi di adattamento che aumentano i costi, le perdite di materiale e la qualità del prodotto. Pertanto, gli ingegneri devono analizzare attentamente i requisiti di tolleranza, tenendo conto degli aspetti funzionali ed economici, per garantire l’affidabilità e l’efficienza dei processi di assemblaggio.