Metody ochrony katodowej w rurociągach naftowych
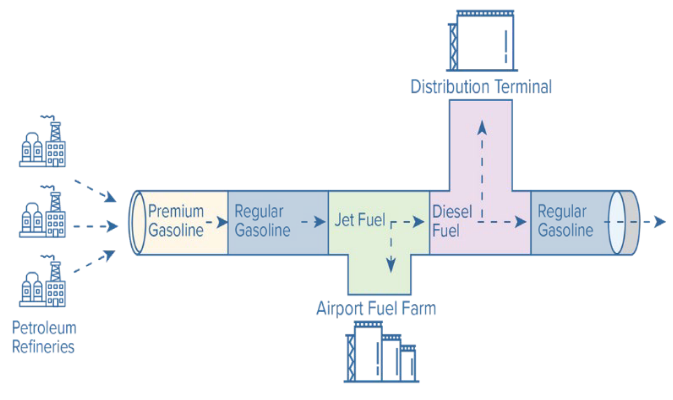
Spis treści
Korozja jest jednym z najpoważniejszych problemów w eksploatacji rurociągów naftowych. Prowadzi do zmniejszenia wytrzymałości konstrukcji, wycieków ropy oraz kosztownych napraw i awarii, co stanowi zarówno zagrożenie ekonomiczne, jak i środowiskowe. Właściwa ochrona infrastruktury przesyłowej jest kluczowa dla zapewnienia długotrwałej i bezpiecznej eksploatacji rurociągów.
Jedną z najbardziej efektywnych metod zapobiegania korozji w rurociągach jest ochrona katodowa. Jest to technologia elektrochemiczna, która polega na kontrolowanym dostarczaniu prądu elektrycznego do rurociągu, co skutecznie ogranicza proces utleniania metalu. Metoda ta znajduje zastosowanie zarówno w rurociągach podziemnych, jak i podmorskich, gdzie korozja jest szczególnie intensywna.
W niniejszym artykule zostaną omówione zasady działania ochrony katodowej, jej rodzaje, komponenty systemu oraz praktyczne zastosowanie w przemyśle naftowym. Przeanalizujemy także korzyści wynikające z tej technologii oraz wyzwania związane z jej wdrażaniem.
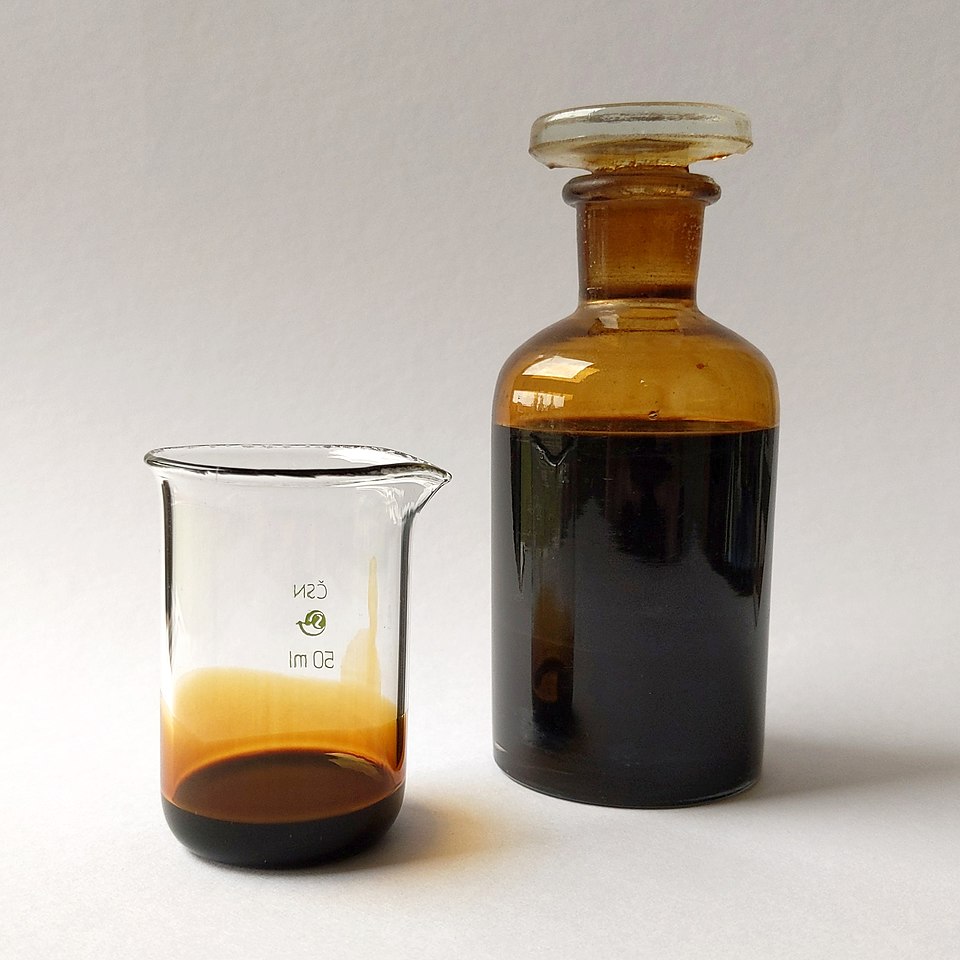
Zasada działania ochrony katodowej
Mechanizm korozji elektrochemicznej w rurociągach
Korozja elektrochemiczna w rurociągach metalowych wynika z różnicy potencjałów elektrycznych pomiędzy różnymi częściami struktury. W obecności wilgoci i elektrolitów (np. gleby lub wody morskiej) metal rurociągu zaczyna działać jak ogniwo galwaniczne, gdzie występują:
- Anoda – obszar, w którym zachodzi utlenianie metalu i jego degradacja.
- Katoda – obszar, w którym redukowane są jony z otoczenia, a metal nie ulega korozji.
Proces ten prowadzi do stopniowego rozkładu rurociągu, zwłaszcza w miejscach narażonych na działanie agresywnych czynników, takich jak związki siarki, tlen czy chlorki.
Jak działa ochrona katodowa?
Ochrona katodowa polega na przekierowaniu reakcji korozyjnej tak, aby rurociąg działał jako katoda, co eliminuje degradację metalu. W tym celu stosuje się zewnętrzne źródło elektronów, które neutralizuje potencjał elektrochemiczny rurociągu i zapobiega jego utlenianiu.
- Obniżenie potencjału elektrochemicznego metalu poniżej poziomu, przy którym zachodzi korozja.
- Dostarczanie zewnętrznych elektronów do struktury rurociągu, co zapobiega procesowi utleniania metalu.
- Wykorzystanie anod protektorowych lub systemów prądu stałego (ICCP) do kontrolowania przepływu prądu ochronnego.
Dzięki zastosowaniu ochrony katodowej procesy korozyjne są znacząco spowolnione lub całkowicie zahamowane, co pozwala na długotrwałą ochronę infrastruktury przesyłowej.
Główne komponenty systemu ochrony katodowej
System ochrony katodowej składa się z kilku kluczowych elementów:
- Anody – odpowiedzialne za dostarczanie prądu ochronnego i stopniowe zużywanie się zamiast rurociągu.
- Źródła prądu stałego – stosowane w ochronie ICCP do kontrolowanego dostarczania elektronów do rurociągu.
- Czujników i sond referencyjnych – monitorujące poziom ochrony i potencjał elektrochemiczny instalacji.
- Kable i systemy połączeniowe – zapewniające efektywne przekazywanie prądu ochronnego.
Systemy te muszą być regularnie monitorowane i konserwowane, aby zapewnić ich skuteczność i dostosowanie do warunków eksploatacyjnych.
Rodzaje ochrony katodowej
Ochrona katodowa rurociągów naftowych może być realizowana na dwa sposoby: poprzez zastosowanie anod galwanicznych (protektorowych) lub poprzez dostarczanie prądu stałego z zewnętrznego źródła (ICCP – Impressed Current Cathodic Protection). Wybór odpowiedniej metody zależy od warunków środowiskowych, długości rurociągu oraz przewodnictwa elektrycznego otaczającego medium.
Ochrona katodowa galwaniczna (anodowa)
Ochrona galwaniczna polega na wykorzystaniu anod protektorowych, które wykonane są z metali o niższym potencjale elektrochemicznym niż materiał rurociągu. Dzięki temu anoda ulega kontrolowanej korozji, chroniąc metal rurociągu przed degradacją.
W systemach ochrony galwanicznej anody wykonane są najczęściej z cynku, magnezu lub aluminium. Te materiały mają wyższy potencjał elektrochemiczny niż stal rurociągu, dzięki czemu oddają elektrony do chronionej konstrukcji i same stopniowo się zużywają.
Do zalet tej metody należą między innymi; Brak konieczności stosowania zewnętrznego źródła prądu, co upraszcza instalację, dobra skuteczność w środowiskach o niskiej rezystywności, np. w wodzie morskiej, oraz minimalne wymagania dotyczące konserwacji, ponieważ system działa pasywnie.
Niestety, jak każda metoda ma ona swoje ograniczenia, którymi są: krótsza żywotność anod, które stopniowo się zużywają i wymagają wymiany i mniejsza efektywność w środowiskach o wysokiej rezystywności (np. suche gleby), gdzie prąd ochronny rozchodzi się słabiej.
Ochrona katodowa z prądem zewnętrznym (ICCP)
Ochrona katodowa ICCP (Impressed Current Cathodic Protection) wykorzystuje zewnętrzne źródło prądu stałego do dostarczania elektronów do rurociągu, eliminując ryzyko jego korozji. Jest to bardziej zaawansowana metoda, stosowana głównie w rurociągach o dużej długości oraz w środowiskach o wysokiej rezystywności.
W systemie ICCP stosuje się nierozpuszczalne anody, wykonane z materiałów odpornych na degradację, takich jak tytan pokryty tlenkami metali mieszanych (MMO), grafit czy krzem metalurgiczny. Prąd ochronny generowany jest przez prostownik, który dostarcza napięcie do anod, wymuszając przepływ elektronów do rurociągu i chroniąc go przed utlenianiem.
Zalety tej metody to: długoterminowa ochrona, ponieważ anody ICCP nie zużywają się tak szybko jak anody galwaniczne, regulowana intensywność ochrony, co pozwala na dostosowanie poziomu ochrony do zmieniających się warunków eksploatacyjnych oraz możliwość ochrony dużych rurociągów i instalacji offshore, gdzie anody galwaniczne byłyby niewystarczające.
Ograniczenia ochrony ICCP: wymaga zasilania elektrycznego, co oznacza dodatkowe koszty eksploatacyjne i konieczność zabezpieczenia przed awariami prądu i bardziej skomplikowana instalacja, wymagająca monitorowania i okresowej regulacji systemu.
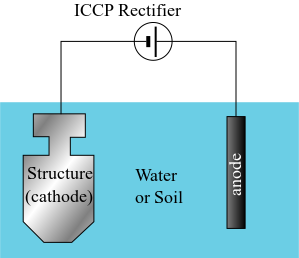
Kluczowe elementy systemu ochrony katodowej
System ochrony katodowej składa się z kilku kluczowych komponentów, które wspólnie zapewniają skuteczną ochronę rurociągów przed korozją. Ich odpowiedni dobór i regularna konserwacja mają kluczowe znaczenie dla trwałości infrastruktury przesyłowej.
Anody
Anody w systemach ochrony katodowej pełnią funkcję źródła elektronów, które przeciwdziałają procesowi korozji. W zależności od rodzaju ochrony katodowej stosuje się różne typy anod:
- Anody galwaniczne (protektorowe) – wykonane z metali bardziej aktywnych elektrochemicznie niż stal rurociągu. Najczęściej stosuje się anody z cynku, magnezu i aluminium, które stopniowo się rozpuszczają, oddając elektrony chronionej instalacji. Są wykorzystywane głównie w rurociągach podziemnych oraz instalacjach morskich.
- Anody nierozpuszczalne (ICCP) – stosowane w systemach ochrony katodowej z prądem zewnętrznym. Wykonane są z materiałów odpornych na korozję, takich jak tytan pokryty tlenkami metali mieszanych (MMO), grafit, krzem metalurgiczny. Ich zadaniem jest przewodzenie prądu ochronnego bez zużywania się, co zapewnia długoterminową ochronę dużych instalacji.
Odpowiedni dobór anod jest kluczowy dla skuteczności ochrony katodowej. Czynniki takie jak środowisko pracy, długość rurociągu i przewodnictwo elektryczne medium decydują o wyborze konkretnego typu anod.
Źródła zasilania
W systemach ochrony katodowej ICCP niezbędnym elementem jest źródło prądu stałego, które pozwala na kontrolowane dostarczanie elektronów do rurociągu. Wyróżniamy dwa podstawowe rodzaje źródeł zasilania:
- Prostowniki prądu stałego – urządzenia przekształcające prąd zmienny na prąd stały o określonym napięciu i natężeniu. Umożliwiają one precyzyjne dostosowanie poziomu ochrony katodowej do warunków eksploatacyjnych.
- Zasilanie z odnawialnych źródeł energii – w miejscach oddalonych od sieci energetycznej stosuje się systemy zasilania oparte na panelach słonecznych i turbinach wiatrowych, co pozwala na niezależność energetyczną i obniżenie kosztów operacyjnych.
Prawidłowe funkcjonowanie systemu ochrony katodowej ICCP wymaga ciągłego monitorowania napięcia i natężenia prądu, aby zapewnić optymalny poziom ochrony przed korozją.
Monitorowanie i kontrola systemu
Aby zapewnić skuteczność ochrony katodowej, konieczna jest ciągła kontrola potencjału elektrochemicznego rurociągu. Do tego celu stosuje się różne technologie monitorowania:
- Sondy referencyjne (elektrody pomiarowe) – umieszczane w pobliżu chronionej instalacji, umożliwiają pomiar potencjału rurociągu względem środowiska. Najczęściej stosowane są elektrody Cu/CuSO₄ (miedź/siarczan miedzi) dla rurociągów podziemnych oraz Ag/AgCl (srebro/chlorek srebra) dla instalacji morskich.
- Czujniki prądu korozyjnego – wykrywające anomalie w przepływie prądu ochronnego, co pozwala na szybką reakcję w przypadku awarii systemu.
- Zdalne systemy monitorowania – wykorzystujące technologie IoT i telemetryczne, umożliwiające bieżące śledzenie parametrów ochrony katodowej w czasie rzeczywistym i reagowanie na potencjalne zagrożenia.
Regularna inspekcja i monitoring pozwalają na szybkie wykrycie ewentualnych usterek i dostosowanie parametrów systemu, co zwiększa efektywność ochrony i ogranicza koszty konserwacji.
Kable i systemy połączeniowe
W systemach ochrony katodowej niezwykle ważne są odpowiednie przewody i połączenia elektryczne, które umożliwiają skuteczny przepływ prądu ochronnego. Kluczowe elementy systemu obejmują: kable odporne na korozję i uszkodzenia mechaniczne, pokryte warstwą izolacyjną chroniącą przed wilgocią i substancjami chemicznymi, złącza anodowe i katodowe, które muszą być odpowiednio izolowane, aby minimalizować straty prądu oraz skrzynki testowe i punkty pomiarowe, umożliwiające sprawdzenie skuteczności systemu w różnych lokalizacjach wzdłuż rurociągu.
Niewłaściwe wykonanie połączeń może prowadzić do strat prądu ochronnego i nieskutecznej ochrony przed korozją, dlatego dobór i jakość instalacji elektrycznej mają kluczowe znaczenie dla efektywności całego systemu. System ochrony katodowej składa się z wielu współpracujących ze sobą elementów, których właściwe funkcjonowanie zapewnia skuteczną ochronę przed korozją. Anody, źródła zasilania, systemy monitorowania oraz kable i połączenia muszą być odpowiednio dobrane i regularnie kontrolowane, aby zapewnić długotrwałą ochronę rurociągów naftowych.
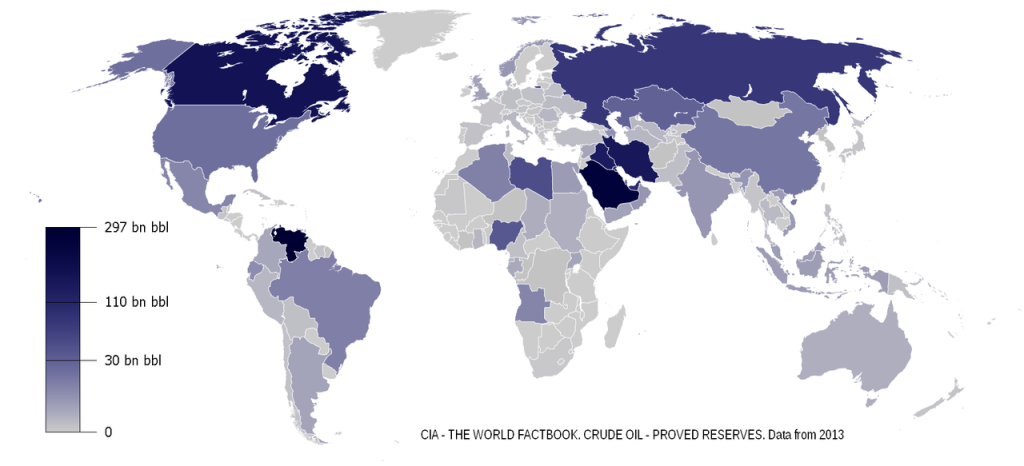
Praktyczne zastosowanie ochrony katodowej w rurociągach naftowych
Ochrona katodowa jest jedną z najczęściej stosowanych metod ochrony przed korozją w rurociągach naftowych. Jej skuteczność została potwierdzona w wielu projektach na całym świecie, zarówno w instalacjach podziemnych, jak i podmorskich. W tej sekcji omówimy rzeczywiste przypadki zastosowania ochrony katodowej, wyzwania związane z jej implementacją oraz kluczowe regulacje branżowe.
Zastosowanie ochrony katodowej w różnych warunkach
W rurociągach transportujących ropę naftową i jej produkty ochrona katodowa jest stosowana w celu zapobiegania korozji powodowanej przez kontakt metalu z wilgotnym gruntem i wodą gruntową. W środowiskach o niskiej rezystywności gleby (np. obszary wilgotne, bagienne) stosuje się anody galwaniczne, natomiast w miejscach o wysokiej rezystywności (np. pustynne tereny, gleby suche) konieczne jest wykorzystanie ochrony ICCP, ponieważ naturalny przepływ prądu ochronnego jest ograniczony.
Podmorskie rurociągi przesyłowe są narażone na silne działanie wody morskiej, która jest silnym elektrolitem, przyspieszającym procesy korozyjne. W tego typu środowiskach ochrona katodowa galwaniczna z anodami aluminiowymi lub cynkowymi jest standardowym rozwiązaniem, ponieważ zapewnia długoterminową ochronę bez potrzeby stosowania zewnętrznego zasilania. W przypadku dużych konstrukcji offshore, takich jak platformy wiertnicze i terminale morskie, częściej stosuje się systemy ICCP, które umożliwiają precyzyjną kontrolę poziomu ochrony.
Wyzwania związane z wdrażaniem ochrony katodowej
Pomimo skuteczności ochrony katodowej, jej wdrożenie wiąże się z różnymi wyzwaniami technicznymi i operacyjnymi. Do najczęstszych problemów należą:
- Nieodpowiednie zaprojektowanie systemu – niewłaściwe rozmieszczenie anod lub błędne określenie parametrów prądu ochronnego może prowadzić do nieskutecznej ochrony rurociągu lub wręcz przyspieszenia lokalnych uszkodzeń.
- Zmienność warunków środowiskowych – różnice w składzie gruntu, zasoleniu wody czy temperaturze mogą wymagać ciągłej regulacji systemu ochrony ICCP, aby dostosować poziom ochrony do warunków eksploatacyjnych.
- Interferencje z innymi instalacjami – w obszarach z dużą liczbą rurociągów, kabli lub infrastruktury elektroenergetycznej mogą występować zakłócenia w przepływie prądu ochronnego, co wymaga szczegółowych badań i optymalizacji systemu.
- Konserwacja i monitorowanie – systemy ochrony katodowej wymagają regularnych inspekcji i pomiarów, aby zapewnić ich długoterminową skuteczność. Brak odpowiedniego monitoringu może prowadzić do niezauważonych awarii i szybszej degradacji rurociągu.
Normy i regulacje dotyczące ochrony katodowej
Ochrona katodowa w przemyśle naftowym jest ściśle regulowana przez międzynarodowe normy i standardy, które określają wymagania dotyczące projektowania, instalacji i monitorowania systemów ochrony. Do najważniejszych norm należą:
- NACE SP0169 – międzynarodowy standard opracowany przez National Association of Corrosion Engineers (NACE), określający zasady projektowania i konserwacji systemów ochrony katodowej rurociągów podziemnych.
- ISO 15589-1 – norma międzynarodowa regulująca ochronę katodową rurociągów stalowych, uwzględniająca zarówno systemy ICCP, jak i anody galwaniczne.
- DNV-RP-F103 – wytyczne dotyczące ochrony katodowej rurociągów i konstrukcji podmorskich stosowane w przemyśle offshore.
- EN 12954 – europejski standard określający wymagania dotyczące ochrony katodowej rurociągów transportujących węglowodory i wodę.
Przestrzeganie tych regulacji jest kluczowe dla zapewnienia bezpieczeństwa operacyjnego i skutecznej ochrony przed korozją.
Korzyści wynikające z ochrony katodowej
Ochrona katodowa odgrywa kluczową rolę w zabezpieczaniu rurociągów naftowych przed korozją, zapewniając ich długoterminową trwałość oraz niezawodność. Dzięki niej można skutecznie zmniejszyć ryzyko awarii, ograniczyć koszty konserwacji i spełnić wymagania regulacyjne, co czyni ją jedną z najbardziej opłacalnych metod ochrony infrastruktury przesyłowej.
Rurociągi narażone na korozję wymagają częstych inspekcji i napraw, które generują znaczne koszty operacyjne oraz ryzyko przestojów w przesyle surowców. Dzięki zastosowaniu ochrony katodowej procesy korozyjne są istotnie spowolnione lub całkowicie zahamowane, co pozwala na wydłużenie żywotności instalacji nawet o kilkadziesiąt lat. W praktyce oznacza to mniejszą konieczność wymiany odcinków rurociągów, ograniczenie awarii oraz niższe wydatki na konserwację.
Nieodpowiednia ochrona przed korozją może prowadzić do wycieków ropy i gazu, które stanowią poważne zagrożenie dla środowiska i mogą skutkować surowymi karami finansowymi dla operatorów rurociągów. Systemy ochrony katodowej minimalizują ryzyko perforacji rurociągów i niekontrolowanych wycieków, co zapobiega katastrofom ekologicznym i zwiększa bezpieczeństwo transportu surowców.
Oprócz aspektów technicznych ochrona katodowa jest także niezbędna do spełnienia międzynarodowych norm bezpieczeństwa, takich jak NACE SP0169 czy ISO 15589-1, które regulują stosowanie środków zapobiegających korozji. Wdrożenie tej technologii pozwala uniknąć problemów związanych z niedostosowaniem do przepisów oraz ogranicza ryzyko finansowe wynikające z ewentualnych sankcji i odszkodowań.
Metody ochrony katodowej w rurociągach naftowych – podsumowanie
Ochrona katodowa jest niezastąpioną metodą ochrony rurociągów naftowych przed korozją, zapewniając ich długowieczność i niezawodność. Dzięki niej można skutecznie ograniczyć degradację metalu, zmniejszyć ryzyko awarii oraz obniżyć koszty konserwacji.
Współczesne systemy ochrony katodowej, wspierane przez nowoczesne technologie monitoringu i regulacji, pozwalają na skuteczne dostosowanie poziomu ochrony do zmieniających się warunków. Ich stosowanie jest nie tylko rekomendowane, ale także wymagane przez międzynarodowe normy i standardy bezpieczeństwa, co czyni je nieodzownym elementem zarządzania infrastrukturą naftową.
Artykuł ten powstał na podstawie książki „Metallurgy and Corrosion Control in Oil and Gas Production” autorstwa Roberta Heidersbacha.